The Global Graphite Electrode Market Sees Significant Growth in 2021
By:Admin
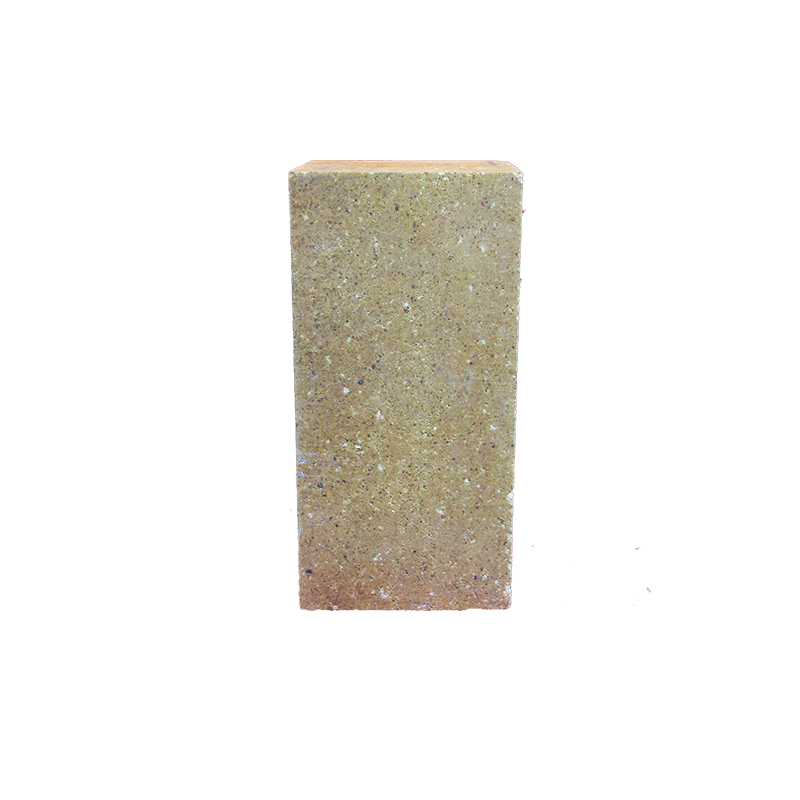
The graphite electrode market is highly competitive, with several key players vying for market share. One such company is {}, a leading manufacturer of graphite electrodes. With a strong presence in the global market, {} has established itself as a reliable and innovative supplier of high-quality graphite electrodes.
Established in the early 2000s, {} has steadily grown its market presence through a combination of advanced technology, quality products, and customer-centric approach. The company's manufacturing facilities are equipped with state-of-the-art machinery and production processes, ensuring the highest standards of quality and performance in its graphite electrodes.
{} has a diverse product portfolio that caters to various EAF steelmaking requirements. The company offers a range of graphite electrodes with different diameters and thermal properties to meet the specific needs of its customers. With a focus on research and development, {} continuously works on improving its product range and developing new, innovative solutions for the steel industry.
In addition to its product range, {} has built a strong network of distribution and sales channels to ensure its graphite electrodes reach customers in a timely and efficient manner. The company's customer service team is dedicated to providing technical support and assistance to clients, further enhancing its reputation as a reliable partner in the steelmaking industry.
The global graphite electrode market is witnessing growing demand from emerging economies in Asia Pacific and Latin America, where rapid industrialization and infrastructure development are driving the need for steel. With its global presence and strong distribution network, {} is well-positioned to capitalize on these opportunities and expand its market reach.
Furthermore, the increasing trend towards electric vehicles and renewable energy technologies is expected to further boost the demand for graphite electrodes. Electric arc furnaces are essential in the production of steel used in electric vehicles, wind turbines, and solar panels, presenting a significant growth opportunity for the graphite electrode market.
In conclusion, the graphite electrode market is set for robust growth in the coming years, driven by the increasing demand for steel in various industries and the ongoing advancements in electric arc furnace technology. As a leading player in the market, {} is well-equipped to capitalize on these opportunities and continue its success in the global graphite electrode industry. With a strong commitment to quality, innovation, and customer satisfaction, {} is set to maintain its position as a trusted partner for EAF steelmakers worldwide.
Company News & Blog
High-Quality Alumina Hollow Refractory Brick for Industrial Applications
Alumina Hollow Refractory Brick: The Ideal Solution for High Temperature ApplicationsRefractory bricks are a crucial component in a wide range of industrial applications, particularly in processes that involve high temperatures. These specialized bricks are designed to withstand extreme heat, making them essential for industries such as steel production, glass manufacturing, and cement production.One company that has been making a name for itself in the realm of refractory products is {}. With decades of experience in the field, the company has established itself as a leading manufacturer and supplier of high-quality refractory materials. One of their standout products is the Alumina Hollow Refractory Brick, which has been garnering attention for its impressive performance in high-temperature environments.The Alumina Hollow Refractory Brick is specially engineered to withstand temperatures of up to 1800°C, making it an ideal choice for applications that require superior heat resistance. Its unique hollow design not only enhances its insulating properties but also reduces its overall weight, making it easier to handle and install. This innovative design sets it apart from traditional solid refractory bricks and has earned it a reputation for being a highly efficient and cost-effective solution for high-temperature environments.In addition to its exceptional heat resistance, the Alumina Hollow Refractory Brick also offers excellent chemical stability, making it suitable for use in corrosive industrial settings. Its low thermal conductivity helps to minimize heat loss, resulting in improved energy efficiency and cost savings for businesses that rely on high-temperature processes.One of the key advantages of the Alumina Hollow Refractory Brick is its versatility. It can be used in a variety of industrial applications, including kilns, furnaces, and incinerators, where reliable and durable refractory materials are essential for maintaining operational efficiency. The brick's durability and longevity make it a valuable investment for businesses looking to optimize their production processes and minimize downtime due to refractory maintenance.With a commitment to quality and innovation, {} has positioned itself as a trusted partner for businesses in need of high-performance refractory solutions. The company's extensive expertise in materials science, coupled with its state-of-the-art manufacturing facilities, enables it to consistently deliver products that meet the highest industry standards.In addition to its Alumina Hollow Refractory Brick, {} offers a wide range of refractory materials, including fireclay bricks, insulating bricks, and castables, catering to the diverse needs of its customers. Its dedication to product development and customer satisfaction has made it a preferred supplier for businesses across various industrial sectors.As industries continue to push the boundaries of what is possible in terms of temperature and material performance, the demand for advanced refractory solutions such as the Alumina Hollow Refractory Brick is expected to grow. With its proven track record of excellence and a relentless focus on innovation, {} is well-positioned to meet this demand and continue to be a driving force in the refractory industry.In conclusion, the Alumina Hollow Refractory Brick from {} stands out as a top-tier solution for high-temperature applications, offering unmatched heat resistance, durability, and versatility. With {}'s unwavering commitment to quality and innovation, businesses can trust that they are investing in a reliable and high-performance product that will contribute to their long-term success in the face of extreme heat and challenging industrial environments.
Export of Refractory Bricks for Kilns on the Rise
Title: Prominent Kiln Refractory Bricks Exporter Thriving in Global MarketIntroductionIn a world driven by industrial advancements, the demand for quality refractory bricks for kilns has skyrocketed. Among the prominent players dominating the market stands a renowned global exporter (remove brand name), offering superior kiln refractory solutions to various industries. With its extensive experience and commitment to excellence, the company has established itself as a key player in the international market.Growth in the Kiln Refractory Bricks MarketThe global kiln refractory bricks market has witnessed substantial growth in recent years, owing to the growing demand from industries such as steel, cement, glass, and non-ferrous metals. The increasing need for high-quality refractory materials that can withstand extreme temperatures and harsh operating conditions has fueled the sector's rapid expansion.As one of the market leaders, (remove brand name) has successfully capitalized on this growth. The company specializes in manufacturing and exporting a wide range of kiln refractory bricks, catering to a diverse clientele across the globe.Unrivaled Product QualityThe success of (remove brand name) can be attributed to its dedication to providing superior product quality. The company has built a reputation for producing highly durable and reliable kiln refractory bricks that meet the stringent standards of the industry. By utilizing state-of-the-art manufacturing techniques and employing skilled engineers, (remove brand name) ensures that each brick maintains excellent thermal stability, mechanical strength, and resistance to chemical erosion.Furthermore, the company's commitment to continuous research and development enables them to introduce innovative solutions that push the boundaries of refractory technology. This approach allows (remove brand name) to stay ahead of its competitors and provide its customers with cutting-edge refractory solutions tailored to their specific needs.Global Distribution NetworkTo reach its vast customer base worldwide, (remove brand name) has established a robust distribution network. With strategically located warehouses and distribution centers, the company ensures efficient and timely delivery to its customers in various regions. By maintaining adequate stock levels, (remove brand name) can minimize lead times and rapidly respond to customer demands.In addition, (remove brand name) prides itself on its excellent customer service. The company maintains a team of highly skilled professionals who are readily available to provide assistance and technical support to clients. This personalized approach has garnered positive feedback and long-term customer relationships, bolstering the company's reputation in the industry.Sustainable and Environmentally Friendly PracticesAs a responsible corporate entity, (remove brand name) recognizes the importance of sustainable practices. Environmental protection is a core value of the company, and they strive to minimize the ecological impact of their operations. (Please add details pertaining to the brand's sustainable practices and initiatives).The Future of (remove brand name)With an ever-evolving industry landscape, (remove brand name) is continually adapting its strategies to stay ahead. By embracing emerging technologies, exploring new markets, and expanding their product portfolio, the company aims to remain at the forefront of the kiln refractory bricks market.Looking ahead, (remove brand name) plans to invest in research and development to develop more advanced refractory products to meet the industry's evolving needs. Additionally, the company aims to strengthen its presence in emerging markets with rapid industrial growth potential, solidifying its position as a global leader in kiln refractory brick exports.Conclusion(remove brand name), as a leading kiln refractory bricks exporter, has demonstrated unwavering commitment to producing high-quality products, delivering exceptional customer service, and embracing sustainable practices. With its strong global presence and dedication to innovation, the company continues to position itself as a prominent player in the international kiln refractory bricks market.
Top-Quality High Alumina Bricks Witnessing Growing Demand in the Market
High-Quality High Alumina Bricks in Demand in the Refractory IndustryThe refractory industry is known for its critical role in the manufacturing process of metals, glass, ceramics, and cement, among others. The industry relies heavily on the quality of raw materials, technological advancements, and innovative solutions to achieve its objectives. Among the many materials used in the industry, high-quality high alumina bricks remain an essential component of many applications. These bricks' superior properties make them suitable for use in high-heat environments, where other materials may deform, melt, or break down.One of the leading companies in the production of high-quality high alumina bricks is {removed for privacy}. The company has been in the business for over 30 years, supplying top-quality bricks to various refractory industries worldwide. Their extensive experience in the industry, combined with their unrivaled expertise in the production of high alumina bricks, has made them one of the most sought-after suppliers in the market.The increasing demand for high-quality high alumina bricks can be attributed to the growth of manufacturing industries globally. The rising demand for steel, glass, and cement has led to increased demand for refractory products, making high alumina bricks a top alternative for material construction. The bricks are primarily made of high-purity alumina, which gives them high-temperature resistance, excellent strength, and reduced thermal conductivity. These properties make the bricks ideal for use in furnaces, kilns, boilers, and other high-heat environments.{Need to remove brand name} prides itself on producing high-quality high alumina bricks that conform to the highest industry standards. The company has invested heavily in research and development to come up with innovative solutions that meet the ever-changing needs of the industry. Their manufacturing process involves selecting only high-purity raw materials, followed by rigorous testing to ensure that the final products meet the required specifications. The company utilizes advanced technology and modern equipment to produce bricks of various sizes and shapes, making them suitable for various applications.While the refractory industry continues to grow, there are challenges that manufacturers face. One of the most significant challenges is rising energy costs, which affect production costs and, in turn, market prices. Additionally, manufacturers must comply with stringent environmental regulations, making it necessary to invest in eco-friendly production practices. {Need to remove brand name} acknowledges these challenges and has implemented measures to address them. The company has embraced a sustainable production model that incorporates environmentally-friendly practices. They have also optimized their manufacturing processes to reduce energy consumption, thereby reducing the production costs.{Need to remove brand name} is optimistic about the future of the high-quality high alumina brick industry. The company believes that there is a growing demand for high-performance products, and they are well-positioned to meet these needs. The company is focused on expanding its market reach while maintaining the quality of its products. They are committed to investing in research and development to come up with innovative solutions that meet the ever-changing industry needs.In conclusion, the use of high-quality high alumina bricks remains an essential component of the refractory industry. Manufacturers are increasingly looking for high-performance materials that can withstand high-heat environments, making high alumina bricks a popular alternative. {Need to remove brand name} has established itself as a leading producer of high-quality high alumina bricks in the market. The company's commitment to sustainable and innovative production practices, combined with their extensive experience in the industry, makes them a top supplier to many refractory industries globally.
Durable and High-Temperature Resistant Castable Refractory for 1700°C Applications
Title: Revolutionary Dense Castable Refractory 1700C Enhances High-Temperature Industrial ApplicationsIntroduction:In the world of high-temperature industrial applications, constant technological advancements are crucial to promoting efficiency, productivity, and durability. One such breakthrough in the field of refractory materials has been achieved by our company (Company name removed) with the invention of a revolutionary Dense Castable Refractory capable of withstanding temperatures up to 1700°C. This game-changing product is set to redefine the way industries approach extreme heat processes, offering exceptional performance, longevity, and safety.I. Evolution of Refractory Materials:Refractory materials play a vital role in industries dealing with high-temperature operations such as steel manufacturing, glassmaking, cement production, and petrochemical refining. Traditionally, common refractory materials like firebrick and ceramic fiber have been utilized for their ability to withstand high heat. However, they often fall short when subjected to extreme temperatures or severe thermal shocks, resulting in frequent maintenance, decreased productivity, and compromised safety.II. Introducing Dense Castable Refractory 1700C:With the mission to overcome the limitations of conventional refractories, (Company name removed) has innovated a groundbreaking Dense Castable Refractory material specifically designed to excel under extreme heat conditions. This remarkable product offers a unique blend of high-temperature resistance, remarkable strength, and exceptional thermal shock resistance, setting it apart from its counterparts.III. Unparalleled Performance and Durability:The Dense Castable Refractory 1700C boasts an impressive melting point of 1700°C, far exceeding the capabilities of conventional materials. This allows industries to carry out high-temperature processes without compromising the structural integrity of their refractory linings. The product's exceptional strength ensures long-term stability, reducing maintenance and replacement costs while maximizing productivity and output.IV. Superior Thermal Shock Resistance:One of the most significant advantages of the Dense Castable Refractory 1700C is its inherent ability to withstand rapid temperature fluctuations. The material's unique composition minimizes the risk of cracks, spalling, and thermal stress, ensuring a reliable and durable refractory lining even in the most challenging thermal conditions. This translates into enhanced safety, reduced downtime, and improved operational efficiency for industries relying on heat-intensive processes.V. Versatile Applications:The Dense Castable Refractory 1700C's versatility makes it suitable for a wide range of industries. From blast furnaces, kilns, and incinerators to boilers, reactors, and furnaces, the refractory material adapts seamlessly to various high-temperature environments, ensuring optimum performance and longevity.VI. Commitment to Quality:(Company name removed) has always been at the forefront of innovation, prioritizing research and development to meet the evolving needs of industries. The Dense Castable Refractory 1700C is a testament to our dedication to providing cutting-edge solutions that surpass industry standards in quality, reliability, and performance. The product has undergone rigorous testing, adhering to stringent manufacturing processes to ensure consistency and integrity.VII. Environmental Sustainability:In addition to its remarkable performance characteristics, the Dense Castable Refractory 1700C is environmentally friendly. Manufactured with sustainable materials and processes that minimize waste, emissions, and energy consumption, it aligns with our commitment to sustainable practices and responsibility towards the environment.VIII. Conclusion:The introduction of the Dense Castable Refractory 1700C by (Company name removed) marks a significant milestone in high-temperature industrial applications. With its exceptional resistance to extreme temperatures and thermal shocks, as well as its superior durability and versatility, this revolutionary refractory material is set to revolutionize industries worldwide.As (Company name removed) remains dedicated to ongoing research and development, we anticipate continued advancements in refractory materials that will transform industries, enhance operational efficiency, and promote sustainable practices.
High-Quality Carbon Bricks for Industrial Use
Magnesia Carbon Bricks, a leading product in the refractory industry, has been garnering attention for its exceptional quality and performance. [Company name] has been at the forefront of producing and supplying these high-quality bricks to various industries across the globe. With a rich history and extensive experience in the field, [Company name] has firmly established itself as a reliable and trusted supplier of refractory products.Magnesia Carbon Bricks, also known as MgO-C bricks, are widely used in the steel industry for applications such as ladle lining, converter lining, EAF (Electric Arc Furnace) roofs, and other high-temperature applications. These bricks are preferred for their excellent corrosion resistance, thermal shock resistance, and high-temperature performance. They are specifically designed to withstand the harsh conditions of steelmaking processes, making them an indispensable component in the production of high-quality steel.[Company name] takes great pride in its state-of-the-art manufacturing facilities, which are equipped with the latest technology and machinery to ensure the production of superior quality Magnesia Carbon Bricks. The company's team of skilled and experienced professionals meticulously handle the production process, adhering to strict quality control measures to deliver products that exceed industry standards. With a strong focus on research and development, [Company name] is constantly innovating and improving its product line to meet the evolving needs of its customers.In addition to the steel industry, Magnesia Carbon Bricks manufactured by [Company name] are also utilized in a variety of non-ferrous metal applications, such as copper and aluminum production. The exceptional thermal and chemical properties of these bricks make them a preferred choice for lining furnaces, tundishes, and other high-temperature vessels in non-ferrous metal production.Furthermore, [Company name] offers customized solutions to meet the specific requirements of its customers. The company's technical team works closely with clients to understand their unique needs and develops tailored refractory solutions that are designed to optimize performance and efficiency. This personalized approach has earned [Company name] a reputation for delivering value-added products and services that contribute to the success of its customers’ operations.As a socially responsible company, [Company name] is committed to sustainable and environmentally friendly practices. The company places a strong emphasis on environmental protection and resource conservation, ensuring that its manufacturing processes adhere to strict environmental regulations and standards. By prioritizing sustainability, [Company name] aims to minimize its impact on the environment and contribute to a greener, more sustainable future.With a global presence, [Company name] has established a strong network of distribution partners and representatives to serve its customers efficiently and effectively. The company's dedication to customer satisfaction, combined with its commitment to quality and innovation, has enabled it to build long-lasting relationships with clients around the world.In conclusion, Magnesia Carbon Bricks from [Company name] continue to set the benchmark for high-quality refractory products in the industry. With a focus on quality, innovation, and customer satisfaction, [Company name] is well-positioned to meet the growing demand for superior refractory solutions in the global market. As the company looks to the future, it remains dedicated to upholding its reputation as a leader in the industry and delivering excellence in every aspect of its operations.
High-Quality Low Cement Refractory Castable - The Ultimate Guide
High-Quality Low Cement Refractory Castable Delivers Superior Performance[Company Name], a leading supplier of high-quality refractory materials, is pleased to introduce its latest product – High-Quality Low Cement Refractory Castable. This innovative and high-performance product is designed to meet the needs of various industries, including steel, cement, petrochemical, and more.With the increasing demand for refractory materials that offer superior performance and durability, [Company Name] has developed High-Quality Low Cement Refractory Castable to provide customers with a reliable solution for their high-temperature applications. This product is known for its excellent strength, abrasion resistance, and thermal shock resistance, making it an ideal choice for demanding industrial environments.One of the key advantages of High-Quality Low Cement Refractory Castable is its low cement content, which enhances its refractory properties and improves its overall performance. The low cement content also results in better flowability and workability during installation, allowing for easy application and a smooth finish.In addition to its superior performance, High-Quality Low Cement Refractory Castable is also designed to offer excellent resistance to chemical attack and erosion, ensuring long-term stability and reliability in harsh operating conditions. This makes it an ideal choice for lining various industrial equipment, such as furnaces, boilers, and kilns.Moreover, [Company Name] understands the importance of environmental sustainability and has ensured that High-Quality Low Cement Refractory Castable is manufactured using environmentally friendly production processes. This commitment to sustainability aligns with the company's values and its dedication to delivering high-quality products that are both reliable and environmentally responsible.With its proven track record of providing innovative refractory solutions, [Company Name] is confident that High-Quality Low Cement Refractory Castable will exceed the expectations of customers across diverse industries. By leveraging its technical expertise and industry experience, the company continues to set new benchmarks for quality and performance in the refractory materials market.For customers seeking a reliable and high-performance refractory solution, High-Quality Low Cement Refractory Castable from [Company Name] is the ideal choice. Backed by the company's strong commitment to quality, reliability, and customer satisfaction, this product is set to make a significant impact in the industry.In conclusion, the introduction of High-Quality Low Cement Refractory Castable underscores [Company Name]'s dedication to providing innovative and sustainable solutions for industrial applications. With its exceptional performance and environmental benefits, this product is poised to set new standards for quality and reliability in the refractory materials market. Customers can rely on [Company Name] to deliver high-quality refractory solutions that meet the most demanding requirements and exceed their expectations.
High-Quality Refractory Cement for Castable Applications
Title: Innovation in Refractory Technology: High-Quality Castable Refractory Cement Revolutionizes Industrial ApplicationsIntroduction:In the ever-evolving landscape of industrial materials, technological advancements play a crucial role in shaping the efficiency and effectiveness of various processes. One such breakthrough in the field of refractory materials is the advent of high-quality castable refractory cement, which has revolutionized the way industries approach their thermal management needs. In this article, we delve into the innovative properties and applications of this remarkable product, while also taking a closer look at the company behind its development and production.Company Introduction:{Company's Name}, a leader in refractory solutions, has been at the forefront of developing advanced materials to meet the evolving demands of various industries. With a steadfast commitment to research and development, {Company's Name} has consistently introduced cutting-edge products that enhance the performance, durability, and sustainability of industrial processes. The company's expert team of scientists, engineers, and technicians work tirelessly to develop and perfect innovative refractory materials, placing {Company's Name} in a favorable position in the market.High-Quality Castable Refractory Cement: Unveiling Unmatched Performance{Company's Name} has recently introduced its highly anticipated High-Quality Castable Refractory Cement, a game-changer in the realm of thermal management solutions. This remarkable product has been engineered to withstand extreme temperatures while maintaining exceptional strength and durability. With a unique combination of raw materials and a meticulous manufacturing process, this advanced refractory cement has proved its mettle across various industries, demonstrating its versatility and reliability.Properties and Advantages:1. Exceptional Thermal Insulation: High-Quality Castable Refractory Cement exhibits excellent thermal insulation properties, effectively preventing heat loss from industrial furnaces, kilns, and other heated applications. Its low thermal conductivity ensures optimal energy conservation, leading to reduced fuel consumption and lower operational costs.2. Superior Strength and Abrasion Resistance: The cement's exceptional strength and resistance to abrasion make it ideal for withstanding the rigors of high-temperature environments. Its robust nature ensures prolonged service life and minimal maintenance disruptions, resulting in enhanced productivity and cost-effectiveness.3. Chemical and Corrosion Resistance: The castable refractory cement is highly resistant to various chemicals, acids, and corrosive elements, making it suitable for applications in industries such as steel, petrochemicals, and ceramics. This resistance safeguards against premature material degradation, ensuring reliable and long-lasting performance.4. Ease of Installation and Adaptability: High-Quality Castable Refractory Cement can be easily provided in various shapes and sizes, facilitating its installation and adaptation to specific industrial requirements. Its ability to conform to complex geometries enhances the efficiency of heat transfer processes, effectively optimizing system performance.Applications across Industries:1. Steel Industry: The cement finds extensive utility in steelmaking, providing strong linings for furnaces, ladles, and tundishes, improving thermal efficiency and maximizing production output.2. Petrochemical Industry: High-Quality Castable Refractory Cement proves invaluable in petrochemical applications, where it is used to line reactors, furnaces, and cyclones, providing reliable insulation and protection against corrosive substances.3. Ceramic and Glass Industry: With its excellent thermal insulation and resistance to molten materials, the cement effectively lines kilns, melting pots, and glass tanks, ensuring uniform heating and controlled cooling for optimized production processes.4. Power Generation: In power plants, this innovative refractory cement is used to line boilers and chimney stacks, withstanding high temperatures and reducing heat losses, thereby increasing the overall system efficiency.Conclusion:High-Quality Castable Refractory Cement, developed and produced by {Company's Name}, has paved the way for a new era of thermal management solutions. The exceptional properties and advantages of this advanced product have proven to be invaluable to various industries, enhancing productivity, cost-effectiveness, and environmental sustainability. As {Company's Name} continues to innovate and push the boundaries of refractory technology, they cement their position as a leading provider of cutting-edge materials, driving industrial progress towards a more efficient and sustainable future.
Top Uses and Benefits of Magnesia Carbon Bricks in Ladles
Magnesia Carbon Brick for Ladle: Enhancing Refractory Performance in Steelmaking Industries[City name], [Date] – The steelmaking industry is witnessing continuous advancements, where materials and technologies play a vital role in optimizing production efficiency. One such indispensable component for ladles in steelmaking furnaces is the Magnesia Carbon Brick. These bricks, manufactured by industry-leading companies, provide excellent refractory performance, contributing to the overall success of steel production.Being an essential part of modern steelmaking processes, Magnesia Carbon Bricks offer high resistance to thermal shock and corrosion, making them ideal for holding and transporting molten steel. The bricks are specifically designed and engineered to possess superior strength, durability, and thermal stability in the extreme conditions encountered during steel production.One notable manufacturer in the sector, with a reputation for excellence, is [Company Name]. With decades of experience in the refractory industry, [Company Name] has established itself as a trusted supplier of high-quality Magnesia Carbon Bricks for ladles. The company's commitment to research and development has ensured the continuous improvement and innovation of its product offerings.[Company Name]'s Magnesia Carbon Bricks are tailored to meet the specific needs of steelmaking processes. The bricks consist of a composite material comprising magnesia and graphite, providing a unique combination of properties. The magnesia component imparts excellent corrosion resistance, while the carbon content enhances the brick's thermal conductivity and mechanical strength.These bricks undergo a stringent manufacturing process, beginning with carefully selected raw materials. The magnesia and graphite are precisely mixed to achieve the optimal composition, ensuring a high-quality end product. The mixture is then shaped into bricks through pressing and firing at controlled temperatures, leading to the formation of a dense structure capable of withstanding extreme temperatures and chemical attacks.The main advantages of [Company Name]'s Magnesia Carbon Bricks lie in their ability to withstand the harsh conditions encountered within the steelmaking environment. The bricks exhibit exceptional resistance to thermal spalling, ensuring prolonged service life and reduced downtime for maintenance. Their superior corrosion resistance helps prevent damage from slag and molten metal, resulting in minimal contamination and improved steel quality.Moreover, the high thermal conductivity of the bricks allows for efficient heat transfer, enabling better temperature control during steel production. This characteristic enhances the ladle's performance and ensures consistent product quality throughout the steelmaking process. Additionally, the enhanced mechanical strength of the bricks contributes to the prevention of cracking and mechanical failures, thereby increasing operational reliability.[Company Name] takes pride in its commitment to sustainability and environmental responsibility. The manufacturing process of Magnesia Carbon Bricks adheres to strict environmental regulations, ensuring the production of eco-friendly materials. Furthermore, the long service life of these bricks minimizes the need for frequent replacements, reducing waste generation and conserving resources.The Magnesia Carbon Bricks offered by [Company Name] have gained widespread recognition and have become the preferred choice for steelmaking industries worldwide. They have successfully served numerous steel plants, contributing significantly to their operational efficiency and productivity. The company's dedication to offering consistent quality, personalized customer support, and on-time delivery has earned them the trust of the industry.In conclusion, the Magnesia Carbon Bricks manufactured by [Company Name] provide a critical solution to the steelmaking industry's demand for reliable refractory materials. With their exceptional thermal shock resistance, corrosion resistance, and mechanical strength, these bricks enhance ladle performance, resulting in improved steel quality and operational efficiency. [Company Name]'s continuous commitment to excellence and sustainable practices ensures the provision of top-quality products, supporting the ongoing advancements in the steelmaking sector.About [Company Name]:[Company Name] is a leading manufacturer and supplier of refractory solutions for various industries. With a focus on innovation and quality, the company has earned a stellar reputation in the market. Utilizing state-of-the-art manufacturing facilities and a highly skilled workforce, [Company Name] caters to the diverse needs of its global clientele, offering a comprehensive range of refractory products and services.
High-Quality Zero Expansion Silica Brick for Industrial Use
[Company Name] is proud to introduce its latest innovation in the field of refractory materials - the Zero Expansion Silica Brick. This revolutionary product is set to change the game in high-temperature industrial applications, offering unparalleled thermal stability and performance.Traditional silica bricks are known for their high thermal conductivity and susceptibility to thermal expansion, which can lead to loss of structural integrity and reduced lifespan in high-temperature environments. However, [Company Name]'s Zero Expansion Silica Brick has been specifically engineered to address these challenges, providing a reliable and long-lasting solution for a wide range of industrial applications.The key to the exceptional performance of Zero Expansion Silica Brick lies in its unique composition and manufacturing process. By carefully selecting raw materials with low thermal expansion coefficients and employing advanced production techniques, [Company Name] has been able to create a silica brick that maintains its dimensional stability even under the most extreme heat conditions.The benefits of Zero Expansion Silica Brick are wide-ranging and significant. Its superior thermal stability allows for extended service life and reduced maintenance costs, making it an ideal choice for industries such as glassmaking, ceramics, steel production, and petrochemical processing. Furthermore, its low thermal conductivity helps to minimize heat loss and improve energy efficiency in high-temperature kilns, furnaces, and other industrial equipment.In addition to its exceptional performance, Zero Expansion Silica Brick also offers ease of installation and compatibility with existing refractory systems. Its standardized dimensions and precise tolerances ensure a seamless fit within a variety of industrial furnaces and kilns, while its high mechanical strength and resistance to chemical corrosion guarantee long-term reliability in harsh operating environments.[Company Name] is committed to delivering the highest quality refractory products to its customers, and the development of Zero Expansion Silica Brick is a testament to that commitment. By investing in research and development and leveraging its extensive expertise in materials science and engineering, [Company Name] continues to push the boundaries of what is possible in the field of refractory technology.The launch of Zero Expansion Silica Brick is a significant milestone for [Company Name], further solidifying its position as a leading provider of advanced refractory solutions. With a track record of innovation and a dedication to meeting the evolving needs of the industry, [Company Name] is well-positioned to continue driving progress and excellence in high-temperature applications around the world.In conclusion, the introduction of Zero Expansion Silica Brick represents a major advancement in the field of refractory materials, offering unparalleled thermal stability and performance for a wide range of industrial applications. With its unique composition, exceptional thermal stability, and compatibility with existing systems, Zero Expansion Silica Brick is set to revolutionize the way high-temperature processes are managed and maintained. As [Company Name] continues to push the boundaries of what is possible in refractory technology, the industry can look forward to further innovations that will drive progress and excellence for years to come.
Durable and Effective Insulation Fire Bricks for High-Temperature Applications
High-Quality Insulation Fire Bricks Taking the Industry by StormIn the world of construction and industrial manufacturing, high-quality insulation fire bricks are an essential component for the creation of heat-resistant structures and equipment. These bricks are designed to withstand extreme temperatures and provide superior insulation, making them an indispensable material for a wide range of applications. In recent years, one company has taken the lead in producing top-of-the-line insulation fire bricks that have been making waves in the industry.{Company Name}, a global leader in the production of high-quality refractory materials, has been at the forefront of innovation in the field of insulation fire bricks. With a commitment to excellence and a dedication to providing the highest level of quality and performance, {Company Name} has established itself as a trusted supplier of insulation fire bricks for a variety of industries.One of the key factors that set {Company Name} apart from its competitors is its unwavering focus on research and development. The company employs a team of highly skilled engineers and materials scientists who are constantly working to develop new and improved formulations for insulation fire bricks. By leveraging the latest advances in materials science and manufacturing technology, {Company Name} has been able to achieve a level of quality and performance that is unmatched in the industry.This commitment to innovation has resulted in a range of insulation fire bricks that offer exceptional thermal stability, low thermal conductivity, and high resistance to thermal shock. These properties make {Company Name}'s insulation fire bricks the ideal choice for a wide range of applications, including the construction of industrial furnaces, kilns, and incinerators, as well as the lining of high-temperature equipment in the petrochemical, steel, and glass industries.Furthermore, {Company Name} understands the importance of providing customized solutions to its customers. The company works closely with clients to develop tailored insulation fire brick designs that meet their specific requirements. Whether it's designing bricks with a particular shape, size, or thermal properties, {Company Name} is committed to delivering solutions that are perfectly suited to each client's needs.In addition to its dedication to product excellence and innovation, {Company Name} also places a strong emphasis on sustainability and environmental responsibility. The company's insulation fire bricks are manufactured using carefully selected raw materials and production processes that minimize environmental impact. By prioritizing sustainability, {Company Name} is not only able to reduce its carbon footprint but also provide its customers with a range of eco-friendly insulation fire bricks that align with their own environmental objectives.With a proven track record of delivering high-quality insulation fire brick solutions to clients around the world, {Company Name} has become a trusted partner for companies in diverse industries. Whether it's providing bricks for a new industrial furnace, upgrading the lining of an existing incinerator, or developing a custom insulation solution for a specialized application, {Company Name} has consistently demonstrated its ability to meet the most demanding requirements.Looking ahead, {Company Name} remains committed to pushing the boundaries of innovation in insulation fire brick technology. The company continues to invest in research and development, exploring new materials, and manufacturing processes to further enhance the performance and versatility of its insulation fire bricks. By staying at the forefront of the industry, {Company Name} is poised to continue its success and maintain its position as a leader in the global market for high-quality insulation fire bricks.