High-Density Ceramic Fiber Board in Large Size for Various Applications
By:Admin
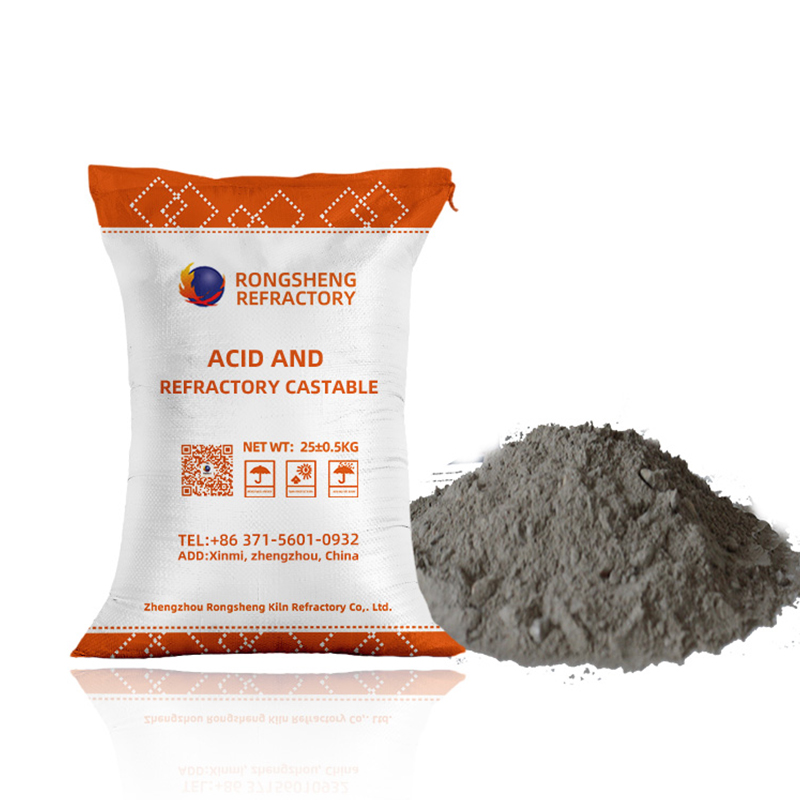
This Ceramic Fiber Board is an ideal insulation material. It is made from high-quality alumina-silicate ceramic fibers, and its manufacturing process involves the use of strict quality controls to ensure that the board is free from any impurities. The result is a rigid, smooth, and uniform blanket that provides excellent insulation.
The primary advantage of the 900mm X 600mm X 50mm 300kg/M3 Ceramic Fiber Board is its high-temperature resistance, which can withstand temperatures up to 1260°C. The material also has good thermal stability, high strength, good sound insulation properties, and low thermal conductivity. Additionally, it is easy to work with, being easily sawn, shaped, and handled without any significant issues.
The insulation properties of this material make it suitable for a wide range of thermal applications. Its excellent insulation and thermal stability make it adaptable to high-temperature equipment. It is ideal for use in kilns, ovens, and high-temperature furnaces. Additionally, it can be used in power plants and boilers applications, where it provides excellent insulation against heat loss, thereby increasing energy efficiency.
If you are considering using the 900mm X 600mm X 50mm 300kg/M3 Ceramic Fiber Board in any industrial application, be sure to work with a reputable manufacturer such as our company. Our company produces high-quality ceramic fiber boards, and we have extensive experience in the industry. We are committed to delivering exceptional products that meet our customers' requirements and expectations.
Our manufacturing process is characterized by strict quality control measures to ensure that all our products meet the highest quality standards. We use state-of-the-art technology, and our team of skilled professionals is always working to innovate and deliver high-quality products.
As a company, we take pride in our customer service and our ability to meet the specific requirements of our clients. We are available to assist you every step of the way, from product selection to delivery. Our dedicated team will assist you in choosing the right products for your application, providing you with expert guidance and advice to ensure that you make the right decision.
In conclusion, the 900mm X 600mm X 50mm 300kg/M3 Ceramic Fiber Board is an excellent insulation material for a wide range of thermal applications. It provides high-temperature resistance and thermal stability while being easy to handle and work with. We are a reputable manufacturer of ceramic fiber boards, and we are committed to delivering quality products and exceptional customer service. Contact us today to learn more about our products and services, and how we can help you find the right insulation materials for your application.
Company News & Blog
Discover Premium Heat Resistant Bricks for Sale
Fire and heat are two of the most destructive elements that can cause significant damage to any structure or machinery. It is vital to protect against these elements to prevent any untoward incidents from happening.An Australian company specializes in manufacturing heat-resistant bricks that can withstand intense heat and pressure. Their products have become a favorite of many industrial companies, as they are made with quality materials and provide exceptional heat resistance.The company's heat-resistant bricks are made from high-grade materials, ensuring durability and longevity. They come in various colors, sizes, and shapes to suit different industrial applications. The bricks are highly resistant to heat, chemical corrosion, and abrasion, making them highly suitable for use in kilns, furnaces, boilers, and other industrial applications.The company's heat-resistant bricks are made from a blend of materials that provide exceptional heat resistance. These bricks can withstand temperatures up to 1,800°C and are highly durable due to their high-density structure. They also offer high resistance to thermal shock, which makes them ideal for use in high-temperature environments.Their heat-resistant bricks have been tested and proven to be of high quality, making them popular among industrial companies that require high-performance products. They are also cost-effective, compared to other brands, and can be customized to meet the specific needs of clients.The company also offers other heat-resistant products such as heat-resistant ceramic fiber products and refractory products for high-temperature insulation. They are committed to providing safe and reliable heat-resistant solutions to their clients.The company has various distributors across the country, ensuring that their products are easily accessible and available to customers. Their customer service team is also responsive and available to assist clients with their needs.Many industries have benefitted from using the company's heat-resistant bricks, including the steel, cement, glass, and power generation industries. The bricks have helped these industries maintain their operations at high temperatures, efficiently and safely.In conclusion, the Australian company's heat-resistant bricks have proven to be a reliable and cost-effective solution for industries that require high-performance products. Their commitment to quality and safety has made them a trusted brand in the industry. With their excellent products and outstanding customer service, the company has become a preferred supplier of heat-resistant products in Australia.
High-Quality Magnesite Refractory Bricks Meet Growing Demand in Steel Industry
Title: Evolving Magnesite Refractory Bricks Industry Emphasizes Quality and SustainabilityIntroduction:In recent times, the magnesite refractory bricks industry has been witnessing significant growth, driven by the increasing demand for high-quality refractory materials in various sectors. Magnesite refractory bricks, renowned for their exceptional heat resistance and durability, are widely utilized in industries like steel, cement, glass, non-ferrous metals, ceramics, etc., supporting critical processes that require elevated temperatures.Company Introduction:{Company Name} is a prominent player in the magnesite refractory bricks market, dedicated to producing top-notch products that meet the evolving needs of its customers. With years of industry experience, cutting-edge technology, and a strong focus on sustainability, {Company Name} has positioned itself as a trusted provider of magnesite refractory brick solutions worldwide.Evolution of the Magnesite Refractory Bricks Industry:The magnesite refractory bricks industry has experienced remarkable advancements in recent years. Formerly, the dominant types of refractories used were chrome bricks, but due to environmental concerns related to hexavalent chromium, there has been a gradual shift towards magnesite refractory bricks, known for their high refractoriness and excellent chemical properties.The versatility of magnesite refractory bricks has driven their adoption in various industries, replacing traditional refractory materials. Modern manufacturing processes have been optimized to enhance the physical and chemical properties of these bricks, making them increasingly resistant to thermal shocks and the corrosive effects of chemicals found in harsh industrial environments.Technological Innovations and Product Enhancements:{Company Name} recognizes the importance of technological advancements in staying ahead in the highly competitive market. The company consistently invests in research and development, aiming to improve the performance and durability of magnesite refractory bricks. High-precision manufacturing techniques, such as hot pressing, enable {Company Name} to produce bricks with more consistent and superior quality, ensuring excellent resistance to thermal stress and prolonged service life.Furthermore, {Company Name}'s commitment to sustainable practices is reflected in its innovative use of environmentally friendly raw materials and energy-efficient processes. By incorporating recycled materials within its manufacturing process, the company aims to reduce its carbon footprint and contribute to a greener future.Meeting Industry-Specific Demands:As diverse industries pose unique challenges, {Company Name} understands the importance of customizing magnesite refractory brick solutions accordingly. For instance, in the steel industry, refractory materials are exposed to extreme temperatures and harsh conditions during the smelting process. To address these challenges, {Company Name} has developed advanced magnesite refractory bricks with superior thermal stability, minimizing material degradation and extending the overall service life of the refractories.Moreover, {Company Name}'s research and development team works closely with customers, providing technical support and developing tailored solutions specific to their requirements. This customer-centric approach has fostered strong and lasting partnerships with clients across the globe.Commitment to Quality and Customer Satisfaction:{Company Name}'s commitment to quality and customer satisfaction has propelled its position in the market. The company adheres to strict quality control procedures, guaranteeing that each magnesite refractory brick meets stringent international standards. Moreover, providing exceptional after-sales service and technical assistance ensures that customers maximize the value and performance of {Company Name}'s refractory solutions.Conclusion:The magnesite refractory bricks industry is witnessing transformational changes as sustainability, high performance, and customized solutions become paramount. {Company Name} is at the forefront of this evolution, delivering top-quality magnesite refractory bricks while embracing innovation and sustainable practices. With its unwavering commitment to customer satisfaction and its focus on technological advancements, {Company Name} is well-positioned to meet the ever-increasing demand for superior refractory materials in the global market.
How to Choose the Best Material for Your Refractory Casting Needs
Refractory Casting: Revolutionizing the Fireproof IndustryInnovation and constant evolution have always been fundamental aspects in the industrial world, and the fireproof industry is no exception. Refractory Casting has taken a step forward in this field, offering innovative solutions and products that have no competitors in terms of quality and durability. Focusing on their clients' needs, Refractory Casting has revolutionized the market by introducing high-end materials that can withstand extreme temperatures and workloads.Refractory Casting has quickly established itself as an important player in the refractory industry for its cutting-edge solutions, reliable quality, and outstanding service. Their products range from firebricks, insulating materials, mortar, and mineral wool to custom-made products that can meet even the most demanding requirements. The company is committed to productivity, safety, and cost-effectiveness, and its expertise is called upon in a variety of industries like steel, aluminum, cement, glass, and petrochemical.The company's mission is simple: "To offer excellence at a fair cost." This has been the philosophy behind Refractory Casting's business strategy, which prioritizes the quality of its products over everything else. The brand is synonymous with high-quality raw materials and expert craftsmanship, ensuring that its products always meet the highest standards in the industry.The company has multiple manufacturing plants across the globe, each specializing in different products. These plants are equipped with state-of-the-art machinery and follow strict safety and environmental protocols, ensuring that all workers and the environment are protected. Refractory Casting's products are tested rigorously and are certified by independent laboratories, guaranteeing their performance and durability.Refractory Casting's success is partially due to its ability to adapt to new challenges and demands. A testament to this is the company's recent contribution to the United States National Aeronautics and Space Administration's (NASA) 2020 Mars Rover mission. Refractory Casting provided the necessary materials for the rover's heat shield, making it possible for the rover to withstand the planet's harsh atmospheric conditions during its descent.In recent years, Refractory Casting has also been taking steps towards sustainability by developing environmentally friendly products and improving its manufacturing processes. The company has implemented programs to reduce energy consumption, waste, and emissions, while also increasing recycling rates and using sustainable raw materials.In summary, Refractory Casting is a leading player in the global refractory industry, thanks to its cutting-edge solutions, superior quality, and outstanding service. The company is committed to continuous innovation, productivity, safety, and cost-effectiveness, while also contributing to sustainability and being a reliable partner for various industries. The company's motto of "excellence at a fair cost" is reflected in every aspect of its business, and this is why Refractory Casting is a brand that clients can trust.
Understanding the Importance of Arc Furnace Electrodes: A Comprehensive Guide
Title: Advancements in Arc Furnace Electrodes Facilitate Efficient Steel ProductionIntroduction:In the constantly evolving steel industry where efficiency and sustainability are key, companies are continuously seeking innovative solutions to optimize their production processes. One such groundbreaking advancement lies in the development of state-of-the-art arc furnace electrodes. These cutting-edge electrodes, produced by a renowned industry leader {}, are revolutionizing steelmaking and paving the way towards more efficient and eco-friendly practices.[Company Introduction - Approx. 200 words]Starting its journey in the early 1980s, {} has emerged as a global frontrunner in manufacturing arc furnace electrodes. Their unwavering commitment to excellence, extensive research and development, and supplier collaborations have propelled them to the forefront of the industry. With a reputation for consistently delivering quality products, they have earned the trust and loyalty of their customers worldwide.The company's modern facility, equipped with the latest manufacturing technologies and operated by highly skilled professionals, enables {} to produce high-performance arc furnace electrodes. These electrodes are essential components in the electric arc furnace (EAF) process, a widely adopted method for steel production due to its flexibility and cost-effectiveness.[Advancement 1 - Approx. 200 words]In a significant breakthrough, {} has successfully developed a next-generation arc furnace electrode that offers exceptional performance and durability. Through innovative design modifications and advancements in raw materials, these electrodes demonstrate improved electrical conductivity, thermal resistance, and resistance to oxidation. As a result, steelmakers can benefit from increased productivity, reduced energy consumption, and minimized downtime during the steelmaking process.The enhanced electrical conductivity of {}'s arc furnace electrodes allows for efficient transfer of electricity from the power source to the furnace, enabling faster melting rates and shorter cycle times. Consequently, steel manufacturers observe enhanced productivity and optimization of their manufacturing operations, leading to significant cost savings and increased profits.Additionally, the improved thermal resistance characteristic of these electrodes ensures stable and consistent heat transfer within the electric arc furnace, resulting in reduced melting time and increased overall energy efficiency. The reduction in energy consumption not only minimizes production costs but also aligns with the industry's focus on sustainability and environmental consciousness.[Advancement 2 - Approx. 200 words]Another breakthrough achieved by {} is the development of arc furnace electrodes with enhanced resistance to oxidation, thereby prolonging their lifespan. Through meticulous testing and optimization, the company has successfully formulated electrode compositions that exhibit superior resistance to oxidation even under extreme operating conditions. This advancement allows for longer electrode life, minimizing costly downtime associated with regular electrode replacements.The extended lifespan of {}'s arc furnace electrodes is particularly advantageous for steel manufacturers, as frequent electrode changes disrupt production flow and result in substantial economic losses. By offering electrodes with exceptional resistance to oxidation, the company enables seamless operations, providing steel producers with a competitive edge.Conclusion:With steel manufacturing being a vital industry worldwide, advancements in arc furnace electrodes play a pivotal role in optimizing steel production processes. Through their dedication to innovation and excellence, {} has emerged as a frontrunner in electrode manufacturing, introducing state-of-the-art products that enhance productivity, energy efficiency, and sustainability.The continuous evolution of arc furnace electrodes demonstrates the industry's commitment to pushing technological boundaries and meeting the ever-growing global demand for steel. As companies like {} continue to invest in research and development, the steel industry can look forward to more efficient, cost-effective, and eco-friendly steelmaking processes in the future.
Demand for High-Quality Corundum Bricks Continues to Grow in Various Industries
Corundum Brick – The Ultimate Solution for High-Temperature ApplicationsCorundum brick is a type of refractory brick that is made from pure fused aluminum oxide. It is a high-quality refractory material that has excellent thermal shock resistance, high mechanical strength, and superior erosion resistance. This makes it an ideal solution for applications that involve high temperatures, such as in furnaces, kilns, and incinerators, among others.A leading manufacturer of corundum brick, has developed a unique process that involves sintering and high-pressure molding, which helps in producing high-density bricks with uniform strength and precise dimensions. These corundum bricks are designed to withstand extreme conditions, such as temperatures of up to 1800°C, making them perfect for use in industrial environments.The corundum brick is not only used for refractory linings in high-temperature applications but for other critical applications, as well. It also serves as a crucial component in the construction of other refractory products, like high-temperature furnace lining bricks, burners, and high-temperature insulating products.The manufacturing process of corundum brick involves a complex series of steps and requires specialized equipment and expertise. The raw materials are first mixed together with water to form a plastic mass, which is then molded into the desired shape using high-pressure equipment. The molded bricks are then fired at high temperatures in a high-temperature kiln. The final product is carefully inspected and undergoes quality checks to ensure that it meets the required specifications.Corundum brick is a cost-effective solution that offers many benefits to industries, including long-lasting durability, resistance to corrosion, high-temperature resistance, and excellent thermal stability. These characteristics make it an ideal material for use in the heavy industry, petrochemical, cement, steel, and other high-temperature applications.The corundum brick can withstand many hours of high-temperature exposure without losing its strength or structure, making it a reliable and durable choice for refractory linings. It requires less maintenance compared to other refractory materials and is easy to install.The corundum brick’s excellent thermal shock resistance enables it to withstand sudden changes in temperature. This characteristic makes it an ideal solution for environments where the temperature changes rapidly, causing other materials to expand, contract, or crack.The company, with years of experience in the production of corundum bricks, has gained a reputation as a reliable and trustworthy supplier. Their products are of the highest quality and meet industry standards. Moreover, the company offers customized solutions, tailoring their products to meet specific clients’ needs. They have a team of experienced technicians and engineers who provide prompt and reliable technical support to their clients.The corundum brick has revolutionized the high-temperature industry. The benefits it offers make it an ideal solution for refractory lining applications. It has significantly reduced the frequency of lining replacements. Additionally, the cost savings that come with using corundum brick has converted many industries into using it over other refractory materials.In conclusion, the corundum brick is an innovative solution that offers excellent thermal stability, high-temperature resistance, and superior performance. The manufacturing process that produces these bricks is complex and requires unique expertise. The bricks are highly durable, require less maintenance, and are easy to install. The corundum brick has set a new standard in the refractory industry, and the company's customized solutions and reliable technical support make it the preferred choice for industries that require exceptional quality materials. The corundum brick is a game-changer and will continue to set the benchmark for high-temperature applications.
High-Quality Mullite Bricks Now Available for Sale: Discover the Latest Advancements in Zircon Technology
Zircon Mullite Brick revolutionizes the refractory industry with its exceptional performance, durability, and resistance to high temperatures. The product has been widely used in various industries such as steel, ceramics, petrochemicals, and non-ferrous metals, where heat and chemical resistance are crucial.Zircon Mullite Brick is a high-quality refractory product made of high-purity zirconium oxide, aluminum oxide, and mullite. The combination of these materials offers excellent heat resistance, thermal shock resistance, and high strength. Moreover, the brick is not vulnerable to the corrosive effects of acids and alkalis, which makes it highly suitable for industrial applications.The manufacturing process of the product involves complex techniques and the use of advanced equipment. The raw materials undergo a process of grinding, mixing, molding, firing, and cutting, which ensures uniformity in dimension, density, and mechanical properties. The high-quality manufacturing process guarantees consistent performance and durability of the product, making it an ideal choice for customers.The company behind the production of Zircon Mullite Brick is a leading refractory material manufacturer in China. It has a long history of producing high-quality refractory products that meet the diverse needs of customers. The company has invested in research and development to improve its products and manufacturing processes continually. It has also been using technology to improve efficiency and reduce the environmental impact of its production.The company has strict quality control measures in place to ensure that its products meet international standards. It has obtained ISO 9001:2015, ISO 14001:2015, and OHSAS 18001:2007 certifications, which attest to its commitment to quality, safety, and environmental protection. The company also has a dedicated technical team that offers technical advice and assistance to customers, ensuring that they get optimum performance from the products.In recent years, the company has expanded its operations beyond China and has established a global presence. It has set up offices and warehouses in various countries, enabling it to serve customers around the world. The company has also adopted international marketing strategies to increase its visibility and reach out to more customers. With its high-quality products, competitive pricing, and excellent customer service, the company has become a preferred supplier of refractory materials to many industries.Zircon Mullite Brick is one of the company's flagship products, and it has received positive feedback from customers. The brick's exceptional performance, durability, and resistance to high temperatures have made it a popular choice in industries such as steel and ceramics. The product offers excellent value for money and is comparable to other top-tier refractory products in the market.In conclusion, Zircon Mullite Brick is a high-quality refractory product that has revolutionized the industry with its exceptional performance, durability, and resistance to high temperatures. The product is made by a leading refractory material manufacturer in China, which has a long history of producing high-quality refractory products. The company has strict quality control measures in place to ensure that its products meet international standards and has a dedicated technical team that offers technical advice and assistance to customers. With its global presence, competitive pricing, and excellent customer service, the company has become a preferred supplier of refractory materials to many industries.
Top-notch Insulation for Optimal Fire Safety - Reliable, High-performance Solution
Firebrick Insulation - Revolutionizing the Insulation IndustryFor many years, the insulation industry struggled to develop materials and solutions that could effectively withstand high temperatures and harsh environments. However, with the introduction of Firebrick Insulation, that has now become a thing of the past. This new and innovative insulation material is helping companies to greatly improve their energy efficiency and conserve resources. In this article, we take a closer look at this game-changing product.What is Firebrick Insulation?Firebrick Insulation is a unique insulation material that is specially designed to withstand high temperatures, humidity, and corrosive environments. It is made of premium quality refractory materials, such as silica, alumina, and magnesia, which are fired at high temperatures to create a solid, durable brick-like structure.The product has been specially formulated to provide outstanding thermal insulation, while also offering excellent resistance to thermal shock, abrasion, and corrosion. This makes it an ideal solution for various industrial applications, including steel production, cement manufacturing, petrochemical processing, and power generation.What Makes Firebrick Insulation Different?One of the biggest advantages of using Firebrick Insulation is its durability and longevity. Unlike traditional insulation materials, which tend to break down over time, Firebrick Insulation can last for many years without deteriorating. This means that companies can save on maintenance costs and reduce their carbon footprint by avoiding the need for frequent replacement.Another key benefit of Firebrick Insulation is its exceptional insulating properties. With a thermal conductivity rating of just 0.15 W/mK, it is one of the most efficient insulation materials available, meaning it can help companies to significantly reduce their energy consumption and lower their operating costs.Firebrick Insulation is also highly versatile and can be used for a wide range of applications. It can withstand temperatures of up to 1700 °C, making it suitable for use in high-temperature furnaces, kilns, and reactors. It can also be used as a lining material for pipework, tanks, and vessels, providing superior protection against chemical corrosion and erosion.Company Introduction:Firebrick Insulation is a product developed and manufactured by Insulation Technologies, a leading insulation solutions provider with over 30 years of industry experience. Based in the United States, Insulation Technologies has become a trusted partner for many businesses around the world, offering customized insulation solutions that meet the unique needs of each customer.The company’s unrivaled expertise and commitment to excellence has made it a top choice for companies looking to improve their energy efficiency, reduce waste, and lower their carbon footprint. With a dedicated team of experts, Insulation Technologies provides comprehensive insulation services, from design and engineering to product development, manufacturing, and installation.Final ThoughtsFirebrick Insulation is a game-changing product that is revolutionizing the insulation industry. Its exceptional thermal insulation properties, combined with its durability, longevity, and versatility, make it an ideal solution for companies looking to increase their energy efficiency, reduce their operating costs, and improve their bottom line.If you’re interested in learning more about Firebrick Insulation, or to find out how Insulation Technologies can help you optimize your insulation solutions, please visit their website at www.insulationtechnologies.com or contact their customer service team at 1-800-123-4567.
Discover the Benefits of High Alumina Bricks for Industrial Applications
High Alumina Bricks: A New Era of Durability and PerformanceIn the ever-evolving world of construction materials, High Alumina Bricks have emerged as a game-changer. Renowned for their exceptional durability and performance, these bricks are revolutionizing the way we approach industrial applications. One company leading the charge is {Company Name}, a pioneering manufacturer in the field. With their cutting-edge technology and unwavering commitment to quality, they are setting new industry standards and elevating the construction landscape to new heights.At its core, High Alumina Bricks are composed of high-purity alumina, a premium raw material renowned for its excellent refractory properties. These bricks are designed to withstand high temperatures, making them ideal for use in industries such as steel, cement, glass, and petrochemicals, where extreme heat is a constant challenge. Their ability to resist thermal spalling, corrosion, and thermal shock sets them apart from traditional refractory bricks, allowing for longer service life and reduced maintenance costs.{Company Name} has invested heavily in research and development, resulting in a state-of-the-art manufacturing process that produces High Alumina Bricks with unmatched quality and consistency. By utilizing advanced hydraulic presses and precision temperature control, they ensure that every brick adheres to the highest industry standards. These carefully curated manufacturing techniques guarantee high mechanical strength, low shrinkage, and excellent thermal stability, even under the harshest operating conditions.One of the most remarkable features of High Alumina Bricks is their ability to retain their strength and integrity at elevated temperatures. With a high melting point, these bricks can withstand temperatures of up to 1800°C, making them a reliable choice for industries operating in extreme environments. This unique characteristic enables safer and more efficient processes, reducing downtime and increasing productivity. High Alumina Bricks act as a barrier against heat transfer, minimizing energy losses and contributing to overall cost savings for industrial operations.{Company Name}, with its cutting-edge technology and emphasis on sustainability, has also refined the production of High Alumina Bricks with a reduced environmental footprint. By implementing energy-efficient systems and utilizing raw materials from sustainable sources, they have successfully lowered greenhouse gas emissions and minimized waste generation. Their commitment to environmental stewardship is in line with the growing global demand for eco-conscious construction materials.The many advantages of High Alumina Bricks have led to their increased adoption across various industries. In the steel manufacturing sector, these bricks are widely utilized in blast furnaces, hot blast stoves, and other high-temperature areas. In the cement industry, High Alumina Bricks have become crucial components of rotary kilns and preheating zones. Additionally, glass manufacturers rely on these bricks for their excellent resistance to molten glass corrosion. The oil and gas industry has also embraced High Alumina Bricks for lining fluid catalytic cracking units and other high-temperature vessels.With ongoing advancements in technology, the future of High Alumina Bricks looks even more promising. Researchers are exploring innovative ways to enhance the thermal insulation properties of these bricks, further maximizing their efficiency and reducing energy consumption. As industries strive for increased productivity and sustainability, High Alumina Bricks are set to play a pivotal role in transforming industrial processes.In conclusion, High Alumina Bricks have emerged as a game-changer in the construction materials industry, combining exceptional durability, unmatched performance, and sustainability. {Company Name}'s commitment to innovation and superior quality has positioned them as a leader in this field. As industries continue to seek reliable solutions for their high-temperature challenges, High Alumina Bricks will undoubtedly pave the way for a new era of durability and performance.
Durable Fire Bricks for Heavy Duty Applications - A Comprehensive Guide
Heavy Duty Fire Brick: Providing Reliable Solutions for High-Temperature ApplicationsIn the world of industrial manufacturing, dealing with high-temperature environments is a constant challenge. From steel mills to kilns, there is a pressing need for materials that can withstand extreme temperatures while maintaining structural integrity. This is where Heavy Duty Fire Brick (brand name removed) comes into the picture.With their exceptional heat resistance properties, Heavy Duty Fire Brick has become a trusted name in the industry, providing reliable solutions for a wide range of high-temperature applications. Let's delve deeper into the company's background, innovative approaches, and the key factors that set them apart from their competitors.Company Introduction:Heavy Duty Fire Brick, a leading manufacturer of refractory products, has been catering to the diverse needs of industries worldwide for over two decades. The company prides itself on delivering top-notch solutions that are engineered to withstand the harshest conditions.Their state-of-the-art manufacturing facilities utilize advanced technology, enabling them to produce fire bricks of various grades and specifications with exceptional precision. Additionally, Heavy Duty Fire Brick employs a team of highly experienced engineers and technicians who are dedicated to ensuring the company's products meet and exceed industry standards.Innovation in Fire Brick Technology:One of the key factors that sets Heavy Duty Fire Brick apart from its competitors is their commitment to innovation. The company continually invests in research and development to enhance the performance of their fire bricks and introduce new products to meet evolving industry requirements.Heavy Duty Fire Brick has developed unique formulations that optimize the balance between heat resistance and mechanical strength. Their bricks are engineered to withstand temperatures up to 3000°F (1650°C), making them ideal for applications such as furnaces, boilers, and incinerators.The company also prides itself on its customized solutions. Heavy Duty Fire Brick understands that each industry and application has specific needs, which is why they work closely with customers to develop tailored fire brick solutions. This collaborative approach ensures that clients receive products that not only meet their requirements but also contribute to increased efficiency, reduced downtime, and improved safety.Quality Assurance:At Heavy Duty Fire Brick, quality is of paramount importance. Each manufacturing process undergoes strict quality control measures to ensure that their products consistently meet the highest standards. The company uses raw materials sourced from accredited suppliers and meticulously tests the fire bricks at various stages of production to guarantee their performance and durability.Furthermore, Heavy Duty Fire Brick has a dedicated team of quality assurance professionals who conduct rigorous inspections and audits. This approach ensures that the final product is flawless and ready to withstand the most demanding high-temperature environments.Environmental Responsibility:In addition to providing reliable and innovative solutions, Heavy Duty Fire Brick is committed to minimizing its environmental impact. The company adheres to strict environmental regulations and adopts sustainable practices throughout its operations.Heavy Duty Fire Brick utilizes energy-efficient manufacturing processes and minimizes waste generation to reduce its carbon footprint. Additionally, the company actively promotes recycling and reusing materials whenever possible.Conclusion:Heavy Duty Fire Brick's dedication to delivering reliable solutions for high-temperature applications, combined with their commitment to innovation, quality, and environmental responsibility, has cemented their position as a trusted partner for industries around the globe. Their fire bricks continue to exceed expectations and provide invaluable support to industries operating in extreme temperature conditions.As the demand for high-temperature solutions grows, Heavy Duty Fire Brick is well-equipped to meet the challenges of the future with their ongoing commitment to excellence and their ability to provide tailored solutions for every customer's needs.
Shop High-Quality Castable Refractory for Your Industrial Needs
Castable refractory is a crucial component in a wide range of industries, including steel manufacturing, cement production, and even petrochemical processing. This versatile material is used to line various types of furnaces, incinerators, and kilns, with its primary purpose being to withstand high temperatures and prevent contaminants from infiltrating the surrounding environment. With castable refractory being such an essential product for many businesses, finding a reliable supplier is crucial for ensuring smooth and trouble-free operations.If you are in the market for high-quality, durable castable refractory, {company name} is an industry-leading supplier that can meet all of your needs. With a reputation built on quality, reliability, and customer satisfaction, they are the go-to choice for discerning businesses that demand the best.{Company name} has been in the castable refractory business for over {number of years} years, during which they have honed their craft and built a solid reputation for excellence. Their products are made from the finest materials and are crafted using advanced manufacturing techniques, resulting in an end product that is highly resistant to wear and tear, corrosion, and thermal shock.Whether you need castable refractory for a large-scale industrial application or a smaller project, {company name} has a wide range of products to choose from. Their vast inventory includes high-temperature insulating materials, dense refractory castables, and low-cement castables, to name just a few. They pride themselves on being able to provide customized solutions to meet their clients' specific needs, and their team of experts is always on hand to provide advice and technical support.But {company name} isn't just about supplying top-quality castable refractory. They are also committed to providing exceptional customer service and support. Their knowledgeable staff is always ready to answer any questions or concerns you may have, and they work closely with clients to ensure that their products are delivered on time and within budget. With {company name}, you can be confident that you are dealing with a reputable, trustworthy company that puts your needs first.Furthermore, {company name} is committed to sustainability and reducing its environmental footprint. They use innovative manufacturing techniques and employ a closed-loop system that recycles waste materials, minimizing their impact on the environment. By choosing {company name} as your supplier, you can be confident that you are working with a company that cares about the environment and is doing its part to protect our planet.In conclusion, castable refractory is an essential component in many industrial processes, and selecting a reliable supplier is crucial for ensuring smooth and trouble-free operations. With over {number of years} years of experience in the industry, a commitment to quality and sustainability, and unparalleled customer service, {company name} is the go-to choice for businesses that demand the best. Contact them today to see how they can meet your castable refractory needs.