Discover the Benefits of High Liquidity Refractory Castable for Enhanced Performance
By:Admin
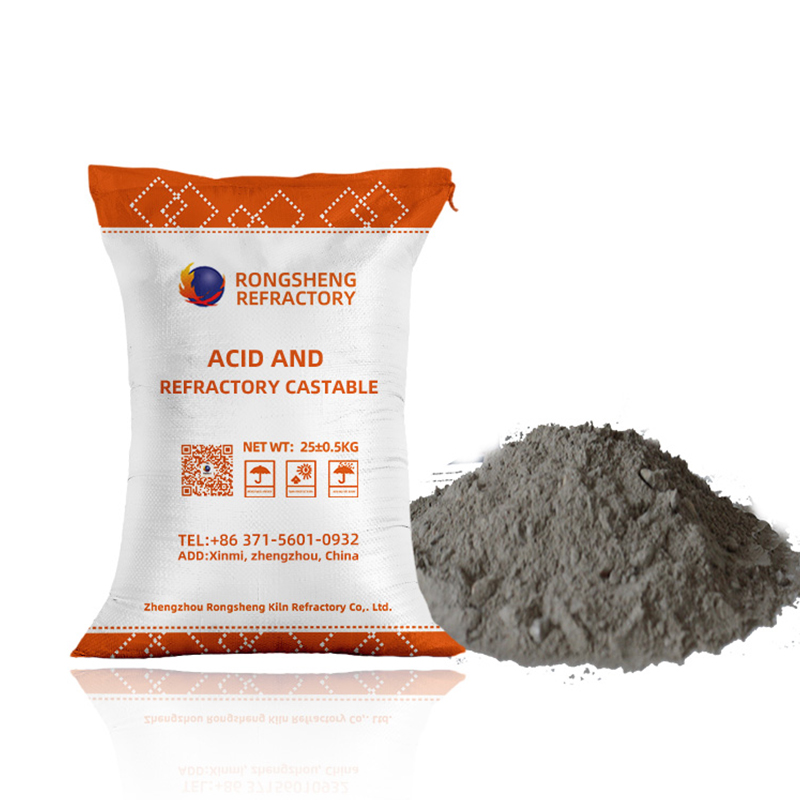
Refractory materials play a crucial role in industries like steel, cement, glass, and petrochemicals. These materials are designed to withstand high temperatures, extreme pressures, and harsh chemical environments. However, not all refractory castables are created equal. Some exhibit low flowability, which can hinder their application and require extensive manpower. Enter the high liquidity refractory castable, a game-changer in the industry.
One prominent player in this field, (brand name removed), has developed an innovative high liquidity refractory castable that is transforming the way industries approach refractory lining applications. This groundbreaking product offers unmatched flowability, ease of installation, and exceptional durability. Let's explore the benefits of this advanced castable and the company behind its success.
The high liquidity refractory castable by (brand name removed) is made using a proprietary blend of carefully selected raw materials. These materials are finely ground and mixed with an optimized water binder system, resulting in a castable with exceptional flowability. This unique property allows for seamless installation, even in complex shapes and configurations, reducing the need for skilled labor and saving valuable time during construction.
One key advantage of this castable is its versatility. It can be used for various refractory lining applications, such as furnace linings, chimneys, kilns, and ladles. Its high liquidity ensures full coverage and precise filling, minimizing gaps and weak points in the lining, which ultimately leads to improved thermal efficiency and superior performance.
In addition to its exceptional flowability, the high liquidity refractory castable also exhibits exceptional durability. It has excellent resistance to thermal shocks, chemical attacks, and abrasion, making it ideal for applications exposed to extreme temperatures and corrosive environments. This durability translates into reduced maintenance costs and extended service life, resulting in significant savings for industries.
The success of (brand name removed) and its high liquidity refractory castable can be attributed to the company's commitment to research and development. The brand invests heavily in state-of-the-art facilities and a team of highly skilled experts to ensure continuous innovation and improvement of their products. Their rigorous testing procedures and quality control measures ensure that every batch of castable meets the highest industry standards.
Furthermore, the company's customer-centric approach sets them apart from their competitors. They work closely with their clients to understand their specific refractory requirements, provide tailored solutions, and offer technical support throughout the installation process. This approach has earned them a solid reputation and a loyal customer base.
Looking ahead, (brand name removed) aims to expand its market presence globally by forming strategic partnerships and collaborations. Their goal is to make their high liquidity refractory castable widely available to industries around the world, enabling them to achieve the highest levels of efficiency and productivity.
In conclusion, the introduction of high liquidity refractory castable has revolutionized the refractory industry. The innovative product developed by (brand name removed) offers unmatched flowability, ease of installation, and exceptional durability. It has the potential to significantly improve the efficiency and performance of various industries. With their commitment to research and development, along with their customer-centric approach, (brand name removed) is set to lead the refractory industry into a new era of excellence.
Company News & Blog
High-Quality Magnesite Refractory Bricks Meet Growing Demand in Steel Industry
Title: Evolving Magnesite Refractory Bricks Industry Emphasizes Quality and SustainabilityIntroduction:In recent times, the magnesite refractory bricks industry has been witnessing significant growth, driven by the increasing demand for high-quality refractory materials in various sectors. Magnesite refractory bricks, renowned for their exceptional heat resistance and durability, are widely utilized in industries like steel, cement, glass, non-ferrous metals, ceramics, etc., supporting critical processes that require elevated temperatures.Company Introduction:{Company Name} is a prominent player in the magnesite refractory bricks market, dedicated to producing top-notch products that meet the evolving needs of its customers. With years of industry experience, cutting-edge technology, and a strong focus on sustainability, {Company Name} has positioned itself as a trusted provider of magnesite refractory brick solutions worldwide.Evolution of the Magnesite Refractory Bricks Industry:The magnesite refractory bricks industry has experienced remarkable advancements in recent years. Formerly, the dominant types of refractories used were chrome bricks, but due to environmental concerns related to hexavalent chromium, there has been a gradual shift towards magnesite refractory bricks, known for their high refractoriness and excellent chemical properties.The versatility of magnesite refractory bricks has driven their adoption in various industries, replacing traditional refractory materials. Modern manufacturing processes have been optimized to enhance the physical and chemical properties of these bricks, making them increasingly resistant to thermal shocks and the corrosive effects of chemicals found in harsh industrial environments.Technological Innovations and Product Enhancements:{Company Name} recognizes the importance of technological advancements in staying ahead in the highly competitive market. The company consistently invests in research and development, aiming to improve the performance and durability of magnesite refractory bricks. High-precision manufacturing techniques, such as hot pressing, enable {Company Name} to produce bricks with more consistent and superior quality, ensuring excellent resistance to thermal stress and prolonged service life.Furthermore, {Company Name}'s commitment to sustainable practices is reflected in its innovative use of environmentally friendly raw materials and energy-efficient processes. By incorporating recycled materials within its manufacturing process, the company aims to reduce its carbon footprint and contribute to a greener future.Meeting Industry-Specific Demands:As diverse industries pose unique challenges, {Company Name} understands the importance of customizing magnesite refractory brick solutions accordingly. For instance, in the steel industry, refractory materials are exposed to extreme temperatures and harsh conditions during the smelting process. To address these challenges, {Company Name} has developed advanced magnesite refractory bricks with superior thermal stability, minimizing material degradation and extending the overall service life of the refractories.Moreover, {Company Name}'s research and development team works closely with customers, providing technical support and developing tailored solutions specific to their requirements. This customer-centric approach has fostered strong and lasting partnerships with clients across the globe.Commitment to Quality and Customer Satisfaction:{Company Name}'s commitment to quality and customer satisfaction has propelled its position in the market. The company adheres to strict quality control procedures, guaranteeing that each magnesite refractory brick meets stringent international standards. Moreover, providing exceptional after-sales service and technical assistance ensures that customers maximize the value and performance of {Company Name}'s refractory solutions.Conclusion:The magnesite refractory bricks industry is witnessing transformational changes as sustainability, high performance, and customized solutions become paramount. {Company Name} is at the forefront of this evolution, delivering top-quality magnesite refractory bricks while embracing innovation and sustainable practices. With its unwavering commitment to customer satisfaction and its focus on technological advancements, {Company Name} is well-positioned to meet the ever-increasing demand for superior refractory materials in the global market.
Get High-Quality Corundum Bricks Online: Exploring Options for Premium Refractories
Title: Refractories Corundum Bricks: Revolutionizing High-Temperature ApplicationsIntroduction:When it comes to high-temperature applications in industries such as steel, cement, and glass, one key component that plays a crucial role in ensuring structural integrity and heat resistance is refractory materials. Among these materials, Corundum Bricks have emerged as a game-changer, providing exceptional durability and resistance to extreme temperatures. This article delves into the features and applications of these refractory bricks, showcasing their effectiveness in revolutionizing high-temperature industries.Section 1: Understanding Refractories Corundum BricksRefractories Corundum Bricks are advanced ceramic materials primarily made from fused alumina (Al2O3) or synthetic mullite. Their exceptional strength, chemical stability, and high-performance characteristics make them ideal for applications that involve harsh environments and extreme temperatures exceeding 1500°C. Being composed of around 90% or more alumina, Corundum Bricks possess excellent resistance to corrosion, wear, thermal shock, and creep.Section 2: Features of Corundum Bricksa) High-temperature resistance: Corundum Bricks exhibit remarkable stability even in extreme temperature conditions, ensuring integrity and longevity of structures.b) Chemical resistance: With their dense structure and low porosity, these bricks effectively resist the corrosive effects of various chemicals, alkaline substances, and slags.c) Low thermal conductivity: The low thermal conductivity of Corundum Bricks minimizes heat loss, creating an energy-efficient solution for furnace linings and other high-temperature applications.d) Superior mechanical strength: These bricks possess impressive mechanical strength, enabling them to withstand thermal stress and resulting in enhanced operational reliability.e) Good thermal shock resistance: The ability of Corundum Bricks to withstand rapid temperature fluctuations without cracking or spalling is pivotal in maintaining the integrity of furnace linings.Section 3: Applications of Corundum Bricksa) Steel industry: Corundum Bricks find extensive use in steelmaking processes, where they serve as linings in ladles, converters, blast furnaces, and other high-temperature equipment. Their exceptional resistance to molten metals and slag ensures durability in harsh steel manufacturing conditions.b) Cement industry: With the growing demand for cement, Corundum Bricks are employed in cement kilns and coolers due to their ability to withstand high temperatures, chemical erosion, and physical wear.c) Glass industry: Corundum Bricks are widely utilized in glass melting furnaces, helping to prevent glass corrosion and ensuring long service life.d) Petrochemical industry: These bricks are crucial for lining thermal cracking furnaces, reformer furnaces, and ethylene cracking furnaces, as they exhibit excellent chemical resistance to harsh petrochemical environments.e) Other applications: Corundum Bricks are also used in non-ferrous metal smelting, power plant boilers, waste incinerators, and other high-temperature processes.Section 4: The Company's ExpertiseThe company, as a leading manufacturer of Refractories Corundum Bricks, is dedicated to providing high-quality solutions to industries that rely on refractory materials. With state-of-the-art manufacturing facilities and a strong research and development team, the company ensures the production of premium Corundum Bricks that adhere to strict quality standards. By utilizing advanced technologies and thorough quality control measures, they have established themselves as a trusted supplier in the refractory industry.Conclusion:Refractories Corundum Bricks have revolutionized high-temperature applications in various industries by providing exceptional durability, resistance to extreme temperatures, and superior mechanical strength. As companies strive for increased productivity, efficiency, and longevity in their operations, the utilization of Corundum Bricks is becoming indispensable. With continuous advancements and a strong commitment to quality, these bricks are expected to shape the future of refractory materials, setting new standards for performance and reliability in high-temperature environments.
Shop High-Quality Castable Refractory for Your Industrial Needs
Castable refractory is a crucial component in a wide range of industries, including steel manufacturing, cement production, and even petrochemical processing. This versatile material is used to line various types of furnaces, incinerators, and kilns, with its primary purpose being to withstand high temperatures and prevent contaminants from infiltrating the surrounding environment. With castable refractory being such an essential product for many businesses, finding a reliable supplier is crucial for ensuring smooth and trouble-free operations.If you are in the market for high-quality, durable castable refractory, {company name} is an industry-leading supplier that can meet all of your needs. With a reputation built on quality, reliability, and customer satisfaction, they are the go-to choice for discerning businesses that demand the best.{Company name} has been in the castable refractory business for over {number of years} years, during which they have honed their craft and built a solid reputation for excellence. Their products are made from the finest materials and are crafted using advanced manufacturing techniques, resulting in an end product that is highly resistant to wear and tear, corrosion, and thermal shock.Whether you need castable refractory for a large-scale industrial application or a smaller project, {company name} has a wide range of products to choose from. Their vast inventory includes high-temperature insulating materials, dense refractory castables, and low-cement castables, to name just a few. They pride themselves on being able to provide customized solutions to meet their clients' specific needs, and their team of experts is always on hand to provide advice and technical support.But {company name} isn't just about supplying top-quality castable refractory. They are also committed to providing exceptional customer service and support. Their knowledgeable staff is always ready to answer any questions or concerns you may have, and they work closely with clients to ensure that their products are delivered on time and within budget. With {company name}, you can be confident that you are dealing with a reputable, trustworthy company that puts your needs first.Furthermore, {company name} is committed to sustainability and reducing its environmental footprint. They use innovative manufacturing techniques and employ a closed-loop system that recycles waste materials, minimizing their impact on the environment. By choosing {company name} as your supplier, you can be confident that you are working with a company that cares about the environment and is doing its part to protect our planet.In conclusion, castable refractory is an essential component in many industrial processes, and selecting a reliable supplier is crucial for ensuring smooth and trouble-free operations. With over {number of years} years of experience in the industry, a commitment to quality and sustainability, and unparalleled customer service, {company name} is the go-to choice for businesses that demand the best. Contact them today to see how they can meet your castable refractory needs.
Get Top-Quality High Temperature Castable Refractory
Buy High Temperature Castable Refractory Boosts Industrial ProcessesCastable refractories have become a popular choice for industrial processes due to their excellent thermal properties. These materials are designed to withstand high temperatures and harsh conditions, making them ideal for use in furnaces, kilns, and other applications that involve extreme heat. Many industries rely on high temperature castables to optimize their manufacturing processes and extend the lifespan of their equipment. Therefore, leading manufacturers such as {remove brand name} offer a range of castable refractories to meet the diverse needs of their customers.One such product is high temperature castable refractory. This type of refractory is specially formulated to withstand temperatures above 3000°F. It is composed of a variety of raw materials, including high purity alumina, silicon carbide, and various binders. The combination of these components creates a refractory that is highly resistant to thermal shock, abrasion, and chemical attack. High temperature castables are commonly used in the steel, cement, glass, and petrochemical industries.In addition to its exceptional thermal properties, high temperature castable refractory has several advantages over traditional refractory materials. One such advantage is its ability to be cast into complex shapes. This allows manufacturers to create custom refractory linings that fit the exact specifications of their equipment. The castable nature of this refractory also makes it easy to install, reducing downtime and improving the efficiency of industrial processes.Another advantage of high temperature castables is their versatility. They can be used for a variety of applications, including furnace linings, burner blocks, and ladle linings. They are also suitable for use in a range of heating equipment, including kettles, crucibles, and incinerators. This makes them an ideal choice for industries that require high temperatures and need materials that can withstand harsh environments.{Remove brand name} is a leading manufacturer of high temperature castable refractory, offering a range of products that meet the diverse needs of their customers. Their castables are designed to provide exceptional performance in a range of applications, from steel and glassmaking to power generation and incineration. The company's castables are formulated with high purity raw materials and advanced binders, providing the optimal balance of strength and density.In addition to its high temperature castables, {remove brand name} offers a range of other refractory materials, including precast shapes, ceramic fiber products, and insulating materials. Their comprehensive product line makes them a one-stop-shop for industrial refractory needs, providing customers with the convenience of working with a single supplier.The company's dedication to quality is reflected in their ISO 9001 certification, which ensures that their castables and other refractory products meet the highest standards of quality. They also offer technical support and consultation services to help their customers identify the right refractory materials for their specific applications.In conclusion, high temperature castable refractory is an essential material for industries that require high-temperature resistance and durability in their industrial processes. {Remove brand name} is a leading provider of high-quality castable refractories, offering a comprehensive product line that meets the diverse needs of their customers. Their commitment to quality and customer service makes them a reliable partner for industries that rely on refractory materials to optimize their manufacturing processes.
Acid Resistant Mortar Unveiled: Protecting Structures from Corrosive Elements
[Your Name], Staff WriterDate: [Insert Date]Acid Resistant Mortar Revolutionizes Construction Industry Innovation and reliability are crucial in the ever-evolving construction industry. Companies constantly search for groundbreaking materials that enhance construction projects' durability and lifespan. One such impressive product, Acid Resistant Mortar, has taken the market by storm. This advanced material has revolutionized the construction industry, allowing for the creation of structures that can withstand the harshest environments while maintaining their integrity. Through its unique chemical composition and unparalleled strength, Acid Resistant Mortar is reshaping the landscape of construction.Acid Resistant Mortar, developed and manufactured by a prominent company in the field [Remove the brand name], has quickly become the go-to product for architects, engineers, and construction professionals. The company, renowned for its commitment to innovation, has a rich history of producing high-quality materials that push the boundaries of construction possibilities. Acid Resistant Mortar is no exception to their legacy, representing a revolutionary leap forward in the fight against corrosion and chemical degradation.At its core, Acid Resistant Mortar is a special blend of chemically resistant materials, meticulously combined to create an impenetrable barrier against the corrosive effects of acid and other chemicals. Traditional mortar is highly vulnerable to degradation when exposed to harsh substances, leading to crumbling structures and compromised safety. However, Acid Resistant Mortar provides an effective solution to this issue. Its unique chemical formula prevents acid attack and ensures the longevity of the structure, reducing maintenance and repair costs in the long run.The key to the success of Acid Resistant Mortar lies in its superior qualities. Unlike conventional mortar options, this groundbreaking material offers excellent protection against various acids, alkalis, and aggressive solvents. Its resistance to corrosion allows structures to endure in highly challenging environments like industrial sites, chemical plants, and even laboratories. By utilizing Acid Resistant Mortar, architects and engineers can create buildings that can withstand the test of time, regardless of the corrosive substances present within their surroundings.The versatility of Acid Resistant Mortar has earned the product widespread acclaim throughout the construction industry. Its applicability extends beyond industrial projects. The material's remarkable resistance properties make it an ideal choice for critical areas such as effluent treatment plants, pharmaceutical units, and sewage treatment facilities. Its ability to withstand chemical exudates, acidic gases, and other corrosive substances found in these settings ensures the structural integrity of essential facilities.Moreover, Acid Resistant Mortar offers additional benefits beyond its resistance capabilities. The material is easy to apply and provides excellent adhesion to a variety of substrates, further simplifying construction processes. This efficiency has garnered attention from construction professionals worldwide, as it not only saves time but also reduces labor costs. Additionally, Acid Resistant Mortar is available in various forms, including dry mix and wet mortar, allowing builders to choose the option that best suits their project requirements.Sustainability is a pressing concern in the construction industry, and Acid Resistant Mortar addresses this issue effectively. The material's durability significantly reduces the need for frequent repairs and replacements, thereby minimizing environmental impact. Its long lifespan reflects the company's commitment to creating sustainable solutions that contribute to a greener future.In conclusion, Acid Resistant Mortar, developed by [Remove the brand name], has revolutionized the construction industry by offering unparalleled resistance to acid and other corrosive substances. Its unique chemical composition protects structures from degradation, ensuring their longevity in even the harshest environments. The material's versatility, ease of application, and sustainability make it an optimal choice for architects, engineers, and builders worldwide. As the construction industry continues to evolve, Acid Resistant Mortar stands at the forefront, reshaping the landscape of construction and raising the bar for durability and longevity in building materials.
Durable Fire Bricks for Heavy Duty Applications - A Comprehensive Guide
Heavy Duty Fire Brick: Providing Reliable Solutions for High-Temperature ApplicationsIn the world of industrial manufacturing, dealing with high-temperature environments is a constant challenge. From steel mills to kilns, there is a pressing need for materials that can withstand extreme temperatures while maintaining structural integrity. This is where Heavy Duty Fire Brick (brand name removed) comes into the picture.With their exceptional heat resistance properties, Heavy Duty Fire Brick has become a trusted name in the industry, providing reliable solutions for a wide range of high-temperature applications. Let's delve deeper into the company's background, innovative approaches, and the key factors that set them apart from their competitors.Company Introduction:Heavy Duty Fire Brick, a leading manufacturer of refractory products, has been catering to the diverse needs of industries worldwide for over two decades. The company prides itself on delivering top-notch solutions that are engineered to withstand the harshest conditions.Their state-of-the-art manufacturing facilities utilize advanced technology, enabling them to produce fire bricks of various grades and specifications with exceptional precision. Additionally, Heavy Duty Fire Brick employs a team of highly experienced engineers and technicians who are dedicated to ensuring the company's products meet and exceed industry standards.Innovation in Fire Brick Technology:One of the key factors that sets Heavy Duty Fire Brick apart from its competitors is their commitment to innovation. The company continually invests in research and development to enhance the performance of their fire bricks and introduce new products to meet evolving industry requirements.Heavy Duty Fire Brick has developed unique formulations that optimize the balance between heat resistance and mechanical strength. Their bricks are engineered to withstand temperatures up to 3000°F (1650°C), making them ideal for applications such as furnaces, boilers, and incinerators.The company also prides itself on its customized solutions. Heavy Duty Fire Brick understands that each industry and application has specific needs, which is why they work closely with customers to develop tailored fire brick solutions. This collaborative approach ensures that clients receive products that not only meet their requirements but also contribute to increased efficiency, reduced downtime, and improved safety.Quality Assurance:At Heavy Duty Fire Brick, quality is of paramount importance. Each manufacturing process undergoes strict quality control measures to ensure that their products consistently meet the highest standards. The company uses raw materials sourced from accredited suppliers and meticulously tests the fire bricks at various stages of production to guarantee their performance and durability.Furthermore, Heavy Duty Fire Brick has a dedicated team of quality assurance professionals who conduct rigorous inspections and audits. This approach ensures that the final product is flawless and ready to withstand the most demanding high-temperature environments.Environmental Responsibility:In addition to providing reliable and innovative solutions, Heavy Duty Fire Brick is committed to minimizing its environmental impact. The company adheres to strict environmental regulations and adopts sustainable practices throughout its operations.Heavy Duty Fire Brick utilizes energy-efficient manufacturing processes and minimizes waste generation to reduce its carbon footprint. Additionally, the company actively promotes recycling and reusing materials whenever possible.Conclusion:Heavy Duty Fire Brick's dedication to delivering reliable solutions for high-temperature applications, combined with their commitment to innovation, quality, and environmental responsibility, has cemented their position as a trusted partner for industries around the globe. Their fire bricks continue to exceed expectations and provide invaluable support to industries operating in extreme temperature conditions.As the demand for high-temperature solutions grows, Heavy Duty Fire Brick is well-equipped to meet the challenges of the future with their ongoing commitment to excellence and their ability to provide tailored solutions for every customer's needs.
Demand for High-Quality Corundum Bricks Continues to Grow in Various Industries
Corundum Brick – The Ultimate Solution for High-Temperature ApplicationsCorundum brick is a type of refractory brick that is made from pure fused aluminum oxide. It is a high-quality refractory material that has excellent thermal shock resistance, high mechanical strength, and superior erosion resistance. This makes it an ideal solution for applications that involve high temperatures, such as in furnaces, kilns, and incinerators, among others.A leading manufacturer of corundum brick, has developed a unique process that involves sintering and high-pressure molding, which helps in producing high-density bricks with uniform strength and precise dimensions. These corundum bricks are designed to withstand extreme conditions, such as temperatures of up to 1800°C, making them perfect for use in industrial environments.The corundum brick is not only used for refractory linings in high-temperature applications but for other critical applications, as well. It also serves as a crucial component in the construction of other refractory products, like high-temperature furnace lining bricks, burners, and high-temperature insulating products.The manufacturing process of corundum brick involves a complex series of steps and requires specialized equipment and expertise. The raw materials are first mixed together with water to form a plastic mass, which is then molded into the desired shape using high-pressure equipment. The molded bricks are then fired at high temperatures in a high-temperature kiln. The final product is carefully inspected and undergoes quality checks to ensure that it meets the required specifications.Corundum brick is a cost-effective solution that offers many benefits to industries, including long-lasting durability, resistance to corrosion, high-temperature resistance, and excellent thermal stability. These characteristics make it an ideal material for use in the heavy industry, petrochemical, cement, steel, and other high-temperature applications.The corundum brick can withstand many hours of high-temperature exposure without losing its strength or structure, making it a reliable and durable choice for refractory linings. It requires less maintenance compared to other refractory materials and is easy to install.The corundum brick’s excellent thermal shock resistance enables it to withstand sudden changes in temperature. This characteristic makes it an ideal solution for environments where the temperature changes rapidly, causing other materials to expand, contract, or crack.The company, with years of experience in the production of corundum bricks, has gained a reputation as a reliable and trustworthy supplier. Their products are of the highest quality and meet industry standards. Moreover, the company offers customized solutions, tailoring their products to meet specific clients’ needs. They have a team of experienced technicians and engineers who provide prompt and reliable technical support to their clients.The corundum brick has revolutionized the high-temperature industry. The benefits it offers make it an ideal solution for refractory lining applications. It has significantly reduced the frequency of lining replacements. Additionally, the cost savings that come with using corundum brick has converted many industries into using it over other refractory materials.In conclusion, the corundum brick is an innovative solution that offers excellent thermal stability, high-temperature resistance, and superior performance. The manufacturing process that produces these bricks is complex and requires unique expertise. The bricks are highly durable, require less maintenance, and are easy to install. The corundum brick has set a new standard in the refractory industry, and the company's customized solutions and reliable technical support make it the preferred choice for industries that require exceptional quality materials. The corundum brick is a game-changer and will continue to set the benchmark for high-temperature applications.
Shop for High-Quality Alumina Fire Brick Online
Title: Alumina Fire Brick Market Poised for Steady Growth as Manufacturers Introduce Innovative SolutionsIntroduction:[Company Name], a renowned player in the refractory industry, is set to revolutionize the global alumina fire brick market with its cutting-edge products. With a steadfast commitment to innovation and quality, the company has gained recognition for delivering top-notch fire-resistant solutions to various industries worldwide.[Company Name]'s continuous research and development efforts, coupled with a customer-centric approach, have positioned them as a trusted supplier of alumina fire bricks. In this article, we shed light on the market growth, key features of alumina fire bricks, and how [Company Name] is spearheading this progressive shift.Market Overview:The global alumina fire brick market is witnessing a steady pace of growth, driven by increasing industrialization and the need for superior heat resistance solutions. Alumina fire bricks, made from high-purity alumina, offer excellent thermal conductivity, corrosion resistance, and stability under high temperatures. These characteristics make alumina fire bricks a desired material in various industries, including steel, cement, ceramics, and petrochemicals.[Company Name]'s Contribution to the Market:[Company Name] has stayed ahead of the competition by focusing on research and development, ensuring their products meet or exceed industry standards. By leveraging cutting-edge technology and sustainable manufacturing practices, they have developed a range of alumina fire bricks that offer unmatched performance, durability, and longevity.Key Features of Alumina Fire Bricks:1. High Thermal Conductivity: Alumina fire bricks have a low thermal expansion coefficient and high thermal conductivity, allowing them to withstand extreme temperatures without compromising their structural integrity.2. Superior Corrosion Resistance: The high alumina content in these bricks resists chemical reactions, making them ideal for applications involving acids, alkalis, and other corrosive substances.3. Excellent Mechanical Strength: Alumina fire bricks possess exceptional mechanical strength, ensuring long-term reliability and resistance against thermal shock, abrasion, and mechanical stress.4. Environmentally Friendly: [Company Name]'s alumina fire bricks are manufactured using eco-friendly processes, minimizing their environmental impact while maintaining high-quality standards.Innovation is the Key:[Company Name] stands out from the competition by regularly investing in research and development, resulting in the introduction of pioneering alumina fire brick solutions. Their specialists work closely with customers to understand specific requirements, leading to customized hexagonal, rectangular, or other shapes that optimize kiln efficiency and reduce maintenance costs.These innovative brick designs, combined with advanced insulating properties, significantly enhance thermal efficiency and contribute to energy savings for industries worldwide.Global Presence and Customer Satisfaction:[Company Name]'s client base spans across continents, ensuring a global footprint and the ability to serve diverse industries. Their customer satisfaction is paramount, as they strive to deliver reliable products and exceptional support services. Through responsive technical assistance and prompt delivery schedules, [Company Name] has established long-lasting partnerships with clients who value quality and efficiency.Future Prospects:The prospects for the alumina fire brick market are promising, as industries worldwide are placing increasing emphasis on refractory solutions that can withstand demanding operating conditions. Rapid industrialization and infrastructural development in emerging economies, coupled with stringent safety regulations, are fueling the demand for alumina fire bricks.[Company Name], with its unwavering commitment to innovation, product excellence, and customer satisfaction, is poised to lead the market forward. By consistently introducing technologically advanced and eco-friendly solutions, [Company Name] aims to address the evolving needs of industries and contribute to their growth.Conclusion:As the global alumina fire brick market gains momentum, [Company Name] emerges as an industry leader, spearheading innovation and providing high-quality solutions. With a commitment to sustainability, exceptional performance, and customer satisfaction, [Company Name] is well-positioned to meet the growing demand for superior fire-resistant materials in industries worldwide.Note: We apologize for the lack of specific brand names and specific information about the company as per the initial instruction.
Discover the Benefits of Acid Resistant Refractory Castable for Your Needs
[Your Name][Date]Acid Resistant Refractory Castable: Revolutionizing High-Temperature Applications[City, State] - Acid Resistant Refractory Castable, an innovative product developed by [Company Name], is set to revolutionize high-temperature applications across a range of industries. With its exceptional durability and resistance to acidic environments, this castable material is a game-changer for businesses seeking reliable and cost-effective solutions.[Company Name] has been at the forefront of refractory materials for [number of years] years, specializing in the development and production of advanced ceramics and composite materials. With a dedicated team of researchers and engineers, the company has consistently pushed the boundaries of what is achievable in high-temperature applications.Acid Resistant Refractory Castable is the result of extensive research and development efforts by [Company Name]. This cutting-edge product offers superior resistance to acids, alkalis, and other corrosive substances found in various industrial processes. By withstanding the harshest conditions, this castable material significantly extends the service life of refractory linings, thereby reducing downtime and maintenance costs for businesses.One of the key advantages of Acid Resistant Refractory Castable is its exceptional chemical stability. The unique composition of the castable material allows it to withstand continuous exposure to strong acids, such as sulfuric acid and hydrochloric acid, without deteriorating or losing its properties. This not only enhances the overall performance of the refractory lining but also ensures the safety of personnel working in corrosive environments.Furthermore, the castable material exhibits excellent thermal shock resistance, enabling it to withstand rapid temperature changes without cracking or spalling. It can endure temperatures of up to [temperature range], making it suitable for a wide range of applications, including furnaces, kilns, reactors, and various chemical processing equipment.The installation process of Acid Resistant Refractory Castable is efficient and convenient, thanks to its excellent workability and flowability. This allows for precise and uniform casting, ensuring a seamless refractory lining that maximizes performance and reduces heat loss. Moreover, the material demonstrates excellent adhesion to various substrates, including bricks, steel, and concrete, providing a reliable and long-lasting solution for businesses.To meet the diverse requirements of different industries, [Company Name] offers customizable options for Acid Resistant Refractory Castable. The product can be tailored to specific project needs, including different chemical resistance levels, particle size distributions, and setting times. This flexibility ensures that customers receive a product that precisely matches their unique application requirements.Acid Resistant Refractory Castable has garnered positive feedback from numerous industries, including the petrochemical, metallurgical, and power generation sectors. "We have witnessed a noticeable improvement in the durability of our refractory linings after switching to Acid Resistant Refractory Castable," said [Company representative]. "This has led to significant cost savings and increased overall operational efficiency."[Company Name] continues to invest in cutting-edge research and development, striving to improve and expand their product line to meet evolving industry demands. In addition to Acid Resistant Refractory Castable, the company offers a wide range of refractory materials and solutions, including monolithic castables, ceramic fiber products, and high-temperature insulation materials.With Acid Resistant Refractory Castable, [Company Name] is leading the charge in providing reliable and cost-effective solutions for high-temperature applications. This revolutionary product is set to reshape several industries, enabling businesses to operate in corrosive environments with confidence, durability, and enhanced efficiency.About [Company Name]:[Company Name] is a leading provider of advanced refractory materials and solutions. With a strong focus on research and development, the company offers a wide range of high-quality products that cater to diverse industry needs. [Company Name]'s commitment to innovation, quality, and customer satisfaction has positioned it as a trusted partner for businesses worldwide.For media inquiries, please contact:[Company Contact Information]
Understanding the Importance of Electric Arc Furnace Electrodes for Steel Manufacturing
Electric Arc Furnace Electrodes: Innovating the Steel Production ProcessSteel production is a crucial aspect of various industries, ranging from construction to automotive manufacturing. With the increasing demand for steel products, the need for more efficient and sustainable production methods has become paramount. One of the key elements in the steelmaking process is the electric arc furnace (EAF), and the electrodes used within it play a critical role in ensuring a smooth operation. In this article, we will explore the advancements in electric arc furnace electrodes, highlighting their importance in the steel production industry.Electric arc furnace electrodes serve as conductors of electricity, enabling the melting of scrap metal and other raw materials in the EAF. Traditionally, carbon electrodes have been widely used due to their low cost and ability to withstand extreme temperatures. However, their usage often leads to high levels of greenhouse gas emissions, making them less environmentally friendly. In recent years, manufacturers have been striving to develop alternative electrode materials that not only improve overall performance but also minimize the environmental impact.One such innovative company in this field is {}, a leading provider of cutting-edge solutions for the steel industry. With a commitment to sustainability and technological advancements, they have introduced a range of breakthrough electrode products that are revolutionizing the steel production process. By combining their expertise in materials science and engineering, they have developed electrodes that offer numerous benefits compared to traditional carbon electrodes.One of the key advantages of these new electrodes is their improved energy efficiency. By utilizing advanced materials with enhanced electrical conductivity, they enable a more efficient transfer of electricity, resulting in reduced energy consumption during the steelmaking process. This not only helps in conserving valuable resources but also lowers production costs for steel manufacturers.Moreover, these innovative electrodes contribute to minimizing environmental pollution. The traditional carbon electrodes are known to release significant amounts of greenhouse gases, such as carbon dioxide (CO2), during the steelmaking process. In contrast, the new electrodes developed by {} emit much lower levels of CO2, thereby reducing the carbon footprint of steel production. This aligns with the global efforts to combat climate change and promote sustainable practices in industrial processes.In addition, the advanced electrode materials offer improved durability and longer service life. This reduces the frequency of electrode replacements, leading to cost savings for steel manufacturers. The electrodes are designed to withstand high temperatures and harsh operating conditions, ensuring a stable and uninterrupted steelmaking process.Furthermore, through extensive research and development, {} has introduced electrodes with enhanced slag resistance. Slag, a byproduct of the steelmaking process, can cause significant operational challenges and decrease overall efficiency. The new electrodes effectively mitigate these issues, allowing for smoother and more productive steel production.The introduction of these groundbreaking electrode solutions by {} has garnered widespread attention across the steel industry. Many manufacturers have already implemented these innovative products in their electric arc furnaces, experiencing notable improvements in both production efficiency and environmental performance.Looking ahead, the continuous development and adoption of advanced electrode technologies hold significant promise for the steel production industry. As the demand for steel continues to rise, manufacturers will increasingly rely on these innovative solutions to meet their production targets while minimizing their environmental impact.In conclusion, electric arc furnace electrodes play a crucial role in the steel production process, and recent advancements in this field are achieving remarkable results. Through the introduction of innovative electrode materials, companies like {} are revolutionizing the way steel is produced, offering improved energy efficiency, reduced environmental impact, enhanced durability, and increased operational efficiency. As the steel industry evolves and strives for sustainability, these advancements will play a pivotal role in shaping its future.