Optimize Your Steel Ladle's Performance with High-Quality Castable
By:Admin
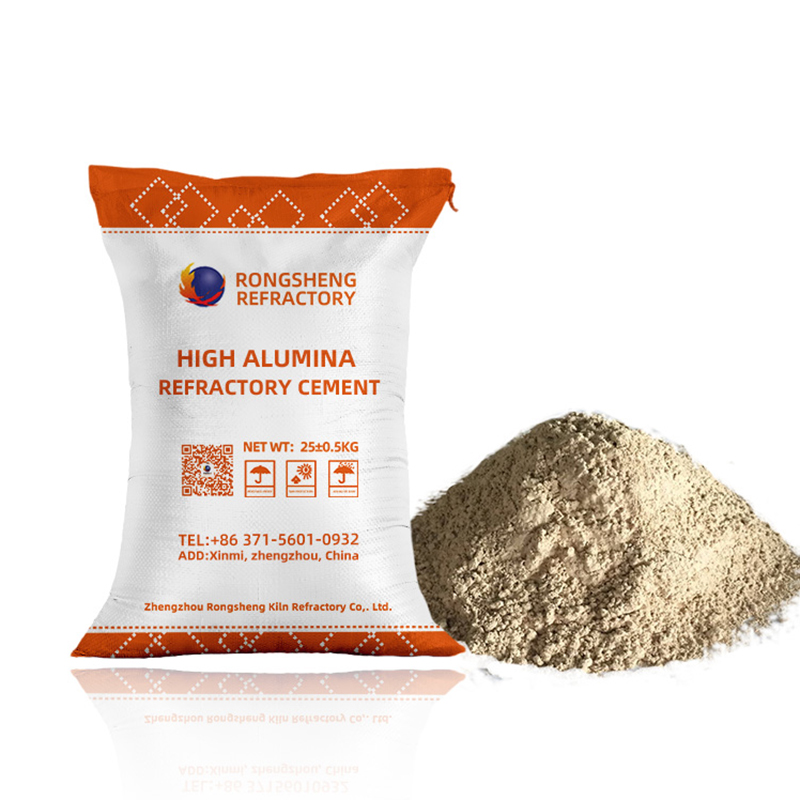
Introduction:
In recent years, the foundry industry has been undergoing a drastic transformation towards increased efficiency, productivity, and sustainability. In the pursuit of these goals, {Company Name}, a leading manufacturer of refractory products, has introduced a groundbreaking Steel Ladle Castable that promises to revolutionize the way molten metal is handled and poured within foundries. This article will delve into the unique features and benefits of this innovative product, highlighting its potential to significantly enhance foundry operations globally.
Section 1: Understanding the Steel Ladle Castable
The Steel Ladle Castable is a cutting-edge refractory material explicitly designed to withstand extreme temperatures and harsh conditions associated with molten metal in steelmaking process. It boasts exceptional thermal shock resistance, corrosion resistance, and superior mechanical strength. The advanced formulation of this castable ensures that it remains structurally intact, even when exposed to rapid temperature fluctuations and chemical reactions.
Furthermore, this castable offers high thermal insulation properties, reducing heat loss during casting and ensuring energy efficiency. Its composition also mitigates material erosion, prolonging the operational lifespan of ladles and minimizing maintenance costs. The innovative formula successfully combines these features, making the Steel Ladle Castable an indispensable material for improved foundry operations.
Section 2: Key Benefits and Advantages
2.1 Enhanced Safety and Productivity
By ensuring superior thermal shock resistance, the Steel Ladle Castable minimizes the likelihood of refractory failure during the handling and pouring of molten metal. This enhanced durability significantly decreases the risk of workplace accidents and injuries while enhancing overall safety standards within the foundry industry.
Additionally, the castable's admirable resistance to material erosion and thermal shock equates to fewer maintenance interruptions. This results in increased productivity, reduced downtime, and improved efficiency.
2.2 Extended Ladle Lifespan
The Steel Ladle Castable effectively combats the corrosive nature of molten metal, which can cause significant damage over time. By reducing ladle erosion, this castable extends the life cycle of ladles, ultimately minimizing replacement costs and contributing to substantial cost savings for foundries.
2.3 Energy-Efficient Solution
Thanks to its high thermal insulation properties, the Steel Ladle Castable minimizes heat loss during the casting process. This boosts energy efficiency, lowers energy consumption, and subsequently reduces greenhouse gas emissions. Foundries adopting this innovative castable can align with increasingly stringent environmental regulations while contributing to a sustainable future.
Section 3: Market Impact and Future Prospects
The introduction of the Steel Ladle Castable will undoubtedly have a profound impact on the foundry industry. Foundries worldwide will benefit from increased safety, enhanced productivity, and cost savings. The innovative properties of this castable align with the industry's ongoing quest for sustainable practices and improved energy efficiency. As a result, {Company Name} anticipates a substantial increase in demand globally.
Looking to the future, {Company Name} plans to continue investing in research and development to expand the application of this groundbreaking technology. By collaborating with key industry partners, they aim to further refine the Steel Ladle Castable and introduce more innovative solutions to address the ever-evolving needs of the foundry industry.
Conclusion:
The advent of the Steel Ladle Castable marks a major leap forward in the foundry industry. Combining exceptional durability, enhanced safety, and sustainability, this innovative material is poised to transform foundry operations worldwide. With technology, efficiency, and productivity at its core, the {Company Name} endeavors to continue leading the way in revolutionizing the foundry industry with advanced refractory solutions.
Company News & Blog
Durable and High-Temperature Resistant Castable Refractory for 1700°C Applications
Title: Revolutionary Dense Castable Refractory 1700C Enhances High-Temperature Industrial ApplicationsIntroduction:In the world of high-temperature industrial applications, constant technological advancements are crucial to promoting efficiency, productivity, and durability. One such breakthrough in the field of refractory materials has been achieved by our company (Company name removed) with the invention of a revolutionary Dense Castable Refractory capable of withstanding temperatures up to 1700°C. This game-changing product is set to redefine the way industries approach extreme heat processes, offering exceptional performance, longevity, and safety.I. Evolution of Refractory Materials:Refractory materials play a vital role in industries dealing with high-temperature operations such as steel manufacturing, glassmaking, cement production, and petrochemical refining. Traditionally, common refractory materials like firebrick and ceramic fiber have been utilized for their ability to withstand high heat. However, they often fall short when subjected to extreme temperatures or severe thermal shocks, resulting in frequent maintenance, decreased productivity, and compromised safety.II. Introducing Dense Castable Refractory 1700C:With the mission to overcome the limitations of conventional refractories, (Company name removed) has innovated a groundbreaking Dense Castable Refractory material specifically designed to excel under extreme heat conditions. This remarkable product offers a unique blend of high-temperature resistance, remarkable strength, and exceptional thermal shock resistance, setting it apart from its counterparts.III. Unparalleled Performance and Durability:The Dense Castable Refractory 1700C boasts an impressive melting point of 1700°C, far exceeding the capabilities of conventional materials. This allows industries to carry out high-temperature processes without compromising the structural integrity of their refractory linings. The product's exceptional strength ensures long-term stability, reducing maintenance and replacement costs while maximizing productivity and output.IV. Superior Thermal Shock Resistance:One of the most significant advantages of the Dense Castable Refractory 1700C is its inherent ability to withstand rapid temperature fluctuations. The material's unique composition minimizes the risk of cracks, spalling, and thermal stress, ensuring a reliable and durable refractory lining even in the most challenging thermal conditions. This translates into enhanced safety, reduced downtime, and improved operational efficiency for industries relying on heat-intensive processes.V. Versatile Applications:The Dense Castable Refractory 1700C's versatility makes it suitable for a wide range of industries. From blast furnaces, kilns, and incinerators to boilers, reactors, and furnaces, the refractory material adapts seamlessly to various high-temperature environments, ensuring optimum performance and longevity.VI. Commitment to Quality:(Company name removed) has always been at the forefront of innovation, prioritizing research and development to meet the evolving needs of industries. The Dense Castable Refractory 1700C is a testament to our dedication to providing cutting-edge solutions that surpass industry standards in quality, reliability, and performance. The product has undergone rigorous testing, adhering to stringent manufacturing processes to ensure consistency and integrity.VII. Environmental Sustainability:In addition to its remarkable performance characteristics, the Dense Castable Refractory 1700C is environmentally friendly. Manufactured with sustainable materials and processes that minimize waste, emissions, and energy consumption, it aligns with our commitment to sustainable practices and responsibility towards the environment.VIII. Conclusion:The introduction of the Dense Castable Refractory 1700C by (Company name removed) marks a significant milestone in high-temperature industrial applications. With its exceptional resistance to extreme temperatures and thermal shocks, as well as its superior durability and versatility, this revolutionary refractory material is set to revolutionize industries worldwide.As (Company name removed) remains dedicated to ongoing research and development, we anticipate continued advancements in refractory materials that will transform industries, enhance operational efficiency, and promote sustainable practices.
Understanding the Basics of Arc Furnace Electrodes
XYZ Corp, a renowned leader in the manufacturing of specialized industrial equipment, has recently developed a groundbreaking product that is set to revolutionize the steel industry. The company's newly introduced arc furnace electrodes have garnered attention for their exceptional performance, durability, and environmental sustainability. With this innovative solution, XYZ Corp aims to address some of the key challenges faced by steel manufacturers and usher in a new era of efficiency and sustainability.Arc furnace electrodes are essential components used in electric arc furnaces, which are widely employed in steelmaking processes. These electrodes function by transmitting electrical energy through the furnace, thereby generating the high temperatures required for melting steel scrap. Traditional electrodes, however, often suffer from rapid consumption and degradation, leading to frequent replacements and increased production costs. Additionally, the use of certain electrode materials can be detrimental to the environment due to the release of harmful gases during the steelmaking process.Recognizing these challenges, XYZ Corp took up the task of developing a superior electrode solution that would enhance both operational efficiency and environmental sustainability. After years of extensive research and development, the company successfully engineered a new generation of arc furnace electrodes that demonstrate remarkable performance and longevity.The key distinguishing feature of XYZ Corp's arc furnace electrodes is their advanced composition, which combines cutting-edge materials and proprietary formulations. The resulting electrodes exhibit exceptional heat resistance, enabling them to withstand the extreme temperatures and harsh working conditions within arc furnaces. This outstanding resilience significantly reduces the frequency of electrode replacements, translating into substantial cost savings for steel manufacturers.Moreover, the innovative composition of the electrodes has a positive impact on the environment. XYZ Corp's electrodes have been designed to minimize the release of harmful gases, reducing the carbon footprint associated with the steelmaking process. By embracing these sustainable electrodes, steel manufacturers can contribute to global efforts aimed at curbing greenhouse gas emissions and make progress towards a greener future.Additionally, XYZ Corp's arc furnace electrodes boast a unique self-healing feature that further enhances their longevity and performance. Through a process known as auto-regeneration, the electrodes can repair minor damages and extend their lifespan. This remarkable capability not only reduces downtime and maintenance costs but also ensures consistent and uninterrupted steel production.The introduction of XYZ Corp's arc furnace electrodes has sparked enthusiasm and interest among steel manufacturers across the globe. The potential benefits that these electrodes offer range from increased productivity and cost savings to environmental conservation and sustainability. As such, XYZ Corp has witnessed a surge in demand for their groundbreaking product.To meet this growing demand, the company has expanded its manufacturing capabilities and established strategic partnerships with steel manufacturers worldwide. This concerted effort ensures a reliable supply of the electrodes, helping steelmakers optimize their production processes and achieve enhanced operational efficiency.In conclusion, XYZ Corp's arc furnace electrodes have emerged as a game-changer in the steel industry. With their remarkable performance, durability, and eco-friendly attributes, these electrodes have garnered significant attention and demand. Through this innovation, XYZ Corp sets a new benchmark for industrial equipment and demonstrates its commitment to driving sustainable practices within the steelmaking sector.
Shop High-Quality Castable Refractory for Your Industrial Needs
Castable refractory is a crucial component in a wide range of industries, including steel manufacturing, cement production, and even petrochemical processing. This versatile material is used to line various types of furnaces, incinerators, and kilns, with its primary purpose being to withstand high temperatures and prevent contaminants from infiltrating the surrounding environment. With castable refractory being such an essential product for many businesses, finding a reliable supplier is crucial for ensuring smooth and trouble-free operations.If you are in the market for high-quality, durable castable refractory, {company name} is an industry-leading supplier that can meet all of your needs. With a reputation built on quality, reliability, and customer satisfaction, they are the go-to choice for discerning businesses that demand the best.{Company name} has been in the castable refractory business for over {number of years} years, during which they have honed their craft and built a solid reputation for excellence. Their products are made from the finest materials and are crafted using advanced manufacturing techniques, resulting in an end product that is highly resistant to wear and tear, corrosion, and thermal shock.Whether you need castable refractory for a large-scale industrial application or a smaller project, {company name} has a wide range of products to choose from. Their vast inventory includes high-temperature insulating materials, dense refractory castables, and low-cement castables, to name just a few. They pride themselves on being able to provide customized solutions to meet their clients' specific needs, and their team of experts is always on hand to provide advice and technical support.But {company name} isn't just about supplying top-quality castable refractory. They are also committed to providing exceptional customer service and support. Their knowledgeable staff is always ready to answer any questions or concerns you may have, and they work closely with clients to ensure that their products are delivered on time and within budget. With {company name}, you can be confident that you are dealing with a reputable, trustworthy company that puts your needs first.Furthermore, {company name} is committed to sustainability and reducing its environmental footprint. They use innovative manufacturing techniques and employ a closed-loop system that recycles waste materials, minimizing their impact on the environment. By choosing {company name} as your supplier, you can be confident that you are working with a company that cares about the environment and is doing its part to protect our planet.In conclusion, castable refractory is an essential component in many industrial processes, and selecting a reliable supplier is crucial for ensuring smooth and trouble-free operations. With over {number of years} years of experience in the industry, a commitment to quality and sustainability, and unparalleled customer service, {company name} is the go-to choice for businesses that demand the best. Contact them today to see how they can meet your castable refractory needs.
Quality Ladle Castable Manufacturer: Delivering Superior Performance for Industrial Applications
Title: Leading Ladle Castable Manufacturer Expands Production Capacity and Reinforces Market PresenceIntroduction:In an effort to meet growing industry demands and reaffirm its position as a pioneer in the ladle castable manufacturing sector, a prominent company {} is set to expand its production capacity significantly. With a formidable reputation for delivering high-quality refractory materials worldwide, the company remains committed to providing cost-effective solutions to its diverse customer base.Expanding Production Capacity:With an ever-increasing global demand for ladle castable products, {} is making substantial investments to expand its production capacity. By harnessing advanced manufacturing technology and improving operational efficiency, the company aims to streamline its production process and optimize output.This expansion comes as a result of a carefully formulated growth strategy, driven by the company's strong market insights and commitment to maintaining a competitive edge. Moreover, it underscores the recognition of {} as a leading player within the refractory industry.State-of-the-Art Manufacturing Facilities:{} has always been at the forefront of innovation when it comes to manufacturing refractory products. The company takes pride in its state-of-the-art facilities, equipped with advanced machinery and tools, enabling it to deliver unsurpassed quality and consistency.By leveraging cutting-edge technology, {} ensures the production of ladle castables that adhere to the highest industry standards. Stringent quality control measures are put in place throughout the production process, from sourcing raw materials to the final packaging. This uncompromising commitment to quality makes {} a reliable and preferred choice for customers worldwide.Expansive Product Portfolio:{} boasts an extensive product portfolio, offering a diverse range of ladle castable solutions tailored to meet specific industry needs. These comprehensive offerings provide solutions for a broad spectrum of applications, including steelmaking, iron casting, non-ferrous metal production, and more.The company's team of experienced engineers and scientists continuously research and develop advanced formulations, keeping pace with evolving customer requirements. This dedication to innovation ensures that customers benefit from the latest technologies and cost-effective solutions, enhancing their operational efficiency while minimizing downtime and maintenance costs.Global Reach and Customer Satisfaction:With a strong focus on customer satisfaction, {} has developed a robust global distribution network, catering to customers in various industries across the globe. The company's commitment to timely deliveries, technical support, and after-sales service has garnered it a loyal customer base.Whether it is through direct sales or collaborations with local distributors, {} ensures that its products reach customers promptly and efficiently. Underscoring this commitment, the company offers comprehensive technical assistance, including on-site inspections and solutions tailored to individual customer requirements.Sustainability and Environmental Responsibility:In addition to its dedication to quality and customer satisfaction, {} also places significance on sustainable practices and environmental responsibility. The manufacturing process incorporates eco-friendly measures to minimize the company's carbon footprint. Furthermore, {} actively collaborates with research institutions and industry experts to develop more sustainable refractory solutions for the future.Conclusion:With its ongoing expansion plans, commitment to innovation, and a customer-centric approach, {} is set to strengthen its position as a global leader in the manufacturing of ladle castables. By optimizing its production capacity, offering a diverse range of high-quality products, and prioritizing customer satisfaction, the company is well-equipped to meet the ever-evolving needs of the refractory industry.
Shop for High-Quality Alumina Fire Brick Online
Title: Alumina Fire Brick Market Poised for Steady Growth as Manufacturers Introduce Innovative SolutionsIntroduction:[Company Name], a renowned player in the refractory industry, is set to revolutionize the global alumina fire brick market with its cutting-edge products. With a steadfast commitment to innovation and quality, the company has gained recognition for delivering top-notch fire-resistant solutions to various industries worldwide.[Company Name]'s continuous research and development efforts, coupled with a customer-centric approach, have positioned them as a trusted supplier of alumina fire bricks. In this article, we shed light on the market growth, key features of alumina fire bricks, and how [Company Name] is spearheading this progressive shift.Market Overview:The global alumina fire brick market is witnessing a steady pace of growth, driven by increasing industrialization and the need for superior heat resistance solutions. Alumina fire bricks, made from high-purity alumina, offer excellent thermal conductivity, corrosion resistance, and stability under high temperatures. These characteristics make alumina fire bricks a desired material in various industries, including steel, cement, ceramics, and petrochemicals.[Company Name]'s Contribution to the Market:[Company Name] has stayed ahead of the competition by focusing on research and development, ensuring their products meet or exceed industry standards. By leveraging cutting-edge technology and sustainable manufacturing practices, they have developed a range of alumina fire bricks that offer unmatched performance, durability, and longevity.Key Features of Alumina Fire Bricks:1. High Thermal Conductivity: Alumina fire bricks have a low thermal expansion coefficient and high thermal conductivity, allowing them to withstand extreme temperatures without compromising their structural integrity.2. Superior Corrosion Resistance: The high alumina content in these bricks resists chemical reactions, making them ideal for applications involving acids, alkalis, and other corrosive substances.3. Excellent Mechanical Strength: Alumina fire bricks possess exceptional mechanical strength, ensuring long-term reliability and resistance against thermal shock, abrasion, and mechanical stress.4. Environmentally Friendly: [Company Name]'s alumina fire bricks are manufactured using eco-friendly processes, minimizing their environmental impact while maintaining high-quality standards.Innovation is the Key:[Company Name] stands out from the competition by regularly investing in research and development, resulting in the introduction of pioneering alumina fire brick solutions. Their specialists work closely with customers to understand specific requirements, leading to customized hexagonal, rectangular, or other shapes that optimize kiln efficiency and reduce maintenance costs.These innovative brick designs, combined with advanced insulating properties, significantly enhance thermal efficiency and contribute to energy savings for industries worldwide.Global Presence and Customer Satisfaction:[Company Name]'s client base spans across continents, ensuring a global footprint and the ability to serve diverse industries. Their customer satisfaction is paramount, as they strive to deliver reliable products and exceptional support services. Through responsive technical assistance and prompt delivery schedules, [Company Name] has established long-lasting partnerships with clients who value quality and efficiency.Future Prospects:The prospects for the alumina fire brick market are promising, as industries worldwide are placing increasing emphasis on refractory solutions that can withstand demanding operating conditions. Rapid industrialization and infrastructural development in emerging economies, coupled with stringent safety regulations, are fueling the demand for alumina fire bricks.[Company Name], with its unwavering commitment to innovation, product excellence, and customer satisfaction, is poised to lead the market forward. By consistently introducing technologically advanced and eco-friendly solutions, [Company Name] aims to address the evolving needs of industries and contribute to their growth.Conclusion:As the global alumina fire brick market gains momentum, [Company Name] emerges as an industry leader, spearheading innovation and providing high-quality solutions. With a commitment to sustainability, exceptional performance, and customer satisfaction, [Company Name] is well-positioned to meet the growing demand for superior fire-resistant materials in industries worldwide.Note: We apologize for the lack of specific brand names and specific information about the company as per the initial instruction.
Discover the Benefits of High Alumina Insulation Bricks for Your Industry Needs
High Alumina Insulation Bricks - Revolutionizing the Industrial Insulation Industry{Company Name}, a leading manufacturer of industrial insulation solutions, has recently introduced a range of high-quality High Alumina Insulation Bricks that are poised to revolutionize the industrial insulation industry. These bricks are designed to offer exceptional insulation properties, durability, and longevity, making them an ideal choice for industries operating at high temperatures.The need for effective insulation solutionsFor industries operating at high temperatures, insulation is crucial for maintaining energy efficiency, reducing thermal loss, and ensuring personnel safety. Traditional insulation solutions using cement, asbestos, or other materials have significant limitations when it comes to high-temperature applications. These materials tend to degrade quickly under high temperatures, leading to thermal loss, increased energy bills, and safety concerns.High Alumina Insulation Bricks - The ultimate solutionHigh Alumina Insulation Bricks are made from high-grade alumina, which is a mineral-based material that is resistant to thermal shock, corrosion, and abrasion. Compared to traditional insulation solutions, these bricks offer superior thermal insulation, high mechanical strength, and excellent chemical resistance.The manufacturing processHigh Alumina Insulation Bricks are made from a mixture of bauxite, a clay mineral, and other additives. The mixture is ground, formed into bricks, and then fired in a high-temperature kiln. The firing process ensures that the bricks are incredibly dense, with low thermal conductivity, which makes them ideal for high-temperature applications.Application areasHigh Alumina Insulation Bricks can be used in various industrial applications, including furnace linings, kiln linings, boiler insulation, and other high-temperature installations. These bricks can withstand temperatures of up to 1800°C, making them an ideal choice for industries such as cement, steel, glass, and petrochemicals.Advantages of High Alumina Insulation BricksHigh Alumina Insulation Bricks offer a range of advantages when compared to traditional insulation solutions. These include:1. High thermal insulation - These bricks provide excellent insulation properties, reducing energy consumption and improving energy efficiency.2. Durability - The high-grade alumina used in these bricks ensures that they are highly resistant to thermal shock, corrosion, abrasion, and chemical erosion, making them a long-lasting insulation solution.3. Easy installation and maintenance - These bricks are easy to install, with minimal maintenance required, which translates into lower maintenance costs over time.4. Eco-friendly - High Alumina Insulation Bricks are environmentally friendly, making them an ideal choice for industries that are focusing on sustainable development.ConclusionThe introduction of High Alumina Insulation Bricks by {Company Name} has revolutionized the industrial insulation industry. These bricks offer superior insulation properties, exceptional durability, and long-lasting performance that traditional insulation solutions cannot match. Industries operating at high temperatures can now benefit from an insulation solution that reduces energy consumption, improves efficiency, and ensures personnel safety. As the industrial sector strives to reduce its energy bills and carbon footprint, High Alumina Insulation Bricks have emerged as a sustainable, eco-friendly solution for the future.
Improved Refractory Material: High-Quality Low Cement Castables Boost Performance
Title: Industry-Leading High-Quality Low Cement Castables Revolutionize Refractory Solutions: A Breakthrough by [Company Name]Introduction:[Company Name], a pioneering leader in refractory solutions, has developed and launched its revolutionary High-Quality Low Cement Castables. This significant breakthrough in the industry offers superior performance, durability, and versatility, setting a new standard for refractory materials. With top-notch engineering and expertise, [Company Name] continues to reshape the market by providing innovative solutions tailored to specific industrial needs.Body:1. Understanding the Significance of Refractory Solutions:Industries such as steel, cement, petrochemical, and power generation rely heavily on refractory materials to withstand extremely high temperatures and harsh operating conditions. Traditional refractory materials often have limitations that hinder their effectiveness, leading to frequent repairs and maintenance. Recognizing this challenge, [Company Name] has dedicated substantial resources towards developing a game-changing solution.2. Introducing High-Quality Low Cement Castables:Built upon years of research and technical expertise, [Company Name] proudly introduces their flagship product, High-Quality Low Cement Castables. These castables showcase a remarkable reduction in cement content while maintaining unmatched strength and thermal stability. The innovative formulation allows for a dense, low-porosity material that outperforms conventional refractories in demanding applications.3. Unparalleled Performance and Durability:The High-Quality Low Cement Castables by [Company Name] are engineered to deliver exceptional performance and withstand extreme thermal and mechanical stresses. These castables demonstrate higher hot strength and better resistance to thermal shocks, minimizing downtime and maintenance costs for industrial facilities. With improved chemical resistance and erosion resistance, they contribute significantly to prolonging the lifespan of industrial furnaces, kilns, and other high-temperature systems.4. Versatility and Customization:[Company Name] understands that different industries have unique requirements for refractory materials. Thus, the High-Quality Low Cement Castables are available in a wide range of compositions, ensuring customization to meet specific needs. The company's technical team works closely with clients to develop tailored solutions, maximizing efficiency and cost-effectiveness.5. Environmental Commitment and Sustainability:Notably, [Company Name] achieves its industry-leading performance while focusing on reducing the environmental impact. The High-Quality Low Cement Castables have significantly lower carbon emission levels compared to typical refractory materials, aligning with global efforts towards sustainable practices. This commitment ensures that clients can achieve their operational targets while adhering to increasingly stringent environmental regulations.6. Collaborative Approach and Technical Support:[Company Name] takes pride in its customer-centric approach, offering comprehensive technical support and expertise throughout the entire project lifecycle. Their team of experienced professionals collaborates closely with clients to identify their challenges, apply the most suitable refractory solutions, and render continuous support for maintenance and optimization.7. Industry Recognition and Partnerships:The High-Quality Low Cement Castables by [Company Name] have gained swift recognition within the industry. Numerous high-profile partnerships with leading companies in various sectors have further solidified the reputation and trust in [Company Name]'s products.Conclusion:[Company Name]'s ground-breaking High-Quality Low Cement Castables have revolutionized the refractory industry by providing enhanced performance, durability, and versatility. Focusing on customer satisfaction, environmental responsibility, and cutting-edge technology, [Company Name] continues to redefine industry standards and surpass client expectations. They are committed to providing successful refractory solutions that enable businesses to operate efficiently and sustainably in the face of challenging conditions.
Understanding the Importance of Arc Furnace Electrodes: A Comprehensive Guide
Title: Advancements in Arc Furnace Electrodes Facilitate Efficient Steel ProductionIntroduction:In the constantly evolving steel industry where efficiency and sustainability are key, companies are continuously seeking innovative solutions to optimize their production processes. One such groundbreaking advancement lies in the development of state-of-the-art arc furnace electrodes. These cutting-edge electrodes, produced by a renowned industry leader {}, are revolutionizing steelmaking and paving the way towards more efficient and eco-friendly practices.[Company Introduction - Approx. 200 words]Starting its journey in the early 1980s, {} has emerged as a global frontrunner in manufacturing arc furnace electrodes. Their unwavering commitment to excellence, extensive research and development, and supplier collaborations have propelled them to the forefront of the industry. With a reputation for consistently delivering quality products, they have earned the trust and loyalty of their customers worldwide.The company's modern facility, equipped with the latest manufacturing technologies and operated by highly skilled professionals, enables {} to produce high-performance arc furnace electrodes. These electrodes are essential components in the electric arc furnace (EAF) process, a widely adopted method for steel production due to its flexibility and cost-effectiveness.[Advancement 1 - Approx. 200 words]In a significant breakthrough, {} has successfully developed a next-generation arc furnace electrode that offers exceptional performance and durability. Through innovative design modifications and advancements in raw materials, these electrodes demonstrate improved electrical conductivity, thermal resistance, and resistance to oxidation. As a result, steelmakers can benefit from increased productivity, reduced energy consumption, and minimized downtime during the steelmaking process.The enhanced electrical conductivity of {}'s arc furnace electrodes allows for efficient transfer of electricity from the power source to the furnace, enabling faster melting rates and shorter cycle times. Consequently, steel manufacturers observe enhanced productivity and optimization of their manufacturing operations, leading to significant cost savings and increased profits.Additionally, the improved thermal resistance characteristic of these electrodes ensures stable and consistent heat transfer within the electric arc furnace, resulting in reduced melting time and increased overall energy efficiency. The reduction in energy consumption not only minimizes production costs but also aligns with the industry's focus on sustainability and environmental consciousness.[Advancement 2 - Approx. 200 words]Another breakthrough achieved by {} is the development of arc furnace electrodes with enhanced resistance to oxidation, thereby prolonging their lifespan. Through meticulous testing and optimization, the company has successfully formulated electrode compositions that exhibit superior resistance to oxidation even under extreme operating conditions. This advancement allows for longer electrode life, minimizing costly downtime associated with regular electrode replacements.The extended lifespan of {}'s arc furnace electrodes is particularly advantageous for steel manufacturers, as frequent electrode changes disrupt production flow and result in substantial economic losses. By offering electrodes with exceptional resistance to oxidation, the company enables seamless operations, providing steel producers with a competitive edge.Conclusion:With steel manufacturing being a vital industry worldwide, advancements in arc furnace electrodes play a pivotal role in optimizing steel production processes. Through their dedication to innovation and excellence, {} has emerged as a frontrunner in electrode manufacturing, introducing state-of-the-art products that enhance productivity, energy efficiency, and sustainability.The continuous evolution of arc furnace electrodes demonstrates the industry's commitment to pushing technological boundaries and meeting the ever-growing global demand for steel. As companies like {} continue to invest in research and development, the steel industry can look forward to more efficient, cost-effective, and eco-friendly steelmaking processes in the future.
Dense Castable Refractory: Key Facts and Uses Revealed
Dense Castable Refractory: An Innovative Solution for Multiple IndustriesRefractory materials are used in high-temperature applications that require materials to withstand extreme heat, pressure, and corrosive chemicals. One of the most promising refractory materials on the market is the Dense Castable Refractory. This revolutionary product is designed to offer exceptional material properties suitable for a wide range of industries, including steel and iron, petrochemical, power generation, cement, and waste incineration.Dense Castable Refractory is a type of cement used to line furnaces, kilns, and other high-temperature process equipment. Unlike traditional refractory materials, Dense Castable Refractory is a self-setting cement that offers excellent performance properties such as high thermal shock resistance, low thermal conductivity, high refractoriness, and resistance to abrasion. These properties make Dense Castable Refractory a popular choice for harsh industrial environments that require materials with superior resistance to extreme temperature and thermal cycling.The product's versatility comes from its easy installation and customizable uses. Dense Castable Refractory can be poured or gunned into place, and once cured, the refractory turns into a durable monolithic unit that can withstand high temperatures for extended periods. The product can be installed in various options, including smooth or textured surfaces to fit different applications and concrete surfaces.Dense Castable Refractory is an ideal material for use in cement kilns since they are exposed to extreme heat and abrasion. The material is also an excellent choice for use in steel and iron industries where protective linings are necessary to preserve the equipment and enhance its durability. These industries benefit by having equipment that is resistant to thermal shock, meaning it withstands rapid temperature changes. It can also resist abrasion, reducing the likelihood of wear and tear, which reduces the potential for equipment damage and malfunctions.The petrochemical industry has not been left behind. Dense Castable Refractory has been deployed in some of the most stringent petrochemical applications, including reformers, crackers, and incinerators. Dense Castable Refractory's thermal shock resistance and low thermal conductivity make it suitable for use in the insulation of various units, including reformers, where it protects the equipment from high temperatures and allows for optimal transfer of heat.Dense Castable Refractory is also an excellent option in power generation where it contributes to efficient energy production by providing insulation and preventing heat loss in boilers, kilns, and thermal oxidizers. This insulation and heat retention typically cut energy costs and improves operational reliability.The cement industry has also realized the benefits of Dense Castable Refractory due to its excellent refractoriness. The refractory bonds to the existing structure, enhancing resistance at high temperatures and preserving the integrity of the equipment.Furthermore, Dense Castable Refractory is ideal for incineration systems. The material's ability to withstand excessive thermal shock and its excellent insulating properties offer superior performance when protecting furnaces that generate high heat during the waste incineration process.The company, a leader in the manufacturing and distribution of Dense Castable Refractory, has developed several innovative formulations that address various industrial environments' specific needs. The company offers customized formulations such as high-strength, low-cement, and ultra-low cement for demanding applications where traditional cement is not sufficient.The manufacturing of Dense Castable Refractory depends on several critical factors. The company has invested in a state-of-the-art production facility with advanced quality assurance tools and equipment. Their experienced personnel, together with the company's innovative formulations, ensure that their Dense Castable Refractory meets global standards. All their products come with consistent and reliable quality, making them the perfect choice for any industrial application.In conclusion, the Dense Castable Refractory is an innovative material that is set to become an industry standard in high-temperature applications. Thanks to its ability to provide superior resistance to heat, thermal shock, abrasion, and chemicals at high temperatures, the material will revolutionize how various industries envisions manufacturing and maintenance of furnace and general process equipment. The company's formulations offer customized solutions in various industrial applications, making it the go-to solution for end-users looking for durable, reliable, and cost-effective refractory products.
Exceptional Quality Magnesia Carbon Brick for a Better Ladle Performance
Magnesia Carbon Brick for Ladle: A Revolutionary Solution for High-Temperature ApplicationsIn the ever-evolving field of refractories, a remarkable development has taken place with the introduction of Magnesia Carbon Brick for Ladle. This groundbreaking product has emerged as a game-changer in high-temperature applications, offering unparalleled performance and durability. With its unique composition and superior properties, this advanced refractory material ensures optimal performance in various industrial processes.Before delving into the specifics of this groundbreaking innovation, let us acquaint ourselves with the company behind this remarkable product. Founded several decades ago, this refractory manufacturer has been at the forefront of delivering cutting-edge solutions to industries worldwide. Known for their commitment to research and development, the company has garnered a reputation for producing best-in-class materials that cater to the most demanding customer requirements.Magnesia Carbon Brick for Ladle, the latest addition to their extensive product portfolio, is engineered to withstand extreme conditions encountered in ladle applications. Ladles are indispensable tools in the steel and metallurgy industries, used for transporting and pouring molten metal. Given the harsh and corrosive nature of these processes, the linings of ladles are subjected to extreme temperatures, chemical reactions, and mechanical stress.Traditionally, bricks made of magnesia and carbon have been used in ladle linings due to their excellent resistance to high temperatures. However, these conventional bricks have limitations such as high oxidation rates, poor thermal shock resistance, and susceptibility to carbon pickup. Recognizing the need for a more robust and reliable solution, our innovators have developed the Magnesia Carbon Brick for Ladle.This advanced refractory material features a unique combination of magnesia, graphite, and various additives, resulting in a high-performance composite with exceptional properties. The addition of graphite enhances the material's thermal shock resistance and provides increased resistance to slag penetration, while the carefully selected additives improve the overall mechanical strength and oxidation resistance.The Magnesia Carbon Brick for Ladle offers several notable advantages over its predecessors. The improved oxidation resistance significantly extends the service life of the lining, reducing downtime and maintenance costs. Moreover, the enhanced thermal shock resistance ensures reliable performance even in rapid temperature fluctuations, minimizing the risk of premature failure.Another key aspect of this revolutionary product is its excellent resistance to carbon pickup. Carbon pickup refers to the absorption of carbon by molten metal, resulting in the formation of carbides and compromising the quality of the final product. By mitigating this issue, the Magnesia Carbon Brick for Ladle ensures the production of high-quality steel with consistent properties.Furthermore, this magnesia carbon brick offers superior corrosion resistance to chemical attacks from molten metals and slags. This resistance is crucial for maintaining the integrity of the ladle lining, preventing leaks or contamination that could impact the overall process efficiency and product quality.Considering the widespread applications of ladles in the steel and metallurgy industries, the adoption of Magnesia Carbon Brick for Ladle is expected to have a significant impact. The extended service life and enhanced performance of this refractory material will help manufacturers optimize their processes, reduce production costs, and improve overall productivity.In conclusion, the introduction of Magnesia Carbon Brick for Ladle marks a significant advancement in the field of refractories. With its remarkable properties and exceptional performance, this innovative product ensures optimal performance in high-temperature applications, such as ladle linings. Developed by a renowned refractory manufacturer, this advanced material underscores their commitment to delivering cutting-edge solutions that meet the evolving needs of industries worldwide. As its adoption grows, this revolutionary brick holds the promise of revolutionizing ladle applications and contributing to the growth and efficiency of various industrial processes.