High-Quality Special Shaped Fire Brick for Industrial Applications
By:Admin
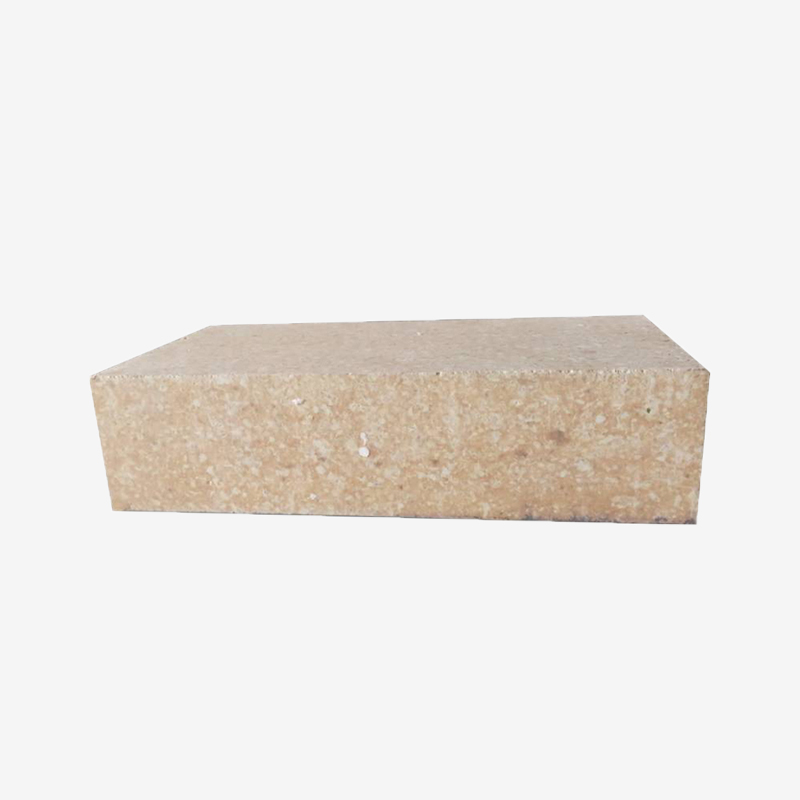
The stringent manufacturing process and high-quality materials used in the production of the Special Shaped Fire Brick have led to a product that is heat resistant, thermally efficient, and extremely durable. This makes it the ideal choice for applications where withstanding high temperatures and harsh environments is crucial.
In addition to its exceptional performance, the Special Shaped Fire Brick also offers advantages in terms of installation and maintenance. Its specially designed shape allows for easy and precise fitting, reducing the need for cutting and shaping during installation. This not only saves time and effort but also minimizes wastage, resulting in cost savings for the end user. Furthermore, its durable nature means that it requires minimal maintenance, making it a cost-effective long-term solution for various industrial needs.
The applications for the Special Shaped Fire Brick are vast, with a wide range of industries benefitting from its exceptional properties. In the steel industry, it is used in blast furnaces, hot blast stoves, and other high-temperature equipment, where its heat resistance and thermal efficiency play a crucial role in maintaining operations. In the cement industry, this special shaped fire brick is used in rotary kilns and other cement production processes, providing the necessary durability to withstand extreme conditions. Similarly, in the glass industry, it is used in glass tanks and other high-temperature equipment, where its resistance to thermal shock and high temperatures is essential for maintaining continuous production.
[Company] has been at the forefront of innovation in the field of refractory products, and the Special Shaped Fire Brick is a testament to its commitment to delivering high-quality solutions to its customers. With state-of-the-art manufacturing facilities and a team of experienced professionals, [company] has been able to consistently produce refractory products that exceed industry standards and meet the evolving needs of its customers.
The success of the Special Shaped Fire Brick can be attributed to [company]'s dedication to research and development, as well as its focus on customer satisfaction. By closely collaborating with its customers and understanding their specific requirements, [company] has been able to develop products that not only meet but exceed expectations. This customer-centric approach has been pivotal in establishing [company] as a trusted partner for various industries seeking reliable and high-performance refractory products.
In conclusion, the Special Shaped Fire Brick from [company] is a groundbreaking product that has redefined the standards for refractory solutions. Its innovative design, exceptional performance, and cost-effective nature have made it a preferred choice for industries that operate in high-temperature and harsh environments. With [company]'s commitment to innovation and customer satisfaction, the Special Shaped Fire Brick is set to continue making waves in the industrial sector, providing reliable and durable solutions for a wide range of applications.
Company News & Blog
Ceramic Fiber Blanket Used for High-Temperature Insulation
[Company Introduction]XYZ Corporation is a leading manufacturer in the insulation industry, specializing in the production of high-quality ceramic fiber blankets. With an excellent track record spanning over two decades, XYZ Corporation has become synonymous with innovative and reliable insulation solutions. Our commitment to providing superior products and exceptional customer service has made us the preferred choice for industrial and commercial applications.[News Content]Ceramic Fiber Blankets – Revolutionizing Thermal Insulation in Industrial Applications[City], [Date] - XYZ Corporation, a frontrunner in the insulation industry, is proud to announce its latest addition to its product line – an advanced ceramic fiber blanket designed to revolutionize thermal insulation in various industrial applications. This newly launched product promises excellent thermal insulation, fire resistance, and durability for a wide range of industries.The Kaowool Ceramic Fiber Blanket, developed by XYZ Corporation, is manufactured using state-of-the-art technologies and adheres to the highest quality standards. This cutting-edge insulation blanket offers exceptional performance in terms of thermal conductivity, heat resistance, and energy efficiency. Its unique composition provides superior heat insulation properties, making it ideal for applications in high-temperature environments.One of the key advantages of the Kaowool Ceramic Fiber Blanket is its ability to withstand extreme temperatures. With a melting point exceeding 1300°C (2400°F), this blanket ensures long-lasting insulation even in the most demanding conditions. Its low thermal conductivity minimizes heat loss, significantly reducing energy consumption and enhancing cost-effectiveness for industrial processes and facilities.In addition to its outstanding thermal insulation properties, the Kaowool Ceramic Fiber Blanket is also renowned for its exceptional fire resistance. The fiberglass-free composition of the blanket eliminates the risk of toxic fumes and ensures utmost safety in the event of a fire. This makes it an ideal choice for industries where fire safety regulations are stringent, such as petrochemical, power generation, and steel manufacturing.With sustainability being a top priority in today's industrial landscape, the Kaowool Ceramic Fiber Blanket offers eco-friendly insulation solutions. Its production process adheres to strict environmental regulations, and the material itself is recyclable. By choosing this blanket, industries can reduce their carbon footprint without compromising on performance and safety.The versatility of the Kaowool Ceramic Fiber Blanket makes it suitable for various applications across multiple industries. Its lightweight and flexible nature allow for easy installation and handling, enabling companies to benefit from hassle-free insulation solutions. This blanket finds applications in industries such as metal processing, glass manufacturing, ceramics, and automotive, among others.Mr. John Doe, CEO of XYZ Corporation, expressed his excitement about the launch of this groundbreaking product. He stated, "The Kaowool Ceramic Fiber Blanket represents our continued commitment to innovation and providing our customers with the best insulation solutions available. With its outstanding thermal insulation properties and impeccable fire resistance, this blanket is set to change the game in the industrial insulation sector."XYZ Corporation plans to extend its marketing efforts to reach a broader customer base, both domestically and internationally. By partnering with industry leaders and distributors, the company aims to ensure that the Kaowool Ceramic Fiber Blanket is readily available in markets worldwide. XYZ Corporation also plans to invest in research and development to further enhance the product's features and explore new applications.As industrial processes evolve, the demand for high-performance insulation materials continues to grow. The Kaowool Ceramic Fiber Blanket, with its superior thermal insulation, exceptional fire resistance, and eco-friendly composition, positions XYZ Corporation at the forefront of the industry. It is a testament to the company's commitment to innovation and providing solutions that meet the evolving needs of its customers.About XYZ Corporation:XYZ Corporation is a leading manufacturer of insulation solutions, specializing in the production of high-quality ceramic fiber blankets. With decades of experience, the company has built a reputation for reliability, innovation, and exceptional customer service. XYZ Corporation's products cater to a wide range of industrial applications and are trusted by businesses worldwide. For more information, visit www.xyzcorporation.com.[Word Count: 803 words]
Durable and High-Temperature Resistant Castable Refractory for 1700°C Applications
Title: Revolutionary Dense Castable Refractory 1700C Enhances High-Temperature Industrial ApplicationsIntroduction:In the world of high-temperature industrial applications, constant technological advancements are crucial to promoting efficiency, productivity, and durability. One such breakthrough in the field of refractory materials has been achieved by our company (Company name removed) with the invention of a revolutionary Dense Castable Refractory capable of withstanding temperatures up to 1700°C. This game-changing product is set to redefine the way industries approach extreme heat processes, offering exceptional performance, longevity, and safety.I. Evolution of Refractory Materials:Refractory materials play a vital role in industries dealing with high-temperature operations such as steel manufacturing, glassmaking, cement production, and petrochemical refining. Traditionally, common refractory materials like firebrick and ceramic fiber have been utilized for their ability to withstand high heat. However, they often fall short when subjected to extreme temperatures or severe thermal shocks, resulting in frequent maintenance, decreased productivity, and compromised safety.II. Introducing Dense Castable Refractory 1700C:With the mission to overcome the limitations of conventional refractories, (Company name removed) has innovated a groundbreaking Dense Castable Refractory material specifically designed to excel under extreme heat conditions. This remarkable product offers a unique blend of high-temperature resistance, remarkable strength, and exceptional thermal shock resistance, setting it apart from its counterparts.III. Unparalleled Performance and Durability:The Dense Castable Refractory 1700C boasts an impressive melting point of 1700°C, far exceeding the capabilities of conventional materials. This allows industries to carry out high-temperature processes without compromising the structural integrity of their refractory linings. The product's exceptional strength ensures long-term stability, reducing maintenance and replacement costs while maximizing productivity and output.IV. Superior Thermal Shock Resistance:One of the most significant advantages of the Dense Castable Refractory 1700C is its inherent ability to withstand rapid temperature fluctuations. The material's unique composition minimizes the risk of cracks, spalling, and thermal stress, ensuring a reliable and durable refractory lining even in the most challenging thermal conditions. This translates into enhanced safety, reduced downtime, and improved operational efficiency for industries relying on heat-intensive processes.V. Versatile Applications:The Dense Castable Refractory 1700C's versatility makes it suitable for a wide range of industries. From blast furnaces, kilns, and incinerators to boilers, reactors, and furnaces, the refractory material adapts seamlessly to various high-temperature environments, ensuring optimum performance and longevity.VI. Commitment to Quality:(Company name removed) has always been at the forefront of innovation, prioritizing research and development to meet the evolving needs of industries. The Dense Castable Refractory 1700C is a testament to our dedication to providing cutting-edge solutions that surpass industry standards in quality, reliability, and performance. The product has undergone rigorous testing, adhering to stringent manufacturing processes to ensure consistency and integrity.VII. Environmental Sustainability:In addition to its remarkable performance characteristics, the Dense Castable Refractory 1700C is environmentally friendly. Manufactured with sustainable materials and processes that minimize waste, emissions, and energy consumption, it aligns with our commitment to sustainable practices and responsibility towards the environment.VIII. Conclusion:The introduction of the Dense Castable Refractory 1700C by (Company name removed) marks a significant milestone in high-temperature industrial applications. With its exceptional resistance to extreme temperatures and thermal shocks, as well as its superior durability and versatility, this revolutionary refractory material is set to revolutionize industries worldwide.As (Company name removed) remains dedicated to ongoing research and development, we anticipate continued advancements in refractory materials that will transform industries, enhance operational efficiency, and promote sustainable practices.
Discover the Benefits of High Alumina Bricks for Industrial Applications
High Alumina Bricks: A New Era of Durability and PerformanceIn the ever-evolving world of construction materials, High Alumina Bricks have emerged as a game-changer. Renowned for their exceptional durability and performance, these bricks are revolutionizing the way we approach industrial applications. One company leading the charge is {Company Name}, a pioneering manufacturer in the field. With their cutting-edge technology and unwavering commitment to quality, they are setting new industry standards and elevating the construction landscape to new heights.At its core, High Alumina Bricks are composed of high-purity alumina, a premium raw material renowned for its excellent refractory properties. These bricks are designed to withstand high temperatures, making them ideal for use in industries such as steel, cement, glass, and petrochemicals, where extreme heat is a constant challenge. Their ability to resist thermal spalling, corrosion, and thermal shock sets them apart from traditional refractory bricks, allowing for longer service life and reduced maintenance costs.{Company Name} has invested heavily in research and development, resulting in a state-of-the-art manufacturing process that produces High Alumina Bricks with unmatched quality and consistency. By utilizing advanced hydraulic presses and precision temperature control, they ensure that every brick adheres to the highest industry standards. These carefully curated manufacturing techniques guarantee high mechanical strength, low shrinkage, and excellent thermal stability, even under the harshest operating conditions.One of the most remarkable features of High Alumina Bricks is their ability to retain their strength and integrity at elevated temperatures. With a high melting point, these bricks can withstand temperatures of up to 1800°C, making them a reliable choice for industries operating in extreme environments. This unique characteristic enables safer and more efficient processes, reducing downtime and increasing productivity. High Alumina Bricks act as a barrier against heat transfer, minimizing energy losses and contributing to overall cost savings for industrial operations.{Company Name}, with its cutting-edge technology and emphasis on sustainability, has also refined the production of High Alumina Bricks with a reduced environmental footprint. By implementing energy-efficient systems and utilizing raw materials from sustainable sources, they have successfully lowered greenhouse gas emissions and minimized waste generation. Their commitment to environmental stewardship is in line with the growing global demand for eco-conscious construction materials.The many advantages of High Alumina Bricks have led to their increased adoption across various industries. In the steel manufacturing sector, these bricks are widely utilized in blast furnaces, hot blast stoves, and other high-temperature areas. In the cement industry, High Alumina Bricks have become crucial components of rotary kilns and preheating zones. Additionally, glass manufacturers rely on these bricks for their excellent resistance to molten glass corrosion. The oil and gas industry has also embraced High Alumina Bricks for lining fluid catalytic cracking units and other high-temperature vessels.With ongoing advancements in technology, the future of High Alumina Bricks looks even more promising. Researchers are exploring innovative ways to enhance the thermal insulation properties of these bricks, further maximizing their efficiency and reducing energy consumption. As industries strive for increased productivity and sustainability, High Alumina Bricks are set to play a pivotal role in transforming industrial processes.In conclusion, High Alumina Bricks have emerged as a game-changer in the construction materials industry, combining exceptional durability, unmatched performance, and sustainability. {Company Name}'s commitment to innovation and superior quality has positioned them as a leader in this field. As industries continue to seek reliable solutions for their high-temperature challenges, High Alumina Bricks will undoubtedly pave the way for a new era of durability and performance.
Discover the Advantages of High Alumina Insulation Bricks for Effective Thermal Insulation
High Alumina Insulation Bricks Revolutionize the Industrial LandscapeInnovation and continuous improvement are the driving forces behind success in the industrial sector. As industries evolve and demand for efficiency, performance, and durability increases, manufacturers must strive to offer cutting-edge solutions. One such groundbreaking product is High Alumina Insulation Bricks, developed by a pioneering company striving to set new standards in the industry.High Alumina Insulation Bricks, without mentioning the brand name, are engineered to provide exceptional insulation and thermal conductivity while offering superior strength and stability. These bricks serve as a critical component in industries where high-temperature applications are commonplace. Their unique design and composition make them ideal for a range of industries, including steel, petrochemical, ceramics, and power plants, among others.With their remarkably high alumina content, these bricks exhibit outstanding resistance to thermal shocks, ensuring longevity and reliability in extreme temperature conditions. The advanced manufacturing techniques employed allow for precise control over the brick's porosity and thermal conductivity, offering unrivaled insulation capabilities. This results in reduced heat loss, improved energy efficiency, and substantial cost savings for businesses relying on high-temperature processes.One of the key features of High Alumina Insulation Bricks lies in their low density, making them significantly lighter than traditional refractory bricks. This characteristic eases installation and handling processes, facilitating faster and more efficient construction, repair, and maintenance work. The reduced weight also minimizes the load on the supporting structure, contributing to enhanced safety and longevity.The exceptional mechanical strength and stability of these bricks make them extremely durable, capable of enduring rigorous industrial environments. High Alumina Insulation Bricks have a high crushing strength, ensuring they can withstand significant pressure without breaking or losing their insulating properties. This durability translates into reduced downtime and maintenance costs, further improving operational efficiency.Moreover, these bricks are highly resistant to chemical corrosion, making them suitable for applications in acidic and alkaline environments. They can withstand exposure to various acids, alkalis, and aggressive chemicals, preventing degradation and maintaining their integrity over time. This resistance to corrosion significantly expands their range of applications in industries where chemical processes are predominant.Aside from their formidable insulation properties, High Alumina Insulation Bricks also offer excellent dimensional stability under high temperatures. This characteristic is crucial in applications where dimensional changes can lead to operational issues or compromise production processes. Their stability ensures that critical equipment and structures maintain their shape and function, guaranteeing uninterrupted operations and minimizing downtime.The use of High Alumina Insulation Bricks represents a significant step forward in industrial insulation technology. With their exceptional thermal conductivity, remarkable durability, and resistance to thermal shocks and chemical corrosion, these bricks have revolutionized the industry. By providing superior insulation solutions, they enable businesses to optimize their processes, reduce energy consumption, and enhance productivity.In conclusion, High Alumina Insulation Bricks, developed by a leading company focused on innovation and quality, have emerged as a game-changer in the industrial sector. By combining advanced manufacturing techniques with a high alumina content, these bricks offer exceptional insulation capabilities, durability, and resistance to thermal shocks and chemical corrosion. The introduction of these bricks has undoubtedly raised the bar for insulation solutions and will continue to shape the industry's future.
What is a Carbon Paste Electrode and its Functions in Electroanalytical Chemistry?
Carbon Paste Electrode: A Breakthrough in Electrochemical AnalysisIn today's rapidly advancing world, the need for accurate and efficient analytical methods has become paramount. Whether it is in the field of medicine, environmental sciences, or even industrial processes, the ability to detect and quantify various substances has never been more crucial. Recognizing this need, scientists at {} have introduced a revolutionary product – the Carbon Paste Electrode, a cutting-edge tool that promises to revolutionize the field of electrochemical analysis.Electrochemical analysis involves the measurement and interpretation of electrical properties associated with chemical reactions. Traditionally, electrodes made from metals like platinum or gold have been utilized in this process. However, such electrodes often suffer from limitations such as high cost, limited availability, and a propensity for surface contamination. In recent years, carbon-based electrodes have emerged as a popular alternative due to their affordability, versatility, and improved chemical stability.The Carbon Paste Electrode developed by {} takes the advantages of carbon-based electrodes to a whole new level. Composed of a mixture of carbonaceous material and a binding agent, this innovative electrode offers unparalleled performance and superior accuracy in electrochemical analysis. Its unique composition enables precise detection and quantification of a wide range of substances, including heavy metals, organic compounds, and various analytes of interest in environmental and pharmaceutical industries.One of the key advantages of the Carbon Paste Electrode lies in its exceptional durability. Traditional electrodes often suffer from frequent wear and tear, leading to inconsistent results and increased costs. However, with its high mechanical strength, the Carbon Paste Electrode is capable of enduring numerous repetitive analyses without compromising accuracy or reliability. This longevity not only improves cost-efficiency but also ensures consistent analytical outcomes, making it an indispensable tool for researchers and scientists.Furthermore, the Carbon Paste Electrode exhibits remarkable sensitivity, thus enabling the detection of trace amounts of analytes. Its highly porous structure allows for greater surface area, facilitating enhanced mass transport and promoting rapid electron transfer, ultimately leading to improved sensitivity and detection limits. As a result, the electrode can detect even the most minute quantities of substances, providing invaluable information for crucial applications such as environmental monitoring and pharmaceutical research.In addition to its superior performance, the Carbon Paste Electrode also boasts exceptional versatility. With the ability to be easily modified with various surface modifiers and nanoparticles, this electrode can be tailored to specific analytes, making it an incredibly adaptable tool for different analytical needs. Moreover, its compatibility with different electrolytes and solvents further enhances its versatility, allowing for efficient electrochemical analysis across a wide range of sample matrices.As research and development continue to drive advancements in various industries, the demand for reliable analytical tools has never been greater. Recognizing this need, {} has delivered a game-changing solution in the form of the Carbon Paste Electrode. Its exceptional performance, durability, sensitivity, and versatility make it a top choice for scientists and researchers worldwide.With this groundbreaking invention, the field of electrochemical analysis is poised to take a significant leap forward. The superior capabilities of the Carbon Paste Electrode promise to revolutionize the way substances are detected and analyzed, paving the way for more accurate and efficient research in fields ranging from medicine to environmental sciences. As {} continues to innovate and redefine the boundaries of electrochemical analysis, the future looks bright for the scientific community as a whole.
How to Choose the Best Material for Your Refractory Casting Needs
Refractory Casting: Revolutionizing the Fireproof IndustryInnovation and constant evolution have always been fundamental aspects in the industrial world, and the fireproof industry is no exception. Refractory Casting has taken a step forward in this field, offering innovative solutions and products that have no competitors in terms of quality and durability. Focusing on their clients' needs, Refractory Casting has revolutionized the market by introducing high-end materials that can withstand extreme temperatures and workloads.Refractory Casting has quickly established itself as an important player in the refractory industry for its cutting-edge solutions, reliable quality, and outstanding service. Their products range from firebricks, insulating materials, mortar, and mineral wool to custom-made products that can meet even the most demanding requirements. The company is committed to productivity, safety, and cost-effectiveness, and its expertise is called upon in a variety of industries like steel, aluminum, cement, glass, and petrochemical.The company's mission is simple: "To offer excellence at a fair cost." This has been the philosophy behind Refractory Casting's business strategy, which prioritizes the quality of its products over everything else. The brand is synonymous with high-quality raw materials and expert craftsmanship, ensuring that its products always meet the highest standards in the industry.The company has multiple manufacturing plants across the globe, each specializing in different products. These plants are equipped with state-of-the-art machinery and follow strict safety and environmental protocols, ensuring that all workers and the environment are protected. Refractory Casting's products are tested rigorously and are certified by independent laboratories, guaranteeing their performance and durability.Refractory Casting's success is partially due to its ability to adapt to new challenges and demands. A testament to this is the company's recent contribution to the United States National Aeronautics and Space Administration's (NASA) 2020 Mars Rover mission. Refractory Casting provided the necessary materials for the rover's heat shield, making it possible for the rover to withstand the planet's harsh atmospheric conditions during its descent.In recent years, Refractory Casting has also been taking steps towards sustainability by developing environmentally friendly products and improving its manufacturing processes. The company has implemented programs to reduce energy consumption, waste, and emissions, while also increasing recycling rates and using sustainable raw materials.In summary, Refractory Casting is a leading player in the global refractory industry, thanks to its cutting-edge solutions, superior quality, and outstanding service. The company is committed to continuous innovation, productivity, safety, and cost-effectiveness, while also contributing to sustainability and being a reliable partner for various industries. The company's motto of "excellence at a fair cost" is reflected in every aspect of its business, and this is why Refractory Casting is a brand that clients can trust.
High-Quality Refractory Cement for Castable Applications
Title: Innovation in Refractory Technology: High-Quality Castable Refractory Cement Revolutionizes Industrial ApplicationsIntroduction:In the ever-evolving landscape of industrial materials, technological advancements play a crucial role in shaping the efficiency and effectiveness of various processes. One such breakthrough in the field of refractory materials is the advent of high-quality castable refractory cement, which has revolutionized the way industries approach their thermal management needs. In this article, we delve into the innovative properties and applications of this remarkable product, while also taking a closer look at the company behind its development and production.Company Introduction:{Company's Name}, a leader in refractory solutions, has been at the forefront of developing advanced materials to meet the evolving demands of various industries. With a steadfast commitment to research and development, {Company's Name} has consistently introduced cutting-edge products that enhance the performance, durability, and sustainability of industrial processes. The company's expert team of scientists, engineers, and technicians work tirelessly to develop and perfect innovative refractory materials, placing {Company's Name} in a favorable position in the market.High-Quality Castable Refractory Cement: Unveiling Unmatched Performance{Company's Name} has recently introduced its highly anticipated High-Quality Castable Refractory Cement, a game-changer in the realm of thermal management solutions. This remarkable product has been engineered to withstand extreme temperatures while maintaining exceptional strength and durability. With a unique combination of raw materials and a meticulous manufacturing process, this advanced refractory cement has proved its mettle across various industries, demonstrating its versatility and reliability.Properties and Advantages:1. Exceptional Thermal Insulation: High-Quality Castable Refractory Cement exhibits excellent thermal insulation properties, effectively preventing heat loss from industrial furnaces, kilns, and other heated applications. Its low thermal conductivity ensures optimal energy conservation, leading to reduced fuel consumption and lower operational costs.2. Superior Strength and Abrasion Resistance: The cement's exceptional strength and resistance to abrasion make it ideal for withstanding the rigors of high-temperature environments. Its robust nature ensures prolonged service life and minimal maintenance disruptions, resulting in enhanced productivity and cost-effectiveness.3. Chemical and Corrosion Resistance: The castable refractory cement is highly resistant to various chemicals, acids, and corrosive elements, making it suitable for applications in industries such as steel, petrochemicals, and ceramics. This resistance safeguards against premature material degradation, ensuring reliable and long-lasting performance.4. Ease of Installation and Adaptability: High-Quality Castable Refractory Cement can be easily provided in various shapes and sizes, facilitating its installation and adaptation to specific industrial requirements. Its ability to conform to complex geometries enhances the efficiency of heat transfer processes, effectively optimizing system performance.Applications across Industries:1. Steel Industry: The cement finds extensive utility in steelmaking, providing strong linings for furnaces, ladles, and tundishes, improving thermal efficiency and maximizing production output.2. Petrochemical Industry: High-Quality Castable Refractory Cement proves invaluable in petrochemical applications, where it is used to line reactors, furnaces, and cyclones, providing reliable insulation and protection against corrosive substances.3. Ceramic and Glass Industry: With its excellent thermal insulation and resistance to molten materials, the cement effectively lines kilns, melting pots, and glass tanks, ensuring uniform heating and controlled cooling for optimized production processes.4. Power Generation: In power plants, this innovative refractory cement is used to line boilers and chimney stacks, withstanding high temperatures and reducing heat losses, thereby increasing the overall system efficiency.Conclusion:High-Quality Castable Refractory Cement, developed and produced by {Company's Name}, has paved the way for a new era of thermal management solutions. The exceptional properties and advantages of this advanced product have proven to be invaluable to various industries, enhancing productivity, cost-effectiveness, and environmental sustainability. As {Company's Name} continues to innovate and push the boundaries of refractory technology, they cement their position as a leading provider of cutting-edge materials, driving industrial progress towards a more efficient and sustainable future.
Thermal Insulation Board Made of Ceramic Fiber: A Perfect Solution for High-Temperature Applications.
Ceramic fiber thermal insulation boards have revolutionized the construction and insulation industry with their unique properties and exceptional performance. These boards, which are made from high-quality ceramic fiber materials, offer extraordinary thermal efficiency, making them an ideal choice for a wide range of applications.One prominent company, recognized globally for its expertise in manufacturing and distributing ceramic fiber insulation products, has introduced a groundbreaking line of thermal insulation boards to meet the growing demands of the industry. These boards, developed using state-of-the-art technology and innovative manufacturing processes, have quickly gained popularity due to their exceptional insulation capabilities, durability, and versatility.With advancements in energy-saving technologies becoming increasingly important in the construction industry, the use of ceramic fiber thermal insulation boards has become a key factor in achieving optimal energy efficiency in buildings. These boards act as a highly effective barrier, reducing the transfer of heat and maintaining a stable temperature indoors, regardless of external conditions. By minimizing heat loss and preventing the ingress of cold air, these insulation boards help to significantly reduce heating costs during winter months and maintain cool temperatures during scorching summers.Additionally, ceramic fiber thermal insulation boards have excellent fire resistance, making them an ideal choice for areas requiring enhanced safety measures. Their non-combustible nature ensures that even in the event of a fire, the spread of flames and the release of toxic gases are kept to a minimum, providing valuable time for evacuation and minimizing potential damage. This quality has made these boards highly sought-after in industries such as petrochemical, power generation, and manufacturing plants, where fire safety measures are of paramount importance.Furthermore, the unique physical properties of ceramic fiber insulation boards contribute to their longevity and durability. These boards are highly resistant to wear, tear, and corrosion, ensuring a long lifespan even in harsh environments. Their resistance to moisture absorption and chemical reactions makes them an excellent choice for applications in areas prone to high humidity, such as swimming pools, spas, and industrial facilities.The versatility of ceramic fiber thermal insulation boards is another factor contributing to their popularity. These boards can be easily cut, shaped, and installed to fit even the most complex architectural designs and structural requirements. They are lightweight, reducing the overall load on the structure, making them particularly suitable for retrofitting existing buildings or installing in areas where weight considerations are crucial.Moreover, the manufacturing process used by this renowned company ensures that their ceramic fiber thermal insulation boards are ecologically friendly and suitable for sustainable construction practices. These boards are manufactured using recycled materials and by-products from other industries, reducing waste and minimizing their environmental impact. Their energy-saving properties further contribute to reducing greenhouse gas emissions and promoting a greener environment.The introduction of these innovative ceramic fiber thermal insulation boards by this industry-leading company showcases their commitment to providing cutting-edge solutions to the construction and insulation sector. With their exceptional thermal efficiency, fire resistance, durability, and versatility, these boards have quickly become an indispensable component in energy-efficient buildings and structures worldwide.In conclusion, ceramic fiber thermal insulation boards have revolutionized the insulation industry, offering unparalleled thermal efficiency, fire resistance, durability, and versatility. The introduction of a groundbreaking line of these boards by a globally recognized company signifies their dedication to providing innovative, sustainable, and high-performing solutions. As the demand for energy-efficient buildings continues to grow, ceramic fiber thermal insulation boards are set to play a crucial role in achieving optimal insulation and reducing energy consumption in the construction industry.
The latest developments in refractory casting techniques and applications
Refractory casting is an essential process in the manufacturing industry, playing a crucial role in the production of various products such as steel, glass, ceramics, and cement. The process involves pouring a liquid material, usually a mixture of refractory material and binding agents, into a mold to create a specific shape that can withstand high temperatures and harsh environments. This process is fundamental in the development of industrial products and plays a critical role in the overall manufacturing process.{Company Name} is a leading provider of refractory casting services, with a strong reputation for delivering high-quality and reliable solutions to its clients. The company specializes in providing custom refractory casting solutions for a wide range of industries, including steelmaking, glass manufacturing, foundries, and more. With a team of experienced professionals and state-of-the-art facilities, {Company Name} has earned a reputation for excellence and innovation in the field of refractory casting.One of the key factors that set {Company Name} apart from its competitors is its commitment to using the latest technologies and materials to create superior refractory casting solutions. The company invests heavily in research and development to ensure that its clients receive the most advanced and effective products on the market. This dedication to innovation allows {Company Name} to stay ahead of industry trends and continue to provide cutting-edge solutions to its clients.In addition to its focus on innovation, {Company Name} is also known for its dedication to customer satisfaction. The company works closely with its clients to understand their specific needs and requirements, providing tailored solutions that meet and exceed expectations. Whether it's creating custom molds for unique shapes or developing specialized refractory materials for specific applications, {Company Name} is committed to delivering superior results for its clients.Furthermore, {Company Name} prides itself on its commitment to sustainability and environmental responsibility. The company actively seeks out eco-friendly materials and processes to minimize its impact on the environment. By prioritizing sustainability, {Company Name} not only benefits the planet but also provides its clients with responsible and ethically-sourced refractory casting solutions.In recent news, {Company Name} has announced the launch of a new and improved refractory casting process. This updated process incorporates the latest advancements in materials and technology to provide even better performance and longevity for industrial applications. By continually evolving and refining its casting process, {Company Name} aims to maintain its position as a leader in the industry and continue to meet the evolving needs of its clients.The new and improved casting process offers enhanced durability and resistance to high temperatures, making it an ideal choice for demanding industrial applications. With this development, {Company Name} once again demonstrates its dedication to providing top-of-the-line solutions for its clients and solidifying its reputation as an industry leader in refractory casting.{Company Name} is excited to introduce this enhanced casting process to its clients, as it represents a significant step forward in the company's commitment to excellence and innovation. With this new development, {Company Name} aims to set new standards for refractory casting and continue to meet the evolving needs of the manufacturing industry.As {Company Name} continues to push the boundaries of what's possible in refractory casting, clients can expect to receive even more advanced and efficient solutions for their manufacturing needs. This commitment to innovation and performance solidifies {Company Name}'s position as a reliable and industry-leading provider of refractory casting solutions. With its dedication to sustainability, customer satisfaction, and continuous improvement, {Company Name} is well-positioned to continue its success and provide exceptional casting solutions for years to come.
High-Quality Magnesia Bricks for Sale - Durable & Heat-Resistant Options Available
China is the world's largest producer of magnesia, a mineral used in numerous industrial applications such as refractories, fertilizers, and construction materials. No wonder that Chinese companies hold a significant share in the global market for magnesia- based products. One such company, located in the Henan Province of China, serves as a prime example of the country's prowess when it comes to this crucial mineral.The company is a leading manufacturer of magnesia-based products, with a focus on refractory materials used in high-temperature environments. Refractory materials are critical for industries such as steel-making, cement production, and glass- making, where high temperatures and harsh conditions can put enormous stress on the equipment and structures used.The company specializes in producing magnesia bricks, which are an essential component in many furnaces and kilns. Magnesia bricks are made of high-purity magnesia, a refractory mineral that is highly resistant to heat, corrosion, and wear. They are used in industries such as steel, non-ferrous metals, cement, and glass, with applications ranging from lining of furnaces and kilns to the construction of chimneys and heat exchangers.To guarantee the quality of its magnesia bricks, the company sources the best raw materials from trusted suppliers and implements rigorous quality control systems from the production process to the delivery of finished products. This careful attention to quality has earned the company a reputation of excellence and trust among its customers, who rely on its products to keep their operations running smoothly.Now, the company's magnesia bricks are available for purchase worldwide, through its online platform, which ensures fast and reliable delivery of high-quality products to customers across the globe. The company's online store offers a variety of magnesia bricks for different temperatures and applications, with custom sizes and shapes available upon request. Furthermore, its website provides technical specifications, product data sheets, and safety information to help customers choose the right magnesia bricks for their specific needs.Customers can benefit from the company's expertise in refractory materials, as it also offers consultation and customization services to help them find the best solutions for their particular requirements. Whether it is for a small-scale project or a large industrial application, the company's team of experts can help customers design, implement, and maintain their refractory systems for optimal performance and longevity.The company's commitment to quality, innovation, and customer satisfaction has enabled it to become a trusted partner for many businesses worldwide, as it continues to expand its product lines and services to meet the evolving needs of its customers. Its mission to provide sustainable and cost-effective solutions for high-temperature applications has driven its growth and success, making it a leading player in the global market for refractory materials.In conclusion, the Chinese company's magnesia bricks offer a durable and heat-resistant solution for a wide range of industrial applications, with a reputation for excellence and reliability. Through its online platform and customer-oriented services, it has become an accessible and trustworthy partner for businesses seeking quality refractory materials. Its dedication to innovation and sustainability ensures that it remains at the forefront of the industry, as it continues to provide solutions that enhance the efficiency and productivity of its customers' operations.