High-quality Corundum Brick for Industrial Applications
By:Admin
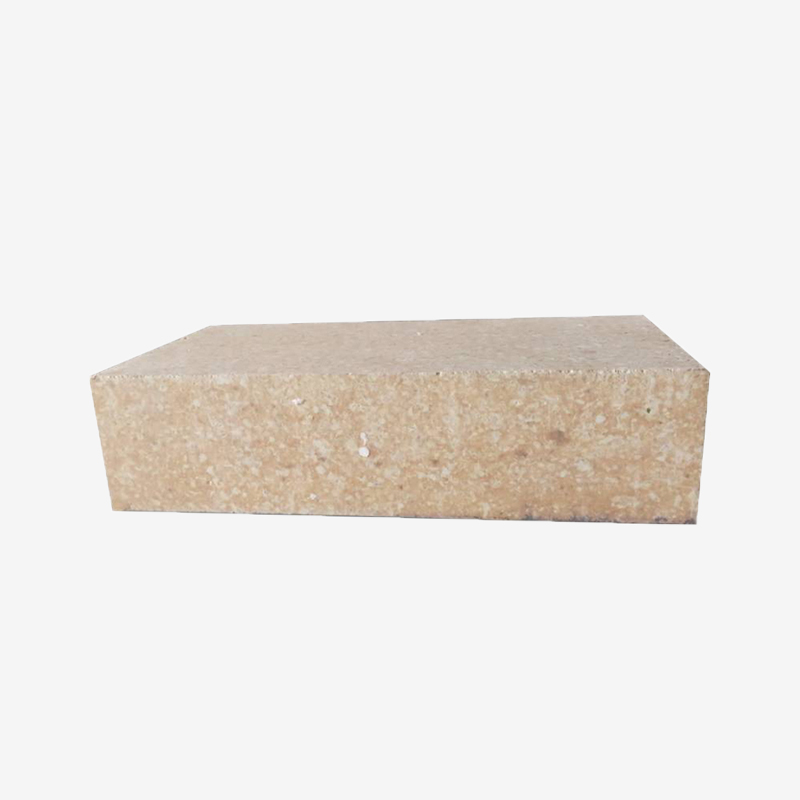
The company behind Corundum Brick is known for its commitment to excellence and innovation. With a strong emphasis on research and development, they have been able to produce a range of refractory products that meet the ever-evolving needs of the market. Their state-of-the-art manufacturing facilities and strict quality control measures ensure that each product meets the highest standards of performance and reliability.
One of the key features of Corundum Brick is its high level of purity, which makes it highly resistant to chemical and physical degradation. This, combined with its excellent thermal conductivity, makes it an ideal choice for applications that involve high temperatures and aggressive chemical environments. From blast furnaces and steel-making facilities to petrochemical plants and incinerators, Corundum Brick has been proven to perform reliably under the most demanding conditions.
Furthermore, the company's dedication to sustainability is reflected in the production process of Corundum Brick. They have implemented environmentally friendly practices to minimize their impact on the environment, such as using recycled materials and optimizing energy usage. As a result, their refractory products not only deliver exceptional performance but also contribute to a more sustainable and eco-friendly industrial landscape.
In addition to its superior technical properties, Corundum Brick is also known for its ease of installation and maintenance. Its consistent dimensions and precise shapes ensure a perfect fit during construction, while its resistance to wear and abrasion minimizes the need for frequent replacements. This not only reduces downtime and maintenance costs but also enhances the overall efficiency of industrial operations.
The company's commitment to customer satisfaction is another aspect that sets them apart in the industry. They offer comprehensive technical support and consultation services to help clients select the most suitable refractory solutions for their specific needs. Furthermore, their responsive customer service team is always ready to address any inquiries or concerns, ensuring a smooth and seamless experience for every client.
As the demand for high-performance refractory products continues to grow, Corundum Brick has established itself as a trusted choice for countless industrial applications. Its track record of success in a wide range of industries, combined with the company's dedication to excellence and sustainability, positions it as a leading player in the global refractory market.
Looking ahead, the company remains committed to pushing the boundaries of innovation and delivering top-quality products that exceed the expectations of their clients. With a keen focus on research and development, they are constantly exploring new technologies and materials to further enhance the performance and versatility of their refractory solutions.
In conclusion, Corundum Brick, manufactured by a reputable and forward-thinking company, stands as a symbol of reliability, durability, and sustainability in the refractory industry. Its exceptional technical properties, combined with the company's unwavering commitment to excellence, make it a top choice for industrial applications where performance and longevity are non-negotiable. As the industry continues to evolve, Corundum Brick is poised to remain at the forefront of innovation and set new benchmarks for refractory excellence.
Company News & Blog
All You Need to Know About Monolithic Castable Refractory for High-Temperature Applications
Monolithic Castable Refractory – Revolutionizing the Refractory IndustryIn the world of heavy industries, refractories play a significant role in ensuring the longevity of high-temperature equipment. Refractories are inorganic, non-metallic materials that can withstand extreme temperatures and harsh environments. They are used as insulators for furnaces, kilns, incinerators, and reactors. Refractories are also used as lining materials in industries such as cement, steel, aluminum, and petrochemical.However, traditional refractory materials such as bricks, tiles, and precast shapes have certain limitations. These materials are time-consuming and require skilled labor for installation. They also have low thermal shock resistance and exhibit cracking, spalling, and erosion after a short period. This leads to frequent maintenance, downtime, and loss of productivity.To overcome these challenges, manufacturers have developed new types of refractory materials, including monolithic castable refractory. This is a revolutionary material that has completely transformed the refractory industry. In this news article, we will explore the benefits and advancements of this innovative material and its impact on various industries.What is Monolithic Castable Refractory?Monolithic castable refractory is a type of refractory material that is made by combining various raw materials such as fine grain, coarse grain, bonding agents, and additives. The mixture is then placed into a mold or sprayed onto a surface. It hardens when exposed to high temperatures and forms a monolithic, seamless structure. The term “monolithic” refers to the fact that it is a single piece, as opposed to traditional refractory materials that are made of multiple pieces.This type of refractory material offers numerous advantages over traditional materials. They include:Less Labor Intensive – Monolithic castables are easier to install compared to traditional materials. They can be poured, sprayed or troweled into place, reducing the need for skilled labor. This significantly lowers the cost of installation and maintenance.Better Insulation Properties - Monolithic castables offer better insulation than traditional materials. This is because they have fewer joints and cracks, which reduce heat loss. This translates to lower energy costs and improved thermal efficiency.Higher Thermal Shock Resistance – Monolithic castables have high thermal shock resistance, which means that they can withstand rapid temperature changes without cracking or spalling. This prolongs the lifespan of the material, reduces maintenance costs and minimizes downtime.Wide Range of Applications – Monolithic castables have a wide range of applications in various industries. They are used as linings in furnaces, kilns, incinerators, and reactors. They are also used as insulating materials for pipes, ducts, boilers, chimneys, and stacks. Their versatility makes them suitable for a broad range of applications.Company Introduction{Remove Brand Name} is a leading global manufacturer of monolithic castable refractory materials. The company was founded over 70 years ago and has since then grown into a global leader in the refractories industry. {Remove Brand Name} offers a wide range of refractory solutions to various industries, including steel, cement, power generation, petrochemical, and aluminum.{Remove Brand Name} has a team of experienced scientists and engineers who are dedicated to developing innovative, high-quality products that meet the needs of their clients. They use state-of-the-art manufacturing processes and equipment to ensure that their products are of the highest quality.{Remove Brand Name} has a strong commitment to sustainable practices, which is reflected in their use of eco-friendly, sustainable raw materials, and their focus on reducing waste and emissions. They work closely with clients to identify their needs and provide customized solutions that meet their specific requirements.Recent DevelopmentsIn recent years, {Remove Brand Name} has made significant advancements in the development of monolithic castable refractory materials. They have developed new products that offer even better thermal performance, insulation, and durability.One of their recent innovations is the use of advanced nanotechnology in their refractory materials. This technology involves the use of nanoparticles that are dispersed throughout the material. The nanoparticles enhance the material's thermal properties, such as thermal conductivity, radiation absorption, and insulation. This results in better thermal efficiency, reduced energy costs, and improved overall performance.{Remove Brand Name} has also developed new manufacturing processes that reduce the environmental impact of their products. They use renewable, eco-friendly raw materials, and reduce waste and emissions during the manufacturing process. This ensures that their products are both high-quality and sustainable.ConclusionIn conclusion, monolithic castable refractory materials have revolutionized the refractory industry. They offer numerous advantages over traditional materials, such as reduced labor costs, better insulation, and higher thermal shock resistance. {Remove Brand Name} is a leading manufacturer of high-quality monolithic castable refractory materials. They have made significant advancements in the development of new products that offer even better thermal performance and durability. With their strong commitment to sustainable practices and client-focused approach, {Remove Brand Name} is poised to continue leading the way in the refractory industry.
Durable and high-quality furnace bricks for your industrial needs
Yellow furnace bricks are a crucial component in the construction and manufacturing industry, known for their durability and heat resistance. These high-quality bricks are used in a wide range of applications, from industrial furnaces and kilns to residential fireplaces and chimneys. With their exceptional thermal conductivity and strength, yellow furnace bricks are a popular choice for projects that require reliable and long-lasting building materials.One company that has been a leading manufacturer of yellow furnace bricks is {}. With over 20 years of experience in the industry, {} has built a reputation for producing top-notch furnace bricks that meet the highest standards of quality and performance. The company's state-of-the-art manufacturing facilities and stringent quality control processes ensure that their bricks are consistently of superior quality, making them a trusted choice for construction and manufacturing projects around the world.{} offers a wide range of yellow furnace bricks, catering to various temperature and application requirements. Their high-alumina bricks are designed to withstand extreme temperatures, making them ideal for use in industrial furnaces and kilns. These bricks are carefully engineered to provide excellent thermal insulation and resistance to chemical corrosion, allowing them to maintain their structural integrity even in the most demanding environments.In addition to high-alumina bricks, {} also produces fireclay bricks that are specifically formulated for use in residential fireplaces and chimneys. These bricks are known for their superior heat retention and fire resistance, making them a popular choice for homeowners and builders who prioritize safety and durability. With a wide range of sizes and shapes available, {} can accommodate a variety of construction and design needs, ensuring that their clients have access to the perfect furnace bricks for their specific projects.As a customer-focused company, {} is committed to providing exceptional service and support to their clients. Their team of experts is dedicated to helping customers find the right furnace bricks for their applications, offering technical guidance and assistance to ensure that every project is a success. With a strong emphasis on quality and reliability, {} has earned the trust and loyalty of numerous clients who rely on their furnace bricks for their critical construction and manufacturing needs.Beyond their commitment to quality and customer satisfaction, {} also places a strong emphasis on environmental responsibility. The company's manufacturing processes are designed to minimize waste and emissions, prioritizing sustainability and eco-friendliness. By adhering to strict environmental standards, {} ensures that their products not only meet the highest performance requirements but also contribute to a cleaner and greener planet.Looking to the future, {} is continuously investing in research and development to further enhance the performance and capabilities of their furnace bricks. By staying at the forefront of technological advancements and industry trends, {} aims to continue providing cutting-edge solutions to their clients, further solidifying their position as a trusted leader in the field of furnace bricks.In conclusion, yellow furnace bricks are an essential building material in the construction and manufacturing industry, renowned for their exceptional durability and heat resistance. With a strong focus on quality, customer satisfaction, and environmental responsibility, {} has established itself as a premier manufacturer of high-quality furnace bricks. Their commitment to innovation and excellence ensures that {} will remain a trusted partner for clients seeking reliable and long-lasting furnace bricks for their projects.
Discover the Benefits of High-Quality Castable Refractory Cement
High-Quality Castable Refractory Cement Offers Superior Performance for Industrial Applications[Company Name], a leading provider of high-quality refractory products, is proud to announce the launch of its new High-Quality Castable Refractory Cement. This cutting-edge cement offers superior performance and durability, making it an ideal choice for a wide range of industrial applications.With a long history of excellence in the refractory industry, [Company Name] has built a reputation for providing top-quality products that meet the demanding needs of its customers. The company's commitment to innovation and continuous improvement has led to the development of the High-Quality Castable Refractory Cement, an advanced solution that delivers exceptional performance in high-temperature environments.The High-Quality Castable Refractory Cement is formulated using a carefully balanced blend of high-quality raw materials, including high-purity alumina, silicate, and other proprietary ingredients. This unique composition ensures that the cement exhibits excellent thermal stability, abrasion resistance, and strength, making it well-suited for use in challenging industrial settings.One of the key features of the High-Quality Castable Refractory Cement is its exceptional resistance to thermal shock. This means that the cement can withstand rapid changes in temperature without experiencing cracking or degradation, ensuring long-term reliability and performance in demanding applications. Additionally, the cement's high abrasion resistance allows it to withstand the harsh conditions present in industrial furnaces, boilers, and kilns without succumbing to wear and tear.The High-Quality Castable Refractory Cement is also designed to offer exceptional workability, allowing for easy and precise installation in a variety of shapes and configurations. Its smooth consistency and excellent bonding properties make it an excellent choice for lining and repairing refractory structures, providing a reliable and long-lasting solution for industrial facilities.In addition to its outstanding performance characteristics, the High-Quality Castable Refractory Cement is also environmentally friendly, with low emissions and minimal environmental impact during manufacturing and use. This aligns with [Company Name]'s commitment to sustainability and responsible business practices, ensuring that customers can benefit from a high-performance product that also supports their environmental goals."We are thrilled to introduce our new High-Quality Castable Refractory Cement to the market," said [Name], [Title] at [Company Name]. "This innovative product represents the culmination of our extensive expertise and dedication to meeting the needs of our customers. We believe that the cement's exceptional performance and environmental benefits will make it a preferred choice for a wide range of industrial applications."The introduction of the High-Quality Castable Refractory Cement further solidifies [Company Name]'s position as a leading provider of advanced refractory solutions. With a strong focus on quality, innovation, and customer satisfaction, the company continues to drive progress in the industry, offering products that meet the evolving needs of modern industrial operations.As industrial facilities continue to push the boundaries of performance and efficiency, the demand for reliable and high-performance refractory solutions is greater than ever. With the launch of the High-Quality Castable Refractory Cement, [Company Name] is well-positioned to meet this demand, offering a product that delivers outstanding performance, durability, and environmental responsibility.The High-Quality Castable Refractory Cement is now available for purchase, and interested customers can contact [Company Name] for more information and to discuss their specific application needs. With its exceptional qualities and proven track record, the cement is poised to become a go-to choice for industrial operators seeking a reliable and high-performance refractory solution.
High-Quality Magnesite Refractory Bricks Meet Growing Demand in Steel Industry
Title: Evolving Magnesite Refractory Bricks Industry Emphasizes Quality and SustainabilityIntroduction:In recent times, the magnesite refractory bricks industry has been witnessing significant growth, driven by the increasing demand for high-quality refractory materials in various sectors. Magnesite refractory bricks, renowned for their exceptional heat resistance and durability, are widely utilized in industries like steel, cement, glass, non-ferrous metals, ceramics, etc., supporting critical processes that require elevated temperatures.Company Introduction:{Company Name} is a prominent player in the magnesite refractory bricks market, dedicated to producing top-notch products that meet the evolving needs of its customers. With years of industry experience, cutting-edge technology, and a strong focus on sustainability, {Company Name} has positioned itself as a trusted provider of magnesite refractory brick solutions worldwide.Evolution of the Magnesite Refractory Bricks Industry:The magnesite refractory bricks industry has experienced remarkable advancements in recent years. Formerly, the dominant types of refractories used were chrome bricks, but due to environmental concerns related to hexavalent chromium, there has been a gradual shift towards magnesite refractory bricks, known for their high refractoriness and excellent chemical properties.The versatility of magnesite refractory bricks has driven their adoption in various industries, replacing traditional refractory materials. Modern manufacturing processes have been optimized to enhance the physical and chemical properties of these bricks, making them increasingly resistant to thermal shocks and the corrosive effects of chemicals found in harsh industrial environments.Technological Innovations and Product Enhancements:{Company Name} recognizes the importance of technological advancements in staying ahead in the highly competitive market. The company consistently invests in research and development, aiming to improve the performance and durability of magnesite refractory bricks. High-precision manufacturing techniques, such as hot pressing, enable {Company Name} to produce bricks with more consistent and superior quality, ensuring excellent resistance to thermal stress and prolonged service life.Furthermore, {Company Name}'s commitment to sustainable practices is reflected in its innovative use of environmentally friendly raw materials and energy-efficient processes. By incorporating recycled materials within its manufacturing process, the company aims to reduce its carbon footprint and contribute to a greener future.Meeting Industry-Specific Demands:As diverse industries pose unique challenges, {Company Name} understands the importance of customizing magnesite refractory brick solutions accordingly. For instance, in the steel industry, refractory materials are exposed to extreme temperatures and harsh conditions during the smelting process. To address these challenges, {Company Name} has developed advanced magnesite refractory bricks with superior thermal stability, minimizing material degradation and extending the overall service life of the refractories.Moreover, {Company Name}'s research and development team works closely with customers, providing technical support and developing tailored solutions specific to their requirements. This customer-centric approach has fostered strong and lasting partnerships with clients across the globe.Commitment to Quality and Customer Satisfaction:{Company Name}'s commitment to quality and customer satisfaction has propelled its position in the market. The company adheres to strict quality control procedures, guaranteeing that each magnesite refractory brick meets stringent international standards. Moreover, providing exceptional after-sales service and technical assistance ensures that customers maximize the value and performance of {Company Name}'s refractory solutions.Conclusion:The magnesite refractory bricks industry is witnessing transformational changes as sustainability, high performance, and customized solutions become paramount. {Company Name} is at the forefront of this evolution, delivering top-quality magnesite refractory bricks while embracing innovation and sustainable practices. With its unwavering commitment to customer satisfaction and its focus on technological advancements, {Company Name} is well-positioned to meet the ever-increasing demand for superior refractory materials in the global market.
The latest developments in refractory casting techniques and applications
Refractory casting is an essential process in the manufacturing industry, playing a crucial role in the production of various products such as steel, glass, ceramics, and cement. The process involves pouring a liquid material, usually a mixture of refractory material and binding agents, into a mold to create a specific shape that can withstand high temperatures and harsh environments. This process is fundamental in the development of industrial products and plays a critical role in the overall manufacturing process.{Company Name} is a leading provider of refractory casting services, with a strong reputation for delivering high-quality and reliable solutions to its clients. The company specializes in providing custom refractory casting solutions for a wide range of industries, including steelmaking, glass manufacturing, foundries, and more. With a team of experienced professionals and state-of-the-art facilities, {Company Name} has earned a reputation for excellence and innovation in the field of refractory casting.One of the key factors that set {Company Name} apart from its competitors is its commitment to using the latest technologies and materials to create superior refractory casting solutions. The company invests heavily in research and development to ensure that its clients receive the most advanced and effective products on the market. This dedication to innovation allows {Company Name} to stay ahead of industry trends and continue to provide cutting-edge solutions to its clients.In addition to its focus on innovation, {Company Name} is also known for its dedication to customer satisfaction. The company works closely with its clients to understand their specific needs and requirements, providing tailored solutions that meet and exceed expectations. Whether it's creating custom molds for unique shapes or developing specialized refractory materials for specific applications, {Company Name} is committed to delivering superior results for its clients.Furthermore, {Company Name} prides itself on its commitment to sustainability and environmental responsibility. The company actively seeks out eco-friendly materials and processes to minimize its impact on the environment. By prioritizing sustainability, {Company Name} not only benefits the planet but also provides its clients with responsible and ethically-sourced refractory casting solutions.In recent news, {Company Name} has announced the launch of a new and improved refractory casting process. This updated process incorporates the latest advancements in materials and technology to provide even better performance and longevity for industrial applications. By continually evolving and refining its casting process, {Company Name} aims to maintain its position as a leader in the industry and continue to meet the evolving needs of its clients.The new and improved casting process offers enhanced durability and resistance to high temperatures, making it an ideal choice for demanding industrial applications. With this development, {Company Name} once again demonstrates its dedication to providing top-of-the-line solutions for its clients and solidifying its reputation as an industry leader in refractory casting.{Company Name} is excited to introduce this enhanced casting process to its clients, as it represents a significant step forward in the company's commitment to excellence and innovation. With this new development, {Company Name} aims to set new standards for refractory casting and continue to meet the evolving needs of the manufacturing industry.As {Company Name} continues to push the boundaries of what's possible in refractory casting, clients can expect to receive even more advanced and efficient solutions for their manufacturing needs. This commitment to innovation and performance solidifies {Company Name}'s position as a reliable and industry-leading provider of refractory casting solutions. With its dedication to sustainability, customer satisfaction, and continuous improvement, {Company Name} is well-positioned to continue its success and provide exceptional casting solutions for years to come.
Discover the Benefits of Acid Resistant Refractory Castable for Your Needs
[Your Name][Date]Acid Resistant Refractory Castable: Revolutionizing High-Temperature Applications[City, State] - Acid Resistant Refractory Castable, an innovative product developed by [Company Name], is set to revolutionize high-temperature applications across a range of industries. With its exceptional durability and resistance to acidic environments, this castable material is a game-changer for businesses seeking reliable and cost-effective solutions.[Company Name] has been at the forefront of refractory materials for [number of years] years, specializing in the development and production of advanced ceramics and composite materials. With a dedicated team of researchers and engineers, the company has consistently pushed the boundaries of what is achievable in high-temperature applications.Acid Resistant Refractory Castable is the result of extensive research and development efforts by [Company Name]. This cutting-edge product offers superior resistance to acids, alkalis, and other corrosive substances found in various industrial processes. By withstanding the harshest conditions, this castable material significantly extends the service life of refractory linings, thereby reducing downtime and maintenance costs for businesses.One of the key advantages of Acid Resistant Refractory Castable is its exceptional chemical stability. The unique composition of the castable material allows it to withstand continuous exposure to strong acids, such as sulfuric acid and hydrochloric acid, without deteriorating or losing its properties. This not only enhances the overall performance of the refractory lining but also ensures the safety of personnel working in corrosive environments.Furthermore, the castable material exhibits excellent thermal shock resistance, enabling it to withstand rapid temperature changes without cracking or spalling. It can endure temperatures of up to [temperature range], making it suitable for a wide range of applications, including furnaces, kilns, reactors, and various chemical processing equipment.The installation process of Acid Resistant Refractory Castable is efficient and convenient, thanks to its excellent workability and flowability. This allows for precise and uniform casting, ensuring a seamless refractory lining that maximizes performance and reduces heat loss. Moreover, the material demonstrates excellent adhesion to various substrates, including bricks, steel, and concrete, providing a reliable and long-lasting solution for businesses.To meet the diverse requirements of different industries, [Company Name] offers customizable options for Acid Resistant Refractory Castable. The product can be tailored to specific project needs, including different chemical resistance levels, particle size distributions, and setting times. This flexibility ensures that customers receive a product that precisely matches their unique application requirements.Acid Resistant Refractory Castable has garnered positive feedback from numerous industries, including the petrochemical, metallurgical, and power generation sectors. "We have witnessed a noticeable improvement in the durability of our refractory linings after switching to Acid Resistant Refractory Castable," said [Company representative]. "This has led to significant cost savings and increased overall operational efficiency."[Company Name] continues to invest in cutting-edge research and development, striving to improve and expand their product line to meet evolving industry demands. In addition to Acid Resistant Refractory Castable, the company offers a wide range of refractory materials and solutions, including monolithic castables, ceramic fiber products, and high-temperature insulation materials.With Acid Resistant Refractory Castable, [Company Name] is leading the charge in providing reliable and cost-effective solutions for high-temperature applications. This revolutionary product is set to reshape several industries, enabling businesses to operate in corrosive environments with confidence, durability, and enhanced efficiency.About [Company Name]:[Company Name] is a leading provider of advanced refractory materials and solutions. With a strong focus on research and development, the company offers a wide range of high-quality products that cater to diverse industry needs. [Company Name]'s commitment to innovation, quality, and customer satisfaction has positioned it as a trusted partner for businesses worldwide.For media inquiries, please contact:[Company Contact Information]
Durable and High-Quality Alumina Fire Brick for Various Applications
High-Quality Alumina Fire Brick: The Ultimate Heat-Resistant SolutionIn the world of industrial applications, high temperatures are a common challenge. From the steel industry to glass manufacturing and beyond, the need for materials that can withstand extreme heat is essential. This is where high-quality alumina fire bricks come into play, offering a solution that is both reliable and effective in protecting against the intense heat of industrial processes.One company that is at the forefront of providing high-quality alumina fire bricks is {company name}. With a strong reputation for excellence in the field of refractory materials, {company name} has been a key player in meeting the needs of various industries that rely on heat-resistant materials.{Company name} has a long history of producing high-quality refractory products, and their alumina fire bricks are no exception. Made from high-grade alumina, these fire bricks are designed to withstand temperatures of up to 1700°C, making them an ideal choice for applications where extreme heat is a constant factor.The secret to the exceptional heat resistance of {company name}'s alumina fire bricks lies in their composition. These bricks are made from high-purity raw materials, which are carefully selected to ensure the highest level of quality and performance. In addition, the manufacturing process is closely monitored to guarantee that every brick meets the company's stringent standards for durability and reliability.One of the key advantages of {company name}'s alumina fire bricks is their versatility. These bricks are suitable for a wide range of industrial applications, including furnaces, kilns, incinerators, and more. Regardless of the specific industry or process, these fire bricks can be relied upon to provide the heat resistance and protection needed to keep operations running smoothly.In addition to their exceptional heat resistance, {company name}'s alumina fire bricks are also known for their durability. Unlike inferior materials, these bricks are designed to withstand the harsh conditions of industrial processes without succumbing to wear and tear. This means that businesses can count on these fire bricks to provide long-term performance and value, ultimately leading to cost savings and improved efficiency.Another important factor that sets {company name}'s alumina fire bricks apart is their commitment to quality and innovation. The company invests heavily in research and development to ensure that their products are always at the cutting edge of technology. This dedication to innovation has led to the development of advanced formulations and manufacturing techniques that further enhance the performance and durability of their fire bricks.As a result of their unwavering commitment to quality and innovation, {company name} has earned a reputation as a trusted supplier of high-quality alumina fire bricks. Their products are relied upon by a wide range of industries around the world, and their customer base continues to grow as more businesses recognize the superior performance and value that {company name} has to offer.In conclusion, high-quality alumina fire bricks are a crucial component in a wide range of industrial applications, and {company name} is a leading provider of these essential materials. With a strong focus on quality, durability, and innovation, {company name} has established itself as a trusted partner for businesses that rely on heat-resistant materials to keep their operations running smoothly. With their advanced formulations and cutting-edge manufacturing techniques, {company name} continues to set the standard for excellence in the field of refractory materials, providing the ultimate heat-resistant solution for industries around the world.
Demand for High-Quality Corundum Bricks Continues to Grow in Various Industries
Corundum Brick – The Ultimate Solution for High-Temperature ApplicationsCorundum brick is a type of refractory brick that is made from pure fused aluminum oxide. It is a high-quality refractory material that has excellent thermal shock resistance, high mechanical strength, and superior erosion resistance. This makes it an ideal solution for applications that involve high temperatures, such as in furnaces, kilns, and incinerators, among others.A leading manufacturer of corundum brick, has developed a unique process that involves sintering and high-pressure molding, which helps in producing high-density bricks with uniform strength and precise dimensions. These corundum bricks are designed to withstand extreme conditions, such as temperatures of up to 1800°C, making them perfect for use in industrial environments.The corundum brick is not only used for refractory linings in high-temperature applications but for other critical applications, as well. It also serves as a crucial component in the construction of other refractory products, like high-temperature furnace lining bricks, burners, and high-temperature insulating products.The manufacturing process of corundum brick involves a complex series of steps and requires specialized equipment and expertise. The raw materials are first mixed together with water to form a plastic mass, which is then molded into the desired shape using high-pressure equipment. The molded bricks are then fired at high temperatures in a high-temperature kiln. The final product is carefully inspected and undergoes quality checks to ensure that it meets the required specifications.Corundum brick is a cost-effective solution that offers many benefits to industries, including long-lasting durability, resistance to corrosion, high-temperature resistance, and excellent thermal stability. These characteristics make it an ideal material for use in the heavy industry, petrochemical, cement, steel, and other high-temperature applications.The corundum brick can withstand many hours of high-temperature exposure without losing its strength or structure, making it a reliable and durable choice for refractory linings. It requires less maintenance compared to other refractory materials and is easy to install.The corundum brick’s excellent thermal shock resistance enables it to withstand sudden changes in temperature. This characteristic makes it an ideal solution for environments where the temperature changes rapidly, causing other materials to expand, contract, or crack.The company, with years of experience in the production of corundum bricks, has gained a reputation as a reliable and trustworthy supplier. Their products are of the highest quality and meet industry standards. Moreover, the company offers customized solutions, tailoring their products to meet specific clients’ needs. They have a team of experienced technicians and engineers who provide prompt and reliable technical support to their clients.The corundum brick has revolutionized the high-temperature industry. The benefits it offers make it an ideal solution for refractory lining applications. It has significantly reduced the frequency of lining replacements. Additionally, the cost savings that come with using corundum brick has converted many industries into using it over other refractory materials.In conclusion, the corundum brick is an innovative solution that offers excellent thermal stability, high-temperature resistance, and superior performance. The manufacturing process that produces these bricks is complex and requires unique expertise. The bricks are highly durable, require less maintenance, and are easy to install. The corundum brick has set a new standard in the refractory industry, and the company's customized solutions and reliable technical support make it the preferred choice for industries that require exceptional quality materials. The corundum brick is a game-changer and will continue to set the benchmark for high-temperature applications.
High-Quality Magnesia Bricks for Sale - Durable & Heat-Resistant Options Available
China is the world's largest producer of magnesia, a mineral used in numerous industrial applications such as refractories, fertilizers, and construction materials. No wonder that Chinese companies hold a significant share in the global market for magnesia- based products. One such company, located in the Henan Province of China, serves as a prime example of the country's prowess when it comes to this crucial mineral.The company is a leading manufacturer of magnesia-based products, with a focus on refractory materials used in high-temperature environments. Refractory materials are critical for industries such as steel-making, cement production, and glass- making, where high temperatures and harsh conditions can put enormous stress on the equipment and structures used.The company specializes in producing magnesia bricks, which are an essential component in many furnaces and kilns. Magnesia bricks are made of high-purity magnesia, a refractory mineral that is highly resistant to heat, corrosion, and wear. They are used in industries such as steel, non-ferrous metals, cement, and glass, with applications ranging from lining of furnaces and kilns to the construction of chimneys and heat exchangers.To guarantee the quality of its magnesia bricks, the company sources the best raw materials from trusted suppliers and implements rigorous quality control systems from the production process to the delivery of finished products. This careful attention to quality has earned the company a reputation of excellence and trust among its customers, who rely on its products to keep their operations running smoothly.Now, the company's magnesia bricks are available for purchase worldwide, through its online platform, which ensures fast and reliable delivery of high-quality products to customers across the globe. The company's online store offers a variety of magnesia bricks for different temperatures and applications, with custom sizes and shapes available upon request. Furthermore, its website provides technical specifications, product data sheets, and safety information to help customers choose the right magnesia bricks for their specific needs.Customers can benefit from the company's expertise in refractory materials, as it also offers consultation and customization services to help them find the best solutions for their particular requirements. Whether it is for a small-scale project or a large industrial application, the company's team of experts can help customers design, implement, and maintain their refractory systems for optimal performance and longevity.The company's commitment to quality, innovation, and customer satisfaction has enabled it to become a trusted partner for many businesses worldwide, as it continues to expand its product lines and services to meet the evolving needs of its customers. Its mission to provide sustainable and cost-effective solutions for high-temperature applications has driven its growth and success, making it a leading player in the global market for refractory materials.In conclusion, the Chinese company's magnesia bricks offer a durable and heat-resistant solution for a wide range of industrial applications, with a reputation for excellence and reliability. Through its online platform and customer-oriented services, it has become an accessible and trustworthy partner for businesses seeking quality refractory materials. Its dedication to innovation and sustainability ensures that it remains at the forefront of the industry, as it continues to provide solutions that enhance the efficiency and productivity of its customers' operations.
Understanding the Importance of Arc Furnace Electrodes: A Comprehensive Guide
Title: Advancements in Arc Furnace Electrodes Facilitate Efficient Steel ProductionIntroduction:In the constantly evolving steel industry where efficiency and sustainability are key, companies are continuously seeking innovative solutions to optimize their production processes. One such groundbreaking advancement lies in the development of state-of-the-art arc furnace electrodes. These cutting-edge electrodes, produced by a renowned industry leader {}, are revolutionizing steelmaking and paving the way towards more efficient and eco-friendly practices.[Company Introduction - Approx. 200 words]Starting its journey in the early 1980s, {} has emerged as a global frontrunner in manufacturing arc furnace electrodes. Their unwavering commitment to excellence, extensive research and development, and supplier collaborations have propelled them to the forefront of the industry. With a reputation for consistently delivering quality products, they have earned the trust and loyalty of their customers worldwide.The company's modern facility, equipped with the latest manufacturing technologies and operated by highly skilled professionals, enables {} to produce high-performance arc furnace electrodes. These electrodes are essential components in the electric arc furnace (EAF) process, a widely adopted method for steel production due to its flexibility and cost-effectiveness.[Advancement 1 - Approx. 200 words]In a significant breakthrough, {} has successfully developed a next-generation arc furnace electrode that offers exceptional performance and durability. Through innovative design modifications and advancements in raw materials, these electrodes demonstrate improved electrical conductivity, thermal resistance, and resistance to oxidation. As a result, steelmakers can benefit from increased productivity, reduced energy consumption, and minimized downtime during the steelmaking process.The enhanced electrical conductivity of {}'s arc furnace electrodes allows for efficient transfer of electricity from the power source to the furnace, enabling faster melting rates and shorter cycle times. Consequently, steel manufacturers observe enhanced productivity and optimization of their manufacturing operations, leading to significant cost savings and increased profits.Additionally, the improved thermal resistance characteristic of these electrodes ensures stable and consistent heat transfer within the electric arc furnace, resulting in reduced melting time and increased overall energy efficiency. The reduction in energy consumption not only minimizes production costs but also aligns with the industry's focus on sustainability and environmental consciousness.[Advancement 2 - Approx. 200 words]Another breakthrough achieved by {} is the development of arc furnace electrodes with enhanced resistance to oxidation, thereby prolonging their lifespan. Through meticulous testing and optimization, the company has successfully formulated electrode compositions that exhibit superior resistance to oxidation even under extreme operating conditions. This advancement allows for longer electrode life, minimizing costly downtime associated with regular electrode replacements.The extended lifespan of {}'s arc furnace electrodes is particularly advantageous for steel manufacturers, as frequent electrode changes disrupt production flow and result in substantial economic losses. By offering electrodes with exceptional resistance to oxidation, the company enables seamless operations, providing steel producers with a competitive edge.Conclusion:With steel manufacturing being a vital industry worldwide, advancements in arc furnace electrodes play a pivotal role in optimizing steel production processes. Through their dedication to innovation and excellence, {} has emerged as a frontrunner in electrode manufacturing, introducing state-of-the-art products that enhance productivity, energy efficiency, and sustainability.The continuous evolution of arc furnace electrodes demonstrates the industry's commitment to pushing technological boundaries and meeting the ever-growing global demand for steel. As companies like {} continue to invest in research and development, the steel industry can look forward to more efficient, cost-effective, and eco-friendly steelmaking processes in the future.