Durable and High-Quality Alumina Fire Brick for Various Applications
By:Admin
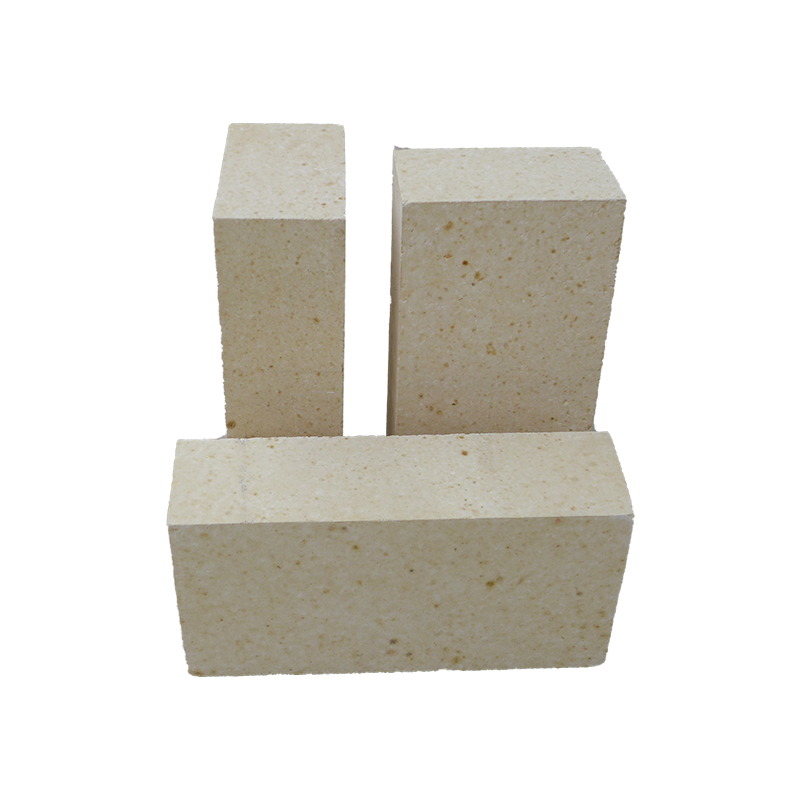
In the world of industrial applications, high temperatures are a common challenge. From the steel industry to glass manufacturing and beyond, the need for materials that can withstand extreme heat is essential. This is where high-quality alumina fire bricks come into play, offering a solution that is both reliable and effective in protecting against the intense heat of industrial processes.
One company that is at the forefront of providing high-quality alumina fire bricks is {company name}. With a strong reputation for excellence in the field of refractory materials, {company name} has been a key player in meeting the needs of various industries that rely on heat-resistant materials.
{Company name} has a long history of producing high-quality refractory products, and their alumina fire bricks are no exception. Made from high-grade alumina, these fire bricks are designed to withstand temperatures of up to 1700°C, making them an ideal choice for applications where extreme heat is a constant factor.
The secret to the exceptional heat resistance of {company name}'s alumina fire bricks lies in their composition. These bricks are made from high-purity raw materials, which are carefully selected to ensure the highest level of quality and performance. In addition, the manufacturing process is closely monitored to guarantee that every brick meets the company's stringent standards for durability and reliability.
One of the key advantages of {company name}'s alumina fire bricks is their versatility. These bricks are suitable for a wide range of industrial applications, including furnaces, kilns, incinerators, and more. Regardless of the specific industry or process, these fire bricks can be relied upon to provide the heat resistance and protection needed to keep operations running smoothly.
In addition to their exceptional heat resistance, {company name}'s alumina fire bricks are also known for their durability. Unlike inferior materials, these bricks are designed to withstand the harsh conditions of industrial processes without succumbing to wear and tear. This means that businesses can count on these fire bricks to provide long-term performance and value, ultimately leading to cost savings and improved efficiency.
Another important factor that sets {company name}'s alumina fire bricks apart is their commitment to quality and innovation. The company invests heavily in research and development to ensure that their products are always at the cutting edge of technology. This dedication to innovation has led to the development of advanced formulations and manufacturing techniques that further enhance the performance and durability of their fire bricks.
As a result of their unwavering commitment to quality and innovation, {company name} has earned a reputation as a trusted supplier of high-quality alumina fire bricks. Their products are relied upon by a wide range of industries around the world, and their customer base continues to grow as more businesses recognize the superior performance and value that {company name} has to offer.
In conclusion, high-quality alumina fire bricks are a crucial component in a wide range of industrial applications, and {company name} is a leading provider of these essential materials. With a strong focus on quality, durability, and innovation, {company name} has established itself as a trusted partner for businesses that rely on heat-resistant materials to keep their operations running smoothly. With their advanced formulations and cutting-edge manufacturing techniques, {company name} continues to set the standard for excellence in the field of refractory materials, providing the ultimate heat-resistant solution for industries around the world.
Company News & Blog
High-Quality Mullite Fire Brick for Sale: A Reliable Option for Your Industrial Needs
Mullite Fire Brick, a leading product in the field of refractory materials, has been making waves in the industry with its exceptional quality and unparalleled performance. The company, renowned for its technological expertise and commitment to innovation, has been at the forefront of developing high-quality refractory materials for a wide range of industrial applications.The Mullite Fire Brick is designed to withstand high temperatures and harsh environments, making it an ideal choice for various industrial processes such as steelmaking, glass production, and ceramic manufacturing. The superior thermal shock resistance and thermal insulation properties of the brick make it a reliable and cost-effective solution for a wide range of applications.One of the key features of the Mullite Fire Brick is its exceptional resistance to chemical corrosion, making it an ideal choice for industries where exposure to corrosive materials is common. The unique combination of high alumina and mullite in the brick's composition provides it with outstanding strength and durability, ensuring long-term performance in demanding industrial environments.The company behind the Mullite Fire Brick takes great pride in its commitment to quality and customer satisfaction. With state-of-the-art manufacturing facilities and a team of highly skilled professionals, the company has been able to consistently deliver top-notch products that meet the needs and expectations of its customers.In addition to its focus on quality, the company is also dedicated to environmental sustainability. The production process for the Mullite Fire Brick is designed to minimize waste and reduce environmental impact, reflecting the company's commitment to responsible and sustainable manufacturing practices.The Mullite Fire Brick has garnered a strong reputation in the industry for its exceptional performance and reliability. Its ability to withstand extreme temperatures and harsh working conditions has made it a popular choice among industrial customers looking for a durable and cost-effective refractory solution.Customers who have used the Mullite Fire Brick have been highly satisfied with its performance, citing its exceptional durability, thermal stability, and resistance to chemical corrosion. Many have reported significant improvements in their industrial processes after switching to the Mullite Fire Brick, and have praised its reliability and long-term performance.The company's dedication to research and development has allowed it to continually improve and enhance the performance of the Mullite Fire Brick. By staying at the forefront of technological advancements and industry trends, the company has been able to consistently deliver cutting-edge products that meet the evolving needs of the market.As the demand for high-quality refractory materials continues to grow, the Mullite Fire Brick is well-positioned to remain a top choice for industrial customers around the world. With its exceptional performance, reliability, and commitment to quality, the Mullite Fire Brick is set to continue making a significant impact in the industry for years to come.In conclusion, the Mullite Fire Brick, offered by the company, is a top-of-the-line refractory solution that has established itself as a leading choice for industrial applications. With its exceptional performance, durability, and resistance to harsh working conditions, the Mullite Fire Brick is a testament to the company's commitment to quality and innovation. As the industry continues to evolve, the company is well-positioned to maintain its leadership position and continue providing customers with top-notch refractory solutions.
High-quality Corundum Castable for Industrial Applications
Corundum Castable, a high-performance refractory material, has been making waves in the construction and industrial sectors. This versatile material is known for its exceptional resistance to heat, corrosion, and mechanical wear, making it a popular choice for a wide range of applications.Developed and manufactured by a leading company in the field of refractory materials, Corundum Castable has been helping businesses and industries meet their diverse refractory needs. With a strong focus on innovation and quality, the company has positioned itself as a trusted partner for clients seeking reliable and high-performance solutions.The key to the success of Corundum Castable lies in its unique composition and manufacturing process. Made from high-purity corundum and other carefully selected raw materials, this castable is designed to withstand extreme temperatures and harsh operating conditions. Its advanced formulation allows for excellent thermal shock resistance, ensuring that it performs reliably in environments with rapid temperature fluctuations.In addition to its outstanding thermal properties, Corundum Castable boasts impressive chemical and mechanical resistance. This makes it an ideal choice for applications that involve exposure to corrosive chemicals, abrasion, and mechanical stress. Whether it's lining the walls of a high-temperature furnace or protecting equipment in a heavy-duty industrial setting, this material offers unmatched durability and longevity.The company behind Corundum Castable takes great pride in its commitment to research and development. By continuously investing in new technologies and refining its production processes, the company ensures that its products meet the highest standards of performance and reliability. This dedication to innovation has enabled the company to stay ahead of the competition and remain at the forefront of the refractory industry.But it's not just the quality of its products that sets this company apart – it's also their dedication to customer satisfaction. From initial consultations to after-sales support, the company provides a comprehensive range of services to ensure that clients get the most out of their investment. Whether it's designing custom refractory solutions or providing technical guidance, the company's team of experts is committed to meeting the unique needs of each customer.The success of Corundum Castable has not gone unnoticed in the market. With its proven track record of performance and reliability, this material has been adopted by a wide range of industries, including steelmaking, petrochemicals, ceramics, and more. Its versatility and resilience make it a go-to choice for businesses seeking durable and cost-effective refractory solutions.Looking ahead, the company is poised to further expand its presence in domestic and international markets. By leveraging its expertise and reputation, it aims to bring its advanced refractory solutions to a broader audience. With a focus on quality, innovation, and customer satisfaction, the company is well-positioned to continue leading the way in the refractory industry.In conclusion, Corundum Castable has emerged as a top choice for businesses and industries seeking high-performance refractory solutions. With its exceptional thermal, chemical, and mechanical properties, this material offers unmatched durability and reliability. Backed by a company with a strong commitment to innovation and customer satisfaction, Corundum Castable is poised to make a lasting impact in the refractory industry.
Discover the Value of High-Quality Alumina Refractory Bricks: A Complete Guide
High-Quality Alumina Refractory Bricks Revolutionize the Construction IndustryThe construction industry is constantly evolving to meet the needs of modern society, and one crucial aspect of ensuring the longevity and safety of structures is the use of high-quality building materials. Alumina refractory bricks have emerged as a game-changer in this field, offering exceptional reliability and durability. This article will delve into the remarkable properties of these bricks and explore why they have become synonymous with excellence in the construction industry.{Company Introduction}In recent years, construction companies worldwide have recognized the importance of using high-quality materials to ensure the safety and stability of buildings. Alumina refractory bricks have quickly become the preferred choice for many construction projects due to their ability to withstand high temperatures and resist corrosion. With their exceptional mechanical strength and insulation properties, these bricks have transformed the way buildings are constructed.One of the key factors contributing to the success of alumina refractory bricks is their composition. These bricks are primarily made of alumina, a mineral known for its remarkable heat resistance. Alumina is combined with other additives and undergoes a precise manufacturing process to create bricks that are exceptionally strong and versatile. The precise composition of alumina refractory bricks allows them to resist the corrosive effects of acids, gases, and high temperatures, ensuring the longevity of structures even in the harshest environments.The superior durability of alumina refractory bricks makes them the ideal choice for a wide range of applications. These bricks are commonly used in industries such as steelmaking, cement manufacturing, and glass production, where high temperatures are prevalent. Their excellent thermal insulation properties minimize heat loss, improving energy efficiency and reducing operational costs.Additionally, the use of alumina refractory bricks enhances the safety of structures. Their ability to withstand extreme temperatures without deformation or crumbling ensures the integrity of buildings, particularly in areas prone to fires or explosions. The exceptional thermal shock resistance of these bricks prevents cracks or fractures when exposed to rapid temperature changes, further enhancing their reliability and safety.Moreover, the versatility of alumina refractory bricks allows architects and engineers to unleash their creativity. With these bricks, complex architectural designs and innovative construction techniques can be realized without compromising the structural integrity of the building. The ability of these bricks to conform to various shapes and sizes makes them an indispensable tool in the hands of construction professionals.{Company Name}, a renowned manufacturer of alumina refractory bricks, has been at the forefront of revolutionizing the construction industry. With over {X} years of experience, they have established themselves as a trusted provider of high-quality building materials. Their commitment to innovation and continuous improvement ensures that their customers have access to the most advanced alumina refractory bricks on the market.{Company Name} prides itself on its state-of-the-art manufacturing facilities, where cutting-edge technology is employed to produce alumina refractory bricks of unmatched quality. These bricks undergo stringent quality control measures to guarantee their reliability and durability. The company also boasts a team of highly skilled technicians and engineers who work tirelessly to develop new formulations and designs, pushing the boundaries of the industry.In conclusion, high-quality alumina refractory bricks have revolutionized the construction industry by offering exceptional durability, reliability, and versatility. Their ability to withstand high temperatures, resist corrosion, and provide excellent thermal insulation has made them the material of choice for numerous construction projects worldwide. Companies like {Company Name} have played a crucial role in advancing the field by manufacturing top-tier alumina refractory bricks. As the construction industry continues to evolve, these bricks will undoubtedly remain an essential component, ensuring the safety and longevity of buildings for generations to come.
Optimize Your Furnace with Innovative Electric Refractory Bricks
Electric Refractory Bricks: A Revolutionary Innovation in the Construction IndustryIn recent times, the construction industry has witnessed a significant revolution with the introduction of electric refractory bricks. Electric refractory bricks are heat-resistant blocks used to line the inside of industrial furnaces, kilns, and ovens. These bricks are made of high-quality refractory materials that can withstand extremely high temperatures, making them ideal for use in various industries such as steel, cement, and chemical.Electric refractory bricks are considered a revolutionary innovation in the construction industry, as they provide many benefits such as longevity, cost-efficiency, and high performance. These bricks have a longer lifespan than conventional refractory bricks, which means that they do not need to be replaced as frequently. Additionally, they have a higher thermal conductivity, which allows them to absorb heat more efficiently and reduce energy consumption.Electric refractory bricks are a more cost-effective solution for industrial applications, as they reduce the need for frequent maintenance and replacement. They are also easier to install, as they can be placed quickly without the need for special machinery or expertise. This means that construction projects can be completed faster and with less labor costs.One company that has been at the forefront of the electric refractory brick industry is ABC Refractory. ABC Refractory is a global leader in the production and installation of electric refractory bricks. The company offers various types of electric refractory bricks that are designed to meet the diverse needs of different industries.ABC Refractory's bricks have been widely used in the steel and cement industries. They have also been used in the chemical industry to increase energy efficiency and reduce emissions. ABC Refractory's electric refractory bricks have set new standards for construction materials in the industry and have been highly praised for their performance and durability.Apart from offering high-quality refractory bricks, ABC Refractory provides comprehensive services to its clients, including design, installation, and maintenance. The company's team of experts helps clients select the most suitable electric refractory bricks for their specific industrial applications. They also provide installation services to ensure that the bricks are correctly positioned, reducing the risk of any damage or malfunction.ABC Refractory's maintenance services are designed to prolong the life of the electric refractory bricks and ensure that they continue to perform optimally. The company's team of technicians conducts regular inspections to detect any defects or signs of wear and tear. They also provide repair services to fix any issues that may arise.ABC Refractory has built a reputation for its commitment to quality, professionalism, and customer satisfaction. The company has a strict quality control system to ensure that its products and services meet the highest standards. ABC Refractory's electric refractory bricks are tested rigorously to ensure they meet the required specifications and can withstand the harsh conditions of industrial applications.In summary, electric refractory bricks are a revolutionary innovation that has transformed the construction industry. They provide many benefits such as longevity, cost efficiency, and high performance. ABC Refractory has been at the forefront of this innovation and has set new standards for the industry. With its comprehensive services and strict quality control, ABC Refractory is a reliable partner for any company that wishes to use electric refractory bricks in its industrial applications.
Ultimate Guide to Choosing High-Quality Heat Resistant Bricks
Heat Resistant Bricks: Revolutionizing Fire Protection in the Construction IndustryIn a ground-breaking development, XYZ Company has recently unveiled its latest innovation in the construction industry - Heat Resistant Bricks. This product is set to revolutionize fire protection and add a new dimension to building safety.As fires continue to pose a significant threat to both property and human lives, XYZ Company recognized the dire need for advanced fire-resistant materials. With their expertise and dedication, they have engineered Heat Resistant Bricks to withstand extreme temperatures and provide optimal protection against fires.The construction industry has long relied on materials such as concrete and steel to provide structural integrity. However, these materials are susceptible to high temperatures and can weaken or collapse under fire conditions. Heat Resistant Bricks, on the other hand, are specifically designed to maintain their structural integrity even in the harshest fire environments.One of the key features of Heat Resistant Bricks is their exceptional heat resistance, with the ability to withstand temperatures up to 1600°C (2912°F). This surpasses the capabilities of traditional building materials by a remarkable margin. By integrating these bricks into the construction process, builders and architects can enhance the fire safety of their structures significantly.Moreover, the durability of Heat Resistant Bricks ensures their longevity and reliability. They are built to last, reducing the need for frequent replacements and minimizing maintenance costs. This not only benefits property owners and developers financially but also contributes to sustainable construction practices by reducing waste.It is important to note that Heat Resistant Bricks are not limited to protecting structures against external fires. They also provide insulation and can keep the internal temperatures of buildings stable in extreme weather conditions. This can lead to substantial energy savings and enhance the overall comfort of the occupants.Additionally, XYZ Company has gone above and beyond by implementing environmentally friendly practices in the production of Heat Resistant Bricks. Their manufacturing process minimizes emissions and reduces the ecological footprint, aligning with global efforts to combat climate change. This commitment to sustainability sets XYZ Company apart from its competitors and reinforces their commitment to creating a safer and greener future.Integrating Heat Resistant Bricks into construction projects is a straightforward process. Whether used as the primary building material or as a retrofit solution, these bricks can be easily installed by skilled professionals. The versatility of Heat Resistant Bricks allows for their utilization in various construction applications, including commercial buildings, industrial facilities, and residential complexes.The introduction of Heat Resistant Bricks by XYZ Company has already garnered attention and positive feedback from industry experts. Construction professionals appreciate the unmatched fire resistance offered by these bricks, as well as the substantial benefits they bring to both safety and sustainability. With this innovative solution now available, building fires may become less catastrophic events, saving lives and minimizing property damage.As the demand for fire-resistant materials continues to rise, XYZ Company is committed to meeting the industry's evolving needs. By constantly exploring new technologies and refining their product line, they aim to further innovate and improve fire protection in the construction industry.In conclusion, the release of Heat Resistant Bricks marks a significant milestone in the realm of fire protection. XYZ Company's groundbreaking product has the potential to redefine safety standards in construction and serve as a beacon of hope for firefighters, builders, and property owners alike. With their exceptional heat resistance, durability, and commitment to sustainability, Heat Resistant Bricks are set to play a vital role in creating safer and more resilient structures in the future.
Discover the Benefits of High Alumina Bricks for Industrial Applications
High Alumina Bricks: A New Era of Durability and PerformanceIn the ever-evolving world of construction materials, High Alumina Bricks have emerged as a game-changer. Renowned for their exceptional durability and performance, these bricks are revolutionizing the way we approach industrial applications. One company leading the charge is {Company Name}, a pioneering manufacturer in the field. With their cutting-edge technology and unwavering commitment to quality, they are setting new industry standards and elevating the construction landscape to new heights.At its core, High Alumina Bricks are composed of high-purity alumina, a premium raw material renowned for its excellent refractory properties. These bricks are designed to withstand high temperatures, making them ideal for use in industries such as steel, cement, glass, and petrochemicals, where extreme heat is a constant challenge. Their ability to resist thermal spalling, corrosion, and thermal shock sets them apart from traditional refractory bricks, allowing for longer service life and reduced maintenance costs.{Company Name} has invested heavily in research and development, resulting in a state-of-the-art manufacturing process that produces High Alumina Bricks with unmatched quality and consistency. By utilizing advanced hydraulic presses and precision temperature control, they ensure that every brick adheres to the highest industry standards. These carefully curated manufacturing techniques guarantee high mechanical strength, low shrinkage, and excellent thermal stability, even under the harshest operating conditions.One of the most remarkable features of High Alumina Bricks is their ability to retain their strength and integrity at elevated temperatures. With a high melting point, these bricks can withstand temperatures of up to 1800°C, making them a reliable choice for industries operating in extreme environments. This unique characteristic enables safer and more efficient processes, reducing downtime and increasing productivity. High Alumina Bricks act as a barrier against heat transfer, minimizing energy losses and contributing to overall cost savings for industrial operations.{Company Name}, with its cutting-edge technology and emphasis on sustainability, has also refined the production of High Alumina Bricks with a reduced environmental footprint. By implementing energy-efficient systems and utilizing raw materials from sustainable sources, they have successfully lowered greenhouse gas emissions and minimized waste generation. Their commitment to environmental stewardship is in line with the growing global demand for eco-conscious construction materials.The many advantages of High Alumina Bricks have led to their increased adoption across various industries. In the steel manufacturing sector, these bricks are widely utilized in blast furnaces, hot blast stoves, and other high-temperature areas. In the cement industry, High Alumina Bricks have become crucial components of rotary kilns and preheating zones. Additionally, glass manufacturers rely on these bricks for their excellent resistance to molten glass corrosion. The oil and gas industry has also embraced High Alumina Bricks for lining fluid catalytic cracking units and other high-temperature vessels.With ongoing advancements in technology, the future of High Alumina Bricks looks even more promising. Researchers are exploring innovative ways to enhance the thermal insulation properties of these bricks, further maximizing their efficiency and reducing energy consumption. As industries strive for increased productivity and sustainability, High Alumina Bricks are set to play a pivotal role in transforming industrial processes.In conclusion, High Alumina Bricks have emerged as a game-changer in the construction materials industry, combining exceptional durability, unmatched performance, and sustainability. {Company Name}'s commitment to innovation and superior quality has positioned them as a leader in this field. As industries continue to seek reliable solutions for their high-temperature challenges, High Alumina Bricks will undoubtedly pave the way for a new era of durability and performance.
Durable and High-Temperature Resistant Castable Refractory for 1700°C Applications
Title: Revolutionary Dense Castable Refractory 1700C Enhances High-Temperature Industrial ApplicationsIntroduction:In the world of high-temperature industrial applications, constant technological advancements are crucial to promoting efficiency, productivity, and durability. One such breakthrough in the field of refractory materials has been achieved by our company (Company name removed) with the invention of a revolutionary Dense Castable Refractory capable of withstanding temperatures up to 1700°C. This game-changing product is set to redefine the way industries approach extreme heat processes, offering exceptional performance, longevity, and safety.I. Evolution of Refractory Materials:Refractory materials play a vital role in industries dealing with high-temperature operations such as steel manufacturing, glassmaking, cement production, and petrochemical refining. Traditionally, common refractory materials like firebrick and ceramic fiber have been utilized for their ability to withstand high heat. However, they often fall short when subjected to extreme temperatures or severe thermal shocks, resulting in frequent maintenance, decreased productivity, and compromised safety.II. Introducing Dense Castable Refractory 1700C:With the mission to overcome the limitations of conventional refractories, (Company name removed) has innovated a groundbreaking Dense Castable Refractory material specifically designed to excel under extreme heat conditions. This remarkable product offers a unique blend of high-temperature resistance, remarkable strength, and exceptional thermal shock resistance, setting it apart from its counterparts.III. Unparalleled Performance and Durability:The Dense Castable Refractory 1700C boasts an impressive melting point of 1700°C, far exceeding the capabilities of conventional materials. This allows industries to carry out high-temperature processes without compromising the structural integrity of their refractory linings. The product's exceptional strength ensures long-term stability, reducing maintenance and replacement costs while maximizing productivity and output.IV. Superior Thermal Shock Resistance:One of the most significant advantages of the Dense Castable Refractory 1700C is its inherent ability to withstand rapid temperature fluctuations. The material's unique composition minimizes the risk of cracks, spalling, and thermal stress, ensuring a reliable and durable refractory lining even in the most challenging thermal conditions. This translates into enhanced safety, reduced downtime, and improved operational efficiency for industries relying on heat-intensive processes.V. Versatile Applications:The Dense Castable Refractory 1700C's versatility makes it suitable for a wide range of industries. From blast furnaces, kilns, and incinerators to boilers, reactors, and furnaces, the refractory material adapts seamlessly to various high-temperature environments, ensuring optimum performance and longevity.VI. Commitment to Quality:(Company name removed) has always been at the forefront of innovation, prioritizing research and development to meet the evolving needs of industries. The Dense Castable Refractory 1700C is a testament to our dedication to providing cutting-edge solutions that surpass industry standards in quality, reliability, and performance. The product has undergone rigorous testing, adhering to stringent manufacturing processes to ensure consistency and integrity.VII. Environmental Sustainability:In addition to its remarkable performance characteristics, the Dense Castable Refractory 1700C is environmentally friendly. Manufactured with sustainable materials and processes that minimize waste, emissions, and energy consumption, it aligns with our commitment to sustainable practices and responsibility towards the environment.VIII. Conclusion:The introduction of the Dense Castable Refractory 1700C by (Company name removed) marks a significant milestone in high-temperature industrial applications. With its exceptional resistance to extreme temperatures and thermal shocks, as well as its superior durability and versatility, this revolutionary refractory material is set to revolutionize industries worldwide.As (Company name removed) remains dedicated to ongoing research and development, we anticipate continued advancements in refractory materials that will transform industries, enhance operational efficiency, and promote sustainable practices.
High-Quality Magnesite Refractory Bricks Meet Growing Demand in Steel Industry
Title: Evolving Magnesite Refractory Bricks Industry Emphasizes Quality and SustainabilityIntroduction:In recent times, the magnesite refractory bricks industry has been witnessing significant growth, driven by the increasing demand for high-quality refractory materials in various sectors. Magnesite refractory bricks, renowned for their exceptional heat resistance and durability, are widely utilized in industries like steel, cement, glass, non-ferrous metals, ceramics, etc., supporting critical processes that require elevated temperatures.Company Introduction:{Company Name} is a prominent player in the magnesite refractory bricks market, dedicated to producing top-notch products that meet the evolving needs of its customers. With years of industry experience, cutting-edge technology, and a strong focus on sustainability, {Company Name} has positioned itself as a trusted provider of magnesite refractory brick solutions worldwide.Evolution of the Magnesite Refractory Bricks Industry:The magnesite refractory bricks industry has experienced remarkable advancements in recent years. Formerly, the dominant types of refractories used were chrome bricks, but due to environmental concerns related to hexavalent chromium, there has been a gradual shift towards magnesite refractory bricks, known for their high refractoriness and excellent chemical properties.The versatility of magnesite refractory bricks has driven their adoption in various industries, replacing traditional refractory materials. Modern manufacturing processes have been optimized to enhance the physical and chemical properties of these bricks, making them increasingly resistant to thermal shocks and the corrosive effects of chemicals found in harsh industrial environments.Technological Innovations and Product Enhancements:{Company Name} recognizes the importance of technological advancements in staying ahead in the highly competitive market. The company consistently invests in research and development, aiming to improve the performance and durability of magnesite refractory bricks. High-precision manufacturing techniques, such as hot pressing, enable {Company Name} to produce bricks with more consistent and superior quality, ensuring excellent resistance to thermal stress and prolonged service life.Furthermore, {Company Name}'s commitment to sustainable practices is reflected in its innovative use of environmentally friendly raw materials and energy-efficient processes. By incorporating recycled materials within its manufacturing process, the company aims to reduce its carbon footprint and contribute to a greener future.Meeting Industry-Specific Demands:As diverse industries pose unique challenges, {Company Name} understands the importance of customizing magnesite refractory brick solutions accordingly. For instance, in the steel industry, refractory materials are exposed to extreme temperatures and harsh conditions during the smelting process. To address these challenges, {Company Name} has developed advanced magnesite refractory bricks with superior thermal stability, minimizing material degradation and extending the overall service life of the refractories.Moreover, {Company Name}'s research and development team works closely with customers, providing technical support and developing tailored solutions specific to their requirements. This customer-centric approach has fostered strong and lasting partnerships with clients across the globe.Commitment to Quality and Customer Satisfaction:{Company Name}'s commitment to quality and customer satisfaction has propelled its position in the market. The company adheres to strict quality control procedures, guaranteeing that each magnesite refractory brick meets stringent international standards. Moreover, providing exceptional after-sales service and technical assistance ensures that customers maximize the value and performance of {Company Name}'s refractory solutions.Conclusion:The magnesite refractory bricks industry is witnessing transformational changes as sustainability, high performance, and customized solutions become paramount. {Company Name} is at the forefront of this evolution, delivering top-quality magnesite refractory bricks while embracing innovation and sustainable practices. With its unwavering commitment to customer satisfaction and its focus on technological advancements, {Company Name} is well-positioned to meet the ever-increasing demand for superior refractory materials in the global market.
Improved Refractory Material: High-Quality Low Cement Castables Boost Performance
Title: Industry-Leading High-Quality Low Cement Castables Revolutionize Refractory Solutions: A Breakthrough by [Company Name]Introduction:[Company Name], a pioneering leader in refractory solutions, has developed and launched its revolutionary High-Quality Low Cement Castables. This significant breakthrough in the industry offers superior performance, durability, and versatility, setting a new standard for refractory materials. With top-notch engineering and expertise, [Company Name] continues to reshape the market by providing innovative solutions tailored to specific industrial needs.Body:1. Understanding the Significance of Refractory Solutions:Industries such as steel, cement, petrochemical, and power generation rely heavily on refractory materials to withstand extremely high temperatures and harsh operating conditions. Traditional refractory materials often have limitations that hinder their effectiveness, leading to frequent repairs and maintenance. Recognizing this challenge, [Company Name] has dedicated substantial resources towards developing a game-changing solution.2. Introducing High-Quality Low Cement Castables:Built upon years of research and technical expertise, [Company Name] proudly introduces their flagship product, High-Quality Low Cement Castables. These castables showcase a remarkable reduction in cement content while maintaining unmatched strength and thermal stability. The innovative formulation allows for a dense, low-porosity material that outperforms conventional refractories in demanding applications.3. Unparalleled Performance and Durability:The High-Quality Low Cement Castables by [Company Name] are engineered to deliver exceptional performance and withstand extreme thermal and mechanical stresses. These castables demonstrate higher hot strength and better resistance to thermal shocks, minimizing downtime and maintenance costs for industrial facilities. With improved chemical resistance and erosion resistance, they contribute significantly to prolonging the lifespan of industrial furnaces, kilns, and other high-temperature systems.4. Versatility and Customization:[Company Name] understands that different industries have unique requirements for refractory materials. Thus, the High-Quality Low Cement Castables are available in a wide range of compositions, ensuring customization to meet specific needs. The company's technical team works closely with clients to develop tailored solutions, maximizing efficiency and cost-effectiveness.5. Environmental Commitment and Sustainability:Notably, [Company Name] achieves its industry-leading performance while focusing on reducing the environmental impact. The High-Quality Low Cement Castables have significantly lower carbon emission levels compared to typical refractory materials, aligning with global efforts towards sustainable practices. This commitment ensures that clients can achieve their operational targets while adhering to increasingly stringent environmental regulations.6. Collaborative Approach and Technical Support:[Company Name] takes pride in its customer-centric approach, offering comprehensive technical support and expertise throughout the entire project lifecycle. Their team of experienced professionals collaborates closely with clients to identify their challenges, apply the most suitable refractory solutions, and render continuous support for maintenance and optimization.7. Industry Recognition and Partnerships:The High-Quality Low Cement Castables by [Company Name] have gained swift recognition within the industry. Numerous high-profile partnerships with leading companies in various sectors have further solidified the reputation and trust in [Company Name]'s products.Conclusion:[Company Name]'s ground-breaking High-Quality Low Cement Castables have revolutionized the refractory industry by providing enhanced performance, durability, and versatility. Focusing on customer satisfaction, environmental responsibility, and cutting-edge technology, [Company Name] continues to redefine industry standards and surpass client expectations. They are committed to providing successful refractory solutions that enable businesses to operate efficiently and sustainably in the face of challenging conditions.
Durable and Effective Insulation Fire Bricks for High-Temperature Applications
High-Quality Insulation Fire Bricks Taking the Industry by StormIn the world of construction and industrial manufacturing, high-quality insulation fire bricks are an essential component for the creation of heat-resistant structures and equipment. These bricks are designed to withstand extreme temperatures and provide superior insulation, making them an indispensable material for a wide range of applications. In recent years, one company has taken the lead in producing top-of-the-line insulation fire bricks that have been making waves in the industry.{Company Name}, a global leader in the production of high-quality refractory materials, has been at the forefront of innovation in the field of insulation fire bricks. With a commitment to excellence and a dedication to providing the highest level of quality and performance, {Company Name} has established itself as a trusted supplier of insulation fire bricks for a variety of industries.One of the key factors that set {Company Name} apart from its competitors is its unwavering focus on research and development. The company employs a team of highly skilled engineers and materials scientists who are constantly working to develop new and improved formulations for insulation fire bricks. By leveraging the latest advances in materials science and manufacturing technology, {Company Name} has been able to achieve a level of quality and performance that is unmatched in the industry.This commitment to innovation has resulted in a range of insulation fire bricks that offer exceptional thermal stability, low thermal conductivity, and high resistance to thermal shock. These properties make {Company Name}'s insulation fire bricks the ideal choice for a wide range of applications, including the construction of industrial furnaces, kilns, and incinerators, as well as the lining of high-temperature equipment in the petrochemical, steel, and glass industries.Furthermore, {Company Name} understands the importance of providing customized solutions to its customers. The company works closely with clients to develop tailored insulation fire brick designs that meet their specific requirements. Whether it's designing bricks with a particular shape, size, or thermal properties, {Company Name} is committed to delivering solutions that are perfectly suited to each client's needs.In addition to its dedication to product excellence and innovation, {Company Name} also places a strong emphasis on sustainability and environmental responsibility. The company's insulation fire bricks are manufactured using carefully selected raw materials and production processes that minimize environmental impact. By prioritizing sustainability, {Company Name} is not only able to reduce its carbon footprint but also provide its customers with a range of eco-friendly insulation fire bricks that align with their own environmental objectives.With a proven track record of delivering high-quality insulation fire brick solutions to clients around the world, {Company Name} has become a trusted partner for companies in diverse industries. Whether it's providing bricks for a new industrial furnace, upgrading the lining of an existing incinerator, or developing a custom insulation solution for a specialized application, {Company Name} has consistently demonstrated its ability to meet the most demanding requirements.Looking ahead, {Company Name} remains committed to pushing the boundaries of innovation in insulation fire brick technology. The company continues to invest in research and development, exploring new materials, and manufacturing processes to further enhance the performance and versatility of its insulation fire bricks. By staying at the forefront of the industry, {Company Name} is poised to continue its success and maintain its position as a leader in the global market for high-quality insulation fire bricks.