- Home
- Blog
- Discover the Effective Solution of Corrosion Resistant Castables: A Breakthrough in the Construction Industry
Discover the Effective Solution of Corrosion Resistant Castables: A Breakthrough in the Construction Industry
By:Admin
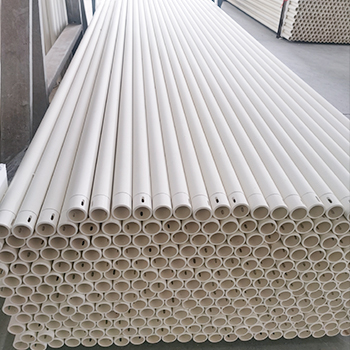
Introduction:
In an era where industrial durability and longevity are paramount, Company XYZ has emerged as a leading innovator in the production of exceptional corrosion resistant castable. Leveraging state-of-the-art technology and a commitment to groundbreaking research, Company XYZ has crafted a game-changing solution that effectively addresses the challenges posed by corrosive environments across various industries.
Paragraph 1: Overview of Corrosion Challenges
Corrosion poses a significant threat to the infrastructure and equipment across a wide range of industries, including oil and gas, petrochemicals, power generation, and metallurgy. The high costs associated with corrosion-related maintenance, replacement, and downtime have compelled companies to seek innovative solutions that extend the lifespan of their assets. Recognizing this pressing need, Company XYZ has developed an advanced corrosion resistant castable designed to overcome the harshest environmental conditions.
Paragraph 2: Unveiling the Revolutionary Corrosion Resistant Castable
Company XYZ's pioneering corrosion resistant castable is the result of years of dedicated research and development. Leveraging cutting-edge materials and manufacturing processes, this castable provides exceptional resistance against corrosion, erosion, and thermal shock. Its unique formula combines several key properties, including high temperature stability, chemical inertness, mechanical strength, and ultra-low porosity, making it an outstanding choice for a wide range of applications.
Paragraph 3: Versatile Applications across Industries
Company XYZ's corrosion resistant castable finds utility in various industries. In the oil and gas sector, it effectively safeguards offshore drilling equipment against the corrosive effects of saltwater, acidic gases, and abrasive particles. Petrochemical plants benefit from its application in critical components such as furnaces, reformers, and catalytic cracking units, increasing the service life of these assets. The power generation industry reaps advantages by using this castable for lining chimneys, boilers, and flue gas desulfurization systems, ensuring extended operational efficiency. Moreover, the metallurgical industry can protect its furnaces, converters, and ladles from corrosion and thermal shock, ultimately enhancing productivity.
Paragraph 4: Unmatched Advantages of Company XYZ's Castable Solution
Company XYZ's corrosion resistant castable offers distinct advantages that set it apart from conventional alternatives. Its superior chemical resistance enables prolonged resistance against a wide range of corrosive substances, including acids, alkalis, and solvents. The castable's exceptional thermal stability allows it to withstand extreme temperatures, reducing the risk of cracks and failures. Furthermore, its high mechanical strength guarantees excellent structural integrity, ensuring long-term durability. Importantly, the ultra-low porosity of the castable minimizes the ingression of corrosive agents, rendering it highly effective in harsh environments.
Paragraph 5: Commitment to Sustainability and Environmental Responsibility
Alongside its innovative corrosion resistant castable, Company XYZ remains steadfast in its commitment to environmental stewardship. The castable is formulated with environmentally friendly materials, minimizing the impact on both human health and the ecosystem. Additionally, the castable's extended service life reduces the need for frequent replacements, resulting in notable cost savings while also decreasing waste generation.
Conclusion:
Through its groundbreaking corrosion resistant castable, Company XYZ has redefined industrial durability and longevity, providing unparalleled protection against corrosive environments. The castable's multi-faceted benefits make it a preferred choice for a wide array of applications in diverse industries, contributing to increased efficiency, reduced maintenance costs, and sustainable practices. As Company XYZ continues to advance the field of corrosion-resistant solutions, it sets a new standard of excellence in the quest for robust and durable infrastructure across the globe.
Company News & Blog
Get High-Quality Corundum Bricks Online: Exploring Options for Premium Refractories
Title: Refractories Corundum Bricks: Revolutionizing High-Temperature ApplicationsIntroduction:When it comes to high-temperature applications in industries such as steel, cement, and glass, one key component that plays a crucial role in ensuring structural integrity and heat resistance is refractory materials. Among these materials, Corundum Bricks have emerged as a game-changer, providing exceptional durability and resistance to extreme temperatures. This article delves into the features and applications of these refractory bricks, showcasing their effectiveness in revolutionizing high-temperature industries.Section 1: Understanding Refractories Corundum BricksRefractories Corundum Bricks are advanced ceramic materials primarily made from fused alumina (Al2O3) or synthetic mullite. Their exceptional strength, chemical stability, and high-performance characteristics make them ideal for applications that involve harsh environments and extreme temperatures exceeding 1500°C. Being composed of around 90% or more alumina, Corundum Bricks possess excellent resistance to corrosion, wear, thermal shock, and creep.Section 2: Features of Corundum Bricksa) High-temperature resistance: Corundum Bricks exhibit remarkable stability even in extreme temperature conditions, ensuring integrity and longevity of structures.b) Chemical resistance: With their dense structure and low porosity, these bricks effectively resist the corrosive effects of various chemicals, alkaline substances, and slags.c) Low thermal conductivity: The low thermal conductivity of Corundum Bricks minimizes heat loss, creating an energy-efficient solution for furnace linings and other high-temperature applications.d) Superior mechanical strength: These bricks possess impressive mechanical strength, enabling them to withstand thermal stress and resulting in enhanced operational reliability.e) Good thermal shock resistance: The ability of Corundum Bricks to withstand rapid temperature fluctuations without cracking or spalling is pivotal in maintaining the integrity of furnace linings.Section 3: Applications of Corundum Bricksa) Steel industry: Corundum Bricks find extensive use in steelmaking processes, where they serve as linings in ladles, converters, blast furnaces, and other high-temperature equipment. Their exceptional resistance to molten metals and slag ensures durability in harsh steel manufacturing conditions.b) Cement industry: With the growing demand for cement, Corundum Bricks are employed in cement kilns and coolers due to their ability to withstand high temperatures, chemical erosion, and physical wear.c) Glass industry: Corundum Bricks are widely utilized in glass melting furnaces, helping to prevent glass corrosion and ensuring long service life.d) Petrochemical industry: These bricks are crucial for lining thermal cracking furnaces, reformer furnaces, and ethylene cracking furnaces, as they exhibit excellent chemical resistance to harsh petrochemical environments.e) Other applications: Corundum Bricks are also used in non-ferrous metal smelting, power plant boilers, waste incinerators, and other high-temperature processes.Section 4: The Company's ExpertiseThe company, as a leading manufacturer of Refractories Corundum Bricks, is dedicated to providing high-quality solutions to industries that rely on refractory materials. With state-of-the-art manufacturing facilities and a strong research and development team, the company ensures the production of premium Corundum Bricks that adhere to strict quality standards. By utilizing advanced technologies and thorough quality control measures, they have established themselves as a trusted supplier in the refractory industry.Conclusion:Refractories Corundum Bricks have revolutionized high-temperature applications in various industries by providing exceptional durability, resistance to extreme temperatures, and superior mechanical strength. As companies strive for increased productivity, efficiency, and longevity in their operations, the utilization of Corundum Bricks is becoming indispensable. With continuous advancements and a strong commitment to quality, these bricks are expected to shape the future of refractory materials, setting new standards for performance and reliability in high-temperature environments.
Dense Castable Refractory: Key Facts and Uses Revealed
Dense Castable Refractory: An Innovative Solution for Multiple IndustriesRefractory materials are used in high-temperature applications that require materials to withstand extreme heat, pressure, and corrosive chemicals. One of the most promising refractory materials on the market is the Dense Castable Refractory. This revolutionary product is designed to offer exceptional material properties suitable for a wide range of industries, including steel and iron, petrochemical, power generation, cement, and waste incineration.Dense Castable Refractory is a type of cement used to line furnaces, kilns, and other high-temperature process equipment. Unlike traditional refractory materials, Dense Castable Refractory is a self-setting cement that offers excellent performance properties such as high thermal shock resistance, low thermal conductivity, high refractoriness, and resistance to abrasion. These properties make Dense Castable Refractory a popular choice for harsh industrial environments that require materials with superior resistance to extreme temperature and thermal cycling.The product's versatility comes from its easy installation and customizable uses. Dense Castable Refractory can be poured or gunned into place, and once cured, the refractory turns into a durable monolithic unit that can withstand high temperatures for extended periods. The product can be installed in various options, including smooth or textured surfaces to fit different applications and concrete surfaces.Dense Castable Refractory is an ideal material for use in cement kilns since they are exposed to extreme heat and abrasion. The material is also an excellent choice for use in steel and iron industries where protective linings are necessary to preserve the equipment and enhance its durability. These industries benefit by having equipment that is resistant to thermal shock, meaning it withstands rapid temperature changes. It can also resist abrasion, reducing the likelihood of wear and tear, which reduces the potential for equipment damage and malfunctions.The petrochemical industry has not been left behind. Dense Castable Refractory has been deployed in some of the most stringent petrochemical applications, including reformers, crackers, and incinerators. Dense Castable Refractory's thermal shock resistance and low thermal conductivity make it suitable for use in the insulation of various units, including reformers, where it protects the equipment from high temperatures and allows for optimal transfer of heat.Dense Castable Refractory is also an excellent option in power generation where it contributes to efficient energy production by providing insulation and preventing heat loss in boilers, kilns, and thermal oxidizers. This insulation and heat retention typically cut energy costs and improves operational reliability.The cement industry has also realized the benefits of Dense Castable Refractory due to its excellent refractoriness. The refractory bonds to the existing structure, enhancing resistance at high temperatures and preserving the integrity of the equipment.Furthermore, Dense Castable Refractory is ideal for incineration systems. The material's ability to withstand excessive thermal shock and its excellent insulating properties offer superior performance when protecting furnaces that generate high heat during the waste incineration process.The company, a leader in the manufacturing and distribution of Dense Castable Refractory, has developed several innovative formulations that address various industrial environments' specific needs. The company offers customized formulations such as high-strength, low-cement, and ultra-low cement for demanding applications where traditional cement is not sufficient.The manufacturing of Dense Castable Refractory depends on several critical factors. The company has invested in a state-of-the-art production facility with advanced quality assurance tools and equipment. Their experienced personnel, together with the company's innovative formulations, ensure that their Dense Castable Refractory meets global standards. All their products come with consistent and reliable quality, making them the perfect choice for any industrial application.In conclusion, the Dense Castable Refractory is an innovative material that is set to become an industry standard in high-temperature applications. Thanks to its ability to provide superior resistance to heat, thermal shock, abrasion, and chemicals at high temperatures, the material will revolutionize how various industries envisions manufacturing and maintenance of furnace and general process equipment. The company's formulations offer customized solutions in various industrial applications, making it the go-to solution for end-users looking for durable, reliable, and cost-effective refractory products.
Demand for High-Quality Carbon Bricks Surges Amidst Growing Industrial Needs
Magnesia Carbon Brick Boosting Production Efficiency for Steel ManufacturingSteel manufacturing has been at the forefront of technological advances and innovation. Manufacturers are always looking for new ways to improve production efficiency, increase product quality, and reduce operating costs. A vital component of the steel manufacturing process is the refractory materials used in the construction of blast furnaces, ladles, and other high-temperature equipment. The quality and durability of these materials are essential for ensuring long-lasting and efficient operation.One of the most popular refractory materials used in the steel industry is Magnesia Carbon Brick. This material is a combination of high purity magnesia and high-quality graphite, allowing for superior thermal shock resistance and corrosion resistance compared to other refractory materials. Magnesia Carbon Brick has been widely applied in the casthouse areas such as the slag line, hot metal transportation chute, and taphole and ladle applications.As the leading refractory manufacturer in China, the {} company has been committed to providing high-quality and reliable refractory solutions to the steel industry for more than 20 years. They have recently launched a new production line for Magnesia Carbon Brick, significantly increasing their production capacity for this highly sought-after product.Magnesia Carbon Brick is preferred by the steel industry for several reasons. Firstly, it is a cost-effective material, with a competitive price when compared to other types of refractories. Secondly, it has a longer lifespan compared to other refractory materials, resulting in lower maintenance costs and a reduction in the frequency of equipment replacement.Thirdly, Magnesia Carbon Brick offers superior thermal shock resistance, which means it can withstand rapid temperature changes without cracking or breaking, prolonging the life of the refractory lining. Finally, Magnesia Carbon Brick has a high resistance to alkaline slag and can resist the erosion caused by molten iron and steel, which is critical to the long-term performance of the refractory lining.These features of Magnesia Carbon Brick are particularly important in the steelmaking process. High-quality refractory materials are necessary to withstand the extreme temperatures and harsh conditions of the blast furnace and other key components of the steelmaking process. Magnesia Carbon Brick can provide the reliability and durability required to operate these critical parts efficiently and cost-effectively.The new Magnesia Carbon Brick production line from {} company is an important development for the steel industry. It provides an opportunity for steel manufacturers to access high-quality refractory materials at competitive prices, helping them to improve production efficiency and reduce operating costs. Additionally, the increased production capacity of {} company means that customers can have a more stable and reliable supply of Magnesia Carbon Brick, ensuring that their operations will not be disrupted by shortages or delays in delivery.The production process of the Magnesia Carbon Brick at {} company is strictly controlled to ensure that the final product is of the highest quality and meets the specific requirements of each individual customer. They use high-purity magnesia and high-quality graphite as raw materials and apply advanced manufacturing techniques, such as mixing, molding, and baking. Additionally, the finished products undergo rigorous testing to ensure that they meet the necessary standards for use in the steel industry.{} company has established a reputation for producing high-quality refractory products and providing excellent customer service. They have a team of experienced engineers and technicians who work closely with customers to provide customized refractory solutions tailored to meet their individual needs. Whether it's choosing the right materials or providing on-site technical support, {} company is committed to ensuring their customers' success.In conclusion, the steel industry is highly competitive, and manufacturers are always searching for ways to improve their production efficiency and reduce operating costs. The Magnesia Carbon Brick produced by {} company is a cost-effective, durable, and reliable refractory material that can help steel manufacturers achieve these goals. With their new and expanded production facilities, {} company is poised to become a leading supplier of Magnesia Carbon Brick to the steel industry.
Exceptional Quality Magnesia Carbon Brick for a Better Ladle Performance
Magnesia Carbon Brick for Ladle: A Revolutionary Solution for High-Temperature ApplicationsIn the ever-evolving field of refractories, a remarkable development has taken place with the introduction of Magnesia Carbon Brick for Ladle. This groundbreaking product has emerged as a game-changer in high-temperature applications, offering unparalleled performance and durability. With its unique composition and superior properties, this advanced refractory material ensures optimal performance in various industrial processes.Before delving into the specifics of this groundbreaking innovation, let us acquaint ourselves with the company behind this remarkable product. Founded several decades ago, this refractory manufacturer has been at the forefront of delivering cutting-edge solutions to industries worldwide. Known for their commitment to research and development, the company has garnered a reputation for producing best-in-class materials that cater to the most demanding customer requirements.Magnesia Carbon Brick for Ladle, the latest addition to their extensive product portfolio, is engineered to withstand extreme conditions encountered in ladle applications. Ladles are indispensable tools in the steel and metallurgy industries, used for transporting and pouring molten metal. Given the harsh and corrosive nature of these processes, the linings of ladles are subjected to extreme temperatures, chemical reactions, and mechanical stress.Traditionally, bricks made of magnesia and carbon have been used in ladle linings due to their excellent resistance to high temperatures. However, these conventional bricks have limitations such as high oxidation rates, poor thermal shock resistance, and susceptibility to carbon pickup. Recognizing the need for a more robust and reliable solution, our innovators have developed the Magnesia Carbon Brick for Ladle.This advanced refractory material features a unique combination of magnesia, graphite, and various additives, resulting in a high-performance composite with exceptional properties. The addition of graphite enhances the material's thermal shock resistance and provides increased resistance to slag penetration, while the carefully selected additives improve the overall mechanical strength and oxidation resistance.The Magnesia Carbon Brick for Ladle offers several notable advantages over its predecessors. The improved oxidation resistance significantly extends the service life of the lining, reducing downtime and maintenance costs. Moreover, the enhanced thermal shock resistance ensures reliable performance even in rapid temperature fluctuations, minimizing the risk of premature failure.Another key aspect of this revolutionary product is its excellent resistance to carbon pickup. Carbon pickup refers to the absorption of carbon by molten metal, resulting in the formation of carbides and compromising the quality of the final product. By mitigating this issue, the Magnesia Carbon Brick for Ladle ensures the production of high-quality steel with consistent properties.Furthermore, this magnesia carbon brick offers superior corrosion resistance to chemical attacks from molten metals and slags. This resistance is crucial for maintaining the integrity of the ladle lining, preventing leaks or contamination that could impact the overall process efficiency and product quality.Considering the widespread applications of ladles in the steel and metallurgy industries, the adoption of Magnesia Carbon Brick for Ladle is expected to have a significant impact. The extended service life and enhanced performance of this refractory material will help manufacturers optimize their processes, reduce production costs, and improve overall productivity.In conclusion, the introduction of Magnesia Carbon Brick for Ladle marks a significant advancement in the field of refractories. With its remarkable properties and exceptional performance, this innovative product ensures optimal performance in high-temperature applications, such as ladle linings. Developed by a renowned refractory manufacturer, this advanced material underscores their commitment to delivering cutting-edge solutions that meet the evolving needs of industries worldwide. As its adoption grows, this revolutionary brick holds the promise of revolutionizing ladle applications and contributing to the growth and efficiency of various industrial processes.
High-Quality Refractory Cement for Castable Applications
Title: Innovation in Refractory Technology: High-Quality Castable Refractory Cement Revolutionizes Industrial ApplicationsIntroduction:In the ever-evolving landscape of industrial materials, technological advancements play a crucial role in shaping the efficiency and effectiveness of various processes. One such breakthrough in the field of refractory materials is the advent of high-quality castable refractory cement, which has revolutionized the way industries approach their thermal management needs. In this article, we delve into the innovative properties and applications of this remarkable product, while also taking a closer look at the company behind its development and production.Company Introduction:{Company's Name}, a leader in refractory solutions, has been at the forefront of developing advanced materials to meet the evolving demands of various industries. With a steadfast commitment to research and development, {Company's Name} has consistently introduced cutting-edge products that enhance the performance, durability, and sustainability of industrial processes. The company's expert team of scientists, engineers, and technicians work tirelessly to develop and perfect innovative refractory materials, placing {Company's Name} in a favorable position in the market.High-Quality Castable Refractory Cement: Unveiling Unmatched Performance{Company's Name} has recently introduced its highly anticipated High-Quality Castable Refractory Cement, a game-changer in the realm of thermal management solutions. This remarkable product has been engineered to withstand extreme temperatures while maintaining exceptional strength and durability. With a unique combination of raw materials and a meticulous manufacturing process, this advanced refractory cement has proved its mettle across various industries, demonstrating its versatility and reliability.Properties and Advantages:1. Exceptional Thermal Insulation: High-Quality Castable Refractory Cement exhibits excellent thermal insulation properties, effectively preventing heat loss from industrial furnaces, kilns, and other heated applications. Its low thermal conductivity ensures optimal energy conservation, leading to reduced fuel consumption and lower operational costs.2. Superior Strength and Abrasion Resistance: The cement's exceptional strength and resistance to abrasion make it ideal for withstanding the rigors of high-temperature environments. Its robust nature ensures prolonged service life and minimal maintenance disruptions, resulting in enhanced productivity and cost-effectiveness.3. Chemical and Corrosion Resistance: The castable refractory cement is highly resistant to various chemicals, acids, and corrosive elements, making it suitable for applications in industries such as steel, petrochemicals, and ceramics. This resistance safeguards against premature material degradation, ensuring reliable and long-lasting performance.4. Ease of Installation and Adaptability: High-Quality Castable Refractory Cement can be easily provided in various shapes and sizes, facilitating its installation and adaptation to specific industrial requirements. Its ability to conform to complex geometries enhances the efficiency of heat transfer processes, effectively optimizing system performance.Applications across Industries:1. Steel Industry: The cement finds extensive utility in steelmaking, providing strong linings for furnaces, ladles, and tundishes, improving thermal efficiency and maximizing production output.2. Petrochemical Industry: High-Quality Castable Refractory Cement proves invaluable in petrochemical applications, where it is used to line reactors, furnaces, and cyclones, providing reliable insulation and protection against corrosive substances.3. Ceramic and Glass Industry: With its excellent thermal insulation and resistance to molten materials, the cement effectively lines kilns, melting pots, and glass tanks, ensuring uniform heating and controlled cooling for optimized production processes.4. Power Generation: In power plants, this innovative refractory cement is used to line boilers and chimney stacks, withstanding high temperatures and reducing heat losses, thereby increasing the overall system efficiency.Conclusion:High-Quality Castable Refractory Cement, developed and produced by {Company's Name}, has paved the way for a new era of thermal management solutions. The exceptional properties and advantages of this advanced product have proven to be invaluable to various industries, enhancing productivity, cost-effectiveness, and environmental sustainability. As {Company's Name} continues to innovate and push the boundaries of refractory technology, they cement their position as a leading provider of cutting-edge materials, driving industrial progress towards a more efficient and sustainable future.
Discover the Latest Advancements in Fire Kiln Refractory Bricks
Fire Kiln Refractory Bricks Continue to Revolutionize the Construction IndustryFire Kiln Refractory Bricks (name removed), a leading manufacturer and supplier of high-quality refractory bricks, has been making waves in the construction industry with its innovative and durable products. These refractory bricks have proven to be a game-changer, offering unparalleled strength and longevity for various applications, including kilns, furnaces, and fireplaces. With a strong commitment to research and development, (name removed) has been able to continuously introduce cutting-edge products, contributing to the growth and advancement of the industry.Refractory bricks are specially designed to withstand high temperatures and harsh conditions, making them essential components in industries that involve extreme heat. Traditional bricks are not suitable for these environments, as they tend to crack, warp, or break under intense heat. In contrast, (name removed)'s fire kiln refractory bricks are manufactured using the highest quality raw materials and advanced techniques, resulting in an incredibly durable product that can withstand temperatures of up to 1800 degrees Celsius.One of the key factors that sets (name removed) apart from its competitors is its commitment to continuous improvement through research and development. The company invests heavily in technology and innovation, ensuring that its products are always at the forefront of the industry. By collaborating with experts and industry professionals, (name removed) is able to identify emerging trends and develop novel solutions to address the unique challenges faced by its customers.(name removed)'s fire kiln refractory bricks come in a variety of shapes, sizes, and compositions to meet the diverse needs of its customers. Whether it's a large industrial furnace or a small backyard fireplace, (name removed) can provide the perfect refractory bricks to ensure optimal performance and longevity. The company also offers customized solutions, working closely with clients to design and manufacture bricks that meet their specific requirements.In addition to their remarkable durability, (name removed)'s refractory bricks offer superior insulation properties, contributing to energy efficiency and cost savings. By minimizing heat loss, these bricks help to maintain stable temperatures and reduce energy consumption, thus increasing the overall efficiency of the system. This not only benefits the environment but also saves the end-users substantial amounts of money in the long run.Furthermore, (name removed) places great emphasis on sustainability and environmental responsibility throughout its manufacturing processes. By using environmentally friendly materials and adopting eco-friendly practices, they strive to minimize their carbon footprint and contribute to a greener future. The company also adheres to strict quality control measures to ensure that its products consistently meet or exceed industry standards.Since its inception, (name removed) has quickly established itself as a trusted and reliable supplier of refractory bricks. Its commitment to excellence, customer satisfaction, and continuous innovation has earned the company a solid reputation in the industry. With a global presence and a vast network of distribution partners, (name removed) is well-equipped to serve clients from various sectors and regions.In conclusion, the innovative fire kiln refractory bricks manufactured by (name removed) have revolutionized the construction industry. These durable and heat-resistant bricks have become the go-to choice for industries that require materials capable of withstanding extreme temperatures. With a focus on research and development, (name removed) continues to introduce cutting-edge solutions, pushing the boundaries of what is possible in the field of refractory brick manufacturing. As the company grows and expands its product offerings, it is poised to play a pivotal role in shaping the future of the industry.
All You Need to Know About Monolithic Castable Refractory for High-Temperature Applications
Monolithic Castable Refractory – Revolutionizing the Refractory IndustryIn the world of heavy industries, refractories play a significant role in ensuring the longevity of high-temperature equipment. Refractories are inorganic, non-metallic materials that can withstand extreme temperatures and harsh environments. They are used as insulators for furnaces, kilns, incinerators, and reactors. Refractories are also used as lining materials in industries such as cement, steel, aluminum, and petrochemical.However, traditional refractory materials such as bricks, tiles, and precast shapes have certain limitations. These materials are time-consuming and require skilled labor for installation. They also have low thermal shock resistance and exhibit cracking, spalling, and erosion after a short period. This leads to frequent maintenance, downtime, and loss of productivity.To overcome these challenges, manufacturers have developed new types of refractory materials, including monolithic castable refractory. This is a revolutionary material that has completely transformed the refractory industry. In this news article, we will explore the benefits and advancements of this innovative material and its impact on various industries.What is Monolithic Castable Refractory?Monolithic castable refractory is a type of refractory material that is made by combining various raw materials such as fine grain, coarse grain, bonding agents, and additives. The mixture is then placed into a mold or sprayed onto a surface. It hardens when exposed to high temperatures and forms a monolithic, seamless structure. The term “monolithic” refers to the fact that it is a single piece, as opposed to traditional refractory materials that are made of multiple pieces.This type of refractory material offers numerous advantages over traditional materials. They include:Less Labor Intensive – Monolithic castables are easier to install compared to traditional materials. They can be poured, sprayed or troweled into place, reducing the need for skilled labor. This significantly lowers the cost of installation and maintenance.Better Insulation Properties - Monolithic castables offer better insulation than traditional materials. This is because they have fewer joints and cracks, which reduce heat loss. This translates to lower energy costs and improved thermal efficiency.Higher Thermal Shock Resistance – Monolithic castables have high thermal shock resistance, which means that they can withstand rapid temperature changes without cracking or spalling. This prolongs the lifespan of the material, reduces maintenance costs and minimizes downtime.Wide Range of Applications – Monolithic castables have a wide range of applications in various industries. They are used as linings in furnaces, kilns, incinerators, and reactors. They are also used as insulating materials for pipes, ducts, boilers, chimneys, and stacks. Their versatility makes them suitable for a broad range of applications.Company Introduction{Remove Brand Name} is a leading global manufacturer of monolithic castable refractory materials. The company was founded over 70 years ago and has since then grown into a global leader in the refractories industry. {Remove Brand Name} offers a wide range of refractory solutions to various industries, including steel, cement, power generation, petrochemical, and aluminum.{Remove Brand Name} has a team of experienced scientists and engineers who are dedicated to developing innovative, high-quality products that meet the needs of their clients. They use state-of-the-art manufacturing processes and equipment to ensure that their products are of the highest quality.{Remove Brand Name} has a strong commitment to sustainable practices, which is reflected in their use of eco-friendly, sustainable raw materials, and their focus on reducing waste and emissions. They work closely with clients to identify their needs and provide customized solutions that meet their specific requirements.Recent DevelopmentsIn recent years, {Remove Brand Name} has made significant advancements in the development of monolithic castable refractory materials. They have developed new products that offer even better thermal performance, insulation, and durability.One of their recent innovations is the use of advanced nanotechnology in their refractory materials. This technology involves the use of nanoparticles that are dispersed throughout the material. The nanoparticles enhance the material's thermal properties, such as thermal conductivity, radiation absorption, and insulation. This results in better thermal efficiency, reduced energy costs, and improved overall performance.{Remove Brand Name} has also developed new manufacturing processes that reduce the environmental impact of their products. They use renewable, eco-friendly raw materials, and reduce waste and emissions during the manufacturing process. This ensures that their products are both high-quality and sustainable.ConclusionIn conclusion, monolithic castable refractory materials have revolutionized the refractory industry. They offer numerous advantages over traditional materials, such as reduced labor costs, better insulation, and higher thermal shock resistance. {Remove Brand Name} is a leading manufacturer of high-quality monolithic castable refractory materials. They have made significant advancements in the development of new products that offer even better thermal performance and durability. With their strong commitment to sustainable practices and client-focused approach, {Remove Brand Name} is poised to continue leading the way in the refractory industry.
Optimize Your Furnace with Innovative Electric Refractory Bricks
Electric Refractory Bricks: A Revolutionary Innovation in the Construction IndustryIn recent times, the construction industry has witnessed a significant revolution with the introduction of electric refractory bricks. Electric refractory bricks are heat-resistant blocks used to line the inside of industrial furnaces, kilns, and ovens. These bricks are made of high-quality refractory materials that can withstand extremely high temperatures, making them ideal for use in various industries such as steel, cement, and chemical.Electric refractory bricks are considered a revolutionary innovation in the construction industry, as they provide many benefits such as longevity, cost-efficiency, and high performance. These bricks have a longer lifespan than conventional refractory bricks, which means that they do not need to be replaced as frequently. Additionally, they have a higher thermal conductivity, which allows them to absorb heat more efficiently and reduce energy consumption.Electric refractory bricks are a more cost-effective solution for industrial applications, as they reduce the need for frequent maintenance and replacement. They are also easier to install, as they can be placed quickly without the need for special machinery or expertise. This means that construction projects can be completed faster and with less labor costs.One company that has been at the forefront of the electric refractory brick industry is ABC Refractory. ABC Refractory is a global leader in the production and installation of electric refractory bricks. The company offers various types of electric refractory bricks that are designed to meet the diverse needs of different industries.ABC Refractory's bricks have been widely used in the steel and cement industries. They have also been used in the chemical industry to increase energy efficiency and reduce emissions. ABC Refractory's electric refractory bricks have set new standards for construction materials in the industry and have been highly praised for their performance and durability.Apart from offering high-quality refractory bricks, ABC Refractory provides comprehensive services to its clients, including design, installation, and maintenance. The company's team of experts helps clients select the most suitable electric refractory bricks for their specific industrial applications. They also provide installation services to ensure that the bricks are correctly positioned, reducing the risk of any damage or malfunction.ABC Refractory's maintenance services are designed to prolong the life of the electric refractory bricks and ensure that they continue to perform optimally. The company's team of technicians conducts regular inspections to detect any defects or signs of wear and tear. They also provide repair services to fix any issues that may arise.ABC Refractory has built a reputation for its commitment to quality, professionalism, and customer satisfaction. The company has a strict quality control system to ensure that its products and services meet the highest standards. ABC Refractory's electric refractory bricks are tested rigorously to ensure they meet the required specifications and can withstand the harsh conditions of industrial applications.In summary, electric refractory bricks are a revolutionary innovation that has transformed the construction industry. They provide many benefits such as longevity, cost efficiency, and high performance. ABC Refractory has been at the forefront of this innovation and has set new standards for the industry. With its comprehensive services and strict quality control, ABC Refractory is a reliable partner for any company that wishes to use electric refractory bricks in its industrial applications.
Insulating Castable Refractory Cement: Enhancing Heat Resistance and Insulation
Insulating Castable Refractory Cement: The Ultimate Solution for Industrial Heat ManagementIndustrial processes that involve high temperature require a lot of heat control mechanisms. Such mechanisms are put in place to prevent the equipment and products from melting or catching fire. Refractories are the materials used in the construction of these heat management systems.The idea of insulation castable refractory cement is nothing new to the industry. However, thanks to advancements in technology, there are more innovative options available today. Insulating castable refractory cement is one such option that has become increasingly popular.This product is particularly known for its ability to offer excellent thermal performance, energy efficiency, and high strength. It is made by mixing high-quality fine powder with fibers and binders, ensuring excellent quality, and performance.Insulating Castable Refractory Cement is a game-changer in the construction and repair of industrial furnaces and boilers. It is also used to insulate pipes and chimneys, making it a versatile product that can be applied in a variety of settings.Due to its high quality, this product from __________ - a global leader in the refractory industry - has become increasingly popular. This company is renowned for its commitment to quality, and customer satisfaction, providing a range of refractory products that meet the most challenging requirements.In addition to its exothermic insulation properties, insulating castable refractory cement also has high compressive strength. As a result, it can withstand heavy weight and pressure without cracking, ensuring durability and longevity, even in the most challenging conditions.The use of Insulating Castable Refractory Cement in the construction of boilers and furnaces has numerous benefits. One of the most significant benefits is energy efficiency. The insulation properties of this product help to reduce energy loss, while also facilitating the maintenance of consistent temperatures during industrial processes.Using this product has also proven to be cost-effective. Although initially more expensive than traditional insulating materials, it offers higher performance, reducing the overall cost of production in the long run.When working with insulating castable refractive cement, it is essential to hire professionals who are knowledgeable in the handling, mixing, and installation process. This not only ensures the best results but also guarantees the safety of the workers involved in the installation process.In conclusion, Insulating Castable Refractory Cement is the ultimate solution for industrial heat management, offering superior thermal performance, high compressive strength, durability, and energy efficiency. With the increasing demand for energy efficiency in industrial processes, investing in this product from __________- a global leader in the refractory industry - is the best solution for businesses that want to stay ahead of the game.
Discover the Benefits of Acid Resistant Refractory Castable for Your Needs
[Your Name][Date]Acid Resistant Refractory Castable: Revolutionizing High-Temperature Applications[City, State] - Acid Resistant Refractory Castable, an innovative product developed by [Company Name], is set to revolutionize high-temperature applications across a range of industries. With its exceptional durability and resistance to acidic environments, this castable material is a game-changer for businesses seeking reliable and cost-effective solutions.[Company Name] has been at the forefront of refractory materials for [number of years] years, specializing in the development and production of advanced ceramics and composite materials. With a dedicated team of researchers and engineers, the company has consistently pushed the boundaries of what is achievable in high-temperature applications.Acid Resistant Refractory Castable is the result of extensive research and development efforts by [Company Name]. This cutting-edge product offers superior resistance to acids, alkalis, and other corrosive substances found in various industrial processes. By withstanding the harshest conditions, this castable material significantly extends the service life of refractory linings, thereby reducing downtime and maintenance costs for businesses.One of the key advantages of Acid Resistant Refractory Castable is its exceptional chemical stability. The unique composition of the castable material allows it to withstand continuous exposure to strong acids, such as sulfuric acid and hydrochloric acid, without deteriorating or losing its properties. This not only enhances the overall performance of the refractory lining but also ensures the safety of personnel working in corrosive environments.Furthermore, the castable material exhibits excellent thermal shock resistance, enabling it to withstand rapid temperature changes without cracking or spalling. It can endure temperatures of up to [temperature range], making it suitable for a wide range of applications, including furnaces, kilns, reactors, and various chemical processing equipment.The installation process of Acid Resistant Refractory Castable is efficient and convenient, thanks to its excellent workability and flowability. This allows for precise and uniform casting, ensuring a seamless refractory lining that maximizes performance and reduces heat loss. Moreover, the material demonstrates excellent adhesion to various substrates, including bricks, steel, and concrete, providing a reliable and long-lasting solution for businesses.To meet the diverse requirements of different industries, [Company Name] offers customizable options for Acid Resistant Refractory Castable. The product can be tailored to specific project needs, including different chemical resistance levels, particle size distributions, and setting times. This flexibility ensures that customers receive a product that precisely matches their unique application requirements.Acid Resistant Refractory Castable has garnered positive feedback from numerous industries, including the petrochemical, metallurgical, and power generation sectors. "We have witnessed a noticeable improvement in the durability of our refractory linings after switching to Acid Resistant Refractory Castable," said [Company representative]. "This has led to significant cost savings and increased overall operational efficiency."[Company Name] continues to invest in cutting-edge research and development, striving to improve and expand their product line to meet evolving industry demands. In addition to Acid Resistant Refractory Castable, the company offers a wide range of refractory materials and solutions, including monolithic castables, ceramic fiber products, and high-temperature insulation materials.With Acid Resistant Refractory Castable, [Company Name] is leading the charge in providing reliable and cost-effective solutions for high-temperature applications. This revolutionary product is set to reshape several industries, enabling businesses to operate in corrosive environments with confidence, durability, and enhanced efficiency.About [Company Name]:[Company Name] is a leading provider of advanced refractory materials and solutions. With a strong focus on research and development, the company offers a wide range of high-quality products that cater to diverse industry needs. [Company Name]'s commitment to innovation, quality, and customer satisfaction has positioned it as a trusted partner for businesses worldwide.For media inquiries, please contact:[Company Contact Information]