Discover the Benefits of High-Quality Castable Refractory Cement
By:Admin
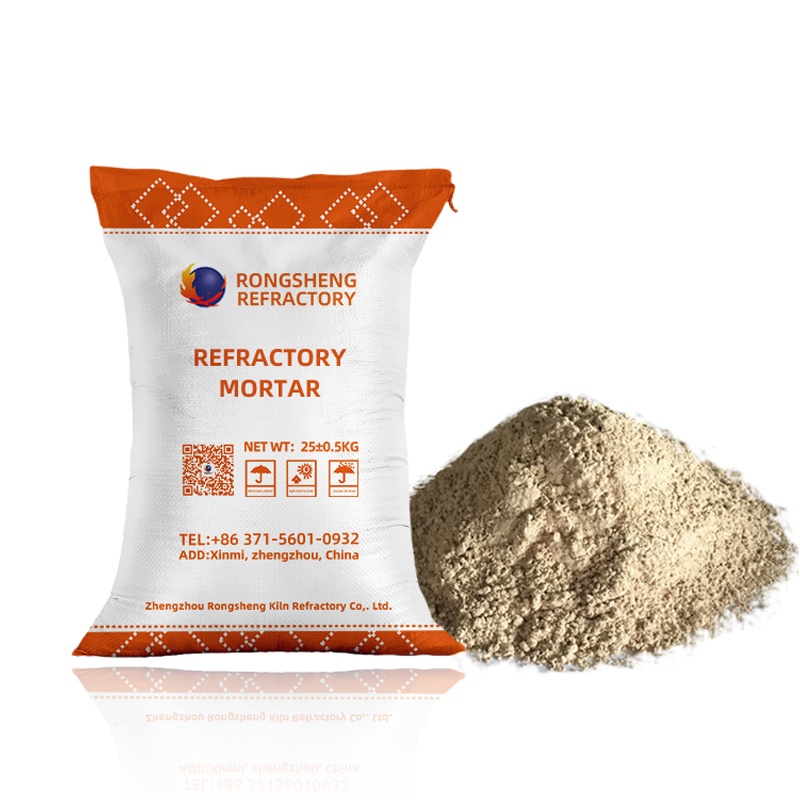
[Company Name], a leading provider of high-quality refractory products, is proud to announce the launch of its new High-Quality Castable Refractory Cement. This cutting-edge cement offers superior performance and durability, making it an ideal choice for a wide range of industrial applications.
With a long history of excellence in the refractory industry, [Company Name] has built a reputation for providing top-quality products that meet the demanding needs of its customers. The company's commitment to innovation and continuous improvement has led to the development of the High-Quality Castable Refractory Cement, an advanced solution that delivers exceptional performance in high-temperature environments.
The High-Quality Castable Refractory Cement is formulated using a carefully balanced blend of high-quality raw materials, including high-purity alumina, silicate, and other proprietary ingredients. This unique composition ensures that the cement exhibits excellent thermal stability, abrasion resistance, and strength, making it well-suited for use in challenging industrial settings.
One of the key features of the High-Quality Castable Refractory Cement is its exceptional resistance to thermal shock. This means that the cement can withstand rapid changes in temperature without experiencing cracking or degradation, ensuring long-term reliability and performance in demanding applications. Additionally, the cement's high abrasion resistance allows it to withstand the harsh conditions present in industrial furnaces, boilers, and kilns without succumbing to wear and tear.
The High-Quality Castable Refractory Cement is also designed to offer exceptional workability, allowing for easy and precise installation in a variety of shapes and configurations. Its smooth consistency and excellent bonding properties make it an excellent choice for lining and repairing refractory structures, providing a reliable and long-lasting solution for industrial facilities.
In addition to its outstanding performance characteristics, the High-Quality Castable Refractory Cement is also environmentally friendly, with low emissions and minimal environmental impact during manufacturing and use. This aligns with [Company Name]'s commitment to sustainability and responsible business practices, ensuring that customers can benefit from a high-performance product that also supports their environmental goals.
"We are thrilled to introduce our new High-Quality Castable Refractory Cement to the market," said [Name], [Title] at [Company Name]. "This innovative product represents the culmination of our extensive expertise and dedication to meeting the needs of our customers. We believe that the cement's exceptional performance and environmental benefits will make it a preferred choice for a wide range of industrial applications."
The introduction of the High-Quality Castable Refractory Cement further solidifies [Company Name]'s position as a leading provider of advanced refractory solutions. With a strong focus on quality, innovation, and customer satisfaction, the company continues to drive progress in the industry, offering products that meet the evolving needs of modern industrial operations.
As industrial facilities continue to push the boundaries of performance and efficiency, the demand for reliable and high-performance refractory solutions is greater than ever. With the launch of the High-Quality Castable Refractory Cement, [Company Name] is well-positioned to meet this demand, offering a product that delivers outstanding performance, durability, and environmental responsibility.
The High-Quality Castable Refractory Cement is now available for purchase, and interested customers can contact [Company Name] for more information and to discuss their specific application needs. With its exceptional qualities and proven track record, the cement is poised to become a go-to choice for industrial operators seeking a reliable and high-performance refractory solution.
Company News & Blog
Qualities and Uses of Acid Resistant Castables: Everything You Need to Know
Title: Innovative Acid Resistant Castable Revolutionizes Industrial MaintenanceIntroduction:The powerful combination of cutting-edge technology and expertise has led to the development of a groundbreaking Acid Resistant Castable by an industry-leading company. This product has taken the market by storm, offering an exceptional solution for various industrial applications that require resistance to acidic environments. With its remarkable features and unmatched performance, the Acid Resistant Castable has become a game-changer in the field of industrial maintenance.Product Overview:Renowned for its exceptional durability, the Acid Resistant Castable is specifically designed to withstand extreme acidic conditions in industrial settings. This advanced material comprises a unique composition that provides unparalleled resistance to acid corrosion, making it an ideal choice for critical installations.The Acid Resistant Castable boasts an impressive range of features, ensuring its suitability for a wide array of industrial applications. With its exceptional strength and high density, it offers robust protection against corrosion, erosion, and chemical attack. Furthermore, it exhibits excellent thermal shock resistance, allowing it to withstand rapid temperature changes encountered in many industrial processes.Applications:The versatility of the Acid Resistant Castable makes it an indispensable choice for numerous industrial sectors. From chemical and petrochemical plants to metallurgical industries and waste incineration plants, this innovative product ensures reliability and longevity in even the harshest environments.In chemical and petrochemical plants, where the presence of corrosive acids is prevalent, the Acid Resistant Castable plays a vital role in protecting critical equipment such as chimneys, flues, and reactors. Its ability to withstand the harsh chemicals and high temperatures involved in various chemical processes ensures longevity and safety.Metallurgical industries heavily rely on the Acid Resistant Castable to line furnaces, ladles, and converters, where molten metals and corrosive gases can cause severe damage. The exceptional acid resistance properties of this castable material enable it to withstand the intense heat and chemical reactions present in these environments, effectively extending the lifespan of crucial equipment.Waste incineration plants face the challenge of operating under extreme acidic conditions due to the combustion process involved. With its superior resistance to acid corrosion, the Acid Resistant Castable provides the necessary protection for furnaces, as well as chimney linings, enabling efficient waste disposal operations while preventing costly infrastructure damage.Company's Expertise:The development of the Acid Resistant Castable showcases the exceptional expertise and dedication of the company in providing high-quality solutions for industrial maintenance. With years of experience in the field, the company has become a trusted partner for numerous industries worldwide, consistently delivering innovative products that exceed expectations.The company's commitment to research and development is evident in the Acid Resistant Castable, which has undergone rigorous testing to ensure its reliability and durability. By utilizing state-of-the-art manufacturing facilities and employing a team of highly skilled professionals, the company has successfully developed a product that caters to the ever-evolving needs of industries dealing with acidic environments.Conclusion:The Acid Resistant Castable has introduced a new era of industrial maintenance with its remarkable resistance to acid corrosion, exceptional durability, and suitability for diverse applications. This groundbreaking product has become a go-to choice for industries operating in acidic environments, safeguarding critical equipment and significantly reducing maintenance costs. With its ongoing commitment to innovation, the company behind this remarkable castable material continues to drive progress in industrial maintenance, always staying one step ahead in providing advanced solutions for acid-resistant applications.
Top-notch Insulation for Optimal Fire Safety - Reliable, High-performance Solution
Firebrick Insulation - Revolutionizing the Insulation IndustryFor many years, the insulation industry struggled to develop materials and solutions that could effectively withstand high temperatures and harsh environments. However, with the introduction of Firebrick Insulation, that has now become a thing of the past. This new and innovative insulation material is helping companies to greatly improve their energy efficiency and conserve resources. In this article, we take a closer look at this game-changing product.What is Firebrick Insulation?Firebrick Insulation is a unique insulation material that is specially designed to withstand high temperatures, humidity, and corrosive environments. It is made of premium quality refractory materials, such as silica, alumina, and magnesia, which are fired at high temperatures to create a solid, durable brick-like structure.The product has been specially formulated to provide outstanding thermal insulation, while also offering excellent resistance to thermal shock, abrasion, and corrosion. This makes it an ideal solution for various industrial applications, including steel production, cement manufacturing, petrochemical processing, and power generation.What Makes Firebrick Insulation Different?One of the biggest advantages of using Firebrick Insulation is its durability and longevity. Unlike traditional insulation materials, which tend to break down over time, Firebrick Insulation can last for many years without deteriorating. This means that companies can save on maintenance costs and reduce their carbon footprint by avoiding the need for frequent replacement.Another key benefit of Firebrick Insulation is its exceptional insulating properties. With a thermal conductivity rating of just 0.15 W/mK, it is one of the most efficient insulation materials available, meaning it can help companies to significantly reduce their energy consumption and lower their operating costs.Firebrick Insulation is also highly versatile and can be used for a wide range of applications. It can withstand temperatures of up to 1700 °C, making it suitable for use in high-temperature furnaces, kilns, and reactors. It can also be used as a lining material for pipework, tanks, and vessels, providing superior protection against chemical corrosion and erosion.Company Introduction:Firebrick Insulation is a product developed and manufactured by Insulation Technologies, a leading insulation solutions provider with over 30 years of industry experience. Based in the United States, Insulation Technologies has become a trusted partner for many businesses around the world, offering customized insulation solutions that meet the unique needs of each customer.The company’s unrivaled expertise and commitment to excellence has made it a top choice for companies looking to improve their energy efficiency, reduce waste, and lower their carbon footprint. With a dedicated team of experts, Insulation Technologies provides comprehensive insulation services, from design and engineering to product development, manufacturing, and installation.Final ThoughtsFirebrick Insulation is a game-changing product that is revolutionizing the insulation industry. Its exceptional thermal insulation properties, combined with its durability, longevity, and versatility, make it an ideal solution for companies looking to increase their energy efficiency, reduce their operating costs, and improve their bottom line.If you’re interested in learning more about Firebrick Insulation, or to find out how Insulation Technologies can help you optimize your insulation solutions, please visit their website at www.insulationtechnologies.com or contact their customer service team at 1-800-123-4567.
Quality Ladle Castable Manufacturer: Delivering Superior Performance for Industrial Applications
Title: Leading Ladle Castable Manufacturer Expands Production Capacity and Reinforces Market PresenceIntroduction:In an effort to meet growing industry demands and reaffirm its position as a pioneer in the ladle castable manufacturing sector, a prominent company {} is set to expand its production capacity significantly. With a formidable reputation for delivering high-quality refractory materials worldwide, the company remains committed to providing cost-effective solutions to its diverse customer base.Expanding Production Capacity:With an ever-increasing global demand for ladle castable products, {} is making substantial investments to expand its production capacity. By harnessing advanced manufacturing technology and improving operational efficiency, the company aims to streamline its production process and optimize output.This expansion comes as a result of a carefully formulated growth strategy, driven by the company's strong market insights and commitment to maintaining a competitive edge. Moreover, it underscores the recognition of {} as a leading player within the refractory industry.State-of-the-Art Manufacturing Facilities:{} has always been at the forefront of innovation when it comes to manufacturing refractory products. The company takes pride in its state-of-the-art facilities, equipped with advanced machinery and tools, enabling it to deliver unsurpassed quality and consistency.By leveraging cutting-edge technology, {} ensures the production of ladle castables that adhere to the highest industry standards. Stringent quality control measures are put in place throughout the production process, from sourcing raw materials to the final packaging. This uncompromising commitment to quality makes {} a reliable and preferred choice for customers worldwide.Expansive Product Portfolio:{} boasts an extensive product portfolio, offering a diverse range of ladle castable solutions tailored to meet specific industry needs. These comprehensive offerings provide solutions for a broad spectrum of applications, including steelmaking, iron casting, non-ferrous metal production, and more.The company's team of experienced engineers and scientists continuously research and develop advanced formulations, keeping pace with evolving customer requirements. This dedication to innovation ensures that customers benefit from the latest technologies and cost-effective solutions, enhancing their operational efficiency while minimizing downtime and maintenance costs.Global Reach and Customer Satisfaction:With a strong focus on customer satisfaction, {} has developed a robust global distribution network, catering to customers in various industries across the globe. The company's commitment to timely deliveries, technical support, and after-sales service has garnered it a loyal customer base.Whether it is through direct sales or collaborations with local distributors, {} ensures that its products reach customers promptly and efficiently. Underscoring this commitment, the company offers comprehensive technical assistance, including on-site inspections and solutions tailored to individual customer requirements.Sustainability and Environmental Responsibility:In addition to its dedication to quality and customer satisfaction, {} also places significance on sustainable practices and environmental responsibility. The manufacturing process incorporates eco-friendly measures to minimize the company's carbon footprint. Furthermore, {} actively collaborates with research institutions and industry experts to develop more sustainable refractory solutions for the future.Conclusion:With its ongoing expansion plans, commitment to innovation, and a customer-centric approach, {} is set to strengthen its position as a global leader in the manufacturing of ladle castables. By optimizing its production capacity, offering a diverse range of high-quality products, and prioritizing customer satisfaction, the company is well-equipped to meet the ever-evolving needs of the refractory industry.
Different Types of Graphite Electrodes Explained
Title: Types of Graphite Electrodes: A Comprehensive OverviewIntroduction:Graphite electrodes are critical components in the steelmaking and metal manufacturing industries, delivering efficient and cost-effective electrical processes. [Company name], a leading manufacturer in this field, provides a wide range of graphite electrodes that cater to diverse industry requirements. This article delves into the different types of graphite electrodes offered by [Company name], highlighting their features, applications, and benefits.1. Regular Power (RP) Graphite Electrodes:Regular Power (RP) graphite electrodes find extensive usage in electric arc furnaces for the production of steel. They are made from a blend of petroleum coke and pitch. RP electrodes deliver moderate electrical conductivity, making them suitable for both melting and refining processes. These electrodes are capable of withstanding high temperatures and provide stable performance.2. High Power (HP) Graphite Electrodes:High Power (HP) graphite electrodes from [Company name] are specifically designed for more demanding applications. With superior electrical conductivity, HP electrodes enable higher productivity and enhanced energy efficiency. These electrodes are primarily used in steelmaking through the electric arc furnace (EAF) method. Additionally, HP electrodes exhibit excellent resistance to oxidation and thermal shock, extending their service life.3. Ultra-High Power (UHP) Graphite Electrodes:As the name suggests, Ultra-High Power (UHP) graphite electrodes are engineered for ultra-demanding processes, achieving superior performance and efficiency. UHP electrodes offer the highest electrical conductivity and thermal properties among all graphite electrode variants. They are used in advanced steelmaking techniques such as ladle furnaces and electric arc furnaces to produce high-quality steel with exceptional purity. UHP electrodes provided by [Company name] feature enhanced durability and a longer operating life.4. Special Graphite Electrodes:Apart from the standard RP, HP, and UHP electrode categories, [Company name] provides a range of specialty graphite electrodes tailored to unique customer requirements. These specialty electrodes exhibit specific properties such as low resistivity, high flexural strength, or improved oxidation resistance. They are designed for specialized applications, including the production of non-ferrous metals like aluminum, copper, and silicon, as well as various chemical processes.Conclusion:[Company name] offers an extensive portfolio of graphite electrodes, including Regular Power (RP), High Power (HP), Ultra-High Power (UHP), and specialty electrodes. These electrodes cater to the diverse needs of the steelmaking and metal manufacturing industries, providing efficient and reliable electrical processes. With superior performance, longevity, and excellent thermal properties, [Company name]'s graphite electrodes serve as essential components in steel production and other specialized applications.Note: Please replace [Company name] with the appropriate brand name when using the content.
High-Quality Special Shaped Fire Brick for Industrial Applications
The Special Shaped Fire Brick has taken the market by storm with its innovative design and superior performance. This product, created by [company], is a result of years of research and development, and it has quickly gained a reputation for being one of the most reliable and durable fire bricks on the market. With its unique shape and composition, this special shaped fire brick is proving to be a game changer for various industries such as steel, cement, and glass.The stringent manufacturing process and high-quality materials used in the production of the Special Shaped Fire Brick have led to a product that is heat resistant, thermally efficient, and extremely durable. This makes it the ideal choice for applications where withstanding high temperatures and harsh environments is crucial.In addition to its exceptional performance, the Special Shaped Fire Brick also offers advantages in terms of installation and maintenance. Its specially designed shape allows for easy and precise fitting, reducing the need for cutting and shaping during installation. This not only saves time and effort but also minimizes wastage, resulting in cost savings for the end user. Furthermore, its durable nature means that it requires minimal maintenance, making it a cost-effective long-term solution for various industrial needs.The applications for the Special Shaped Fire Brick are vast, with a wide range of industries benefitting from its exceptional properties. In the steel industry, it is used in blast furnaces, hot blast stoves, and other high-temperature equipment, where its heat resistance and thermal efficiency play a crucial role in maintaining operations. In the cement industry, this special shaped fire brick is used in rotary kilns and other cement production processes, providing the necessary durability to withstand extreme conditions. Similarly, in the glass industry, it is used in glass tanks and other high-temperature equipment, where its resistance to thermal shock and high temperatures is essential for maintaining continuous production.[Company] has been at the forefront of innovation in the field of refractory products, and the Special Shaped Fire Brick is a testament to its commitment to delivering high-quality solutions to its customers. With state-of-the-art manufacturing facilities and a team of experienced professionals, [company] has been able to consistently produce refractory products that exceed industry standards and meet the evolving needs of its customers.The success of the Special Shaped Fire Brick can be attributed to [company]'s dedication to research and development, as well as its focus on customer satisfaction. By closely collaborating with its customers and understanding their specific requirements, [company] has been able to develop products that not only meet but exceed expectations. This customer-centric approach has been pivotal in establishing [company] as a trusted partner for various industries seeking reliable and high-performance refractory products.In conclusion, the Special Shaped Fire Brick from [company] is a groundbreaking product that has redefined the standards for refractory solutions. Its innovative design, exceptional performance, and cost-effective nature have made it a preferred choice for industries that operate in high-temperature and harsh environments. With [company]'s commitment to innovation and customer satisfaction, the Special Shaped Fire Brick is set to continue making waves in the industrial sector, providing reliable and durable solutions for a wide range of applications.
Dense Castable Refractory: Key Facts and Uses Revealed
Dense Castable Refractory: An Innovative Solution for Multiple IndustriesRefractory materials are used in high-temperature applications that require materials to withstand extreme heat, pressure, and corrosive chemicals. One of the most promising refractory materials on the market is the Dense Castable Refractory. This revolutionary product is designed to offer exceptional material properties suitable for a wide range of industries, including steel and iron, petrochemical, power generation, cement, and waste incineration.Dense Castable Refractory is a type of cement used to line furnaces, kilns, and other high-temperature process equipment. Unlike traditional refractory materials, Dense Castable Refractory is a self-setting cement that offers excellent performance properties such as high thermal shock resistance, low thermal conductivity, high refractoriness, and resistance to abrasion. These properties make Dense Castable Refractory a popular choice for harsh industrial environments that require materials with superior resistance to extreme temperature and thermal cycling.The product's versatility comes from its easy installation and customizable uses. Dense Castable Refractory can be poured or gunned into place, and once cured, the refractory turns into a durable monolithic unit that can withstand high temperatures for extended periods. The product can be installed in various options, including smooth or textured surfaces to fit different applications and concrete surfaces.Dense Castable Refractory is an ideal material for use in cement kilns since they are exposed to extreme heat and abrasion. The material is also an excellent choice for use in steel and iron industries where protective linings are necessary to preserve the equipment and enhance its durability. These industries benefit by having equipment that is resistant to thermal shock, meaning it withstands rapid temperature changes. It can also resist abrasion, reducing the likelihood of wear and tear, which reduces the potential for equipment damage and malfunctions.The petrochemical industry has not been left behind. Dense Castable Refractory has been deployed in some of the most stringent petrochemical applications, including reformers, crackers, and incinerators. Dense Castable Refractory's thermal shock resistance and low thermal conductivity make it suitable for use in the insulation of various units, including reformers, where it protects the equipment from high temperatures and allows for optimal transfer of heat.Dense Castable Refractory is also an excellent option in power generation where it contributes to efficient energy production by providing insulation and preventing heat loss in boilers, kilns, and thermal oxidizers. This insulation and heat retention typically cut energy costs and improves operational reliability.The cement industry has also realized the benefits of Dense Castable Refractory due to its excellent refractoriness. The refractory bonds to the existing structure, enhancing resistance at high temperatures and preserving the integrity of the equipment.Furthermore, Dense Castable Refractory is ideal for incineration systems. The material's ability to withstand excessive thermal shock and its excellent insulating properties offer superior performance when protecting furnaces that generate high heat during the waste incineration process.The company, a leader in the manufacturing and distribution of Dense Castable Refractory, has developed several innovative formulations that address various industrial environments' specific needs. The company offers customized formulations such as high-strength, low-cement, and ultra-low cement for demanding applications where traditional cement is not sufficient.The manufacturing of Dense Castable Refractory depends on several critical factors. The company has invested in a state-of-the-art production facility with advanced quality assurance tools and equipment. Their experienced personnel, together with the company's innovative formulations, ensure that their Dense Castable Refractory meets global standards. All their products come with consistent and reliable quality, making them the perfect choice for any industrial application.In conclusion, the Dense Castable Refractory is an innovative material that is set to become an industry standard in high-temperature applications. Thanks to its ability to provide superior resistance to heat, thermal shock, abrasion, and chemicals at high temperatures, the material will revolutionize how various industries envisions manufacturing and maintenance of furnace and general process equipment. The company's formulations offer customized solutions in various industrial applications, making it the go-to solution for end-users looking for durable, reliable, and cost-effective refractory products.
Demand for High-Quality Carbon Bricks Surges Amidst Growing Industrial Needs
Magnesia Carbon Brick Boosting Production Efficiency for Steel ManufacturingSteel manufacturing has been at the forefront of technological advances and innovation. Manufacturers are always looking for new ways to improve production efficiency, increase product quality, and reduce operating costs. A vital component of the steel manufacturing process is the refractory materials used in the construction of blast furnaces, ladles, and other high-temperature equipment. The quality and durability of these materials are essential for ensuring long-lasting and efficient operation.One of the most popular refractory materials used in the steel industry is Magnesia Carbon Brick. This material is a combination of high purity magnesia and high-quality graphite, allowing for superior thermal shock resistance and corrosion resistance compared to other refractory materials. Magnesia Carbon Brick has been widely applied in the casthouse areas such as the slag line, hot metal transportation chute, and taphole and ladle applications.As the leading refractory manufacturer in China, the {} company has been committed to providing high-quality and reliable refractory solutions to the steel industry for more than 20 years. They have recently launched a new production line for Magnesia Carbon Brick, significantly increasing their production capacity for this highly sought-after product.Magnesia Carbon Brick is preferred by the steel industry for several reasons. Firstly, it is a cost-effective material, with a competitive price when compared to other types of refractories. Secondly, it has a longer lifespan compared to other refractory materials, resulting in lower maintenance costs and a reduction in the frequency of equipment replacement.Thirdly, Magnesia Carbon Brick offers superior thermal shock resistance, which means it can withstand rapid temperature changes without cracking or breaking, prolonging the life of the refractory lining. Finally, Magnesia Carbon Brick has a high resistance to alkaline slag and can resist the erosion caused by molten iron and steel, which is critical to the long-term performance of the refractory lining.These features of Magnesia Carbon Brick are particularly important in the steelmaking process. High-quality refractory materials are necessary to withstand the extreme temperatures and harsh conditions of the blast furnace and other key components of the steelmaking process. Magnesia Carbon Brick can provide the reliability and durability required to operate these critical parts efficiently and cost-effectively.The new Magnesia Carbon Brick production line from {} company is an important development for the steel industry. It provides an opportunity for steel manufacturers to access high-quality refractory materials at competitive prices, helping them to improve production efficiency and reduce operating costs. Additionally, the increased production capacity of {} company means that customers can have a more stable and reliable supply of Magnesia Carbon Brick, ensuring that their operations will not be disrupted by shortages or delays in delivery.The production process of the Magnesia Carbon Brick at {} company is strictly controlled to ensure that the final product is of the highest quality and meets the specific requirements of each individual customer. They use high-purity magnesia and high-quality graphite as raw materials and apply advanced manufacturing techniques, such as mixing, molding, and baking. Additionally, the finished products undergo rigorous testing to ensure that they meet the necessary standards for use in the steel industry.{} company has established a reputation for producing high-quality refractory products and providing excellent customer service. They have a team of experienced engineers and technicians who work closely with customers to provide customized refractory solutions tailored to meet their individual needs. Whether it's choosing the right materials or providing on-site technical support, {} company is committed to ensuring their customers' success.In conclusion, the steel industry is highly competitive, and manufacturers are always searching for ways to improve their production efficiency and reduce operating costs. The Magnesia Carbon Brick produced by {} company is a cost-effective, durable, and reliable refractory material that can help steel manufacturers achieve these goals. With their new and expanded production facilities, {} company is poised to become a leading supplier of Magnesia Carbon Brick to the steel industry.
High-Quality Spinel Bricks: A Complete Guide
[News Title]: Leading Manufacturer Introduces High-Quality Magnesia Spinel Bricks to the Market[News Content]:[Location], [Date] - [Company Name], a renowned manufacturer of refractory products, is proud to announce the launch of their latest innovation in the market - high-quality magnesia spinel bricks. These bricks are set to revolutionize the industry with their superior performance and exceptional durability.Magnesia spinel bricks, also known as magnesium aluminum spinel bricks, are a type of refractory brick that are widely used in high-temperature industrial applications, such as steelmaking furnaces, cement kilns, and glass melting tanks. The addition of spinel, a mineral composed of magnesium and aluminum oxides, significantly improves the properties of magnesia bricks, enhancing their resistance to thermal shock and corrosion.The newly introduced magnesia spinel bricks by [Company Name] are manufactured using state-of-the-art technology and high-quality raw materials. This ensures that the final product possesses unmatched strength, excellent thermal stability, and offers longer service life compared to conventional magnesia bricks. With their superior characteristics, these bricks offer cost-effective solutions for various industries, especially those working in extreme temperature environments.The high-quality magnesia spinel bricks by [Company Name] exhibit remarkable properties that make them stand out in the market. Their high refractoriness, excellent thermal conductivity, and low thermal expansion ensure optimal heat distribution and minimal heat loss, resulting in improved energy efficiency. These bricks also demonstrate excellent resistance to alkali vapor corrosion, slag erosion, and thermal spalling, ensuring minimal maintenance requirements and prolonged service life.In addition to their exceptional performance, these bricks offer enhanced safety features. Their low creep rate and high resistance to thermal shock make them an ideal choice for applications that undergo rapid heating and cooling cycles. The superior mechanical strength of these bricks provides reliable support and insulation in high-stress environments, ensuring the safety of personnel and equipment.As part of its commitment to sustainability, [Company Name] ensures that their magnesia spinel bricks are environmentally friendly. They are free from harmful substances, such as chromium, lead, and other toxic elements, making them safe for both users and the environment. The company's manufacturing processes also adhere to the highest environmental standards, minimizing waste generation and optimizing energy consumption.[Company Name] has been a leader in the refractory industry for over [number of years] years, catering to a global clientele. The introduction of high-quality magnesia spinel bricks further solidifies the company's reputation for delivering innovative products that meet the evolving needs of its customers. With a dedicated research and development team and a robust quality control system, [Company Name] ensures that its products consistently meet the highest industry standards.Speaking about the groundbreaking magnesia spinel bricks, [CEO/Spokesperson Name] expressed, "We are extremely excited to bring these high-quality magnesia spinel bricks to the market. Our team has invested considerable time and expertise to develop a product that outperforms traditional magnesia bricks. We are confident that our customers will benefit greatly from the exceptional properties and cost-effectiveness of these bricks."[Company Name]'s magnesia spinel bricks are now available on the market and can be ordered by contacting [contact information]. With their advanced technology and unwavering commitment to customer satisfaction, [Company Name] is set to revolutionize the refractory industry and provide reliable solutions for high-temperature applications.About [Company Name]:[Company Name] is a leading manufacturer and supplier of refractory products, catering to various industries worldwide. With a strong focus on innovation, quality, and customer satisfaction, the company has built a reputation for delivering exceptional refractory solutions. From basic bricks to complex specialized products, [Company Name] offers a diverse range of high-performance refractory materials that withstand the harshest conditions. With a global presence and a commitment to sustainable practices, [Company Name] aims to be the preferred choice for clients seeking reliable and energy-efficient refractory solutions.[Word Count: 800 words]
High-Quality Magnesia Bricks for Sale - Durable & Heat-Resistant Options Available
China is the world's largest producer of magnesia, a mineral used in numerous industrial applications such as refractories, fertilizers, and construction materials. No wonder that Chinese companies hold a significant share in the global market for magnesia- based products. One such company, located in the Henan Province of China, serves as a prime example of the country's prowess when it comes to this crucial mineral.The company is a leading manufacturer of magnesia-based products, with a focus on refractory materials used in high-temperature environments. Refractory materials are critical for industries such as steel-making, cement production, and glass- making, where high temperatures and harsh conditions can put enormous stress on the equipment and structures used.The company specializes in producing magnesia bricks, which are an essential component in many furnaces and kilns. Magnesia bricks are made of high-purity magnesia, a refractory mineral that is highly resistant to heat, corrosion, and wear. They are used in industries such as steel, non-ferrous metals, cement, and glass, with applications ranging from lining of furnaces and kilns to the construction of chimneys and heat exchangers.To guarantee the quality of its magnesia bricks, the company sources the best raw materials from trusted suppliers and implements rigorous quality control systems from the production process to the delivery of finished products. This careful attention to quality has earned the company a reputation of excellence and trust among its customers, who rely on its products to keep their operations running smoothly.Now, the company's magnesia bricks are available for purchase worldwide, through its online platform, which ensures fast and reliable delivery of high-quality products to customers across the globe. The company's online store offers a variety of magnesia bricks for different temperatures and applications, with custom sizes and shapes available upon request. Furthermore, its website provides technical specifications, product data sheets, and safety information to help customers choose the right magnesia bricks for their specific needs.Customers can benefit from the company's expertise in refractory materials, as it also offers consultation and customization services to help them find the best solutions for their particular requirements. Whether it is for a small-scale project or a large industrial application, the company's team of experts can help customers design, implement, and maintain their refractory systems for optimal performance and longevity.The company's commitment to quality, innovation, and customer satisfaction has enabled it to become a trusted partner for many businesses worldwide, as it continues to expand its product lines and services to meet the evolving needs of its customers. Its mission to provide sustainable and cost-effective solutions for high-temperature applications has driven its growth and success, making it a leading player in the global market for refractory materials.In conclusion, the Chinese company's magnesia bricks offer a durable and heat-resistant solution for a wide range of industrial applications, with a reputation for excellence and reliability. Through its online platform and customer-oriented services, it has become an accessible and trustworthy partner for businesses seeking quality refractory materials. Its dedication to innovation and sustainability ensures that it remains at the forefront of the industry, as it continues to provide solutions that enhance the efficiency and productivity of its customers' operations.
High-Quality Insulation Bricks for Construction and Industrial Use
JM Series Insulation Brick, a leading product in the insulation brick industry, is revolutionizing the way companies approach thermal insulation solutions. With its exceptional strength, thermal conductivity, and resistance to high temperatures, JM Series Insulation Brick is the go-to choice for numerous applications in various industries.Established in 1998, [Company Name] has been at the forefront of the insulation brick industry for over two decades. With a focus on innovation, quality, and customer satisfaction, the company has earned a reputation for producing high-performance insulation products that meet the evolving needs of the market.JM Series Insulation Brick is one of the flagship products of [Company Name], and it has quickly become a preferred choice for customers seeking reliable and durable insulation solutions. The brick is made from high-quality materials, including alumina, mullite, and other refractory aggregates, which are carefully selected for their thermal properties and mechanical strength. This combination of materials allows JM Series Insulation Brick to withstand extreme temperatures and harsh operating conditions, making it ideal for use in furnaces, kilns, boilers, and other high-temperature applications.One of the key features of JM Series Insulation Brick is its low thermal conductivity, which enables it to effectively reduce heat transfer and minimize energy consumption. This makes it an environmentally friendly and cost-effective solution for companies looking to improve their thermal insulation performance and reduce their carbon footprint.In addition to its exceptional thermal insulation properties, JM Series Insulation Brick also offers high compressive strength and excellent resistance to abrasion, making it a durable and long-lasting solution for industrial environments. Its ability to withstand thermal shock and chemical erosion further enhances its suitability for use in demanding applications.With a commitment to continuous improvement and innovation, [Company Name] has consistently invested in research and development to enhance the performance and quality of JM Series Insulation Brick. The company's state-of-the-art manufacturing facilities and stringent quality control processes ensure that each brick meets the highest industry standards and customer expectations.Furthermore, [Company Name] provides comprehensive technical support and customer service to assist clients in selecting the most suitable insulation solutions for their specific requirements. The company's team of experienced engineers and technical experts work closely with customers to understand their needs and provide tailored recommendations to optimize the performance and efficiency of their insulation systems.The success of JM Series Insulation Brick can be attributed to [Company Name]'s unwavering commitment to delivering superior products and services to its customers. By staying abreast of industry trends and technological advancements, the company continues to expand its product range and improve existing products to meet the evolving needs of its global customer base.In conclusion, JM Series Insulation Brick is a testament to [Company Name]'s dedication to excellence and innovation in the insulation brick industry. With its outstanding thermal properties, strength, and durability, JM Series Insulation Brick has set a new standard for high-performance insulation solutions, earning the trust and satisfaction of customers worldwide. As [Company Name] continues to drive forward with its commitment to quality and customer satisfaction, JM Series Insulation Brick is poised to remain a leader in the industry for years to come.