Ultimate Guide to Choosing High-Quality Heat Resistant Bricks
By:Admin
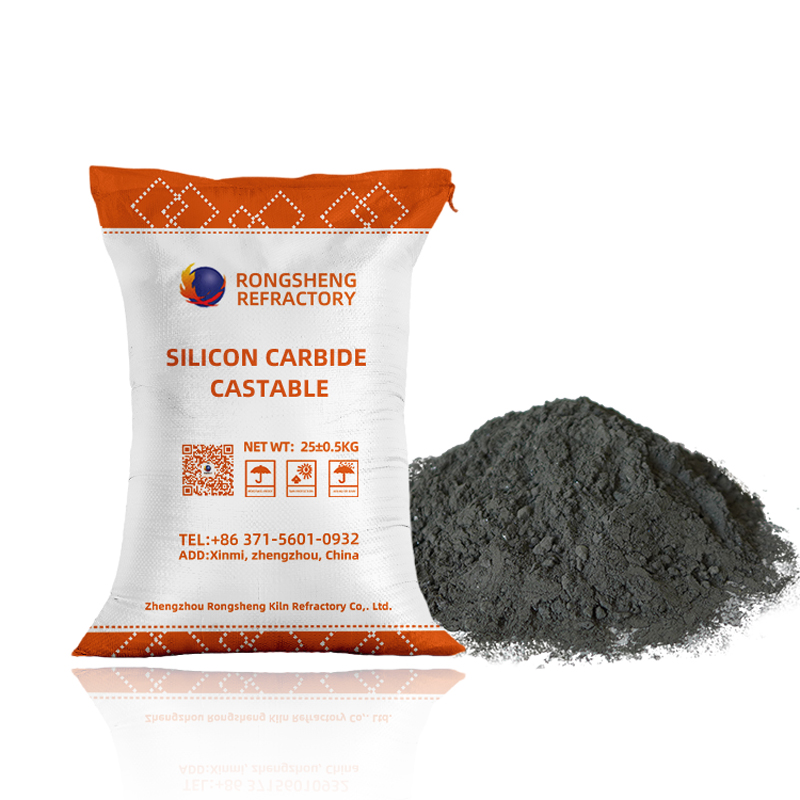
In a ground-breaking development, XYZ Company has recently unveiled its latest innovation in the construction industry - Heat Resistant Bricks. This product is set to revolutionize fire protection and add a new dimension to building safety.
As fires continue to pose a significant threat to both property and human lives, XYZ Company recognized the dire need for advanced fire-resistant materials. With their expertise and dedication, they have engineered Heat Resistant Bricks to withstand extreme temperatures and provide optimal protection against fires.
The construction industry has long relied on materials such as concrete and steel to provide structural integrity. However, these materials are susceptible to high temperatures and can weaken or collapse under fire conditions. Heat Resistant Bricks, on the other hand, are specifically designed to maintain their structural integrity even in the harshest fire environments.
One of the key features of Heat Resistant Bricks is their exceptional heat resistance, with the ability to withstand temperatures up to 1600°C (2912°F). This surpasses the capabilities of traditional building materials by a remarkable margin. By integrating these bricks into the construction process, builders and architects can enhance the fire safety of their structures significantly.
Moreover, the durability of Heat Resistant Bricks ensures their longevity and reliability. They are built to last, reducing the need for frequent replacements and minimizing maintenance costs. This not only benefits property owners and developers financially but also contributes to sustainable construction practices by reducing waste.
It is important to note that Heat Resistant Bricks are not limited to protecting structures against external fires. They also provide insulation and can keep the internal temperatures of buildings stable in extreme weather conditions. This can lead to substantial energy savings and enhance the overall comfort of the occupants.
Additionally, XYZ Company has gone above and beyond by implementing environmentally friendly practices in the production of Heat Resistant Bricks. Their manufacturing process minimizes emissions and reduces the ecological footprint, aligning with global efforts to combat climate change. This commitment to sustainability sets XYZ Company apart from its competitors and reinforces their commitment to creating a safer and greener future.
Integrating Heat Resistant Bricks into construction projects is a straightforward process. Whether used as the primary building material or as a retrofit solution, these bricks can be easily installed by skilled professionals. The versatility of Heat Resistant Bricks allows for their utilization in various construction applications, including commercial buildings, industrial facilities, and residential complexes.
The introduction of Heat Resistant Bricks by XYZ Company has already garnered attention and positive feedback from industry experts. Construction professionals appreciate the unmatched fire resistance offered by these bricks, as well as the substantial benefits they bring to both safety and sustainability. With this innovative solution now available, building fires may become less catastrophic events, saving lives and minimizing property damage.
As the demand for fire-resistant materials continues to rise, XYZ Company is committed to meeting the industry's evolving needs. By constantly exploring new technologies and refining their product line, they aim to further innovate and improve fire protection in the construction industry.
In conclusion, the release of Heat Resistant Bricks marks a significant milestone in the realm of fire protection. XYZ Company's groundbreaking product has the potential to redefine safety standards in construction and serve as a beacon of hope for firefighters, builders, and property owners alike. With their exceptional heat resistance, durability, and commitment to sustainability, Heat Resistant Bricks are set to play a vital role in creating safer and more resilient structures in the future.
Company News & Blog
Discover the Value of High-Quality Alumina Refractory Bricks: A Complete Guide
High-Quality Alumina Refractory Bricks Revolutionize the Construction IndustryThe construction industry is constantly evolving to meet the needs of modern society, and one crucial aspect of ensuring the longevity and safety of structures is the use of high-quality building materials. Alumina refractory bricks have emerged as a game-changer in this field, offering exceptional reliability and durability. This article will delve into the remarkable properties of these bricks and explore why they have become synonymous with excellence in the construction industry.{Company Introduction}In recent years, construction companies worldwide have recognized the importance of using high-quality materials to ensure the safety and stability of buildings. Alumina refractory bricks have quickly become the preferred choice for many construction projects due to their ability to withstand high temperatures and resist corrosion. With their exceptional mechanical strength and insulation properties, these bricks have transformed the way buildings are constructed.One of the key factors contributing to the success of alumina refractory bricks is their composition. These bricks are primarily made of alumina, a mineral known for its remarkable heat resistance. Alumina is combined with other additives and undergoes a precise manufacturing process to create bricks that are exceptionally strong and versatile. The precise composition of alumina refractory bricks allows them to resist the corrosive effects of acids, gases, and high temperatures, ensuring the longevity of structures even in the harshest environments.The superior durability of alumina refractory bricks makes them the ideal choice for a wide range of applications. These bricks are commonly used in industries such as steelmaking, cement manufacturing, and glass production, where high temperatures are prevalent. Their excellent thermal insulation properties minimize heat loss, improving energy efficiency and reducing operational costs.Additionally, the use of alumina refractory bricks enhances the safety of structures. Their ability to withstand extreme temperatures without deformation or crumbling ensures the integrity of buildings, particularly in areas prone to fires or explosions. The exceptional thermal shock resistance of these bricks prevents cracks or fractures when exposed to rapid temperature changes, further enhancing their reliability and safety.Moreover, the versatility of alumina refractory bricks allows architects and engineers to unleash their creativity. With these bricks, complex architectural designs and innovative construction techniques can be realized without compromising the structural integrity of the building. The ability of these bricks to conform to various shapes and sizes makes them an indispensable tool in the hands of construction professionals.{Company Name}, a renowned manufacturer of alumina refractory bricks, has been at the forefront of revolutionizing the construction industry. With over {X} years of experience, they have established themselves as a trusted provider of high-quality building materials. Their commitment to innovation and continuous improvement ensures that their customers have access to the most advanced alumina refractory bricks on the market.{Company Name} prides itself on its state-of-the-art manufacturing facilities, where cutting-edge technology is employed to produce alumina refractory bricks of unmatched quality. These bricks undergo stringent quality control measures to guarantee their reliability and durability. The company also boasts a team of highly skilled technicians and engineers who work tirelessly to develop new formulations and designs, pushing the boundaries of the industry.In conclusion, high-quality alumina refractory bricks have revolutionized the construction industry by offering exceptional durability, reliability, and versatility. Their ability to withstand high temperatures, resist corrosion, and provide excellent thermal insulation has made them the material of choice for numerous construction projects worldwide. Companies like {Company Name} have played a crucial role in advancing the field by manufacturing top-tier alumina refractory bricks. As the construction industry continues to evolve, these bricks will undoubtedly remain an essential component, ensuring the safety and longevity of buildings for generations to come.
Exceptional Quality Magnesia Carbon Brick for a Better Ladle Performance
Magnesia Carbon Brick for Ladle: A Revolutionary Solution for High-Temperature ApplicationsIn the ever-evolving field of refractories, a remarkable development has taken place with the introduction of Magnesia Carbon Brick for Ladle. This groundbreaking product has emerged as a game-changer in high-temperature applications, offering unparalleled performance and durability. With its unique composition and superior properties, this advanced refractory material ensures optimal performance in various industrial processes.Before delving into the specifics of this groundbreaking innovation, let us acquaint ourselves with the company behind this remarkable product. Founded several decades ago, this refractory manufacturer has been at the forefront of delivering cutting-edge solutions to industries worldwide. Known for their commitment to research and development, the company has garnered a reputation for producing best-in-class materials that cater to the most demanding customer requirements.Magnesia Carbon Brick for Ladle, the latest addition to their extensive product portfolio, is engineered to withstand extreme conditions encountered in ladle applications. Ladles are indispensable tools in the steel and metallurgy industries, used for transporting and pouring molten metal. Given the harsh and corrosive nature of these processes, the linings of ladles are subjected to extreme temperatures, chemical reactions, and mechanical stress.Traditionally, bricks made of magnesia and carbon have been used in ladle linings due to their excellent resistance to high temperatures. However, these conventional bricks have limitations such as high oxidation rates, poor thermal shock resistance, and susceptibility to carbon pickup. Recognizing the need for a more robust and reliable solution, our innovators have developed the Magnesia Carbon Brick for Ladle.This advanced refractory material features a unique combination of magnesia, graphite, and various additives, resulting in a high-performance composite with exceptional properties. The addition of graphite enhances the material's thermal shock resistance and provides increased resistance to slag penetration, while the carefully selected additives improve the overall mechanical strength and oxidation resistance.The Magnesia Carbon Brick for Ladle offers several notable advantages over its predecessors. The improved oxidation resistance significantly extends the service life of the lining, reducing downtime and maintenance costs. Moreover, the enhanced thermal shock resistance ensures reliable performance even in rapid temperature fluctuations, minimizing the risk of premature failure.Another key aspect of this revolutionary product is its excellent resistance to carbon pickup. Carbon pickup refers to the absorption of carbon by molten metal, resulting in the formation of carbides and compromising the quality of the final product. By mitigating this issue, the Magnesia Carbon Brick for Ladle ensures the production of high-quality steel with consistent properties.Furthermore, this magnesia carbon brick offers superior corrosion resistance to chemical attacks from molten metals and slags. This resistance is crucial for maintaining the integrity of the ladle lining, preventing leaks or contamination that could impact the overall process efficiency and product quality.Considering the widespread applications of ladles in the steel and metallurgy industries, the adoption of Magnesia Carbon Brick for Ladle is expected to have a significant impact. The extended service life and enhanced performance of this refractory material will help manufacturers optimize their processes, reduce production costs, and improve overall productivity.In conclusion, the introduction of Magnesia Carbon Brick for Ladle marks a significant advancement in the field of refractories. With its remarkable properties and exceptional performance, this innovative product ensures optimal performance in high-temperature applications, such as ladle linings. Developed by a renowned refractory manufacturer, this advanced material underscores their commitment to delivering cutting-edge solutions that meet the evolving needs of industries worldwide. As its adoption grows, this revolutionary brick holds the promise of revolutionizing ladle applications and contributing to the growth and efficiency of various industrial processes.
Top-Quality High Liquidity Refractory Castable: Boost Your Project's Performance
Title: Pioneer Company Unveils High Liquidity Refractory Castable for Enhanced Industrial ApplicationsIntroduction (86 words):In a groundbreaking development, a renowned industry-leading company has introduced an innovative and powerful product to the market – High Liquidity Refractory Castable. Engineered with advanced technology and precision, this next-generation castable material is set to revolutionize industrial applications in various sectors. With its exceptional liquidity and superior performance characteristics, it promises to offer enhanced efficiency, durability, and cost-effectiveness solutions to industries across the globe.Paragraph 1 (115 words):High Liquidity Refractory Castable, developed by an industry pioneer, brings cutting-edge advancements to the field of refractory materials. Designed to withstand high temperatures and resist thermal shocks, this specialized castable constitutes a carefully formulated blend of high-quality raw materials. Its unique composition enables the castable to maintain its original fluidity for an extended period while exhibiting excellent flow and spreading properties. Due to its exceptional liquidity, it allows for easy installation and precise casting even in complex shapes, giving industries greater flexibility. Additionally, this castable offers exceptional mechanical strength, resistance to corrosion, and long-lasting thermal insulation, making it a highly sought-after solution for various demanding industrial applications.Paragraph 2 (110 words):The company responsible for this groundbreaking product has garnered significant global recognition for its expertise and commitment to innovation in the refractory industry. With over two decades of experience, they have become a trusted name, offering specialized solutions tailored to the diverse needs of different sectors. Their in-depth research and development efforts have led to the creation of High Liquidity Refractory Castable, further cementing their status as an industry leader. The company's team of highly skilled professionals and state-of-the-art manufacturing facilities ensure stringent quality control measures throughout the production process, resulting in a product that sets new standards for performance and reliability.Paragraph 3 (146 words):One of the distinguishing features of the High Liquidity Refractory Castable is its exceptional heat resistance capabilities, making it an ideal choice for high-temperature applications found in industries such as steel, ceramics, cement, and petrochemicals. This castable material offers outstanding thermal insulation, with low thermal conductivity that helps conserve energy and reduce operational costs. It also boasts impressive chemical resistance, ensuring durability even when exposed to aggressive environments or corrosive materials. Industries utilizing this castable can benefit from lower maintenance requirements, reduced downtime, and increased operational efficiency, ultimately contributing to long-term cost savings.Paragraph 4 (172 words):Moreover, High Liquidity Refractory Castable showcases remarkable adaptability, providing unparalleled design freedom to engineers and manufacturers. Its fluidity allows for precise casting into intricate shapes, resulting in reduced material wastage and labor costs. The castable's consistent setting time ensures quick and efficient installation, enabling industries to save valuable time during the production process. Its increased workability and ease of application make it an ideal solution for both repair and new construction projects. Whether for lining furnaces, kilns, incinerators, or any other high-temperature equipment, this castable stands out as a reliable, efficient, and versatile option.Conclusion (79 words):As the refractory industry continues to evolve, the introduction of High Liquidity Refractory Castable marks a significant milestone. With its advanced properties, impressive fluidity, and outstanding performance, this innovative product is poised to transform industrial applications across multiple sectors. Engineered by a trusted pioneer in the field, this castable material not only offers durability and enhanced thermal insulation but also provides industries with unparalleled design freedom and cost-effectiveness. As companies strive to optimize efficiency and productivity, this game-changing castable serves as a beacon of progress, paving the way for a new era in refractory engineering.
Experiencing the Benefits of Alkali Resistant Bricks: Strong and Durable Solution for Industrial Needs
[Publication Name][Date]Alkali Resistant Bricks: An Innovative Solution for High Durability Construction[City], [State] - In a constant endeavor to offer cutting-edge solutions to the construction industry, [Company Name] has launched its new line of Alkali Resistant Bricks. These bricks, specially formulated with advanced technology, boast unparalleled durability and resistance against alkali attacks. With this latest addition to their extensive product portfolio, [Company Name] reinforces its commitment to providing high-quality construction materials to cater to diverse project requirements.The high durability of Alkali Resistant Bricks makes them ideally suited for construction projects where exposure to alkalis is a concern. The advanced formulation ensures these bricks can withstand the corrosive effects that arise from the presence of alkalis in construction materials or the surrounding environment. This exceptional resistance makes Alkali Resistant Bricks an essential choice for applications such as chimneys, incinerators, kilns, and foundations in areas with high alkali content."The launch of our Alkali Resistant Bricks is a significant milestone for us. We firmly believe that this new product will revolutionize the construction industry, offering our clients a reliable solution that can withstand challenging environments," said [Spokesperson Name], spokesperson for [Company Name]. "Our team of experts conducted extensive research and development to ensure that these bricks not only possess exceptional resistance to alkali attacks but also meet the highest standards in terms of durability and reliability."Uniquely designed to resist alkalis, these bricks provide a long-lasting solution for high-alkali environments without compromising on quality or performance. They are manufactured using premium raw materials, carefully selected for their alkali-resistant properties, and go through a rigorous quality control process to ensure consistent, reliable, and defect-free products.Furthermore, Alkali Resistant Bricks offer excellent thermal shock resistance, maintaining structural integrity even in environments with extreme temperature variations. This feature makes them suitable for applications subjected to rapid heating and cooling cycles.The impact of alkali attacks on construction materials is a significant concern for engineers and builders alike. Alkalis, commonly present in cement and other building materials, react with certain minerals in bricks, causing them to degrade over time. This degradation not only weakens the structural integrity of the construction but also affects its aesthetics. The use of Alkali Resistant Bricks addresses these concerns and eliminates the need for frequent repairs or replacements, saving both time and money.As a leader in the construction industry, [Company Name] is dedicated to continuously expanding its product range to meet evolving market demands. Through extensive research and innovation, the company has earned a reputable track record of delivering premium construction materials backed by comprehensive technical support. With the introduction of Alkali Resistant Bricks, [Company Name] aims to set a new industry benchmark while solidifying its position as a reliable partner for construction projects of all scales and complexities.About [Company Name]:[Company Name], a renowned name in the construction sector, has been providing innovative solutions to the industry for over [number] years. With a focus on excellence and sustainability, the company offers a wide range of construction materials, including bricks, cement, concrete additives, and more. [Company Name] collaborates with architects, engineers, and contractors to meet their specific project needs, ensuring high-quality and reliable solutions that stand the test of time.For media inquiries, please contact:[Contact Name][Position][Company Name][Phone][Email]Disclaimer: This press release is for informational purposes only. The content does not constitute investment advice or an endorsement of any product, service, or brand. Readers are encouraged to carry out their own research and seek professional advice before making any investment decisions.
All You Need to Know About Monolithic Castable Refractory for High-Temperature Applications
Monolithic Castable Refractory – Revolutionizing the Refractory IndustryIn the world of heavy industries, refractories play a significant role in ensuring the longevity of high-temperature equipment. Refractories are inorganic, non-metallic materials that can withstand extreme temperatures and harsh environments. They are used as insulators for furnaces, kilns, incinerators, and reactors. Refractories are also used as lining materials in industries such as cement, steel, aluminum, and petrochemical.However, traditional refractory materials such as bricks, tiles, and precast shapes have certain limitations. These materials are time-consuming and require skilled labor for installation. They also have low thermal shock resistance and exhibit cracking, spalling, and erosion after a short period. This leads to frequent maintenance, downtime, and loss of productivity.To overcome these challenges, manufacturers have developed new types of refractory materials, including monolithic castable refractory. This is a revolutionary material that has completely transformed the refractory industry. In this news article, we will explore the benefits and advancements of this innovative material and its impact on various industries.What is Monolithic Castable Refractory?Monolithic castable refractory is a type of refractory material that is made by combining various raw materials such as fine grain, coarse grain, bonding agents, and additives. The mixture is then placed into a mold or sprayed onto a surface. It hardens when exposed to high temperatures and forms a monolithic, seamless structure. The term “monolithic” refers to the fact that it is a single piece, as opposed to traditional refractory materials that are made of multiple pieces.This type of refractory material offers numerous advantages over traditional materials. They include:Less Labor Intensive – Monolithic castables are easier to install compared to traditional materials. They can be poured, sprayed or troweled into place, reducing the need for skilled labor. This significantly lowers the cost of installation and maintenance.Better Insulation Properties - Monolithic castables offer better insulation than traditional materials. This is because they have fewer joints and cracks, which reduce heat loss. This translates to lower energy costs and improved thermal efficiency.Higher Thermal Shock Resistance – Monolithic castables have high thermal shock resistance, which means that they can withstand rapid temperature changes without cracking or spalling. This prolongs the lifespan of the material, reduces maintenance costs and minimizes downtime.Wide Range of Applications – Monolithic castables have a wide range of applications in various industries. They are used as linings in furnaces, kilns, incinerators, and reactors. They are also used as insulating materials for pipes, ducts, boilers, chimneys, and stacks. Their versatility makes them suitable for a broad range of applications.Company Introduction{Remove Brand Name} is a leading global manufacturer of monolithic castable refractory materials. The company was founded over 70 years ago and has since then grown into a global leader in the refractories industry. {Remove Brand Name} offers a wide range of refractory solutions to various industries, including steel, cement, power generation, petrochemical, and aluminum.{Remove Brand Name} has a team of experienced scientists and engineers who are dedicated to developing innovative, high-quality products that meet the needs of their clients. They use state-of-the-art manufacturing processes and equipment to ensure that their products are of the highest quality.{Remove Brand Name} has a strong commitment to sustainable practices, which is reflected in their use of eco-friendly, sustainable raw materials, and their focus on reducing waste and emissions. They work closely with clients to identify their needs and provide customized solutions that meet their specific requirements.Recent DevelopmentsIn recent years, {Remove Brand Name} has made significant advancements in the development of monolithic castable refractory materials. They have developed new products that offer even better thermal performance, insulation, and durability.One of their recent innovations is the use of advanced nanotechnology in their refractory materials. This technology involves the use of nanoparticles that are dispersed throughout the material. The nanoparticles enhance the material's thermal properties, such as thermal conductivity, radiation absorption, and insulation. This results in better thermal efficiency, reduced energy costs, and improved overall performance.{Remove Brand Name} has also developed new manufacturing processes that reduce the environmental impact of their products. They use renewable, eco-friendly raw materials, and reduce waste and emissions during the manufacturing process. This ensures that their products are both high-quality and sustainable.ConclusionIn conclusion, monolithic castable refractory materials have revolutionized the refractory industry. They offer numerous advantages over traditional materials, such as reduced labor costs, better insulation, and higher thermal shock resistance. {Remove Brand Name} is a leading manufacturer of high-quality monolithic castable refractory materials. They have made significant advancements in the development of new products that offer even better thermal performance and durability. With their strong commitment to sustainable practices and client-focused approach, {Remove Brand Name} is poised to continue leading the way in the refractory industry.
Understanding the Importance of Electric Arc Furnace Electrodes for Steel Manufacturing
Electric Arc Furnace Electrodes: Innovating the Steel Production ProcessSteel production is a crucial aspect of various industries, ranging from construction to automotive manufacturing. With the increasing demand for steel products, the need for more efficient and sustainable production methods has become paramount. One of the key elements in the steelmaking process is the electric arc furnace (EAF), and the electrodes used within it play a critical role in ensuring a smooth operation. In this article, we will explore the advancements in electric arc furnace electrodes, highlighting their importance in the steel production industry.Electric arc furnace electrodes serve as conductors of electricity, enabling the melting of scrap metal and other raw materials in the EAF. Traditionally, carbon electrodes have been widely used due to their low cost and ability to withstand extreme temperatures. However, their usage often leads to high levels of greenhouse gas emissions, making them less environmentally friendly. In recent years, manufacturers have been striving to develop alternative electrode materials that not only improve overall performance but also minimize the environmental impact.One such innovative company in this field is {}, a leading provider of cutting-edge solutions for the steel industry. With a commitment to sustainability and technological advancements, they have introduced a range of breakthrough electrode products that are revolutionizing the steel production process. By combining their expertise in materials science and engineering, they have developed electrodes that offer numerous benefits compared to traditional carbon electrodes.One of the key advantages of these new electrodes is their improved energy efficiency. By utilizing advanced materials with enhanced electrical conductivity, they enable a more efficient transfer of electricity, resulting in reduced energy consumption during the steelmaking process. This not only helps in conserving valuable resources but also lowers production costs for steel manufacturers.Moreover, these innovative electrodes contribute to minimizing environmental pollution. The traditional carbon electrodes are known to release significant amounts of greenhouse gases, such as carbon dioxide (CO2), during the steelmaking process. In contrast, the new electrodes developed by {} emit much lower levels of CO2, thereby reducing the carbon footprint of steel production. This aligns with the global efforts to combat climate change and promote sustainable practices in industrial processes.In addition, the advanced electrode materials offer improved durability and longer service life. This reduces the frequency of electrode replacements, leading to cost savings for steel manufacturers. The electrodes are designed to withstand high temperatures and harsh operating conditions, ensuring a stable and uninterrupted steelmaking process.Furthermore, through extensive research and development, {} has introduced electrodes with enhanced slag resistance. Slag, a byproduct of the steelmaking process, can cause significant operational challenges and decrease overall efficiency. The new electrodes effectively mitigate these issues, allowing for smoother and more productive steel production.The introduction of these groundbreaking electrode solutions by {} has garnered widespread attention across the steel industry. Many manufacturers have already implemented these innovative products in their electric arc furnaces, experiencing notable improvements in both production efficiency and environmental performance.Looking ahead, the continuous development and adoption of advanced electrode technologies hold significant promise for the steel production industry. As the demand for steel continues to rise, manufacturers will increasingly rely on these innovative solutions to meet their production targets while minimizing their environmental impact.In conclusion, electric arc furnace electrodes play a crucial role in the steel production process, and recent advancements in this field are achieving remarkable results. Through the introduction of innovative electrode materials, companies like {} are revolutionizing the way steel is produced, offering improved energy efficiency, reduced environmental impact, enhanced durability, and increased operational efficiency. As the steel industry evolves and strives for sustainability, these advancements will play a pivotal role in shaping its future.
Ultimate Guide to Choosing and Installing Quality Thermal Insulation Bricks" becomes "The Comprehensive Guide to Selecting and Installing Thermal Insulation Bricks
Title: Innovation in Thermal Insulation Bricks Revolutionizes Energy Efficiency in ConstructionIntroduction:In a bid to address the rising concerns about energy consumption and environmental sustainability in the construction industry, {Company Name}, a pioneer in the field of thermal insulation solutions, has unveiled a groundbreaking product. The company's advanced Thermal Insulation Bricks promise to revolutionize and enhance energy efficiency in buildings while also reducing carbon footprint. With their affordable price and superior insulating properties, these cutting-edge bricks are set to transform the way construction projects are executed.Efficient insulation technology:Thermal insulation plays a crucial role in improving energy performance in buildings, preventing unnecessary heat transfer, and reducing the reliance on artificial cooling and heating systems. Traditionally, insulation materials such as fiberglass and mineral wool have been utilized. However, {Company Name}'s innovative Thermal Insulation Bricks offer significant improvements in terms of efficiency and overall performance.The secret lies in the composition of these bricks, which consist of a unique combination of lightweight minerals, binders, and additives. This blend is formulated to create a low-density structure that minimizes heat conduction and ensures optimal thermal insulation. The bricks possess exceptional insulating properties, thus significantly reducing the transfer of heat, resulting in improved energy efficiency.Energy savings and environmental benefits:By integrating {Company Name}'s Thermal Insulation Bricks into construction projects, builders can achieve substantial energy savings. The impressive insulating capabilities of these bricks help maintain a stable indoor temperature, minimizing the need for energy-intensive heating or cooling systems throughout the year. As a result, households and commercial spaces alike can experience reduced energy consumption and lower utility bills.Moreover, the reduced energy requirements translate into a decrease in carbon emissions. By limiting the reliance on non-renewable energy sources, {Company Name}'s Thermal Insulation Bricks contribute to a greener and more sustainable future for the construction industry. This revolutionary product aligns with current global initiatives to combat climate change and promotes the use of eco-friendly building materials.Versatile applications and adaptability:One of the notable advantages of {Company Name}'s Thermal Insulation Bricks is their versatility in various construction applications. Whether used for external or internal building walls, partition walls, or even roofing structures, these bricks provide exceptional insulation in any scenario. Their lightweight nature simplifies handling and installation, making them a preferred choice for both large-scale commercial projects and smaller residential buildings.Furthermore, the bricks can be easily integrated into existing construction practices without significant modifications, reducing costs and time associated with adopting new technologies. The adaptability of these bricks ensures that builders and contractors can seamlessly incorporate them into ongoing or upcoming construction projects, making energy-efficient establishments more accessible and feasible.Industry recognition and future developments:{Company Name}'s Thermal Insulation Bricks have generated considerable interest within the construction industry, earning recognition for their innovative approach to enhancing energy efficiency. Architects, engineers, and contractors are eager to incorporate this sustainable solution into their projects, accelerating the adoption of greener building practices.Following the success of their current lineup, {Company Name} envisions continuous research and development efforts to further improve their Thermal Insulation Bricks. The company aims to enhance the already remarkable insulating properties, explore new applications, and ensure their products remain at the forefront of energy-efficient building materials.Conclusion:{Company Name}'s introduction of their state-of-the-art Thermal Insulation Bricks signifies a significant leap towards achieving energy-efficient and sustainable buildings. These bricks provide outstanding thermal insulation capabilities, resulting in reduced energy consumption, lower utility costs, and a reduced carbon footprint. With their versatility and ease of integration, these bricks are set to revolutionize the construction industry, enabling the creation of environmentally conscious structures. As the demand for eco-friendly building practices continues to grow, {Company Name} is well-positioned to play a leading role in shaping the future of energy-efficient construction.
Shop High-Quality Castable Refractory for Your Industrial Needs
Castable refractory is a crucial component in a wide range of industries, including steel manufacturing, cement production, and even petrochemical processing. This versatile material is used to line various types of furnaces, incinerators, and kilns, with its primary purpose being to withstand high temperatures and prevent contaminants from infiltrating the surrounding environment. With castable refractory being such an essential product for many businesses, finding a reliable supplier is crucial for ensuring smooth and trouble-free operations.If you are in the market for high-quality, durable castable refractory, {company name} is an industry-leading supplier that can meet all of your needs. With a reputation built on quality, reliability, and customer satisfaction, they are the go-to choice for discerning businesses that demand the best.{Company name} has been in the castable refractory business for over {number of years} years, during which they have honed their craft and built a solid reputation for excellence. Their products are made from the finest materials and are crafted using advanced manufacturing techniques, resulting in an end product that is highly resistant to wear and tear, corrosion, and thermal shock.Whether you need castable refractory for a large-scale industrial application or a smaller project, {company name} has a wide range of products to choose from. Their vast inventory includes high-temperature insulating materials, dense refractory castables, and low-cement castables, to name just a few. They pride themselves on being able to provide customized solutions to meet their clients' specific needs, and their team of experts is always on hand to provide advice and technical support.But {company name} isn't just about supplying top-quality castable refractory. They are also committed to providing exceptional customer service and support. Their knowledgeable staff is always ready to answer any questions or concerns you may have, and they work closely with clients to ensure that their products are delivered on time and within budget. With {company name}, you can be confident that you are dealing with a reputable, trustworthy company that puts your needs first.Furthermore, {company name} is committed to sustainability and reducing its environmental footprint. They use innovative manufacturing techniques and employ a closed-loop system that recycles waste materials, minimizing their impact on the environment. By choosing {company name} as your supplier, you can be confident that you are working with a company that cares about the environment and is doing its part to protect our planet.In conclusion, castable refractory is an essential component in many industrial processes, and selecting a reliable supplier is crucial for ensuring smooth and trouble-free operations. With over {number of years} years of experience in the industry, a commitment to quality and sustainability, and unparalleled customer service, {company name} is the go-to choice for businesses that demand the best. Contact them today to see how they can meet your castable refractory needs.
Discover Effective Tips for Preserving Refractory Cement and Extending Its Lifespan
Saving Refractory Cement Revolutionizes the Construction IndustryWhen it comes to construction materials, durability and reliability are two crucial factors that determine the longevity of a structure. Over the years, numerous innovations have been introduced to improve the quality and performance of building materials. However, one company has taken it a step further by developing a game-changing product that has revolutionized the construction industry - Saving Refractory Cement.Saving Refractory Cement, developed by a leading company in the field, is a high-quality refractory material specifically designed to withstand extreme temperatures and withstand the test of time. With its exceptional properties, this innovative cement has become a go-to choice for construction professionals worldwide.With a focus on sustainability and environmental consciousness, the manufacturers of Saving Refractory Cement have devised a unique formula that significantly reduces carbon emissions during the production process. This makes it an ideal choice for companies and individuals striving to make environmentally responsible construction choices.The exceptional performance of Saving Refractory Cement lies in its high resistance to thermal shock, excellent strength, and exceptional chemical resistance. These properties make it suitable for a wide range of applications, from lining furnaces and kilns to industrial boilers and chimneys. Its ability to withstand extreme temperatures makes it invaluable in industries where high heat is a daily occurrence.Unlike traditional refractory cement, Saving Refractory Cement requires less maintenance and repair. Its longevity ensures that structures built with this innovative material remain intact for years, reducing the need for constant upkeep, and saving businesses both time and money. The durability of Saving Refractory Cement not only enhances the safety of structures but also increases their lifespan, making it a cost-effective choice for all construction projects.Furthermore, the ease of application of Saving Refractory Cement has captivated contractors and builders alike. Its high workability allows for efficient and quick installation, reducing labor costs significantly. Additionally, its versatility enables it to be used in various construction scenarios, further adding to its appeal.The success and popularity of Saving Refractory Cement have made it an essential material in numerous industries, including steel production, glass manufacturing, and power generation. Its ability to withstand extreme temperatures makes it indispensable in these sectors, where maintaining high heat resistance is paramount.In addition to its exceptional properties, Saving Refractory Cement has gained a strong reputation for its commitment to customer satisfaction. The company behind this revolutionary cement provides comprehensive technical support, ensuring that clients receive expert advice on its installation and maintenance. This commitment to excellence has fostered strong relationships with contractors, leading to repeat business and a loyal customer base.As the construction industry continues to evolve, innovation in building materials remains a driving force. Saving Refractory Cement has emerged as a front-runner in this regard, revolutionizing the way structures are built and providing a sustainable and durable solution for construction needs.In conclusion, Saving Refractory Cement has transformed the construction industry with its exceptional properties, environmental consciousness, and commitment to customer satisfaction. Its ability to withstand extreme temperatures, reduced carbon emissions, and ease of application have made it a top choice for construction professionals worldwide. Furthermore, its longevity and cost-effectiveness make it an ideal option for businesses looking to create sustainable structures. With its revolutionary approach, Saving Refractory Cement is undoubtedly reshaping the future of the construction industry.
Unlocking the Potential of Low Cement Castable Refractory Material: A Game-Changer for Industrial Applications
Low Cement Castable Refractory Material: The Newest Addition to {Company Name}'s Product Line{Company Name}, a leading manufacturer of refractory materials, has recently introduced their latest product, the Low Cement Castable Refractory Material. This latest addition to their lineup of innovative products is designed to provide high-quality insulation solutions for a wide range of applications.The Low Cement Castable Refractory Material is a specially formulated and precisely engineered product that is ideal for use in high-temperature environments such as kilns, furnaces, and incinerators. It is created using a unique combination of raw materials that are carefully selected to provide optimum performance, durability, and resistance to extreme temperatures.This innovative product is designed to offer superior insulation performance in comparison to traditional materials. Its low cement content and unique composition result in a product that is highly resistant to thermal shock, chemical attack, and abrasion. It also provides excellent strength and durability, ensuring a long-lasting solution for industrial processes and applications.{Company Name} has built a reputation for delivering high-quality products, and their latest release is no exception. The Low Cement Castable Refractory Material is manufactured using advanced technology and stringent quality control processes, ensuring that it meets the highest standards of performance and reliability.The Low Cement Castable Refractory Material boasts numerous benefits that make it an attractive option for use in a wide range of applications. It provides exceptional thermal insulation, significantly reducing energy consumption and heat loss. Its high strength and abrasion resistance make it suitable for use in environments that involve wear and tear, such as the mining, cement, and steel industries.In addition to its superior performance, the Low Cement Castable Refractory Material is also incredibly versatile, making it suitable for a variety of industrial applications. These include boilers, incinerators, kilns, and furnaces, among others. Its outstanding insulating properties also make it a popular choice for use in high-temperature applications such as metal melting, heat treatment, and forging processes.{Company Name} has always been at the forefront of innovation when it comes to refractory materials. Their latest product, the Low Cement Castable Refractory Material, is a testament to their commitment to delivering the highest standards of quality and reliability to their customers.In conclusion, the introduction of the Low Cement Castable Refractory Material by {Company Name} is a significant development in the field of refractory materials. Its superior performance, strength, and durability make it an excellent choice for use in a wide range of industrial applications. Its versatility also ensures that it can be used for various processes, making it an invaluable asset for businesses in different industries. As a leading manufacturer in the field of refractory materials, {Company Name} has once again demonstrated their commitment to providing high-quality solutions that meet the needs of their customers.