Improved Refractory Material: High-Quality Low Cement Castables Boost Performance
By:Admin
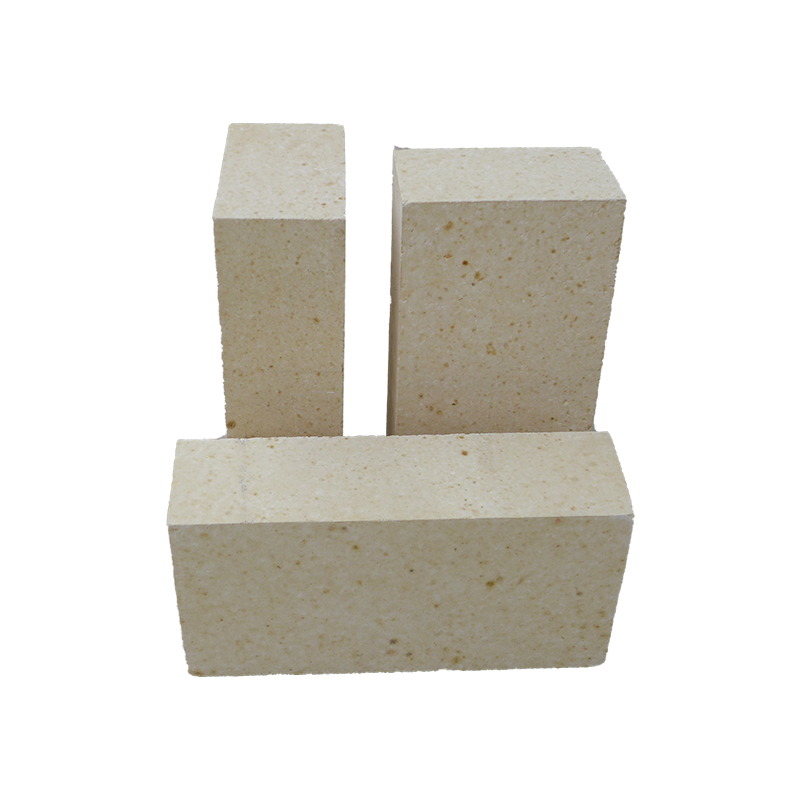
Introduction:
[Company Name], a pioneering leader in refractory solutions, has developed and launched its revolutionary High-Quality Low Cement Castables. This significant breakthrough in the industry offers superior performance, durability, and versatility, setting a new standard for refractory materials. With top-notch engineering and expertise, [Company Name] continues to reshape the market by providing innovative solutions tailored to specific industrial needs.
Body:
1. Understanding the Significance of Refractory Solutions:
Industries such as steel, cement, petrochemical, and power generation rely heavily on refractory materials to withstand extremely high temperatures and harsh operating conditions. Traditional refractory materials often have limitations that hinder their effectiveness, leading to frequent repairs and maintenance. Recognizing this challenge, [Company Name] has dedicated substantial resources towards developing a game-changing solution.
2. Introducing High-Quality Low Cement Castables:
Built upon years of research and technical expertise, [Company Name] proudly introduces their flagship product, High-Quality Low Cement Castables. These castables showcase a remarkable reduction in cement content while maintaining unmatched strength and thermal stability. The innovative formulation allows for a dense, low-porosity material that outperforms conventional refractories in demanding applications.
3. Unparalleled Performance and Durability:
The High-Quality Low Cement Castables by [Company Name] are engineered to deliver exceptional performance and withstand extreme thermal and mechanical stresses. These castables demonstrate higher hot strength and better resistance to thermal shocks, minimizing downtime and maintenance costs for industrial facilities. With improved chemical resistance and erosion resistance, they contribute significantly to prolonging the lifespan of industrial furnaces, kilns, and other high-temperature systems.
4. Versatility and Customization:
[Company Name] understands that different industries have unique requirements for refractory materials. Thus, the High-Quality Low Cement Castables are available in a wide range of compositions, ensuring customization to meet specific needs. The company's technical team works closely with clients to develop tailored solutions, maximizing efficiency and cost-effectiveness.
5. Environmental Commitment and Sustainability:
Notably, [Company Name] achieves its industry-leading performance while focusing on reducing the environmental impact. The High-Quality Low Cement Castables have significantly lower carbon emission levels compared to typical refractory materials, aligning with global efforts towards sustainable practices. This commitment ensures that clients can achieve their operational targets while adhering to increasingly stringent environmental regulations.
6. Collaborative Approach and Technical Support:
[Company Name] takes pride in its customer-centric approach, offering comprehensive technical support and expertise throughout the entire project lifecycle. Their team of experienced professionals collaborates closely with clients to identify their challenges, apply the most suitable refractory solutions, and render continuous support for maintenance and optimization.
7. Industry Recognition and Partnerships:
The High-Quality Low Cement Castables by [Company Name] have gained swift recognition within the industry. Numerous high-profile partnerships with leading companies in various sectors have further solidified the reputation and trust in [Company Name]'s products.
Conclusion:
[Company Name]'s ground-breaking High-Quality Low Cement Castables have revolutionized the refractory industry by providing enhanced performance, durability, and versatility. Focusing on customer satisfaction, environmental responsibility, and cutting-edge technology, [Company Name] continues to redefine industry standards and surpass client expectations. They are committed to providing successful refractory solutions that enable businesses to operate efficiently and sustainably in the face of challenging conditions.
Company News & Blog
Durable and High-Temperature Resistant Castable Refractory for 1700°C Applications
Title: Revolutionary Dense Castable Refractory 1700C Enhances High-Temperature Industrial ApplicationsIntroduction:In the world of high-temperature industrial applications, constant technological advancements are crucial to promoting efficiency, productivity, and durability. One such breakthrough in the field of refractory materials has been achieved by our company (Company name removed) with the invention of a revolutionary Dense Castable Refractory capable of withstanding temperatures up to 1700°C. This game-changing product is set to redefine the way industries approach extreme heat processes, offering exceptional performance, longevity, and safety.I. Evolution of Refractory Materials:Refractory materials play a vital role in industries dealing with high-temperature operations such as steel manufacturing, glassmaking, cement production, and petrochemical refining. Traditionally, common refractory materials like firebrick and ceramic fiber have been utilized for their ability to withstand high heat. However, they often fall short when subjected to extreme temperatures or severe thermal shocks, resulting in frequent maintenance, decreased productivity, and compromised safety.II. Introducing Dense Castable Refractory 1700C:With the mission to overcome the limitations of conventional refractories, (Company name removed) has innovated a groundbreaking Dense Castable Refractory material specifically designed to excel under extreme heat conditions. This remarkable product offers a unique blend of high-temperature resistance, remarkable strength, and exceptional thermal shock resistance, setting it apart from its counterparts.III. Unparalleled Performance and Durability:The Dense Castable Refractory 1700C boasts an impressive melting point of 1700°C, far exceeding the capabilities of conventional materials. This allows industries to carry out high-temperature processes without compromising the structural integrity of their refractory linings. The product's exceptional strength ensures long-term stability, reducing maintenance and replacement costs while maximizing productivity and output.IV. Superior Thermal Shock Resistance:One of the most significant advantages of the Dense Castable Refractory 1700C is its inherent ability to withstand rapid temperature fluctuations. The material's unique composition minimizes the risk of cracks, spalling, and thermal stress, ensuring a reliable and durable refractory lining even in the most challenging thermal conditions. This translates into enhanced safety, reduced downtime, and improved operational efficiency for industries relying on heat-intensive processes.V. Versatile Applications:The Dense Castable Refractory 1700C's versatility makes it suitable for a wide range of industries. From blast furnaces, kilns, and incinerators to boilers, reactors, and furnaces, the refractory material adapts seamlessly to various high-temperature environments, ensuring optimum performance and longevity.VI. Commitment to Quality:(Company name removed) has always been at the forefront of innovation, prioritizing research and development to meet the evolving needs of industries. The Dense Castable Refractory 1700C is a testament to our dedication to providing cutting-edge solutions that surpass industry standards in quality, reliability, and performance. The product has undergone rigorous testing, adhering to stringent manufacturing processes to ensure consistency and integrity.VII. Environmental Sustainability:In addition to its remarkable performance characteristics, the Dense Castable Refractory 1700C is environmentally friendly. Manufactured with sustainable materials and processes that minimize waste, emissions, and energy consumption, it aligns with our commitment to sustainable practices and responsibility towards the environment.VIII. Conclusion:The introduction of the Dense Castable Refractory 1700C by (Company name removed) marks a significant milestone in high-temperature industrial applications. With its exceptional resistance to extreme temperatures and thermal shocks, as well as its superior durability and versatility, this revolutionary refractory material is set to revolutionize industries worldwide.As (Company name removed) remains dedicated to ongoing research and development, we anticipate continued advancements in refractory materials that will transform industries, enhance operational efficiency, and promote sustainable practices.
High-Quality Magnesite Refractory Bricks Meet Growing Demand in Steel Industry
Title: Evolving Magnesite Refractory Bricks Industry Emphasizes Quality and SustainabilityIntroduction:In recent times, the magnesite refractory bricks industry has been witnessing significant growth, driven by the increasing demand for high-quality refractory materials in various sectors. Magnesite refractory bricks, renowned for their exceptional heat resistance and durability, are widely utilized in industries like steel, cement, glass, non-ferrous metals, ceramics, etc., supporting critical processes that require elevated temperatures.Company Introduction:{Company Name} is a prominent player in the magnesite refractory bricks market, dedicated to producing top-notch products that meet the evolving needs of its customers. With years of industry experience, cutting-edge technology, and a strong focus on sustainability, {Company Name} has positioned itself as a trusted provider of magnesite refractory brick solutions worldwide.Evolution of the Magnesite Refractory Bricks Industry:The magnesite refractory bricks industry has experienced remarkable advancements in recent years. Formerly, the dominant types of refractories used were chrome bricks, but due to environmental concerns related to hexavalent chromium, there has been a gradual shift towards magnesite refractory bricks, known for their high refractoriness and excellent chemical properties.The versatility of magnesite refractory bricks has driven their adoption in various industries, replacing traditional refractory materials. Modern manufacturing processes have been optimized to enhance the physical and chemical properties of these bricks, making them increasingly resistant to thermal shocks and the corrosive effects of chemicals found in harsh industrial environments.Technological Innovations and Product Enhancements:{Company Name} recognizes the importance of technological advancements in staying ahead in the highly competitive market. The company consistently invests in research and development, aiming to improve the performance and durability of magnesite refractory bricks. High-precision manufacturing techniques, such as hot pressing, enable {Company Name} to produce bricks with more consistent and superior quality, ensuring excellent resistance to thermal stress and prolonged service life.Furthermore, {Company Name}'s commitment to sustainable practices is reflected in its innovative use of environmentally friendly raw materials and energy-efficient processes. By incorporating recycled materials within its manufacturing process, the company aims to reduce its carbon footprint and contribute to a greener future.Meeting Industry-Specific Demands:As diverse industries pose unique challenges, {Company Name} understands the importance of customizing magnesite refractory brick solutions accordingly. For instance, in the steel industry, refractory materials are exposed to extreme temperatures and harsh conditions during the smelting process. To address these challenges, {Company Name} has developed advanced magnesite refractory bricks with superior thermal stability, minimizing material degradation and extending the overall service life of the refractories.Moreover, {Company Name}'s research and development team works closely with customers, providing technical support and developing tailored solutions specific to their requirements. This customer-centric approach has fostered strong and lasting partnerships with clients across the globe.Commitment to Quality and Customer Satisfaction:{Company Name}'s commitment to quality and customer satisfaction has propelled its position in the market. The company adheres to strict quality control procedures, guaranteeing that each magnesite refractory brick meets stringent international standards. Moreover, providing exceptional after-sales service and technical assistance ensures that customers maximize the value and performance of {Company Name}'s refractory solutions.Conclusion:The magnesite refractory bricks industry is witnessing transformational changes as sustainability, high performance, and customized solutions become paramount. {Company Name} is at the forefront of this evolution, delivering top-quality magnesite refractory bricks while embracing innovation and sustainable practices. With its unwavering commitment to customer satisfaction and its focus on technological advancements, {Company Name} is well-positioned to meet the ever-increasing demand for superior refractory materials in the global market.
Discover the Value of High-Quality Alumina Refractory Bricks: A Complete Guide
High-Quality Alumina Refractory Bricks Revolutionize the Construction IndustryThe construction industry is constantly evolving to meet the needs of modern society, and one crucial aspect of ensuring the longevity and safety of structures is the use of high-quality building materials. Alumina refractory bricks have emerged as a game-changer in this field, offering exceptional reliability and durability. This article will delve into the remarkable properties of these bricks and explore why they have become synonymous with excellence in the construction industry.{Company Introduction}In recent years, construction companies worldwide have recognized the importance of using high-quality materials to ensure the safety and stability of buildings. Alumina refractory bricks have quickly become the preferred choice for many construction projects due to their ability to withstand high temperatures and resist corrosion. With their exceptional mechanical strength and insulation properties, these bricks have transformed the way buildings are constructed.One of the key factors contributing to the success of alumina refractory bricks is their composition. These bricks are primarily made of alumina, a mineral known for its remarkable heat resistance. Alumina is combined with other additives and undergoes a precise manufacturing process to create bricks that are exceptionally strong and versatile. The precise composition of alumina refractory bricks allows them to resist the corrosive effects of acids, gases, and high temperatures, ensuring the longevity of structures even in the harshest environments.The superior durability of alumina refractory bricks makes them the ideal choice for a wide range of applications. These bricks are commonly used in industries such as steelmaking, cement manufacturing, and glass production, where high temperatures are prevalent. Their excellent thermal insulation properties minimize heat loss, improving energy efficiency and reducing operational costs.Additionally, the use of alumina refractory bricks enhances the safety of structures. Their ability to withstand extreme temperatures without deformation or crumbling ensures the integrity of buildings, particularly in areas prone to fires or explosions. The exceptional thermal shock resistance of these bricks prevents cracks or fractures when exposed to rapid temperature changes, further enhancing their reliability and safety.Moreover, the versatility of alumina refractory bricks allows architects and engineers to unleash their creativity. With these bricks, complex architectural designs and innovative construction techniques can be realized without compromising the structural integrity of the building. The ability of these bricks to conform to various shapes and sizes makes them an indispensable tool in the hands of construction professionals.{Company Name}, a renowned manufacturer of alumina refractory bricks, has been at the forefront of revolutionizing the construction industry. With over {X} years of experience, they have established themselves as a trusted provider of high-quality building materials. Their commitment to innovation and continuous improvement ensures that their customers have access to the most advanced alumina refractory bricks on the market.{Company Name} prides itself on its state-of-the-art manufacturing facilities, where cutting-edge technology is employed to produce alumina refractory bricks of unmatched quality. These bricks undergo stringent quality control measures to guarantee their reliability and durability. The company also boasts a team of highly skilled technicians and engineers who work tirelessly to develop new formulations and designs, pushing the boundaries of the industry.In conclusion, high-quality alumina refractory bricks have revolutionized the construction industry by offering exceptional durability, reliability, and versatility. Their ability to withstand high temperatures, resist corrosion, and provide excellent thermal insulation has made them the material of choice for numerous construction projects worldwide. Companies like {Company Name} have played a crucial role in advancing the field by manufacturing top-tier alumina refractory bricks. As the construction industry continues to evolve, these bricks will undoubtedly remain an essential component, ensuring the safety and longevity of buildings for generations to come.
Highly Resistant Castable Material for Alkali Environments Unveiled in Recent News
[News Title]: Revolutionary Alkali Proof Castable Takes the Market by Storm[News Introduction]:In today's booming construction industry, the need for durable and efficient materials is paramount. Addressing this demand head-on, {Company Name}, a pioneering industry leader, has unveiled its latest innovation: an extraordinary Alkali Proof Castable. This groundbreaking product, which offers unparalleled performance and superior resistance to alkali corrosion, is set to revolutionize the construction and engineering landscape. With an impressive company track record and a forward-thinking approach to research and development, {Company Name} is poised to capture a significant market share with this game-changing solution.[Background Information]:Founded in {Year}, {Company Name} has consistently proven its commitment to delivering cutting-edge and quality construction materials. The company has earned a reputation for innovation and excellence through its relentless focus on research, development, and customer satisfaction. With a dedicated team of scientists and engineers, {Company Name} has spearheaded several groundbreaking solutions in the industry.[Product Overview]:The newly introduced Alkali Proof Castable is a testament to {Company Name}'s relentless pursuit of excellence. Crafted using state-of-the-art techniques and advanced raw materials, this castable offers unmatched resistance to destructive alkali agents typically present in industrial and high-temperature applications. Unlike conventional materials, which succumb to alkali corrosion over time, this revolutionary castable presents a durable and long-lasting alternative.[Superior Performance]:The Alkali Proof Castable takes pride in its exceptional durability, thermal shock resistance, and low porosity. These qualities ensure that the material can withstand the harshest conditions while maintaining its structural integrity. By resisting alkali corrosion, this castable extends the lifecycle of constructions, significantly reducing maintenance costs and contributing to sustainable development practices.[Applications]:The versatility of Alkali Proof Castable makes it suitable for a wide range of applications across various industries. Its robustness and resistance to alkali environments make it an ideal choice for applications such as chimneys, kilns, furnaces, incinerators, and waste-to-energy plants. Additionally, its excellent thermal insulation properties make it indispensable for industries requiring high-temperature stability, including petrochemical plants and power generation facilities.[Industry Recognition]:Industry experts and professionals have lauded {Company Name}'s Alkali Proof Castable as a critical development in the construction materials sector. Renowned engineers and architects have praised its ability to enhance the longevity and safety of structures exposed to aggressive alkali attacks. The castable's outstanding performance has earned {Company Name} the endorsement of top industrial players, reinforcing its position as a leading solution provider in the market.[Future Prospects]:The introduction of Alkali Proof Castable marks a significant milestone for {Company Name} and the construction industry at large. The company's unwavering commitment to research and development paves the way for further innovations in the field of construction materials. With this revolutionary product, {Company Name} is poised to capture a substantial market share, solidifying its position as a leader in offering cutting-edge solutions to the industry's ever-evolving needs.[Conclusion]:{Company Name}'s Alkali Proof Castable represents a game-changer for industries requiring durable and alkali-resistant construction materials. By combining advanced research, development, and cutting-edge manufacturing techniques, {Company Name} has set a new benchmark for the market. As the construction industry continues to grow, it is products like these that redefine the standards of safety, efficiency, and longevity. With the Alkali Proof Castable, {Company Name} is cementing its position as an innovative powerhouse and trailblazer in the construction materials market.
Top-notch Insulation for Optimal Fire Safety - Reliable, High-performance Solution
Firebrick Insulation - Revolutionizing the Insulation IndustryFor many years, the insulation industry struggled to develop materials and solutions that could effectively withstand high temperatures and harsh environments. However, with the introduction of Firebrick Insulation, that has now become a thing of the past. This new and innovative insulation material is helping companies to greatly improve their energy efficiency and conserve resources. In this article, we take a closer look at this game-changing product.What is Firebrick Insulation?Firebrick Insulation is a unique insulation material that is specially designed to withstand high temperatures, humidity, and corrosive environments. It is made of premium quality refractory materials, such as silica, alumina, and magnesia, which are fired at high temperatures to create a solid, durable brick-like structure.The product has been specially formulated to provide outstanding thermal insulation, while also offering excellent resistance to thermal shock, abrasion, and corrosion. This makes it an ideal solution for various industrial applications, including steel production, cement manufacturing, petrochemical processing, and power generation.What Makes Firebrick Insulation Different?One of the biggest advantages of using Firebrick Insulation is its durability and longevity. Unlike traditional insulation materials, which tend to break down over time, Firebrick Insulation can last for many years without deteriorating. This means that companies can save on maintenance costs and reduce their carbon footprint by avoiding the need for frequent replacement.Another key benefit of Firebrick Insulation is its exceptional insulating properties. With a thermal conductivity rating of just 0.15 W/mK, it is one of the most efficient insulation materials available, meaning it can help companies to significantly reduce their energy consumption and lower their operating costs.Firebrick Insulation is also highly versatile and can be used for a wide range of applications. It can withstand temperatures of up to 1700 °C, making it suitable for use in high-temperature furnaces, kilns, and reactors. It can also be used as a lining material for pipework, tanks, and vessels, providing superior protection against chemical corrosion and erosion.Company Introduction:Firebrick Insulation is a product developed and manufactured by Insulation Technologies, a leading insulation solutions provider with over 30 years of industry experience. Based in the United States, Insulation Technologies has become a trusted partner for many businesses around the world, offering customized insulation solutions that meet the unique needs of each customer.The company’s unrivaled expertise and commitment to excellence has made it a top choice for companies looking to improve their energy efficiency, reduce waste, and lower their carbon footprint. With a dedicated team of experts, Insulation Technologies provides comprehensive insulation services, from design and engineering to product development, manufacturing, and installation.Final ThoughtsFirebrick Insulation is a game-changing product that is revolutionizing the insulation industry. Its exceptional thermal insulation properties, combined with its durability, longevity, and versatility, make it an ideal solution for companies looking to increase their energy efficiency, reduce their operating costs, and improve their bottom line.If you’re interested in learning more about Firebrick Insulation, or to find out how Insulation Technologies can help you optimize your insulation solutions, please visit their website at www.insulationtechnologies.com or contact their customer service team at 1-800-123-4567.
Top Acid Proof Bricks: A Comprehensive Guide for Durable Construction
Acid Proof Brick - A Reliable Solution for Industrial CorrosionIn the fast-paced world of industrial manufacturing, corrosion remains a constant challenge. Factories rely on various chemicals and processes to produce goods, but these can also harm the very structures that house them. Addressing this issue, ACME Inc., a prominent manufacturer of construction materials, has introduced a groundbreaking solution known as Acid Proof Brick.Acid Proof Brick is a highly durable and chemical-resistant construction material that offers unmatched protection against corrosive substances. The bricks are crafted using a combination of high-quality clay, silica, and alumina, which undergo an intense firing process. This meticulous technique gives the bricks exceptional density, strength, and resistance to acids, bases, and alkalis.One of the key advantages of Acid Proof Brick is its ability to withstand extreme temperatures, making it suitable for a wide range of industries such as chemical plants, oil refineries, power stations, and metal processing facilities. The brick's resistance to thermal shocks ensures that it maintains its integrity even in the harshest environments, preventing potential accidents and prolonging the lifespan of the structures.Moreover, Acid Proof Brick offers exceptional dimensional stability. This means that it maintains its shape and size over time, minimizing the risk of cracks and leaks in the structures. This stability eliminates the need for regular maintenance and repairs, saving companies valuable time and resources in the long run.The installation process of Acid Proof Brick is also worth noting. ACME Inc. provides comprehensive guidance and support to ensure a seamless installation. With their team of highly skilled technicians, they assist clients in every step of the process, from preparation to final inspection. This commitment to customer satisfaction sets ACME Inc. apart from its competitors and has contributed to their impressive track record in providing reliable construction materials.In addition to its superior resistance to corrosion, Acid Proof Brick also offers easy cleaning and maintenance. Its smooth surface allows for effortless removal of chemical residue, ensuring a safe and hygienic working environment. This quality not only benefits the infrastructure but also plays a crucial role in meeting stringent industry regulations and standards.ACME Inc. has emerged as a reliable and trusted provider of Acid Proof Brick due to their commitment to innovation and quality. Their state-of-the-art manufacturing facilities, equipped with modern machinery and stringent quality control measures, ensure that every brick meets the highest standards. Furthermore, the company remains proactive in researching and developing new materials and technologies to address evolving industry needs.The success of Acid Proof Brick can be attributed to its versatility and ability to adapt to various construction requirements. ACME Inc. understands that every industry has unique demands, and thus they offer customization options to suit individual project specifications. This flexibility ensures that their clients can achieve optimal results and enhance the efficiency of their operations.In conclusion, Acid Proof Brick has revolutionized the construction industry by offering robust protection against corrosion and chemical damage. ACME Inc.'s commitment to quality, innovation, and customer satisfaction has made them a go-to choice for industries facing the challenges of extreme environments. With their reliable support and exceptional materials, companies can now focus on their core operations, confident in the durability and longevity of their infrastructure.
Improved Refractory Material: High-Quality Low Cement Castables Boost Performance
Title: Industry-Leading High-Quality Low Cement Castables Revolutionize Refractory Solutions: A Breakthrough by [Company Name]Introduction:[Company Name], a pioneering leader in refractory solutions, has developed and launched its revolutionary High-Quality Low Cement Castables. This significant breakthrough in the industry offers superior performance, durability, and versatility, setting a new standard for refractory materials. With top-notch engineering and expertise, [Company Name] continues to reshape the market by providing innovative solutions tailored to specific industrial needs.Body:1. Understanding the Significance of Refractory Solutions:Industries such as steel, cement, petrochemical, and power generation rely heavily on refractory materials to withstand extremely high temperatures and harsh operating conditions. Traditional refractory materials often have limitations that hinder their effectiveness, leading to frequent repairs and maintenance. Recognizing this challenge, [Company Name] has dedicated substantial resources towards developing a game-changing solution.2. Introducing High-Quality Low Cement Castables:Built upon years of research and technical expertise, [Company Name] proudly introduces their flagship product, High-Quality Low Cement Castables. These castables showcase a remarkable reduction in cement content while maintaining unmatched strength and thermal stability. The innovative formulation allows for a dense, low-porosity material that outperforms conventional refractories in demanding applications.3. Unparalleled Performance and Durability:The High-Quality Low Cement Castables by [Company Name] are engineered to deliver exceptional performance and withstand extreme thermal and mechanical stresses. These castables demonstrate higher hot strength and better resistance to thermal shocks, minimizing downtime and maintenance costs for industrial facilities. With improved chemical resistance and erosion resistance, they contribute significantly to prolonging the lifespan of industrial furnaces, kilns, and other high-temperature systems.4. Versatility and Customization:[Company Name] understands that different industries have unique requirements for refractory materials. Thus, the High-Quality Low Cement Castables are available in a wide range of compositions, ensuring customization to meet specific needs. The company's technical team works closely with clients to develop tailored solutions, maximizing efficiency and cost-effectiveness.5. Environmental Commitment and Sustainability:Notably, [Company Name] achieves its industry-leading performance while focusing on reducing the environmental impact. The High-Quality Low Cement Castables have significantly lower carbon emission levels compared to typical refractory materials, aligning with global efforts towards sustainable practices. This commitment ensures that clients can achieve their operational targets while adhering to increasingly stringent environmental regulations.6. Collaborative Approach and Technical Support:[Company Name] takes pride in its customer-centric approach, offering comprehensive technical support and expertise throughout the entire project lifecycle. Their team of experienced professionals collaborates closely with clients to identify their challenges, apply the most suitable refractory solutions, and render continuous support for maintenance and optimization.7. Industry Recognition and Partnerships:The High-Quality Low Cement Castables by [Company Name] have gained swift recognition within the industry. Numerous high-profile partnerships with leading companies in various sectors have further solidified the reputation and trust in [Company Name]'s products.Conclusion:[Company Name]'s ground-breaking High-Quality Low Cement Castables have revolutionized the refractory industry by providing enhanced performance, durability, and versatility. Focusing on customer satisfaction, environmental responsibility, and cutting-edge technology, [Company Name] continues to redefine industry standards and surpass client expectations. They are committed to providing successful refractory solutions that enable businesses to operate efficiently and sustainably in the face of challenging conditions.
Unlocking the Potential of Low Cement Castable Refractory Material: A Game-Changer for Industrial Applications
Low Cement Castable Refractory Material: The Newest Addition to {Company Name}'s Product Line{Company Name}, a leading manufacturer of refractory materials, has recently introduced their latest product, the Low Cement Castable Refractory Material. This latest addition to their lineup of innovative products is designed to provide high-quality insulation solutions for a wide range of applications.The Low Cement Castable Refractory Material is a specially formulated and precisely engineered product that is ideal for use in high-temperature environments such as kilns, furnaces, and incinerators. It is created using a unique combination of raw materials that are carefully selected to provide optimum performance, durability, and resistance to extreme temperatures.This innovative product is designed to offer superior insulation performance in comparison to traditional materials. Its low cement content and unique composition result in a product that is highly resistant to thermal shock, chemical attack, and abrasion. It also provides excellent strength and durability, ensuring a long-lasting solution for industrial processes and applications.{Company Name} has built a reputation for delivering high-quality products, and their latest release is no exception. The Low Cement Castable Refractory Material is manufactured using advanced technology and stringent quality control processes, ensuring that it meets the highest standards of performance and reliability.The Low Cement Castable Refractory Material boasts numerous benefits that make it an attractive option for use in a wide range of applications. It provides exceptional thermal insulation, significantly reducing energy consumption and heat loss. Its high strength and abrasion resistance make it suitable for use in environments that involve wear and tear, such as the mining, cement, and steel industries.In addition to its superior performance, the Low Cement Castable Refractory Material is also incredibly versatile, making it suitable for a variety of industrial applications. These include boilers, incinerators, kilns, and furnaces, among others. Its outstanding insulating properties also make it a popular choice for use in high-temperature applications such as metal melting, heat treatment, and forging processes.{Company Name} has always been at the forefront of innovation when it comes to refractory materials. Their latest product, the Low Cement Castable Refractory Material, is a testament to their commitment to delivering the highest standards of quality and reliability to their customers.In conclusion, the introduction of the Low Cement Castable Refractory Material by {Company Name} is a significant development in the field of refractory materials. Its superior performance, strength, and durability make it an excellent choice for use in a wide range of industrial applications. Its versatility also ensures that it can be used for various processes, making it an invaluable asset for businesses in different industries. As a leading manufacturer in the field of refractory materials, {Company Name} has once again demonstrated their commitment to providing high-quality solutions that meet the needs of their customers.
Ceramic Fiber Blanket Used for High-Temperature Insulation
[Company Introduction]XYZ Corporation is a leading manufacturer in the insulation industry, specializing in the production of high-quality ceramic fiber blankets. With an excellent track record spanning over two decades, XYZ Corporation has become synonymous with innovative and reliable insulation solutions. Our commitment to providing superior products and exceptional customer service has made us the preferred choice for industrial and commercial applications.[News Content]Ceramic Fiber Blankets – Revolutionizing Thermal Insulation in Industrial Applications[City], [Date] - XYZ Corporation, a frontrunner in the insulation industry, is proud to announce its latest addition to its product line – an advanced ceramic fiber blanket designed to revolutionize thermal insulation in various industrial applications. This newly launched product promises excellent thermal insulation, fire resistance, and durability for a wide range of industries.The Kaowool Ceramic Fiber Blanket, developed by XYZ Corporation, is manufactured using state-of-the-art technologies and adheres to the highest quality standards. This cutting-edge insulation blanket offers exceptional performance in terms of thermal conductivity, heat resistance, and energy efficiency. Its unique composition provides superior heat insulation properties, making it ideal for applications in high-temperature environments.One of the key advantages of the Kaowool Ceramic Fiber Blanket is its ability to withstand extreme temperatures. With a melting point exceeding 1300°C (2400°F), this blanket ensures long-lasting insulation even in the most demanding conditions. Its low thermal conductivity minimizes heat loss, significantly reducing energy consumption and enhancing cost-effectiveness for industrial processes and facilities.In addition to its outstanding thermal insulation properties, the Kaowool Ceramic Fiber Blanket is also renowned for its exceptional fire resistance. The fiberglass-free composition of the blanket eliminates the risk of toxic fumes and ensures utmost safety in the event of a fire. This makes it an ideal choice for industries where fire safety regulations are stringent, such as petrochemical, power generation, and steel manufacturing.With sustainability being a top priority in today's industrial landscape, the Kaowool Ceramic Fiber Blanket offers eco-friendly insulation solutions. Its production process adheres to strict environmental regulations, and the material itself is recyclable. By choosing this blanket, industries can reduce their carbon footprint without compromising on performance and safety.The versatility of the Kaowool Ceramic Fiber Blanket makes it suitable for various applications across multiple industries. Its lightweight and flexible nature allow for easy installation and handling, enabling companies to benefit from hassle-free insulation solutions. This blanket finds applications in industries such as metal processing, glass manufacturing, ceramics, and automotive, among others.Mr. John Doe, CEO of XYZ Corporation, expressed his excitement about the launch of this groundbreaking product. He stated, "The Kaowool Ceramic Fiber Blanket represents our continued commitment to innovation and providing our customers with the best insulation solutions available. With its outstanding thermal insulation properties and impeccable fire resistance, this blanket is set to change the game in the industrial insulation sector."XYZ Corporation plans to extend its marketing efforts to reach a broader customer base, both domestically and internationally. By partnering with industry leaders and distributors, the company aims to ensure that the Kaowool Ceramic Fiber Blanket is readily available in markets worldwide. XYZ Corporation also plans to invest in research and development to further enhance the product's features and explore new applications.As industrial processes evolve, the demand for high-performance insulation materials continues to grow. The Kaowool Ceramic Fiber Blanket, with its superior thermal insulation, exceptional fire resistance, and eco-friendly composition, positions XYZ Corporation at the forefront of the industry. It is a testament to the company's commitment to innovation and providing solutions that meet the evolving needs of its customers.About XYZ Corporation:XYZ Corporation is a leading manufacturer of insulation solutions, specializing in the production of high-quality ceramic fiber blankets. With decades of experience, the company has built a reputation for reliability, innovation, and exceptional customer service. XYZ Corporation's products cater to a wide range of industrial applications and are trusted by businesses worldwide. For more information, visit www.xyzcorporation.com.[Word Count: 803 words]
New Fire Bricks Designed for High-Temperature Applications
Title: Revolutionary Fire-Resistant Bricks Redefine Safety Standards in ConstructionIntroduction:In the ever-evolving world of construction and building materials, ensuring the safety and reliability of structures is of paramount importance. Recognizing the need for superior fire protection, Dineen Fire Bricks, a leading industry player, has introduced a groundbreaking solution that will revolutionize construction practices. Engineered to withstand extreme temperatures and reduce fire risks, the innovative fire-resistant bricks by Dineen are set to redefine safety standards in the construction industry.Breaking New Ground:Dineen Fire Bricks have emerged as a game-changer in the field of fire-resistant building materials. These bricks have been designed and developed using state-of-the-art technology, combining high-quality raw materials to achieve exceptional fire resistance capabilities. The incorporation of advanced manufacturing techniques ensures that these bricks exhibit superior durability and reliability, making them an ideal choice for a wide range of construction projects.Unprecedented Fire Protection:What sets Dineen Fire Bricks apart from traditional flame-resistant bricks is their remarkable fire protection capabilities. These bricks have been subjected to rigorous testing in accordance with international safety protocols, and they have consistently surpassed the required standards. Even in the face of extreme heat and intense flames, these bricks remain structurally intact, minimizing the risk of structural collapse and facilitating swift evacuation procedures. Such unprecedented fire protection contributes significantly to enhancing the overall safety of various building types, including residential, commercial, and industrial structures.Enhanced Structural Integrity:Beyond their exceptional fire resistance properties, Dineen Fire Bricks also offer enhanced structural integrity, thereby ensuring the longevity and stability of buildings. The unique composition of these bricks, coupled with precise manufacturing techniques, guarantees optimum load-bearing capabilities. This feature proves critical during emergencies, as it allows the structure to withstand the weight of debris or collapses that may occur in the event of a fire. By incorporating Dineen Fire Bricks into their projects, architects and engineers can provide an additional layer of reassurance to the occupants, ensuring their safety during unforeseen emergencies.Versatility and Adaptability:Dineen Fire Bricks cater to the diverse needs of the construction industry by offering a range of product variations. From standard fire-resistant bricks to lightweight options, the company provides solutions suitable for different applications. This versatility allows architects and builders to utilize these bricks in both new construction projects and renovation endeavors. Additionally, Dineen Fire Bricks can be seamlessly integrated with existing building materials, making them an attractive choice for retrofitting older structures.Eco-Friendly Solution:With growing concerns about environmental sustainability, Dineen Fire Bricks embody the company's commitment to developing eco-friendly solutions. These bricks are manufactured using responsibly sourced materials and employ energy-efficient production techniques, minimizing carbon emissions. By opting for Dineen Fire Bricks, construction professionals can contribute to the construction industry's efforts to reduce its ecological footprint, making it a compelling choice for environmentally-conscious builders.Looking Ahead:As the demand for safe and reliable building materials continues to rise, Dineen Fire Bricks are poised to carve out a significant presence in the construction market. With their unmatched fire-resistant capabilities, enhanced structural integrity, versatility, and eco-friendly focus, these bricks are set to redefine construction safety standards. The adoption of Dineen Fire Bricks will undoubtedly revolutionize the way structures are built, ensuring the protection and security of occupants for years to come.Conclusion:Dineen Fire Bricks, with their unrivaled fire resistance, superior structural characteristics, and adaptability, represent a landmark innovation in the construction industry. These revolutionary bricks offer a solution that not only enhances safety but also aligns with sustainable practices. By prioritizing and investing in the use of Dineen Fire Bricks, construction professionals can fulfill their responsibility of safeguarding lives and ensuring robust structures in an ever-evolving world.