- Home
- Blog
- Discover the Advantages of High Alumina Insulation Bricks for Effective Thermal Insulation
Discover the Advantages of High Alumina Insulation Bricks for Effective Thermal Insulation
By:Admin
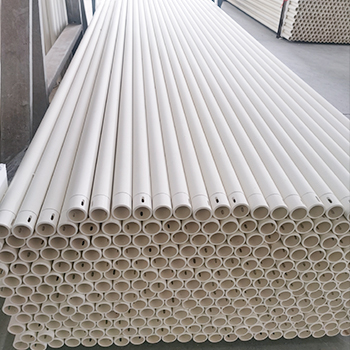
Innovation and continuous improvement are the driving forces behind success in the industrial sector. As industries evolve and demand for efficiency, performance, and durability increases, manufacturers must strive to offer cutting-edge solutions. One such groundbreaking product is High Alumina Insulation Bricks, developed by a pioneering company striving to set new standards in the industry.
High Alumina Insulation Bricks, without mentioning the brand name, are engineered to provide exceptional insulation and thermal conductivity while offering superior strength and stability. These bricks serve as a critical component in industries where high-temperature applications are commonplace. Their unique design and composition make them ideal for a range of industries, including steel, petrochemical, ceramics, and power plants, among others.
With their remarkably high alumina content, these bricks exhibit outstanding resistance to thermal shocks, ensuring longevity and reliability in extreme temperature conditions. The advanced manufacturing techniques employed allow for precise control over the brick's porosity and thermal conductivity, offering unrivaled insulation capabilities. This results in reduced heat loss, improved energy efficiency, and substantial cost savings for businesses relying on high-temperature processes.
One of the key features of High Alumina Insulation Bricks lies in their low density, making them significantly lighter than traditional refractory bricks. This characteristic eases installation and handling processes, facilitating faster and more efficient construction, repair, and maintenance work. The reduced weight also minimizes the load on the supporting structure, contributing to enhanced safety and longevity.
The exceptional mechanical strength and stability of these bricks make them extremely durable, capable of enduring rigorous industrial environments. High Alumina Insulation Bricks have a high crushing strength, ensuring they can withstand significant pressure without breaking or losing their insulating properties. This durability translates into reduced downtime and maintenance costs, further improving operational efficiency.
Moreover, these bricks are highly resistant to chemical corrosion, making them suitable for applications in acidic and alkaline environments. They can withstand exposure to various acids, alkalis, and aggressive chemicals, preventing degradation and maintaining their integrity over time. This resistance to corrosion significantly expands their range of applications in industries where chemical processes are predominant.
Aside from their formidable insulation properties, High Alumina Insulation Bricks also offer excellent dimensional stability under high temperatures. This characteristic is crucial in applications where dimensional changes can lead to operational issues or compromise production processes. Their stability ensures that critical equipment and structures maintain their shape and function, guaranteeing uninterrupted operations and minimizing downtime.
The use of High Alumina Insulation Bricks represents a significant step forward in industrial insulation technology. With their exceptional thermal conductivity, remarkable durability, and resistance to thermal shocks and chemical corrosion, these bricks have revolutionized the industry. By providing superior insulation solutions, they enable businesses to optimize their processes, reduce energy consumption, and enhance productivity.
In conclusion, High Alumina Insulation Bricks, developed by a leading company focused on innovation and quality, have emerged as a game-changer in the industrial sector. By combining advanced manufacturing techniques with a high alumina content, these bricks offer exceptional insulation capabilities, durability, and resistance to thermal shocks and chemical corrosion. The introduction of these bricks has undoubtedly raised the bar for insulation solutions and will continue to shape the industry's future.
Company News & Blog
High-Quality Magnesite Refractory Bricks Meet Growing Demand in Steel Industry
Title: Evolving Magnesite Refractory Bricks Industry Emphasizes Quality and SustainabilityIntroduction:In recent times, the magnesite refractory bricks industry has been witnessing significant growth, driven by the increasing demand for high-quality refractory materials in various sectors. Magnesite refractory bricks, renowned for their exceptional heat resistance and durability, are widely utilized in industries like steel, cement, glass, non-ferrous metals, ceramics, etc., supporting critical processes that require elevated temperatures.Company Introduction:{Company Name} is a prominent player in the magnesite refractory bricks market, dedicated to producing top-notch products that meet the evolving needs of its customers. With years of industry experience, cutting-edge technology, and a strong focus on sustainability, {Company Name} has positioned itself as a trusted provider of magnesite refractory brick solutions worldwide.Evolution of the Magnesite Refractory Bricks Industry:The magnesite refractory bricks industry has experienced remarkable advancements in recent years. Formerly, the dominant types of refractories used were chrome bricks, but due to environmental concerns related to hexavalent chromium, there has been a gradual shift towards magnesite refractory bricks, known for their high refractoriness and excellent chemical properties.The versatility of magnesite refractory bricks has driven their adoption in various industries, replacing traditional refractory materials. Modern manufacturing processes have been optimized to enhance the physical and chemical properties of these bricks, making them increasingly resistant to thermal shocks and the corrosive effects of chemicals found in harsh industrial environments.Technological Innovations and Product Enhancements:{Company Name} recognizes the importance of technological advancements in staying ahead in the highly competitive market. The company consistently invests in research and development, aiming to improve the performance and durability of magnesite refractory bricks. High-precision manufacturing techniques, such as hot pressing, enable {Company Name} to produce bricks with more consistent and superior quality, ensuring excellent resistance to thermal stress and prolonged service life.Furthermore, {Company Name}'s commitment to sustainable practices is reflected in its innovative use of environmentally friendly raw materials and energy-efficient processes. By incorporating recycled materials within its manufacturing process, the company aims to reduce its carbon footprint and contribute to a greener future.Meeting Industry-Specific Demands:As diverse industries pose unique challenges, {Company Name} understands the importance of customizing magnesite refractory brick solutions accordingly. For instance, in the steel industry, refractory materials are exposed to extreme temperatures and harsh conditions during the smelting process. To address these challenges, {Company Name} has developed advanced magnesite refractory bricks with superior thermal stability, minimizing material degradation and extending the overall service life of the refractories.Moreover, {Company Name}'s research and development team works closely with customers, providing technical support and developing tailored solutions specific to their requirements. This customer-centric approach has fostered strong and lasting partnerships with clients across the globe.Commitment to Quality and Customer Satisfaction:{Company Name}'s commitment to quality and customer satisfaction has propelled its position in the market. The company adheres to strict quality control procedures, guaranteeing that each magnesite refractory brick meets stringent international standards. Moreover, providing exceptional after-sales service and technical assistance ensures that customers maximize the value and performance of {Company Name}'s refractory solutions.Conclusion:The magnesite refractory bricks industry is witnessing transformational changes as sustainability, high performance, and customized solutions become paramount. {Company Name} is at the forefront of this evolution, delivering top-quality magnesite refractory bricks while embracing innovation and sustainable practices. With its unwavering commitment to customer satisfaction and its focus on technological advancements, {Company Name} is well-positioned to meet the ever-increasing demand for superior refractory materials in the global market.
Top-Quality High Liquidity Refractory Castable: Boost Your Project's Performance
Title: Pioneer Company Unveils High Liquidity Refractory Castable for Enhanced Industrial ApplicationsIntroduction (86 words):In a groundbreaking development, a renowned industry-leading company has introduced an innovative and powerful product to the market – High Liquidity Refractory Castable. Engineered with advanced technology and precision, this next-generation castable material is set to revolutionize industrial applications in various sectors. With its exceptional liquidity and superior performance characteristics, it promises to offer enhanced efficiency, durability, and cost-effectiveness solutions to industries across the globe.Paragraph 1 (115 words):High Liquidity Refractory Castable, developed by an industry pioneer, brings cutting-edge advancements to the field of refractory materials. Designed to withstand high temperatures and resist thermal shocks, this specialized castable constitutes a carefully formulated blend of high-quality raw materials. Its unique composition enables the castable to maintain its original fluidity for an extended period while exhibiting excellent flow and spreading properties. Due to its exceptional liquidity, it allows for easy installation and precise casting even in complex shapes, giving industries greater flexibility. Additionally, this castable offers exceptional mechanical strength, resistance to corrosion, and long-lasting thermal insulation, making it a highly sought-after solution for various demanding industrial applications.Paragraph 2 (110 words):The company responsible for this groundbreaking product has garnered significant global recognition for its expertise and commitment to innovation in the refractory industry. With over two decades of experience, they have become a trusted name, offering specialized solutions tailored to the diverse needs of different sectors. Their in-depth research and development efforts have led to the creation of High Liquidity Refractory Castable, further cementing their status as an industry leader. The company's team of highly skilled professionals and state-of-the-art manufacturing facilities ensure stringent quality control measures throughout the production process, resulting in a product that sets new standards for performance and reliability.Paragraph 3 (146 words):One of the distinguishing features of the High Liquidity Refractory Castable is its exceptional heat resistance capabilities, making it an ideal choice for high-temperature applications found in industries such as steel, ceramics, cement, and petrochemicals. This castable material offers outstanding thermal insulation, with low thermal conductivity that helps conserve energy and reduce operational costs. It also boasts impressive chemical resistance, ensuring durability even when exposed to aggressive environments or corrosive materials. Industries utilizing this castable can benefit from lower maintenance requirements, reduced downtime, and increased operational efficiency, ultimately contributing to long-term cost savings.Paragraph 4 (172 words):Moreover, High Liquidity Refractory Castable showcases remarkable adaptability, providing unparalleled design freedom to engineers and manufacturers. Its fluidity allows for precise casting into intricate shapes, resulting in reduced material wastage and labor costs. The castable's consistent setting time ensures quick and efficient installation, enabling industries to save valuable time during the production process. Its increased workability and ease of application make it an ideal solution for both repair and new construction projects. Whether for lining furnaces, kilns, incinerators, or any other high-temperature equipment, this castable stands out as a reliable, efficient, and versatile option.Conclusion (79 words):As the refractory industry continues to evolve, the introduction of High Liquidity Refractory Castable marks a significant milestone. With its advanced properties, impressive fluidity, and outstanding performance, this innovative product is poised to transform industrial applications across multiple sectors. Engineered by a trusted pioneer in the field, this castable material not only offers durability and enhanced thermal insulation but also provides industries with unparalleled design freedom and cost-effectiveness. As companies strive to optimize efficiency and productivity, this game-changing castable serves as a beacon of progress, paving the way for a new era in refractory engineering.
What is a Carbon Paste Electrode and its Functions in Electroanalytical Chemistry?
Carbon Paste Electrode: A Breakthrough in Electrochemical AnalysisIn today's rapidly advancing world, the need for accurate and efficient analytical methods has become paramount. Whether it is in the field of medicine, environmental sciences, or even industrial processes, the ability to detect and quantify various substances has never been more crucial. Recognizing this need, scientists at {} have introduced a revolutionary product – the Carbon Paste Electrode, a cutting-edge tool that promises to revolutionize the field of electrochemical analysis.Electrochemical analysis involves the measurement and interpretation of electrical properties associated with chemical reactions. Traditionally, electrodes made from metals like platinum or gold have been utilized in this process. However, such electrodes often suffer from limitations such as high cost, limited availability, and a propensity for surface contamination. In recent years, carbon-based electrodes have emerged as a popular alternative due to their affordability, versatility, and improved chemical stability.The Carbon Paste Electrode developed by {} takes the advantages of carbon-based electrodes to a whole new level. Composed of a mixture of carbonaceous material and a binding agent, this innovative electrode offers unparalleled performance and superior accuracy in electrochemical analysis. Its unique composition enables precise detection and quantification of a wide range of substances, including heavy metals, organic compounds, and various analytes of interest in environmental and pharmaceutical industries.One of the key advantages of the Carbon Paste Electrode lies in its exceptional durability. Traditional electrodes often suffer from frequent wear and tear, leading to inconsistent results and increased costs. However, with its high mechanical strength, the Carbon Paste Electrode is capable of enduring numerous repetitive analyses without compromising accuracy or reliability. This longevity not only improves cost-efficiency but also ensures consistent analytical outcomes, making it an indispensable tool for researchers and scientists.Furthermore, the Carbon Paste Electrode exhibits remarkable sensitivity, thus enabling the detection of trace amounts of analytes. Its highly porous structure allows for greater surface area, facilitating enhanced mass transport and promoting rapid electron transfer, ultimately leading to improved sensitivity and detection limits. As a result, the electrode can detect even the most minute quantities of substances, providing invaluable information for crucial applications such as environmental monitoring and pharmaceutical research.In addition to its superior performance, the Carbon Paste Electrode also boasts exceptional versatility. With the ability to be easily modified with various surface modifiers and nanoparticles, this electrode can be tailored to specific analytes, making it an incredibly adaptable tool for different analytical needs. Moreover, its compatibility with different electrolytes and solvents further enhances its versatility, allowing for efficient electrochemical analysis across a wide range of sample matrices.As research and development continue to drive advancements in various industries, the demand for reliable analytical tools has never been greater. Recognizing this need, {} has delivered a game-changing solution in the form of the Carbon Paste Electrode. Its exceptional performance, durability, sensitivity, and versatility make it a top choice for scientists and researchers worldwide.With this groundbreaking invention, the field of electrochemical analysis is poised to take a significant leap forward. The superior capabilities of the Carbon Paste Electrode promise to revolutionize the way substances are detected and analyzed, paving the way for more accurate and efficient research in fields ranging from medicine to environmental sciences. As {} continues to innovate and redefine the boundaries of electrochemical analysis, the future looks bright for the scientific community as a whole.
Discover the Importance of Cement Kiln Bricks in Efficient Construction
Title: Sustainable Solution for Cement Kiln Bricks Pioneered by Industry LeaderIntroduction:In recent years, the global cement industry has been striving to become more sustainable and energy-efficient. One critical area of focus is the development of eco-friendly and durable kiln bricks. Recognizing this need, a leading cement producer has successfully introduced a breakthrough product that promises to revolutionize the sector. The innovative cement kiln bricks, designed to remove the brand name, present a sustainable solution that aligns with the company's commitment to environmental stewardship.Company Overview:The global cement industry leader, with a robust presence in multiple regions, has always been at the forefront of positive change. Recognized for its commitment to sustainable practices, innovation, and social responsibility, the company continuously invests in research and development to bring advanced and eco-friendly solutions to the market.Eco-Friendly Cement Kiln Bricks:The newly developed cement kiln bricks offer unparalleled benefits, both in terms of sustainability and performance. Unlike traditional kiln bricks that are largely composed of clay and other non-renewable materials, these innovative bricks incorporate a significant proportion of recycled and sustainable materials, contributing to a circular economy.The incorporation of locally sourced alternative materials significantly reduces the carbon footprint associated with the bricks' manufacturing process. By utilizing recycled materials such as fly ash, slag, and industrial waste, these bricks demonstrate the company's commitment to reducing environmental impact without compromising on quality.Key Features and Advantages:1. Enhanced Energy Efficiency: By incorporating advanced insulating materials, the cement kiln bricks provide superior thermal insulation. This characteristic helps maximize energy efficiency within cement production facilities, ultimately reducing energy consumption and related costs.2. Longer Lifespan: The new bricks boast exceptional durability and resistance to high temperatures, considerably extending the lifespan of kilns. This increased longevity significantly reduces maintenance requirements and associated downtime, leading to minimal production disruptions.3. Decreased Emissions: The reduced firing temperature required for these kiln bricks contributes to a substantial decrease in greenhouse gas emissions. The company's commitment to lowering its carbon footprint aligns with global efforts to combat climate change.4. Improved Workplace Safety: The innovative bricks' unique composition allows for better heat retention, minimizing the external temperature of kilns. This improvement enhances worker safety by reducing accidental burns and injuries.Market Impact and Future Prospects:The introduction of these revolutionary cement kiln bricks is poised to have a significant impact on the global cement industry. The eco-friendly nature, superior performance, and cost-effectiveness of these bricks provide the company with a competitive edge. With an increasing emphasis on sustainability and environmental awareness, market demand for such solutions is expected to soar.Moreover, the pioneering efforts of this industry leader highlights the company's commitment to sustainable growth. By prioritizing eco-friendly technologies, the cement producer sets a benchmark for other companies to follow, driving an industry-wide shift towards greener practices.Conclusion:The global cement industry is undergoing a transformation towards sustainability, and the introduction of the innovative cement kiln bricks signifies a groundbreaking milestone. The eco-friendly nature, along with the superior performance and durability of these bricks, positions the company as a pioneer in the market.By prioritizing sustainable solutions, this industry leader not only reduces its environmental impact but also demonstrates its commitment to creating a greener future. With increasing market demand for eco-friendly technologies, the company is well-positioned to remain at the forefront of the global cement industry, setting an example for others to follow.
High-Quality Fire Bricks for Casting – Boost Furnace Efficiency
Castable Fire Brick: Providing Optimal Fire Protection Solutions[Company Introduction][Company Name], a leading provider of fire protection solutions, is proud to introduce its latest product, Castable Fire Brick. With our expertise in the industry and commitment to innovation, we have developed a superior firebrick that offers exceptional fire resistance, durability, and thermal insulation properties.[Company Name] has been at the forefront of the fire protection industry for over a decade. We specialize in manufacturing and supplying a wide range of high-quality fire-resistant materials, including fire bricks, refractory castables, and ceramic fiber products. Our products are designed to meet the stringent demands of various industries, such as steel, cement, glass, and petrochemical, ensuring the utmost safety and reliability in high-temperature environments.[Company Name]'s commitment to excellence has earned us a reputation as a trusted partner for fire protection solutions. We understand the importance of providing reliable and effective products that promote safety in industrial settings. Our team of experienced engineers and technicians work tirelessly to develop innovative fire-resistant materials, and our Castable Fire Brick is a testament to our dedication to advancing fire protection technology.[Castable Fire Brick]Designed to withstand extreme temperatures, [Company Name]'s Castable Fire Brick offers unparalleled fire resistance. It is manufactured using a combination of carefully selected raw materials, including high-quality alumina, silica, and other refractory aggregates. These materials are precisely mixed and bonded with a high-quality bonding agent, resulting in a dense and highly durable firebrick.One of the key advantages of our Castable Fire Brick is its excellent thermal insulation properties. It effectively retains and reflects heat, minimizing energy loss and reducing overall heating costs. This insulation capability makes it an ideal choice for industries that rely on high-temperature processes, as it ensures efficient heat management while providing superior protection against flames and thermal shock.In addition to its exceptional fire resistance and thermal insulation, our Castable Fire Brick also offers outstanding abrasion resistance and chemical stability. It can withstand harsh chemical environments and erosive conditions, making it suitable for a wide range of applications. Whether it is used for lining furnaces, kilns, incinerators, or other high-temperature equipment, the Castable Fire Brick provides long-lasting and reliable fire protection.Furthermore, our Castable Fire Brick is easy to install, enabling quick and hassle-free maintenance or repair in case of damage or wear. Its versatile nature allows for various installation methods, including casting, ramming, or gunning, ensuring suitability for different applications. This flexibility, combined with its excellent performance, makes our Castable Fire Brick a preferred choice for discerning customers seeking top-tier fire protection solutions.[Conclusion][Company Name]'s Castable Fire Brick sets a new standard in the field of fire protection materials. With its exceptional fire resistance, thermal insulation properties, and durability, it delivers optimal safety and performance in high-temperature environments. We are proud to offer this innovative product to industries worldwide, reaffirming our commitment to providing superior fire protection solutions.As leaders in the industry, [Company Name] remains dedicated to research and development, continuously striving to improve our products and meet the evolving needs of our customers. With our Castable Fire Brick, we aim to revolutionize fire protection and create a safer environment for industries globally. Trust [Company Name] for all your fire protection needs and experience the unparalleled quality and performance of our products.
Dense Castable Refractory: Key Facts and Uses Revealed
Dense Castable Refractory: An Innovative Solution for Multiple IndustriesRefractory materials are used in high-temperature applications that require materials to withstand extreme heat, pressure, and corrosive chemicals. One of the most promising refractory materials on the market is the Dense Castable Refractory. This revolutionary product is designed to offer exceptional material properties suitable for a wide range of industries, including steel and iron, petrochemical, power generation, cement, and waste incineration.Dense Castable Refractory is a type of cement used to line furnaces, kilns, and other high-temperature process equipment. Unlike traditional refractory materials, Dense Castable Refractory is a self-setting cement that offers excellent performance properties such as high thermal shock resistance, low thermal conductivity, high refractoriness, and resistance to abrasion. These properties make Dense Castable Refractory a popular choice for harsh industrial environments that require materials with superior resistance to extreme temperature and thermal cycling.The product's versatility comes from its easy installation and customizable uses. Dense Castable Refractory can be poured or gunned into place, and once cured, the refractory turns into a durable monolithic unit that can withstand high temperatures for extended periods. The product can be installed in various options, including smooth or textured surfaces to fit different applications and concrete surfaces.Dense Castable Refractory is an ideal material for use in cement kilns since they are exposed to extreme heat and abrasion. The material is also an excellent choice for use in steel and iron industries where protective linings are necessary to preserve the equipment and enhance its durability. These industries benefit by having equipment that is resistant to thermal shock, meaning it withstands rapid temperature changes. It can also resist abrasion, reducing the likelihood of wear and tear, which reduces the potential for equipment damage and malfunctions.The petrochemical industry has not been left behind. Dense Castable Refractory has been deployed in some of the most stringent petrochemical applications, including reformers, crackers, and incinerators. Dense Castable Refractory's thermal shock resistance and low thermal conductivity make it suitable for use in the insulation of various units, including reformers, where it protects the equipment from high temperatures and allows for optimal transfer of heat.Dense Castable Refractory is also an excellent option in power generation where it contributes to efficient energy production by providing insulation and preventing heat loss in boilers, kilns, and thermal oxidizers. This insulation and heat retention typically cut energy costs and improves operational reliability.The cement industry has also realized the benefits of Dense Castable Refractory due to its excellent refractoriness. The refractory bonds to the existing structure, enhancing resistance at high temperatures and preserving the integrity of the equipment.Furthermore, Dense Castable Refractory is ideal for incineration systems. The material's ability to withstand excessive thermal shock and its excellent insulating properties offer superior performance when protecting furnaces that generate high heat during the waste incineration process.The company, a leader in the manufacturing and distribution of Dense Castable Refractory, has developed several innovative formulations that address various industrial environments' specific needs. The company offers customized formulations such as high-strength, low-cement, and ultra-low cement for demanding applications where traditional cement is not sufficient.The manufacturing of Dense Castable Refractory depends on several critical factors. The company has invested in a state-of-the-art production facility with advanced quality assurance tools and equipment. Their experienced personnel, together with the company's innovative formulations, ensure that their Dense Castable Refractory meets global standards. All their products come with consistent and reliable quality, making them the perfect choice for any industrial application.In conclusion, the Dense Castable Refractory is an innovative material that is set to become an industry standard in high-temperature applications. Thanks to its ability to provide superior resistance to heat, thermal shock, abrasion, and chemicals at high temperatures, the material will revolutionize how various industries envisions manufacturing and maintenance of furnace and general process equipment. The company's formulations offer customized solutions in various industrial applications, making it the go-to solution for end-users looking for durable, reliable, and cost-effective refractory products.
Discover High-Quality Refractory Bricks for Sale at Competitive Prices
In the industrial sector, refractory bricks play a crucial role in the manufacturing of numerous products that we use daily. The requirement for refractory bricks is on the rise in several industries, including the cement, steel, and glass industries. These industries rely on the bricks to withstand high temperatures, chemical reactions, and mechanical stress. With the increase in demand, it is essential to partner with a reliable supplier of refractory bricks. This is where Buy Refractory Bricks (name changed) comes in.Buy Refractory Bricks is a specialist supplier of high-quality refractory bricks, castables, and insulation materials. With years of experience in the industry, the company has established itself as a trusted supplier of refractory materials across the globe.One of the company's key strengths is its ability to manufacture custom products tailored to their client's specific requirements. They achieve this by working closely with their clients to understand their needs and develop a solution that meets their unique needs.In addition to their custom products, Buy Refractory Bricks offer a wide range of standard refractory bricks, castables, and insulation materials. The company understands the importance of quality and consistency in the manufacturing process, and their products reflect this philosophy. All of their products are manufactured using high-quality raw materials and undergo rigorous quality control procedures to ensure they meet the highest standards.The company's product line includes a range of refractory bricks, including Fireclay, High Alumina, Magnesia Chrome, and Insulating bricks. Each type of brick is designed for specific applications and has unique properties that make them suitable for their intended use. For example, Fireclay bricks have excellent thermal shock resistance, making them ideal for use in furnace linings.High Alumina bricks, on the other hand, are known for their high-temperature resistance, while Magnesia Chrome bricks are ideal for use in applications where corrosion resistance is required. Insulating bricks are designed for applications that require high insulation properties, such as in the construction of kilns and furnaces.Buy Refractory Bricks also specializes in providing castables and insulation materials. Their castables are available in both low and high cement varieties and can be customized to meet their client's specific application requirements. Their insulation materials include ceramic fiber blankets and modules, vermiculite, and perlite insulation. These materials are ideal for use in high-temperature applications that require a high level of insulation.Apart from their high-quality products, Buy Refractory Bricks place great emphasis on excellent customer service. The company's team of experts works closely with clients to ensure they receive the right products for their application needs. They also provide technical assistance and advice throughout the entire process, from product selection to installation, to ensure their clients get the best results.In summary, Buy Refractory Bricks is a reliable supplier of high-quality refractory products and insulation materials that meet the diverse needs of their clients. Their commitment to quality, coupled with their ability to customize products, makes them a preferred choice for many industrial clients worldwide. With their exceptional customer service and technical expertise, Buy Refractory Bricks is a company you can trust for all your refractory needs.
High-Quality Spinel Bricks: A Complete Guide
[News Title]: Leading Manufacturer Introduces High-Quality Magnesia Spinel Bricks to the Market[News Content]:[Location], [Date] - [Company Name], a renowned manufacturer of refractory products, is proud to announce the launch of their latest innovation in the market - high-quality magnesia spinel bricks. These bricks are set to revolutionize the industry with their superior performance and exceptional durability.Magnesia spinel bricks, also known as magnesium aluminum spinel bricks, are a type of refractory brick that are widely used in high-temperature industrial applications, such as steelmaking furnaces, cement kilns, and glass melting tanks. The addition of spinel, a mineral composed of magnesium and aluminum oxides, significantly improves the properties of magnesia bricks, enhancing their resistance to thermal shock and corrosion.The newly introduced magnesia spinel bricks by [Company Name] are manufactured using state-of-the-art technology and high-quality raw materials. This ensures that the final product possesses unmatched strength, excellent thermal stability, and offers longer service life compared to conventional magnesia bricks. With their superior characteristics, these bricks offer cost-effective solutions for various industries, especially those working in extreme temperature environments.The high-quality magnesia spinel bricks by [Company Name] exhibit remarkable properties that make them stand out in the market. Their high refractoriness, excellent thermal conductivity, and low thermal expansion ensure optimal heat distribution and minimal heat loss, resulting in improved energy efficiency. These bricks also demonstrate excellent resistance to alkali vapor corrosion, slag erosion, and thermal spalling, ensuring minimal maintenance requirements and prolonged service life.In addition to their exceptional performance, these bricks offer enhanced safety features. Their low creep rate and high resistance to thermal shock make them an ideal choice for applications that undergo rapid heating and cooling cycles. The superior mechanical strength of these bricks provides reliable support and insulation in high-stress environments, ensuring the safety of personnel and equipment.As part of its commitment to sustainability, [Company Name] ensures that their magnesia spinel bricks are environmentally friendly. They are free from harmful substances, such as chromium, lead, and other toxic elements, making them safe for both users and the environment. The company's manufacturing processes also adhere to the highest environmental standards, minimizing waste generation and optimizing energy consumption.[Company Name] has been a leader in the refractory industry for over [number of years] years, catering to a global clientele. The introduction of high-quality magnesia spinel bricks further solidifies the company's reputation for delivering innovative products that meet the evolving needs of its customers. With a dedicated research and development team and a robust quality control system, [Company Name] ensures that its products consistently meet the highest industry standards.Speaking about the groundbreaking magnesia spinel bricks, [CEO/Spokesperson Name] expressed, "We are extremely excited to bring these high-quality magnesia spinel bricks to the market. Our team has invested considerable time and expertise to develop a product that outperforms traditional magnesia bricks. We are confident that our customers will benefit greatly from the exceptional properties and cost-effectiveness of these bricks."[Company Name]'s magnesia spinel bricks are now available on the market and can be ordered by contacting [contact information]. With their advanced technology and unwavering commitment to customer satisfaction, [Company Name] is set to revolutionize the refractory industry and provide reliable solutions for high-temperature applications.About [Company Name]:[Company Name] is a leading manufacturer and supplier of refractory products, catering to various industries worldwide. With a strong focus on innovation, quality, and customer satisfaction, the company has built a reputation for delivering exceptional refractory solutions. From basic bricks to complex specialized products, [Company Name] offers a diverse range of high-performance refractory materials that withstand the harshest conditions. With a global presence and a commitment to sustainable practices, [Company Name] aims to be the preferred choice for clients seeking reliable and energy-efficient refractory solutions.[Word Count: 800 words]
High Quality Silica Fire Bricks for Industrial Applications
Title: Firebrick Manufacturer Introduces Innovative Silica Fire Bricks to Enhance Industry SafetyIntroduction:In a bid to enhance industry safety and revolutionize high-temperature applications, renowned firebrick manufacturer {Company Name} has unveiled its latest innovation - Silica Fire Bricks. With a primary focus on delivering advanced materials for industrial furnaces, kilns, and other high-heat environments, the company's new product has already garnered attention within the sector. This article will dive into the key features and benefits of Silica Fire Bricks while exploring {Company Name}'s commitment to safety and excellence.Section 1: Silica Fire Bricks – The Breakthrough in High-Temperature Applications{Company Name}'s Silica Fire Bricks have been designed to withstand extremely high temperatures, making them an excellent choice for a wide range of industrial applications. These bricks are crafted using high-quality silica and possess exceptional thermal conductivity, allowing efficient heat transfer while ensuring long-lasting durability.Section 2: Unparalleled Strength and Durability for Maximum SafetyOne of the distinctive advantages of Silica Fire Bricks lies in their unmatched strength and durability. With a high melting point and excellent resistance to thermal shock, these firebricks can withstand repeated exposure to extreme temperatures without cracking or corroding. This feature significantly enhances the overall safety of industrial furnaces and kilns, leading to a reduced risk of accidents and equipment failure.Section 3: Optimal Thermal Insulation for Enhanced Energy EfficiencySilica Fire Bricks offer exceptional thermal insulation, which helps to enhance energy efficiency in high-temperature applications. By minimizing heat loss, these bricks not only contribute to cost savings but also play a crucial role in reducing greenhouse gas emissions.Section 4: Versatility and Adaptability for Various IndustriesRecognizing the diverse needs of different industries, {Company Name} has ensured that Silica Fire Bricks can be easily customized based on specific requirements. These bricks are available in various shapes and sizes, enabling seamless integration into different industrial furnaces, kilns, and ovens. Their versatility ensures they can cater to a wide range of industries such as steel, cement, glass, ceramics, and more.Section 5: {Company Name}'s Commitment to Safety and ExcellenceWith a strong emphasis on safety, {Company Name} has positioned itself as a trusted provider of high-quality refractory materials. By adhering to stringent quality control measures and continuously investing in research and development, the company has gained the confidence of industry professionals worldwide.Section 6: Ensuring Sustainable Practices with Silica Fire BricksRecognizing the importance of sustainability, {Company Name} has ensured that the manufacturing process of Silica Fire Bricks follows eco-friendly practices. The raw materials used are sourced responsibly, and the bricks themselves are 100% recyclable. By prioritizing sustainability, the company aims to promote a healthier environment for future generations.Section 7: Conclusion{Company Name}'s Silica Fire Bricks represent a breakthrough in the world of high-temperature applications. With their exceptional thermal conductivity, strength, durability, and energy efficiency, these bricks are set to revolutionize industrial furnaces, kilns, and ovens. As {Company Name} continues to prioritize safety, excellence, and sustainability, it stands poised to further consolidate its position as a leader in the firebrick manufacturing industry.
Insulating Castable Refractory Cement: Enhancing Heat Resistance and Insulation
Insulating Castable Refractory Cement: The Ultimate Solution for Industrial Heat ManagementIndustrial processes that involve high temperature require a lot of heat control mechanisms. Such mechanisms are put in place to prevent the equipment and products from melting or catching fire. Refractories are the materials used in the construction of these heat management systems.The idea of insulation castable refractory cement is nothing new to the industry. However, thanks to advancements in technology, there are more innovative options available today. Insulating castable refractory cement is one such option that has become increasingly popular.This product is particularly known for its ability to offer excellent thermal performance, energy efficiency, and high strength. It is made by mixing high-quality fine powder with fibers and binders, ensuring excellent quality, and performance.Insulating Castable Refractory Cement is a game-changer in the construction and repair of industrial furnaces and boilers. It is also used to insulate pipes and chimneys, making it a versatile product that can be applied in a variety of settings.Due to its high quality, this product from __________ - a global leader in the refractory industry - has become increasingly popular. This company is renowned for its commitment to quality, and customer satisfaction, providing a range of refractory products that meet the most challenging requirements.In addition to its exothermic insulation properties, insulating castable refractory cement also has high compressive strength. As a result, it can withstand heavy weight and pressure without cracking, ensuring durability and longevity, even in the most challenging conditions.The use of Insulating Castable Refractory Cement in the construction of boilers and furnaces has numerous benefits. One of the most significant benefits is energy efficiency. The insulation properties of this product help to reduce energy loss, while also facilitating the maintenance of consistent temperatures during industrial processes.Using this product has also proven to be cost-effective. Although initially more expensive than traditional insulating materials, it offers higher performance, reducing the overall cost of production in the long run.When working with insulating castable refractive cement, it is essential to hire professionals who are knowledgeable in the handling, mixing, and installation process. This not only ensures the best results but also guarantees the safety of the workers involved in the installation process.In conclusion, Insulating Castable Refractory Cement is the ultimate solution for industrial heat management, offering superior thermal performance, high compressive strength, durability, and energy efficiency. With the increasing demand for energy efficiency in industrial processes, investing in this product from __________- a global leader in the refractory industry - is the best solution for businesses that want to stay ahead of the game.