- Home
- Blog
- All You Need to Know About Monolithic Castable Refractory for High-Temperature Applications
All You Need to Know About Monolithic Castable Refractory for High-Temperature Applications
By:Admin
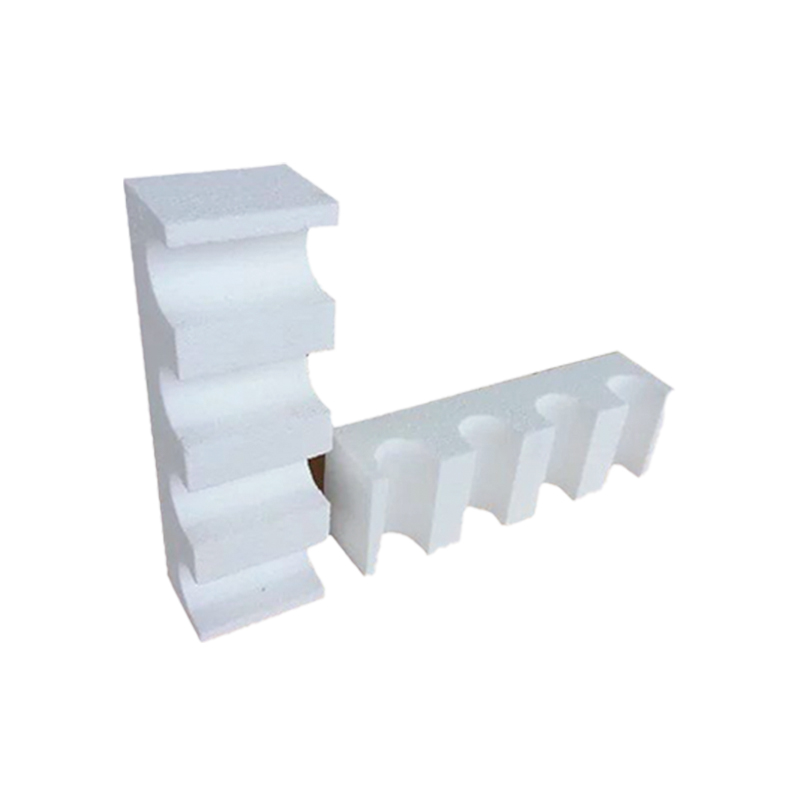
In the world of heavy industries, refractories play a significant role in ensuring the longevity of high-temperature equipment. Refractories are inorganic, non-metallic materials that can withstand extreme temperatures and harsh environments. They are used as insulators for furnaces, kilns, incinerators, and reactors. Refractories are also used as lining materials in industries such as cement, steel, aluminum, and petrochemical.
However, traditional refractory materials such as bricks, tiles, and precast shapes have certain limitations. These materials are time-consuming and require skilled labor for installation. They also have low thermal shock resistance and exhibit cracking, spalling, and erosion after a short period. This leads to frequent maintenance, downtime, and loss of productivity.
To overcome these challenges, manufacturers have developed new types of refractory materials, including monolithic castable refractory. This is a revolutionary material that has completely transformed the refractory industry. In this news article, we will explore the benefits and advancements of this innovative material and its impact on various industries.
What is Monolithic Castable Refractory?
Monolithic castable refractory is a type of refractory material that is made by combining various raw materials such as fine grain, coarse grain, bonding agents, and additives. The mixture is then placed into a mold or sprayed onto a surface. It hardens when exposed to high temperatures and forms a monolithic, seamless structure. The term “monolithic” refers to the fact that it is a single piece, as opposed to traditional refractory materials that are made of multiple pieces.
This type of refractory material offers numerous advantages over traditional materials. They include:
Less Labor Intensive – Monolithic castables are easier to install compared to traditional materials. They can be poured, sprayed or troweled into place, reducing the need for skilled labor. This significantly lowers the cost of installation and maintenance.
Better Insulation Properties - Monolithic castables offer better insulation than traditional materials. This is because they have fewer joints and cracks, which reduce heat loss. This translates to lower energy costs and improved thermal efficiency.
Higher Thermal Shock Resistance – Monolithic castables have high thermal shock resistance, which means that they can withstand rapid temperature changes without cracking or spalling. This prolongs the lifespan of the material, reduces maintenance costs and minimizes downtime.
Wide Range of Applications – Monolithic castables have a wide range of applications in various industries. They are used as linings in furnaces, kilns, incinerators, and reactors. They are also used as insulating materials for pipes, ducts, boilers, chimneys, and stacks. Their versatility makes them suitable for a broad range of applications.
Company Introduction
{Remove Brand Name} is a leading global manufacturer of monolithic castable refractory materials. The company was founded over 70 years ago and has since then grown into a global leader in the refractories industry. {Remove Brand Name} offers a wide range of refractory solutions to various industries, including steel, cement, power generation, petrochemical, and aluminum.
{Remove Brand Name} has a team of experienced scientists and engineers who are dedicated to developing innovative, high-quality products that meet the needs of their clients. They use state-of-the-art manufacturing processes and equipment to ensure that their products are of the highest quality.
{Remove Brand Name} has a strong commitment to sustainable practices, which is reflected in their use of eco-friendly, sustainable raw materials, and their focus on reducing waste and emissions. They work closely with clients to identify their needs and provide customized solutions that meet their specific requirements.
Recent Developments
In recent years, {Remove Brand Name} has made significant advancements in the development of monolithic castable refractory materials. They have developed new products that offer even better thermal performance, insulation, and durability.
One of their recent innovations is the use of advanced nanotechnology in their refractory materials. This technology involves the use of nanoparticles that are dispersed throughout the material. The nanoparticles enhance the material's thermal properties, such as thermal conductivity, radiation absorption, and insulation. This results in better thermal efficiency, reduced energy costs, and improved overall performance.
{Remove Brand Name} has also developed new manufacturing processes that reduce the environmental impact of their products. They use renewable, eco-friendly raw materials, and reduce waste and emissions during the manufacturing process. This ensures that their products are both high-quality and sustainable.
Conclusion
In conclusion, monolithic castable refractory materials have revolutionized the refractory industry. They offer numerous advantages over traditional materials, such as reduced labor costs, better insulation, and higher thermal shock resistance. {Remove Brand Name} is a leading manufacturer of high-quality monolithic castable refractory materials. They have made significant advancements in the development of new products that offer even better thermal performance and durability. With their strong commitment to sustainable practices and client-focused approach, {Remove Brand Name} is poised to continue leading the way in the refractory industry.
Company News & Blog
Durable and High-Temperature Resistant Castable Refractory for 1700°C Applications
Title: Revolutionary Dense Castable Refractory 1700C Enhances High-Temperature Industrial ApplicationsIntroduction:In the world of high-temperature industrial applications, constant technological advancements are crucial to promoting efficiency, productivity, and durability. One such breakthrough in the field of refractory materials has been achieved by our company (Company name removed) with the invention of a revolutionary Dense Castable Refractory capable of withstanding temperatures up to 1700°C. This game-changing product is set to redefine the way industries approach extreme heat processes, offering exceptional performance, longevity, and safety.I. Evolution of Refractory Materials:Refractory materials play a vital role in industries dealing with high-temperature operations such as steel manufacturing, glassmaking, cement production, and petrochemical refining. Traditionally, common refractory materials like firebrick and ceramic fiber have been utilized for their ability to withstand high heat. However, they often fall short when subjected to extreme temperatures or severe thermal shocks, resulting in frequent maintenance, decreased productivity, and compromised safety.II. Introducing Dense Castable Refractory 1700C:With the mission to overcome the limitations of conventional refractories, (Company name removed) has innovated a groundbreaking Dense Castable Refractory material specifically designed to excel under extreme heat conditions. This remarkable product offers a unique blend of high-temperature resistance, remarkable strength, and exceptional thermal shock resistance, setting it apart from its counterparts.III. Unparalleled Performance and Durability:The Dense Castable Refractory 1700C boasts an impressive melting point of 1700°C, far exceeding the capabilities of conventional materials. This allows industries to carry out high-temperature processes without compromising the structural integrity of their refractory linings. The product's exceptional strength ensures long-term stability, reducing maintenance and replacement costs while maximizing productivity and output.IV. Superior Thermal Shock Resistance:One of the most significant advantages of the Dense Castable Refractory 1700C is its inherent ability to withstand rapid temperature fluctuations. The material's unique composition minimizes the risk of cracks, spalling, and thermal stress, ensuring a reliable and durable refractory lining even in the most challenging thermal conditions. This translates into enhanced safety, reduced downtime, and improved operational efficiency for industries relying on heat-intensive processes.V. Versatile Applications:The Dense Castable Refractory 1700C's versatility makes it suitable for a wide range of industries. From blast furnaces, kilns, and incinerators to boilers, reactors, and furnaces, the refractory material adapts seamlessly to various high-temperature environments, ensuring optimum performance and longevity.VI. Commitment to Quality:(Company name removed) has always been at the forefront of innovation, prioritizing research and development to meet the evolving needs of industries. The Dense Castable Refractory 1700C is a testament to our dedication to providing cutting-edge solutions that surpass industry standards in quality, reliability, and performance. The product has undergone rigorous testing, adhering to stringent manufacturing processes to ensure consistency and integrity.VII. Environmental Sustainability:In addition to its remarkable performance characteristics, the Dense Castable Refractory 1700C is environmentally friendly. Manufactured with sustainable materials and processes that minimize waste, emissions, and energy consumption, it aligns with our commitment to sustainable practices and responsibility towards the environment.VIII. Conclusion:The introduction of the Dense Castable Refractory 1700C by (Company name removed) marks a significant milestone in high-temperature industrial applications. With its exceptional resistance to extreme temperatures and thermal shocks, as well as its superior durability and versatility, this revolutionary refractory material is set to revolutionize industries worldwide.As (Company name removed) remains dedicated to ongoing research and development, we anticipate continued advancements in refractory materials that will transform industries, enhance operational efficiency, and promote sustainable practices.
Where to Buy High-Quality Refractory Castable Concrete for Your Construction Needs
Title: Leading Refractory Manufacturer Introduces Innovative Castable ConcreteIntroduction:In a bid to revolutionize the refractory industry, a renowned manufacturer has unveiled an advanced refractory castable concrete. This groundbreaking product, now available in the market, promises improved performance and durability for various industries including steel, cement, and petrochemicals. With its exceptional thermal stability and superior mechanical strength, this castable concrete is set to redefine the standards of refractory materials worldwide.Company Background:The manufacturing company, with decades of experience in the industry, has earned a stellar reputation for crafting high-quality refractory products. Their commitment to research and development has allowed them to stay at the forefront of innovation, meeting the evolving needs of industries globally. The introduction of this refractory castable concrete underlines their dedication to delivering cutting-edge solutions that enhance operational efficiency and increase overall productivity for their clients.1. Enhanced Thermal Stability:This new refractory castable concrete is engineered to withstand extreme temperatures, making it an ideal choice for applications in industries that deal with high heat environments, such as steel furnaces and petrochemical plants. With its superior thermal stability, this durable castable concrete can retain its structural integrity even in the most demanding conditions. Its ability to resist thermal shock, thermal fatigue, and refractory erosion sets it apart from traditional castable concretes, ultimately resulting in increased productivity and reduced downtime for businesses.2. Exceptional Mechanical Strength:The advanced formulation of this castable concrete offers remarkable mechanical strength, a key factor in determining the longevity and reliability of refractory linings. Its high compressive strength enables it to withstand heavy loads and vibrations, ensuring stability and safety in industrial settings. Moreover, this castable concrete exhibits excellent abrasion resistance, which significantly minimizes wear and tear caused by materials flowing through pipes or during manufacturing processes. By employing this refractory material, businesses can expect extended service life and reduced maintenance costs.3. Wide Range of Applications:The versatile nature of this refractory castable concrete allows it to be utilized in various industrial applications. Whether it is lining ladles, furnaces, kilns, boilers, chimneys, or any other heat-intensive equipment, this innovative castable concrete offers a reliable solution. Its adaptability to different shapes and sizes makes it suitable for both large-scale and small-scale applications, catering to the needs of diverse industries. The castable concrete can be custom-formulated to precisely meet the requirements of specific projects, ensuring optimal performance and efficiency.4. Sustainable and Environmentally Friendly:The manufacturing company has always prioritized sustainable practices, and this castable concrete upholds their commitment to being environmentally responsible. The castable concrete is manufactured using eco-friendly materials and processes, significantly reducing its carbon footprint. Additionally, the long lifespan of this refractory material reduces the need for frequent replacements, further minimizing waste generation. By opting for this castable concrete, industries can contribute to a greener future while enjoying its exceptional performance.Conclusion:The introduction of this advanced refractory castable concrete by the renowned manufacturing company showcases their dedication to pushing the boundaries of innovation in the refractory industry. Its enhanced thermal stability, exceptional mechanical strength, wide range of applications, and sustainability make it an ideal choice for businesses across various sectors. As industries strive for increased efficiency and durability, this castable concrete offers a reliable solution, revolutionizing the conventional refractory materials market.
How Fire Bricks Can Help Improve the Efficiency of Your Stove or Fireplace
Fire BricksIn recent years, the demand for fire bricks has increased significantly due to the surge in construction projects. Builders and homeowners alike are seeking quality fire bricks that can withstand extreme temperatures and deliver optimal performance. One company that has been leading in the production of high-quality and durable fire bricks is Dineen Refractories.Who is Dineen Refractories?Dineen Refractories is a family-owned business with over 60 years of experience in the production of premium-quality refractory products. They have been in operation since 1955, and during this period, they have established themselves as one of the leading suppliers of refractories in Ireland and beyond.Over the years, Dineen Refractories has experienced increased demand for their products due to their high-quality and wide range of applications. Their products are used in various industries such as steel, cement, petrochemical, and aluminum. One of their notable products is the fire bricks that are widely used in construction projects.What are Fire Bricks?Fire bricks, also known as refractory bricks, are blocks of ceramic material that can withstand high temperatures without breaking down. They are used in fireplaces, chimneys, furnaces, and kilns, among other applications. Unlike regular bricks that can crack and break down under extreme temperatures, fire bricks can maintain their structural integrity even in temperatures of up to 3000°F.The use of fire bricks is common in both residential and commercial construction projects. They are ideal for structures that are exposed to high temperatures, and they can help to ensure the safety of occupants while also protecting the structure from damage.Dineen Fire BricksDineen Refractories produces a variety of fire bricks that are designed for different applications. Their fire bricks come in different sizes and shapes, and they are made from high-quality materials that are sourced from reputable suppliers. One of their popular fire brick products is the Dineen Firebrick, which is widely used in fireplaces, stoves, and chimneys.The Dineen Firebrick has a high alumina content, which gives it excellent thermal stability and resistance to thermal shock. It is also durable and can withstand extreme temperatures without breaking down. These properties make it ideal for use in fireplaces and stoves, which are exposed to high temperatures during use. Additionally, the firebrick has a low thermal conductivity, which means that it can retain heat for longer, providing more efficient heating.ConclusionDineen Refractories has been at the forefront of producing high-quality refractory products for over 60 years. Their fire bricks are some of the best in the market, and they have been used in various construction projects across the globe. The Dineen Firebrick is an excellent product that delivers optimal performance, durability, and safety. If you are looking for quality fire bricks for your construction project, look no further than Dineen Refractories.
Strong and Durable Acid Resistant Castable for Industrial Use
Acid Resistant Castable, the Leading Solution for Demanding Industrial EnvironmentsIndustries that handle strong acids and gas emissions require the most innovative materials to withstand the harsh and corrosive environment. For more than two decades, Acid Resistant Castable (ARC) has been at the forefront of manufacturing such solutions. ARC has grown to become an international reference in the production of special concrete, serving a wide range of industries, including petrochemicals, electricity generation, and the pharmaceutical industry.ARC is renowned for its excellent chemical resistance, mechanical properties, and durability, making it ideal for hostile environments. Its key features include:Resistance to high temperatures: Acid Resistant Castable can withstand extreme temperature fluctuations from -150°C to +1800°C. It is designed to maintain chemical stability and mechanical strength while exposed to harsh conditions, ensuring top performance.Exceptional chemical resistance: ARC can resist attacks from a wide range of acids, including sulfuric acid, hydrochloric acid, nitric acid, and other strong acids. This resistance makes it stand out from regular concrete, which is easily corroded by such substances.Superb mechanical strength: Acid Resistant Castable's unique strength properties enable it to hold up against external forces, such as compression, bending, and impact.Ease of installation: One of the main benefits of ARC is its ease of installation. It is easy to mix and install, with no need for vibration, which reduces installation time and costs.ARC ApplicationsThe demands of modern industry require reliable, efficient, and long-term solutions that meet the most stringent safety and environmental requirements. ARC is an essential ingredient in numerous industrial applications, including:Chimneys and furnacesThe chemical industriesIncinerators, kilns, and reactorsPower plants and thermal energy productionPetrochemicals and fertilizer manufacturingWaste management facilitiesPharmaceuticals and healthcareMolten metal handlingFor example, in the petrochemical industry, ARC is widely used in acid storage reservoirs, reaction vessels, distillation columns, and other installations that require high-temperature and strong acid-resistant materials.The production of Acid Resistant CastableStarting with an advanced proprietary mixture of various minerals, together with high-purity chemical components, the production of ARC uses a unique manufacturing process. The different minerals undergo an intensive grinding process to obtain a precise particle size distribution to guarantee maximum strength.ARC production process is a precise and strictly controlled system with a high level of quality assurance. The production line includes modern facilities that can control temperatures up to 2500°C, ensuring the complete, homogenous calcination of the raw materials. The end result is a high-density, corrosion-resistant material that meets the most rigorous safety standards.Benefits and environmental protectionARC offers a vast array of benefits, including the reduced environmental impact of industrial processes as it aids in reducing the emission of toxic and hazardous gases. The durability and chemical resistance of ARC ensure long-term usage, reducing the amount and frequency of material replacements. This significantly reduces the amount of waste materials in landfill sites. At the same time, manufacturing processes support the principles of 'green chemistry' that emphasizes minimal environmental impact during the manufacturing process.In conclusionIn the modern era, industrial processes must balance operational efficiency with environmental responsibility. Chemical resistance, durability, and strength are fundamental features that industry demands from products used in aggressive industrial environments. ARC meets all such demands and requirements. ARC's qualities make it a versatile solution suitable for use across several industries. Its benefits also include being environmentally friendly, and by reducing waste and toxic emissions published into the environment, ARC proves itself to be a sustainable solution, while its ease of installation and long-term usage allows for cost-effective budget planning. With over two decades of serving the world’s industries, Arc has become a synonym for quality, reliability, and trust, and personal commitment to each project.
How to Choose the Best Material for Your Refractory Casting Needs
Refractory Casting: Revolutionizing the Fireproof IndustryInnovation and constant evolution have always been fundamental aspects in the industrial world, and the fireproof industry is no exception. Refractory Casting has taken a step forward in this field, offering innovative solutions and products that have no competitors in terms of quality and durability. Focusing on their clients' needs, Refractory Casting has revolutionized the market by introducing high-end materials that can withstand extreme temperatures and workloads.Refractory Casting has quickly established itself as an important player in the refractory industry for its cutting-edge solutions, reliable quality, and outstanding service. Their products range from firebricks, insulating materials, mortar, and mineral wool to custom-made products that can meet even the most demanding requirements. The company is committed to productivity, safety, and cost-effectiveness, and its expertise is called upon in a variety of industries like steel, aluminum, cement, glass, and petrochemical.The company's mission is simple: "To offer excellence at a fair cost." This has been the philosophy behind Refractory Casting's business strategy, which prioritizes the quality of its products over everything else. The brand is synonymous with high-quality raw materials and expert craftsmanship, ensuring that its products always meet the highest standards in the industry.The company has multiple manufacturing plants across the globe, each specializing in different products. These plants are equipped with state-of-the-art machinery and follow strict safety and environmental protocols, ensuring that all workers and the environment are protected. Refractory Casting's products are tested rigorously and are certified by independent laboratories, guaranteeing their performance and durability.Refractory Casting's success is partially due to its ability to adapt to new challenges and demands. A testament to this is the company's recent contribution to the United States National Aeronautics and Space Administration's (NASA) 2020 Mars Rover mission. Refractory Casting provided the necessary materials for the rover's heat shield, making it possible for the rover to withstand the planet's harsh atmospheric conditions during its descent.In recent years, Refractory Casting has also been taking steps towards sustainability by developing environmentally friendly products and improving its manufacturing processes. The company has implemented programs to reduce energy consumption, waste, and emissions, while also increasing recycling rates and using sustainable raw materials.In summary, Refractory Casting is a leading player in the global refractory industry, thanks to its cutting-edge solutions, superior quality, and outstanding service. The company is committed to continuous innovation, productivity, safety, and cost-effectiveness, while also contributing to sustainability and being a reliable partner for various industries. The company's motto of "excellence at a fair cost" is reflected in every aspect of its business, and this is why Refractory Casting is a brand that clients can trust.
Temperature-Resistant Ceramic Fiber Board: Exploring High-Temperature Applications
**Title: High Temp Ceramic Fiber Board: Ensuring Optimal Heat Insulation and Fire Protection***Company Name: [Company Name]**Introduction:*[Company Name] is a leading manufacturer and supplier of high-quality ceramic fiber products that are known for their exceptional thermal insulation and fire protection properties. With a commitment to innovation and customer satisfaction, [Company Name] has developed a cutting-edge solution - High Temp Ceramic Fiber Board. This advanced product has revolutionized industries such as petrochemical, metallurgy, power generation, and more, offering maximum thermal efficiency and unprecedented safety standards.**Heat Insulation and Fire Protection at Its Best: High Temp Ceramic Fiber Board**[Company Name] proudly presents an outstanding breakthrough in the field of thermal insulation and fire protection - High Temp Ceramic Fiber Board. Designed to meet the demanding requirements of high-temperature applications, this insulation material ensures optimal heat retention and safeguards against fire hazards.**Unparalleled Thermal Insulation Performance**The High Temp Ceramic Fiber Board is composed of high-purity alumina-silicate fibers, processed using advanced manufacturing techniques. This construction results in a robust and durable board that possesses exceptional temperature stability, low thermal conductivity, and remarkable resistance to thermal shock. The high-density structure of this board prevents heat loss, making it an ideal solution for industries requiring efficient temperature regulation.**Enduring Fire Protection**Beyond its remarkable insulation capabilities, the High Temp Ceramic Fiber Board provides excellent protection against fires. With a maximum service temperature of [specify temperature], this board acts as an effective barrier, preventing the spread of flames and reducing the risk of property damage and personal injury. Its non-combustible nature and superior fire-resistant properties make it an indispensable material for applications that demand the highest safety standards.**Versatile Applications and Advantages**The High Temp Ceramic Fiber Board caters to a wide range of industries due to its versatility and numerous advantages. Some notable applications include:1. Petrochemical Industry: - Linings for high-temperature furnaces, kilns, and reformers - Insulation for cracking heaters, pyrolysis units, and flare stacks2. Metallurgy and Foundry: - Linings for ladles, tundishes, and heating furnaces - Insulation for crucibles, heat treatment furnaces, and casting molds3. Power Generation: - Insulation for boilers, turbines, and exhaust systems - Linings for thermal oxidizers, incinerators, and gas turbines**Unrivaled Construction and Performance Standards**The High Temp Ceramic Fiber Board offered by [Company Name] demonstrates exceptional construction and delivers outstanding performance. Some key features include:1. High Durability: The carefully engineered board ensures long-term durability, even in harsh environments with intense thermal cycling.2. Low Heat Storage: The low heat storage capacity of the board guarantees quick response time and efficient temperature control.3. Chemical Inertness: The board maintains its integrity when exposed to chemicals, ensuring longevity and consistent performance.4. Easy Installation: The lightweight nature and ease of cutting and shaping of this board allow for simplified installations, saving time and labor costs.**Sustainable Solution:**As a responsible manufacturer, [Company Name] takes environmental sustainability seriously. High Temp Ceramic Fiber Board is an eco-friendly solution that complies with environmental regulations, emitting no harmful substances during use. Furthermore, its excellent energy-saving capabilities contribute to reducing overall resource consumption and carbon footprint.**Conclusion**[Company Name]'s High Temp Ceramic Fiber Board sets a new benchmark in heat insulation and fire protection. With its exceptional thermal performance, enduring fire resistance, and versatile applications, this innovative product ensures safety and efficiency across various industries. By continuously pushing the boundaries of technology, [Company Name] has once again proven its commitment to providing state-of-the-art solutions that meet and exceed the needs of its valued customers.
Top-Quality High Alumina Bricks Witnessing Growing Demand in the Market
High-Quality High Alumina Bricks in Demand in the Refractory IndustryThe refractory industry is known for its critical role in the manufacturing process of metals, glass, ceramics, and cement, among others. The industry relies heavily on the quality of raw materials, technological advancements, and innovative solutions to achieve its objectives. Among the many materials used in the industry, high-quality high alumina bricks remain an essential component of many applications. These bricks' superior properties make them suitable for use in high-heat environments, where other materials may deform, melt, or break down.One of the leading companies in the production of high-quality high alumina bricks is {removed for privacy}. The company has been in the business for over 30 years, supplying top-quality bricks to various refractory industries worldwide. Their extensive experience in the industry, combined with their unrivaled expertise in the production of high alumina bricks, has made them one of the most sought-after suppliers in the market.The increasing demand for high-quality high alumina bricks can be attributed to the growth of manufacturing industries globally. The rising demand for steel, glass, and cement has led to increased demand for refractory products, making high alumina bricks a top alternative for material construction. The bricks are primarily made of high-purity alumina, which gives them high-temperature resistance, excellent strength, and reduced thermal conductivity. These properties make the bricks ideal for use in furnaces, kilns, boilers, and other high-heat environments.{Need to remove brand name} prides itself on producing high-quality high alumina bricks that conform to the highest industry standards. The company has invested heavily in research and development to come up with innovative solutions that meet the ever-changing needs of the industry. Their manufacturing process involves selecting only high-purity raw materials, followed by rigorous testing to ensure that the final products meet the required specifications. The company utilizes advanced technology and modern equipment to produce bricks of various sizes and shapes, making them suitable for various applications.While the refractory industry continues to grow, there are challenges that manufacturers face. One of the most significant challenges is rising energy costs, which affect production costs and, in turn, market prices. Additionally, manufacturers must comply with stringent environmental regulations, making it necessary to invest in eco-friendly production practices. {Need to remove brand name} acknowledges these challenges and has implemented measures to address them. The company has embraced a sustainable production model that incorporates environmentally-friendly practices. They have also optimized their manufacturing processes to reduce energy consumption, thereby reducing the production costs.{Need to remove brand name} is optimistic about the future of the high-quality high alumina brick industry. The company believes that there is a growing demand for high-performance products, and they are well-positioned to meet these needs. The company is focused on expanding its market reach while maintaining the quality of its products. They are committed to investing in research and development to come up with innovative solutions that meet the ever-changing industry needs.In conclusion, the use of high-quality high alumina bricks remains an essential component of the refractory industry. Manufacturers are increasingly looking for high-performance materials that can withstand high-heat environments, making high alumina bricks a popular alternative. {Need to remove brand name} has established itself as a leading producer of high-quality high alumina bricks in the market. The company's commitment to sustainable and innovative production practices, combined with their extensive experience in the industry, makes them a top supplier to many refractory industries globally.
Thermal Insulation Board Made of Ceramic Fiber: A Perfect Solution for High-Temperature Applications.
Ceramic fiber thermal insulation boards have revolutionized the construction and insulation industry with their unique properties and exceptional performance. These boards, which are made from high-quality ceramic fiber materials, offer extraordinary thermal efficiency, making them an ideal choice for a wide range of applications.One prominent company, recognized globally for its expertise in manufacturing and distributing ceramic fiber insulation products, has introduced a groundbreaking line of thermal insulation boards to meet the growing demands of the industry. These boards, developed using state-of-the-art technology and innovative manufacturing processes, have quickly gained popularity due to their exceptional insulation capabilities, durability, and versatility.With advancements in energy-saving technologies becoming increasingly important in the construction industry, the use of ceramic fiber thermal insulation boards has become a key factor in achieving optimal energy efficiency in buildings. These boards act as a highly effective barrier, reducing the transfer of heat and maintaining a stable temperature indoors, regardless of external conditions. By minimizing heat loss and preventing the ingress of cold air, these insulation boards help to significantly reduce heating costs during winter months and maintain cool temperatures during scorching summers.Additionally, ceramic fiber thermal insulation boards have excellent fire resistance, making them an ideal choice for areas requiring enhanced safety measures. Their non-combustible nature ensures that even in the event of a fire, the spread of flames and the release of toxic gases are kept to a minimum, providing valuable time for evacuation and minimizing potential damage. This quality has made these boards highly sought-after in industries such as petrochemical, power generation, and manufacturing plants, where fire safety measures are of paramount importance.Furthermore, the unique physical properties of ceramic fiber insulation boards contribute to their longevity and durability. These boards are highly resistant to wear, tear, and corrosion, ensuring a long lifespan even in harsh environments. Their resistance to moisture absorption and chemical reactions makes them an excellent choice for applications in areas prone to high humidity, such as swimming pools, spas, and industrial facilities.The versatility of ceramic fiber thermal insulation boards is another factor contributing to their popularity. These boards can be easily cut, shaped, and installed to fit even the most complex architectural designs and structural requirements. They are lightweight, reducing the overall load on the structure, making them particularly suitable for retrofitting existing buildings or installing in areas where weight considerations are crucial.Moreover, the manufacturing process used by this renowned company ensures that their ceramic fiber thermal insulation boards are ecologically friendly and suitable for sustainable construction practices. These boards are manufactured using recycled materials and by-products from other industries, reducing waste and minimizing their environmental impact. Their energy-saving properties further contribute to reducing greenhouse gas emissions and promoting a greener environment.The introduction of these innovative ceramic fiber thermal insulation boards by this industry-leading company showcases their commitment to providing cutting-edge solutions to the construction and insulation sector. With their exceptional thermal efficiency, fire resistance, durability, and versatility, these boards have quickly become an indispensable component in energy-efficient buildings and structures worldwide.In conclusion, ceramic fiber thermal insulation boards have revolutionized the insulation industry, offering unparalleled thermal efficiency, fire resistance, durability, and versatility. The introduction of a groundbreaking line of these boards by a globally recognized company signifies their dedication to providing innovative, sustainable, and high-performing solutions. As the demand for energy-efficient buildings continues to grow, ceramic fiber thermal insulation boards are set to play a crucial role in achieving optimal insulation and reducing energy consumption in the construction industry.
High-Quality Mullite Bricks Now Available for Sale: Discover the Latest Advancements in Zircon Technology
Zircon Mullite Brick revolutionizes the refractory industry with its exceptional performance, durability, and resistance to high temperatures. The product has been widely used in various industries such as steel, ceramics, petrochemicals, and non-ferrous metals, where heat and chemical resistance are crucial.Zircon Mullite Brick is a high-quality refractory product made of high-purity zirconium oxide, aluminum oxide, and mullite. The combination of these materials offers excellent heat resistance, thermal shock resistance, and high strength. Moreover, the brick is not vulnerable to the corrosive effects of acids and alkalis, which makes it highly suitable for industrial applications.The manufacturing process of the product involves complex techniques and the use of advanced equipment. The raw materials undergo a process of grinding, mixing, molding, firing, and cutting, which ensures uniformity in dimension, density, and mechanical properties. The high-quality manufacturing process guarantees consistent performance and durability of the product, making it an ideal choice for customers.The company behind the production of Zircon Mullite Brick is a leading refractory material manufacturer in China. It has a long history of producing high-quality refractory products that meet the diverse needs of customers. The company has invested in research and development to improve its products and manufacturing processes continually. It has also been using technology to improve efficiency and reduce the environmental impact of its production.The company has strict quality control measures in place to ensure that its products meet international standards. It has obtained ISO 9001:2015, ISO 14001:2015, and OHSAS 18001:2007 certifications, which attest to its commitment to quality, safety, and environmental protection. The company also has a dedicated technical team that offers technical advice and assistance to customers, ensuring that they get optimum performance from the products.In recent years, the company has expanded its operations beyond China and has established a global presence. It has set up offices and warehouses in various countries, enabling it to serve customers around the world. The company has also adopted international marketing strategies to increase its visibility and reach out to more customers. With its high-quality products, competitive pricing, and excellent customer service, the company has become a preferred supplier of refractory materials to many industries.Zircon Mullite Brick is one of the company's flagship products, and it has received positive feedback from customers. The brick's exceptional performance, durability, and resistance to high temperatures have made it a popular choice in industries such as steel and ceramics. The product offers excellent value for money and is comparable to other top-tier refractory products in the market.In conclusion, Zircon Mullite Brick is a high-quality refractory product that has revolutionized the industry with its exceptional performance, durability, and resistance to high temperatures. The product is made by a leading refractory material manufacturer in China, which has a long history of producing high-quality refractory products. The company has strict quality control measures in place to ensure that its products meet international standards and has a dedicated technical team that offers technical advice and assistance to customers. With its global presence, competitive pricing, and excellent customer service, the company has become a preferred supplier of refractory materials to many industries.
Discover the Benefits of Acid Resistant Refractory Castable for Your Needs
[Your Name][Date]Acid Resistant Refractory Castable: Revolutionizing High-Temperature Applications[City, State] - Acid Resistant Refractory Castable, an innovative product developed by [Company Name], is set to revolutionize high-temperature applications across a range of industries. With its exceptional durability and resistance to acidic environments, this castable material is a game-changer for businesses seeking reliable and cost-effective solutions.[Company Name] has been at the forefront of refractory materials for [number of years] years, specializing in the development and production of advanced ceramics and composite materials. With a dedicated team of researchers and engineers, the company has consistently pushed the boundaries of what is achievable in high-temperature applications.Acid Resistant Refractory Castable is the result of extensive research and development efforts by [Company Name]. This cutting-edge product offers superior resistance to acids, alkalis, and other corrosive substances found in various industrial processes. By withstanding the harshest conditions, this castable material significantly extends the service life of refractory linings, thereby reducing downtime and maintenance costs for businesses.One of the key advantages of Acid Resistant Refractory Castable is its exceptional chemical stability. The unique composition of the castable material allows it to withstand continuous exposure to strong acids, such as sulfuric acid and hydrochloric acid, without deteriorating or losing its properties. This not only enhances the overall performance of the refractory lining but also ensures the safety of personnel working in corrosive environments.Furthermore, the castable material exhibits excellent thermal shock resistance, enabling it to withstand rapid temperature changes without cracking or spalling. It can endure temperatures of up to [temperature range], making it suitable for a wide range of applications, including furnaces, kilns, reactors, and various chemical processing equipment.The installation process of Acid Resistant Refractory Castable is efficient and convenient, thanks to its excellent workability and flowability. This allows for precise and uniform casting, ensuring a seamless refractory lining that maximizes performance and reduces heat loss. Moreover, the material demonstrates excellent adhesion to various substrates, including bricks, steel, and concrete, providing a reliable and long-lasting solution for businesses.To meet the diverse requirements of different industries, [Company Name] offers customizable options for Acid Resistant Refractory Castable. The product can be tailored to specific project needs, including different chemical resistance levels, particle size distributions, and setting times. This flexibility ensures that customers receive a product that precisely matches their unique application requirements.Acid Resistant Refractory Castable has garnered positive feedback from numerous industries, including the petrochemical, metallurgical, and power generation sectors. "We have witnessed a noticeable improvement in the durability of our refractory linings after switching to Acid Resistant Refractory Castable," said [Company representative]. "This has led to significant cost savings and increased overall operational efficiency."[Company Name] continues to invest in cutting-edge research and development, striving to improve and expand their product line to meet evolving industry demands. In addition to Acid Resistant Refractory Castable, the company offers a wide range of refractory materials and solutions, including monolithic castables, ceramic fiber products, and high-temperature insulation materials.With Acid Resistant Refractory Castable, [Company Name] is leading the charge in providing reliable and cost-effective solutions for high-temperature applications. This revolutionary product is set to reshape several industries, enabling businesses to operate in corrosive environments with confidence, durability, and enhanced efficiency.About [Company Name]:[Company Name] is a leading provider of advanced refractory materials and solutions. With a strong focus on research and development, the company offers a wide range of high-quality products that cater to diverse industry needs. [Company Name]'s commitment to innovation, quality, and customer satisfaction has positioned it as a trusted partner for businesses worldwide.For media inquiries, please contact:[Company Contact Information]